
A wide variety of skills are required for railway logistics jobs. While some positions are simple to learn, others require years of experience and classroom training. These jobs require high levels of product and computer knowledge. Some jobs may require extensive overseas travel.
A transport logistics specialist tries to make sense of the logistics world, coordinating the transportation of materials or people. They may also be able to assess the efficiency or solve specific problems. This could be a mechanical check, or determining the best route to transport a specific cargo.
The job of the rail logistics manager is to ensure that trains and other transport modes are well-equipped and operate on time. They also need to make sure that trains are compliant with safety regulations. This job will often involve traveling from place to place to deliver freight. This is just a part of the job.
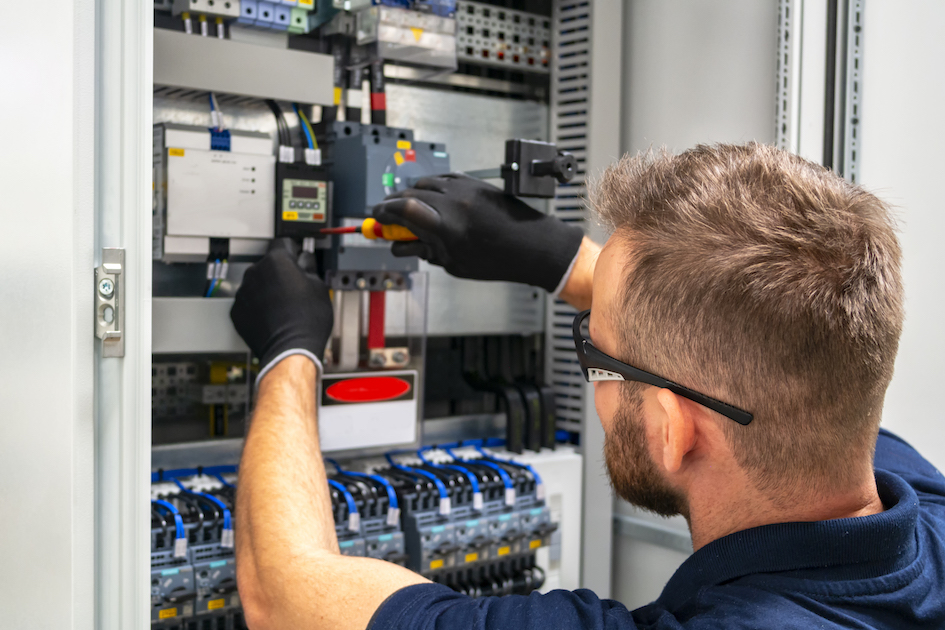
Another entry level position in the industry is that of an intermodal dispatcher. This person coordinates the schedules of several drivers and a shipping firm. The person coordinates the schedule of a group of drivers and a shipping company. It is not uncommon for this position to include administrative duties as well.
An individual who is a railway logistics director may choose to work for a private business or government agency. These roles offer career development opportunities and a good pay. On average, you can earn approximately $45,000 per annum. In addition, a bachelor's degree isn't necessary for many of these jobs. Despite the high wages, the average rail salary remains quite low.
Logistics titles that are commonly used include logistics coordinator, logistics analyst, and logistics manager. These are all vital positions. Each of these roles is important, and each one has its advantages. But there is a chance your skills are better used in one role than in another.
Logistics managers must be able and willing to negotiate the best rates or terms for their clients' transportation needs. This involves analysing the availability of equipment, services, negotiating and analyzing service level. They must also be able apply basic transport management concepts to increase the efficiency of their company’s logistics processes.
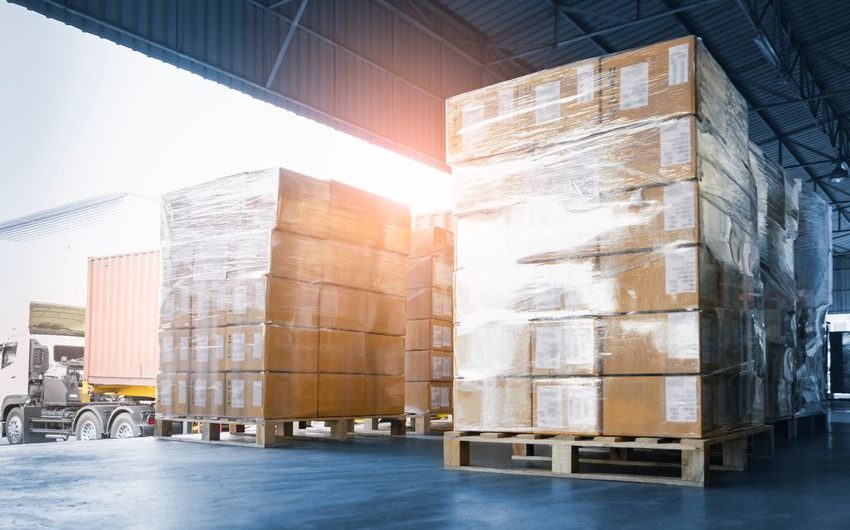
Rail logistics managers might oversee the installation of a state of the art tracking system to track and deliver goods on time. A tracking system may be used to alert customers about the current location of a shipment.
Sometimes, a rail logistics manager can be called upon to give advice on optimizing the transportation process. This will enable them to achieve faster results for their clients.
Many of these roles can be learned through on the job training and experience. Rail logistics coordinators, on the other side, require a bachelor's and years of relevant experience.
FAQ
Is automation necessary in manufacturing?
Automation is important not only for manufacturers but also for service providers. It allows them provide faster and more efficient services. It also helps to reduce costs and improve productivity.
What do we need to know about Manufacturing Processes in order to learn more about Logistics?
No. It doesn't matter if you don't know anything about manufacturing before you learn about logistics. Knowing about manufacturing processes will help you understand how logistics works.
Why automate your warehouse
Automation has become increasingly important in modern warehousing. The rise of e-commerce has led to increased demand for faster delivery times and more efficient processes.
Warehouses need to adapt quickly to meet changing needs. In order to do this, they need to invest in technology. The benefits of automating warehouses are numerous. These are just a few reasons to invest in automation.
-
Increases throughput/productivity
-
Reduces errors
-
Improves accuracy
-
Boosts safety
-
Eliminates bottlenecks
-
This allows companies to scale easily
-
Makes workers more efficient
-
The warehouse can be viewed from all angles.
-
Enhances customer experience
-
Improves employee satisfaction
-
Minimizes downtime and increases uptime
-
Ensures quality products are delivered on time
-
Eliminates human error
-
This helps to ensure compliance with regulations
What are the differences between these four types?
Manufacturing refers the process of turning raw materials into useful products with machines and processes. Manufacturing involves many activities, including designing, building, testing and packaging, shipping, selling, service, and so on.
What are the 7 R's of logistics?
The acronym 7R's of Logistic is an acronym that stands for seven fundamental principles of logistics management. It was developed by the International Association of Business Logisticians (IABL) and published in 2004 as part of its "Seven Principles of Logistics Management" series.
The acronym is composed of the following letters.
-
Responsible – ensure that all actions are legal and don't cause harm to anyone else.
-
Reliable - You can have confidence that you will fulfill your promises.
-
Be responsible - Use resources efficiently and avoid wasting them.
-
Realistic - Consider all aspects of operations, including environmental impact and cost effectiveness.
-
Respectful – Treat others fairly and equitably.
-
Responsive - Look for ways to save time and increase productivity.
-
Recognizable provides value-added products and services to customers
Statistics
- According to a Statista study, U.S. businesses spent $1.63 trillion on logistics in 2019, moving goods from origin to end user through various supply chain network segments. (netsuite.com)
- [54][55] These are the top 50 countries by the total value of manufacturing output in US dollars for its noted year according to World Bank.[56] (en.wikipedia.org)
- You can multiply the result by 100 to get the total percent of monthly overhead. (investopedia.com)
- Many factories witnessed a 30% increase in output due to the shift to electric motors. (en.wikipedia.org)
- According to the United Nations Industrial Development Organization (UNIDO), China is the top manufacturer worldwide by 2019 output, producing 28.7% of the total global manufacturing output, followed by the United States, Japan, Germany, and India.[52][53] (en.wikipedia.org)
External Links
How To
Six Sigma in Manufacturing:
Six Sigma refers to "the application and control of statistical processes (SPC) techniques in order to achieve continuous improvement." Motorola's Quality Improvement Department created Six Sigma at their Tokyo plant, Japan in 1986. Six Sigma's core idea is to improve the quality of processes by standardizing and eliminating defects. This method has been adopted by many companies in recent years as they believe there are no perfect products or services. Six Sigma's main objective is to reduce variations from the production average. You can calculate the percentage of deviation from the norm by taking a sample of your product and comparing it to the average. If the deviation is excessive, it's likely that something needs to be fixed.
Understanding the nature of variability in your business is the first step to Six Sigma. Once you have a good understanding of the basics, you can identify potential sources of variation. These variations can also be classified as random or systematic. Random variations are caused when people make mistakes. While systematic variations are caused outside of the process, they can occur. These are, for instance, random variations that occur when widgets are made and some fall off the production line. You might notice that your widgets always fall apart at the same place every time you put them together.
Once you identify the problem areas, it is time to create solutions. You might need to change the way you work or completely redesign the process. Test them again once you've implemented the changes. If they didn't work, then you'll need to go back to the drawing board and come up with another plan.