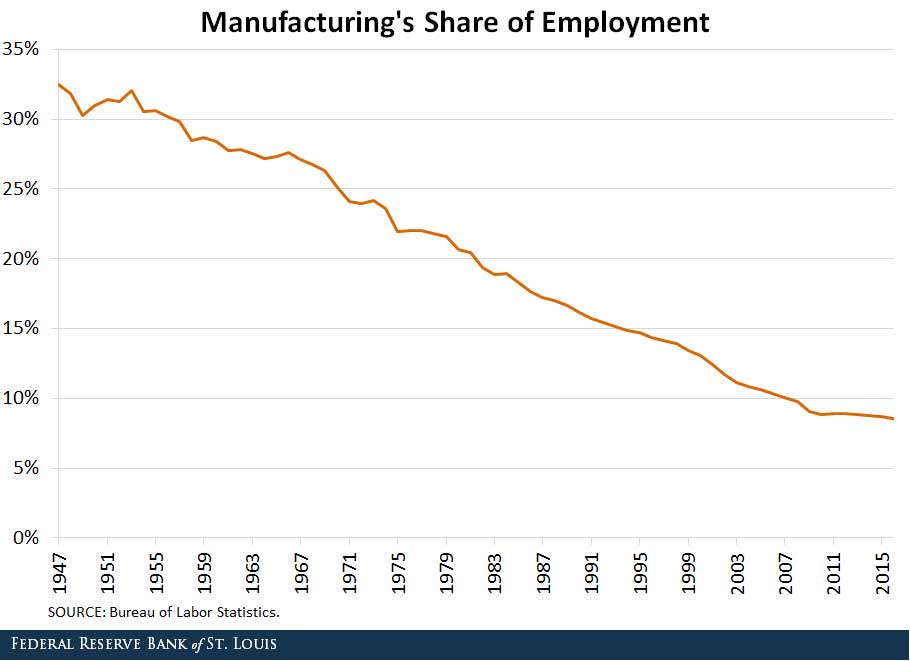
The five principles of Lean Five emphasize eliminating waste. They also encourage value stream mapping to identify areas that can be performed more efficiently. The key to eliminating waste is to differentiate value-added (necessary) waste from non-value-added (unnecessary) waste. The simplest process can be made to use the most energy and time. This allows you to produce high-quality products in a shorter time and keeps customers satisfied.
Value
You can improve the flow of manufacturing by eliminating waste using the Value of Lean 5 principles. It's possible to make production and shipping smoother by eliminating unnecessary steps. This eliminates inventory that is not needed and allows you to reduce your work and save time.

Value stream
Lean manufacturing uses the value stream to reduce waste. This process maps every step in the process to identify elements that are important and eliminate those not. The value stream considers the entire product's lifecycle, from its conception to its disposal. This is the key to eliminating all waste. A value stream can contain three types of waste.
Flow
The first of 5 lean principles, Flow, involves identifying customers' actual needs and evaluating them. This is essential for designing new products and services as customers may not always be able to express their needs clearly. The second step in the process is to determine the value stream. It's the sequence of activities required to complete the project. This requires close collaboration from all project participants.
Pull
In a pull system, the process begins only when there is an order from a customer. For example, a pizza restaurant would not make extra pizzas; they would only produce food when they have received a customer order. This would mean they would waste resources, time, and food.
Perfection
One of 5 principles of lean is the pursuit for perfection. According to this concept perfection is an ideal state which is accurate, complete, and consistent. However, achieving perfection is an elusive goal. This concept is designed to encourage continuous improvement. The result is a better performance for organizations.
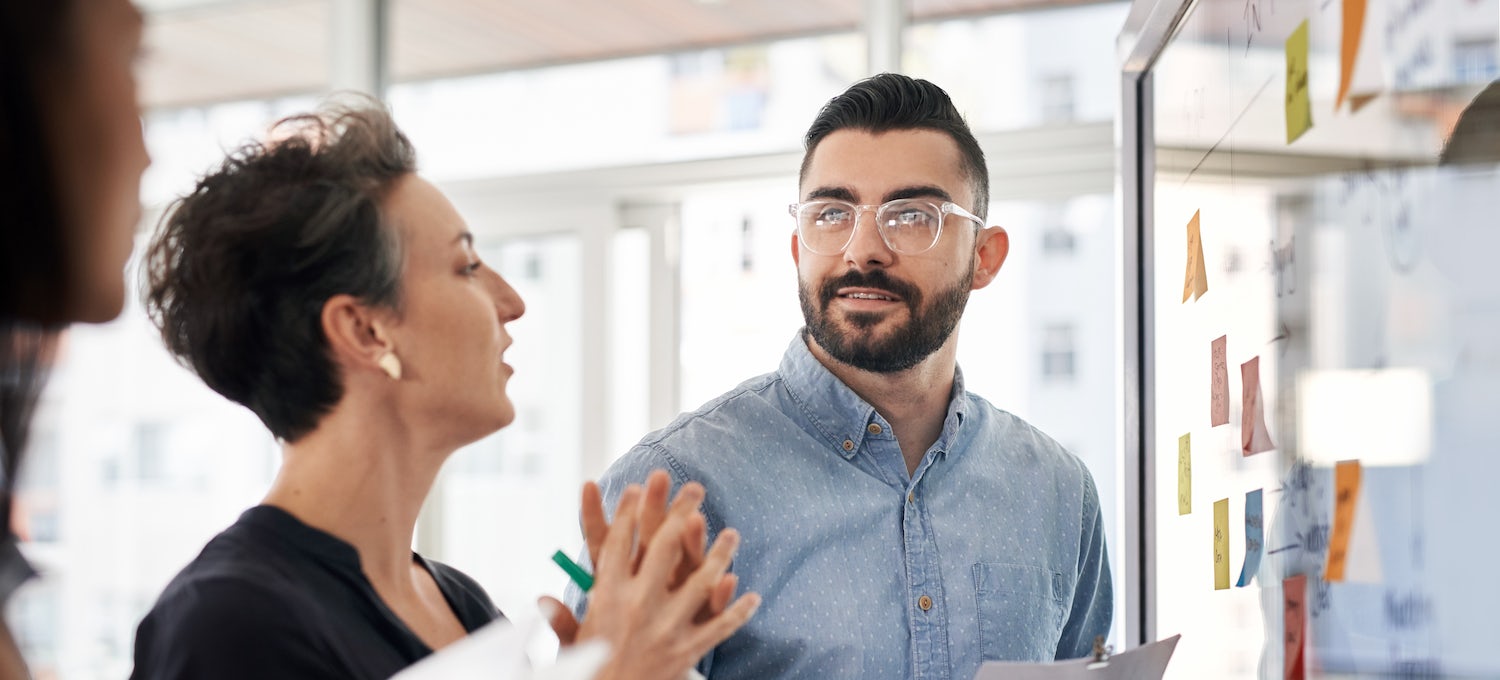
Collaboration of stakeholders
Stakeholder collaboration is a key element of lean project management. This involves collaboration among project team members to solve problems, and increase the project's value. In the planning stage, teams should identify problems and areas of improvement. The doing phase is less about execution and more about gathering information that will assist them in their search for solutions. For collaboration, the team must also take into consideration the organizational structure.
FAQ
What does the term manufacturing industries mean?
Manufacturing Industries is a group of businesses that produce goods for sale. Consumers are people who purchase these goods. To accomplish this goal, these companies employ a range of processes including distribution, sales, management, and production. They create goods from raw materials, using machines and various other equipment. This covers all types of manufactured goods including clothing, food, building supplies and furniture, as well as electronics, tools, machinery, vehicles and pharmaceuticals.
How can overproduction in manufacturing be reduced?
Improved inventory management is the key to reducing overproduction. This would reduce the time needed to manage inventory. This could help us free up our time for other productive tasks.
This can be done by using a Kanban system. A Kanbanboard is a visual tool that allows you to keep track of the work being done. Work items are moved through various states to reach their destination in a Kanban system. Each state represents a different priority level.
For instance, when work moves from one stage to another, the current task is complete enough to be moved to the next stage. However, if a task is still at the beginning stages, it will remain so until it reaches the end of the process.
This helps to keep work moving forward while ensuring that no work is left behind. With a Kanban board, managers can see exactly how much work is being done at any given moment. This information allows them to adjust their workflow based on real-time data.
Another way to control inventory levels is to implement lean manufacturing. Lean manufacturing focuses on eliminating waste throughout the entire production chain. Waste includes anything that does not add value to the product. Some common types of waste include:
-
Overproduction
-
Inventory
-
Packaging that is not necessary
-
Overstock materials
These ideas can help manufacturers improve efficiency and reduce costs.
How can I learn about manufacturing?
The best way to learn about manufacturing is through hands-on experience. But if that is not possible you can always read books and watch educational videos.
What is the role of a manager in manufacturing?
Manufacturing managers must ensure that manufacturing processes are efficient, effective, and cost-effective. They should also be aware of any problems within the company and act accordingly.
They should also know how to communicate with other departments such as sales and marketing.
They should also be aware of the latest trends in their industry and be able to use this information to help improve productivity and efficiency.
What are the 7 Rs of logistics?
The acronym 7Rs of Logistics refers to the seven core principles of logistics management. It was developed by International Association of Business Logisticians (IABL), and published as part of their "Seven Principles of Logistics Management Series" in 2004.
The acronym is made up of the following letters:
-
Responsive - ensure all actions are legal and not harmful to others.
-
Reliable - have confidence in the ability to deliver on commitments made.
-
It is reasonable to use resources efficiently and not waste them.
-
Realistic – Consider all aspects, including cost-effectiveness as well as environmental impact.
-
Respectful - show respect and treat others fairly and fairly
-
Responsive - Look for ways to save time and increase productivity.
-
Recognizable: Provide customers with value-added service
What are the 4 types manufacturing?
Manufacturing is the process of transforming raw materials into useful products using machines and processes. Manufacturing involves many activities, including designing, building, testing and packaging, shipping, selling, service, and so on.
Are there ways to automate parts of manufacturing?
Yes! Yes! Automation has existed since ancient times. The Egyptians invent the wheel thousands of year ago. To help us build assembly lines, we now have robots.
Actually, robotics can be used in manufacturing for many purposes. They include:
-
Automated assembly line robots
-
Robot welding
-
Robot painting
-
Robotics inspection
-
Robots that make products
There are many other examples of how manufacturing could benefit from automation. For example, 3D printing allows us to make custom products without having to wait for weeks or months to get them manufactured.
Statistics
- (2:04) MTO is a production technique wherein products are customized according to customer specifications, and production only starts after an order is received. (oracle.com)
- [54][55] These are the top 50 countries by the total value of manufacturing output in US dollars for its noted year according to World Bank.[56] (en.wikipedia.org)
- Job #1 is delivering the ordered product according to specifications: color, size, brand, and quantity. (netsuite.com)
- In 2021, an estimated 12.1 million Americans work in the manufacturing sector.6 (investopedia.com)
- In the United States, for example, manufacturing makes up 15% of the economic output. (twi-global.com)
External Links
How To
How to use 5S to increase Productivity in Manufacturing
5S stands as "Sort", Set In Order", Standardize", Separate" and "Store". Toyota Motor Corporation developed the 5S method in 1954. It helps companies achieve higher levels of efficiency by improving their work environment.
This approach aims to standardize production procedures, making them predictable, repeatable, and easily measurable. Cleaning, sorting and packing are all done daily. This knowledge allows workers to be more efficient in their work because they are aware of what to expect.
Implementing 5S requires five steps. These are Sort, Set In Order, Standardize. Separate. And Store. Each step requires a different action to increase efficiency. For example, when you sort things, you make them easy to find later. Once you have placed items in an ordered fashion, you will put them together. Once you have separated your inventory into groups and organized them, you will store these groups in easily accessible containers. Finally, when you label your containers, you ensure everything is labeled correctly.
This requires employees to critically evaluate how they work. Employees should understand why they do the tasks they do, and then decide if there are better ways to accomplish them. They will need to develop new skills and techniques in order for the 5S system to be implemented.
The 5S method not only increases efficiency but also boosts morale and teamwork. They will feel motivated to strive for higher levels of efficiency once they start to see results.