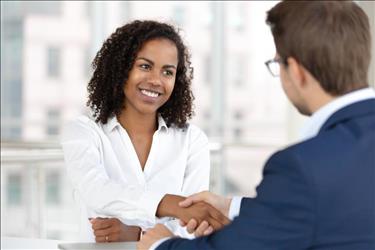
Visual management is the act of using visual signals to convey information. As information can be instantly identified, this process increases efficiency and clarity. There are several kinds of visual control. Here are some examples. You can also read about visual control in Lean manufacturing. Read on to learn more. This method is a great tool to get your business on track with lean production.
Lean manufacturing
Andon is a Japanese term for status-display visualization. It is one of many methods for visual management in lean manufacturing. This method helps workers and supervisors see work-in-progress, process flow, and other vital information. Visual management also allows you to label workspaces, materials and parts. It can help identify inefficiencies, streamline processes and improve efficiency. Below are some of the many benefits of visual control in lean manufacturing.
Lean methodology is incomplete without visible tools that allow for visual management. Operators and supervisors can identify waste and improve process flow to avoid mistakes. It can also reduce safety concerns. Forklift drivers can stay in the right areas by looking at floor markings and other visual indicators. By using visual management in lean manufacturing, workers can work more efficiently. Visual management can reduce waste as well as minimize safety risks.
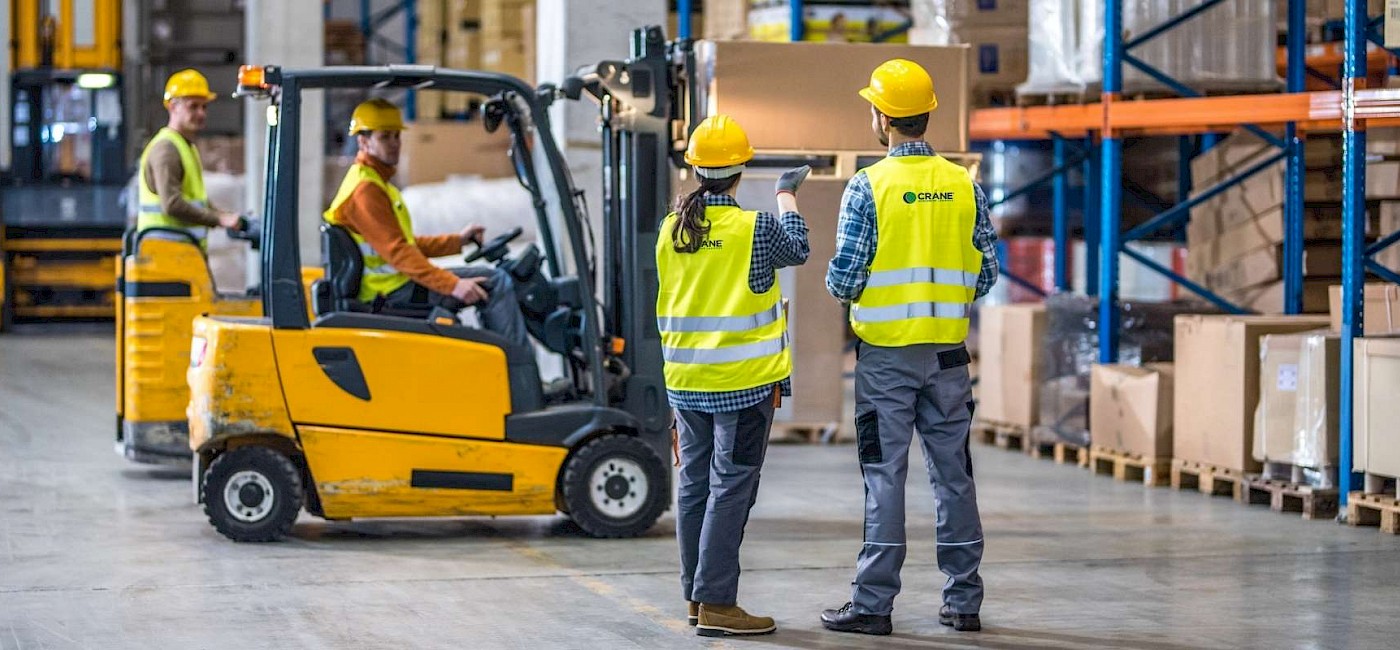
Process control charts
Process control charts can help you visualize performance metrics, establish a baseline and improve output. These charts help operators, managers, and other stakeholders to get on the same page. They identify common causes of variation, set the right path for improvement, and help them communicate with each other. These charts are particularly useful for processes that are out of control because they exhibit unusual patterns of variation. These charts can be useful for visual management as they are easy to create and can be used in order to visualize any system or process.
The control chart serves the primary purpose of tracking process performance over time. These charts provide information about the sequence of measurements and samples taken. Managers can see if the process remains stable or not. These charts can also be used for analytic purposes to identify and propose solutions. A line segment is a segment that connects the centerline of a control chart. This allows an operator to easily compare the process's performance to its baseline. The control limits generally have three standard deviations between the centerline and the edge.
FIFO lane
FIFO lanes can improve throughput and system utilization. You can think of a factory line or a fast food counter. Many of you will have been frustrated by the long lines that can be formed to get your food. FiFo lane allows you to manage work flow and establish priority in lines by using visual management. You can define these lanes by placing painted lines on the floor, markings on roller conveyors, and clearly marked shelf spaces. The first job that arrives from Process A would be placed in the first FIFO lane position. The next job would go into the open position.
Time registration is one way to improve FIFO lane visual control. Employees can track the date and time that carts are placed in a FIFO lane by recording the time and date. Some employees use digital clocks to count the number of products immediately after putting them in the FIFO lane. To record time on carts you can use whiteboard stickers. These whiteboard stickers can be used to indicate the order of each step.
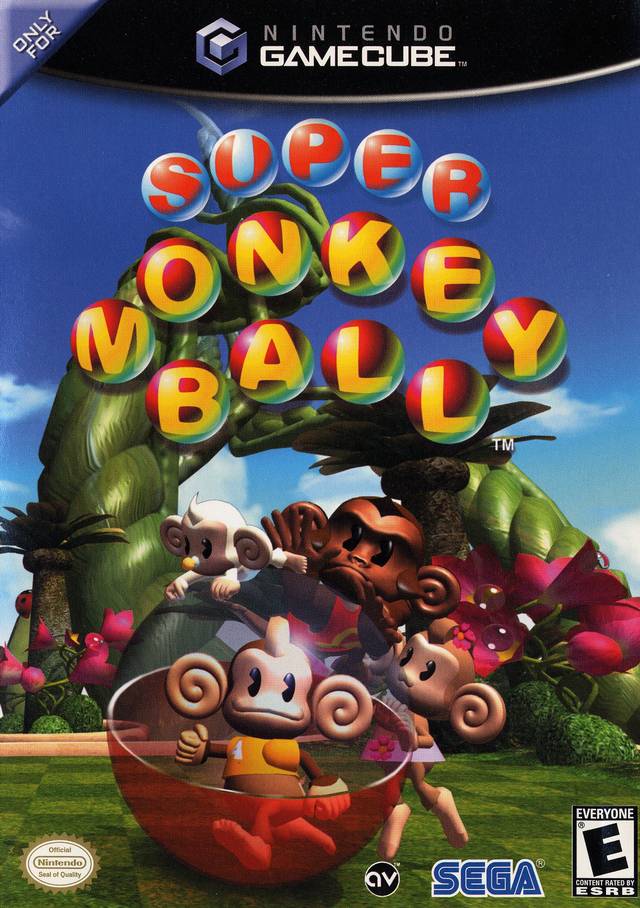
Lean daily management board
The Lean Daily Management Board was created by a multidisciplinary team based on five predetermined metrics: patient outcomes, documentation adherence, employee engagement, and productivity. This team met every day to review progress in each area. To check each day's activity, including medication adherence and falls, the team used checklists. They also used a problem solving tool to respond to any fallouts. Initial data collected January 2014 revealed a medication scan rate 75% and a rate of fall of 1.32/1000 days. These data are not applicable to patient care and continuing education.
Daily management allows for a more visible view of the process and allows for managers to address problems as they arise. Poor performers will not accept more work. Poor performers should make stretching work visible so they can account for extra time and effort. Even though daily management isn’t intended to be punishing, it will highlight any inefficient or ineffective processes. People issues should be addressed for those who can't point out a process's failure.
FAQ
What skills are required to be a production manager?
Being a production planner is not easy. You need to be organized and flexible. It is also important to be able communicate with colleagues and clients.
What is the role of a production manager?
Production planners ensure that all project aspects are completed on time, within budget and within the scope. They make sure that the product and services meet client expectations.
What is the difference in Production Planning and Scheduling, you ask?
Production Planning (PP), or production planning, is the process by which you determine what products are needed at any given time. This is done through forecasting demand and identifying production capacities.
Scheduling is the process of assigning specific dates to tasks so they can be completed within the specified timeframe.
What are the requirements to start a logistics business?
To be a successful businessman in logistics, you will need many skills and knowledge. You must have good communication skills to interact effectively with your clients and suppliers. You will need to know how to interpret data and draw conclusions. You will need to be able handle pressure well and work in stressful situations. You need to be innovative and creative to come up with new ways to increase efficiency. You will need strong leadership skills to motivate and direct your team members towards achieving their organizational goals.
You should also be organized and efficient to meet tight deadlines.
Are there any Manufacturing Processes that we should know before we can learn about Logistics?
No. It doesn't matter if you don't know anything about manufacturing before you learn about logistics. But, being familiar with manufacturing processes will give you a better understanding about how logistics works.
How can we increase manufacturing efficiency?
First, we need to identify which factors are most critical in affecting production times. We must then find ways that we can improve these factors. If you don't know where to start, then think about which factor(s) have the biggest impact on production time. Once you've identified them all, find solutions to each one.
Statistics
- It's estimated that 10.8% of the U.S. GDP in 2020 was contributed to manufacturing. (investopedia.com)
- According to the United Nations Industrial Development Organization (UNIDO), China is the top manufacturer worldwide by 2019 output, producing 28.7% of the total global manufacturing output, followed by the United States, Japan, Germany, and India.[52][53] (en.wikipedia.org)
- [54][55] These are the top 50 countries by the total value of manufacturing output in US dollars for its noted year according to World Bank.[56] (en.wikipedia.org)
- In the United States, for example, manufacturing makes up 15% of the economic output. (twi-global.com)
- According to a Statista study, U.S. businesses spent $1.63 trillion on logistics in 2019, moving goods from origin to end user through various supply chain network segments. (netsuite.com)
External Links
How To
How to Use Lean Manufacturing in the Production of Goods
Lean manufacturing is a management system that aims at increasing efficiency and reducing waste. It was developed by Taiichi Okono in Japan, during the 1970s & 1980s. TPS founder Kanji Takoda awarded him the Toyota Production System Award (TPS). Michael L. Watkins published the original book on lean manufacturing, "The Machine That Changed the World," in 1990.
Lean manufacturing is often defined as a set of principles used to improve the quality, speed, and cost of products and services. It is about eliminating defects and waste from all stages of the value stream. The five-steps of Lean Manufacturing are just-in time (JIT), zero defect and total productive maintenance (TPM), as well as 5S. Lean manufacturing eliminates non-value-added tasks like inspection, rework, waiting.
Lean manufacturing can help companies improve their product quality and reduce costs. Additionally, it helps them achieve their goals more quickly and reduces employee turnover. Lean manufacturing can be used to manage all aspects of the value chain. Customers, suppliers, distributors, retailers and employees are all included. Lean manufacturing can be found in many industries. Toyota's philosophy is the foundation of its success in automotives, electronics and appliances, healthcare, chemical engineers, aerospace, paper and food, among other industries.
Five fundamental principles underlie lean manufacturing.
-
Define Value - Identify the value your business adds to society and what makes you different from competitors.
-
Reduce Waste – Eliminate all activities that don't add value throughout the supply chain.
-
Create Flow. Ensure that your work is uninterrupted and flows seamlessly.
-
Standardize & simplify - Make processes consistent and repeatable.
-
Build Relationships - Establish personal relationships with both internal and external stakeholders.
Lean manufacturing is not a new concept, but it has been gaining popularity over the last few years due to a renewed interest in the economy following the global financial crisis of 2008. Many businesses are now using lean manufacturing to improve their competitiveness. Economists think that lean manufacturing is a crucial factor in economic recovery.
With many benefits, lean manufacturing is becoming more common in the automotive industry. These include better customer satisfaction and lower inventory levels. They also result in lower operating costs.
You can apply Lean Manufacturing to virtually any aspect of your organization. Lean manufacturing is most useful in the production sector of an organisation because it ensures that each step in the value-chain is efficient and productive.
There are three types principally of lean manufacturing:
-
Just-in Time Manufacturing: This lean manufacturing method is commonly called "pull systems." JIT refers to a system in which components are assembled at the point of use instead of being produced ahead of time. This approach is designed to reduce lead times and increase the availability of components. It also reduces inventory.
-
Zero Defects Manufacturing: ZDM ensures that no defective units leave the manufacturing plant. You should repair any part that needs to be repaired during an assembly line. This is also true for finished products that require minor repairs before shipping.
-
Continuous Improvement: Continuous Improvement aims to improve efficiency by continually identifying problems and making adjustments to eliminate or minimize waste. Continuous Improvement (CI) involves continuous improvement in processes, people, tools, and infrastructure.