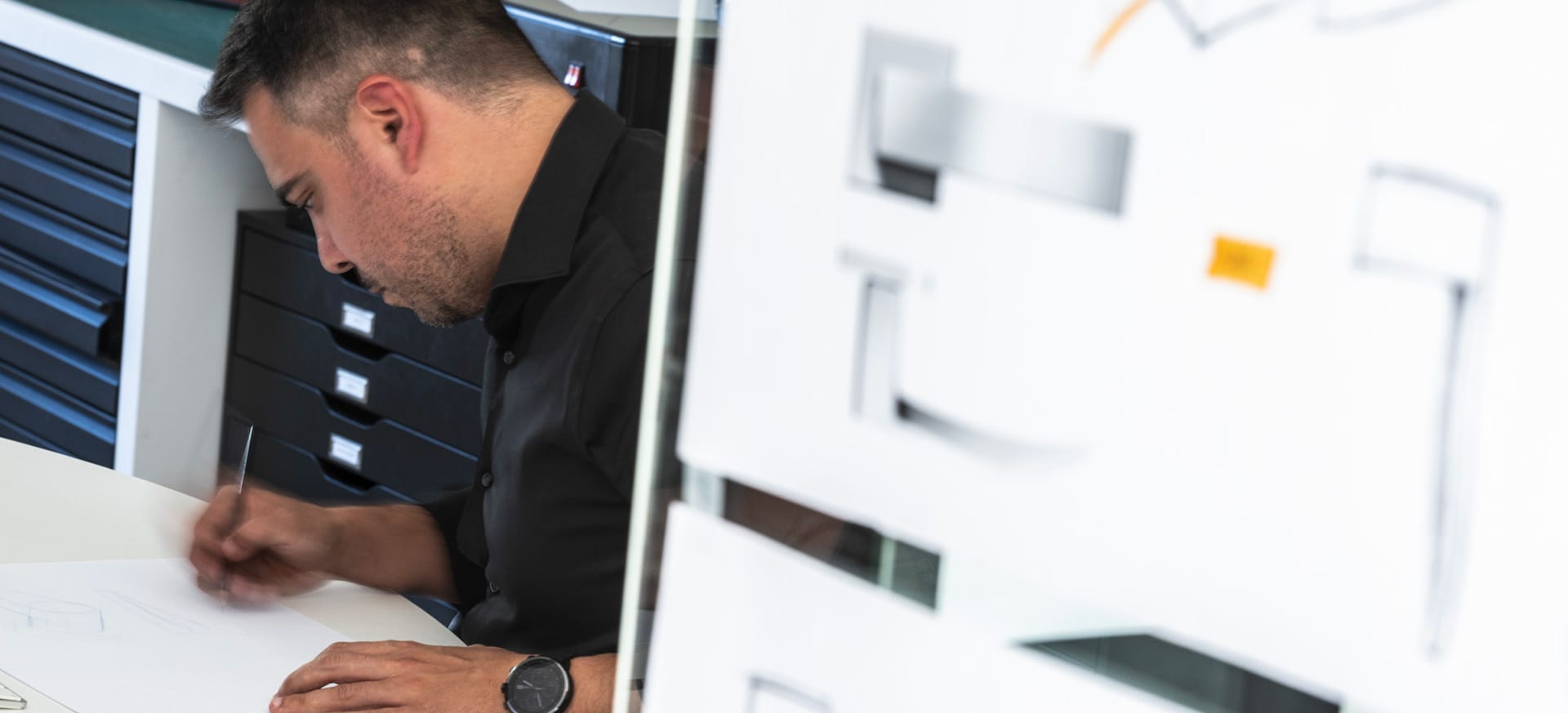
A paper company produces paper, such as paperboard, tissue paper, and newsprint. Paper companies can also manufacture packaging like bags and boxes for shipping. These firms are generally based in America.
The paper industry in the United States is a major part of our economy. The paper industry employs thousands of people and produces goods worth billions each year. Its products can be found in every aspect of life, from consumer goods to commercial services and industrial applications.
Paper companies are headquartered in many different regions of the United States. Some are regionally oriented and others specialize in specific products.
Regardless of the region, these paper companies have a common goal: to create and provide products that people use in their everyday lives. Some of these companies also place a high priority on sustainability.
International Paper, and WestRock are two of the largest paper companies in USA. Both companies are ranked in the Fortune 500 and rank among the largest paper companies in the world.
International Paper's dominance in the US paper industry can be attributed to its extensive portfolio of forest land. It owns more than 42 millions acres of forests and has a variety of pulp, sheet, and containerboard manufacturing facilities in North America.
International Paper's strong focus on diversification is one of the reasons why it dominates in the industry. A diverse workforce helps employees work together.
A diverse workforce allows companies to better understand their clients and prospects.
It can also help them improve their financial performance by reducing costs and lowering expenses. They can improve their financial performance through a reduction in costs and expenses.
The diversity of their workforce can also be a great way to attract and retain good workers. More women and minorities within a company will improve morale. This can be especially important for companies dealing with globalization, economic growth and other issues.
With a focus on sustainable development, these companies are implementing policies that help reduce environmental impact and boost energy efficiency. These companies are working with their suppliers on ways to reduce waste, and to increase recycling.
FAQ
Do we need to know about Manufacturing Processes before learning about Logistics?
No. It doesn't matter if you don't know anything about manufacturing before you learn about logistics. It is important to know about the manufacturing processes in order to understand how logistics works.
How is a production manager different from a producer planner?
The major difference between a Production Planner and a Project Manager is that a Project Manager is often the person responsible for organizing and planning the entire project. While a Production Planner is involved mainly in the planning stage,
Why is logistics important in manufacturing
Logistics are an essential part of any business. They are essential to any business's success.
Logistics play an important role in reducing costs as well as increasing efficiency.
Statistics
- According to a Statista study, U.S. businesses spent $1.63 trillion on logistics in 2019, moving goods from origin to end user through various supply chain network segments. (netsuite.com)
- (2:04) MTO is a production technique wherein products are customized according to customer specifications, and production only starts after an order is received. (oracle.com)
- Job #1 is delivering the ordered product according to specifications: color, size, brand, and quantity. (netsuite.com)
- It's estimated that 10.8% of the U.S. GDP in 2020 was contributed to manufacturing. (investopedia.com)
- You can multiply the result by 100 to get the total percent of monthly overhead. (investopedia.com)
External Links
How To
How to Use Six Sigma in Manufacturing
Six Sigma can be described as "the use of statistical process control (SPC), techniques to achieve continuous improvement." Motorola's Quality Improvement Department, Tokyo, Japan, developed it in 1986. Six Sigma's basic concept is to improve quality and eliminate defects through standardization. Many companies have adopted Six Sigma in recent years because they believe that there are no perfect products and services. Six Sigma's main objective is to reduce variations from the production average. If you take a sample and compare it with the average, you will be able to determine how much of the production process is different from the norm. If the deviation is excessive, it's likely that something needs to be fixed.
Understanding how your business' variability is a key step towards Six Sigma implementation is the first. Once you understand this, you can then identify the causes of variation. Also, you will need to identify the sources of variation. Random variations happen when people make errors; systematic variations are caused externally. You could consider random variations if some widgets fall off the assembly lines. However, if you notice that every time you assemble a widget, it always falls apart at exactly the same place, then that would be a systematic problem.
Once you've identified the problem areas you need to find solutions. That solution might involve changing the way you do things or redesigning the process altogether. Once you have implemented the changes, it is important to test them again to ensure they work. If they don't work, you will need to go back to the drawing boards and create a new plan.