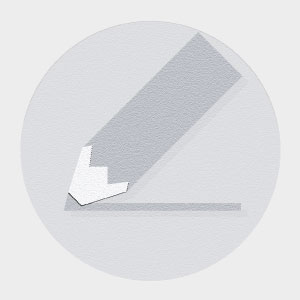
Despite the many benefits of lean manufacturing, there have been some challenges for companies trying to implement this strategy. Companies need to develop a comprehensive plan for overcoming these obstacles. Companies that have implemented Lean know that there are three key issues that hinder its success.
It doesn't matter what size a company may be, commitment to lean manufacturing is crucial for its success. Although there are no easy ways to measure how committed a company has been to lean manufacturing implementations, it is crucial that staff are familiarized with the changes and culture.
Also, it is important to make sure that resources are properly allocated. Many public organisations have reported that they waste allocated budgets by purchasing unnecessary items. Reports also indicate that some managers purchase equipment that isn't necessary to make use of the budget. This can create operational bottlenecks, leading to an inefficient implementation of lean manufacturing.
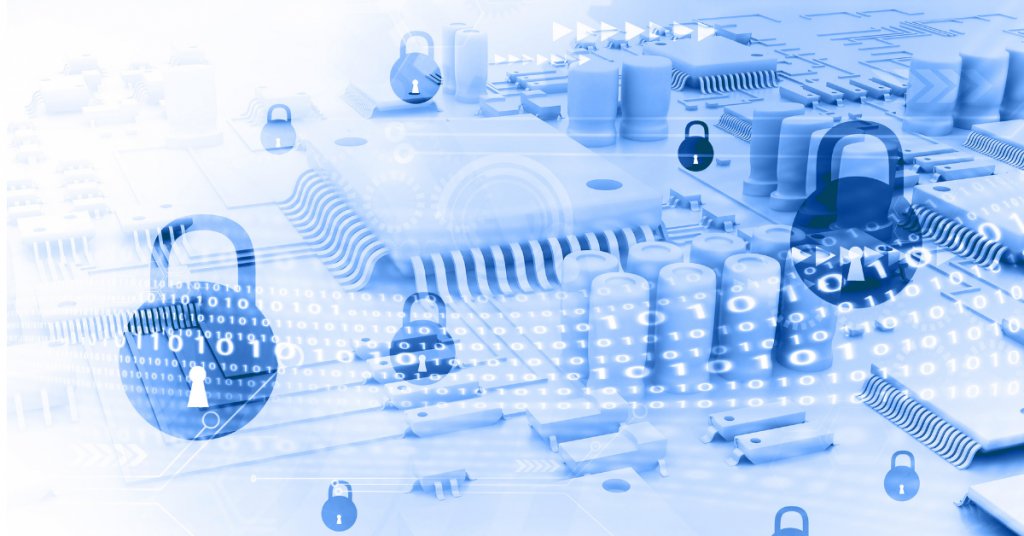
One of the biggest challenges in implementing lean manufacturing is resistance to cultural change. Many employees, especially those that have been with the company for a long time, are not comfortable with change. Some employees will wait for the majority to speak up and convince them to move in a new direction. In order to break through this resistance, management must communicate the benefits of the program and explain why the change is necessary.
Lack of a strategic plan to transform the company is another problem. While companies usually transform several business operations at once, it is important to maintain a long-term strategy. Companies can use this strategy to mentor and identify future leaders, improve their operations, and ensure that they remain competitive in the face technological advances. It helps identify operational bottlenecks and addresses growth opportunities.
This is not all. Training is essential to overcome resistance. Training is essential to help workers understand their roles and expectations. It also helps workers develop multi skills, which they can use to work more independently. Additionally, training helps workers improve their problem solving skills which will help them to sustain Lean through improved performance.
Managers must be open with workers in order to overcome resistance. Managers may put pressure on workers to follow instructions, but managers need to be open and honest with workers about why the change is needed. In some instances, managers were found to have given incorrect instructions to their workers, which resulted in ineffective implementation.
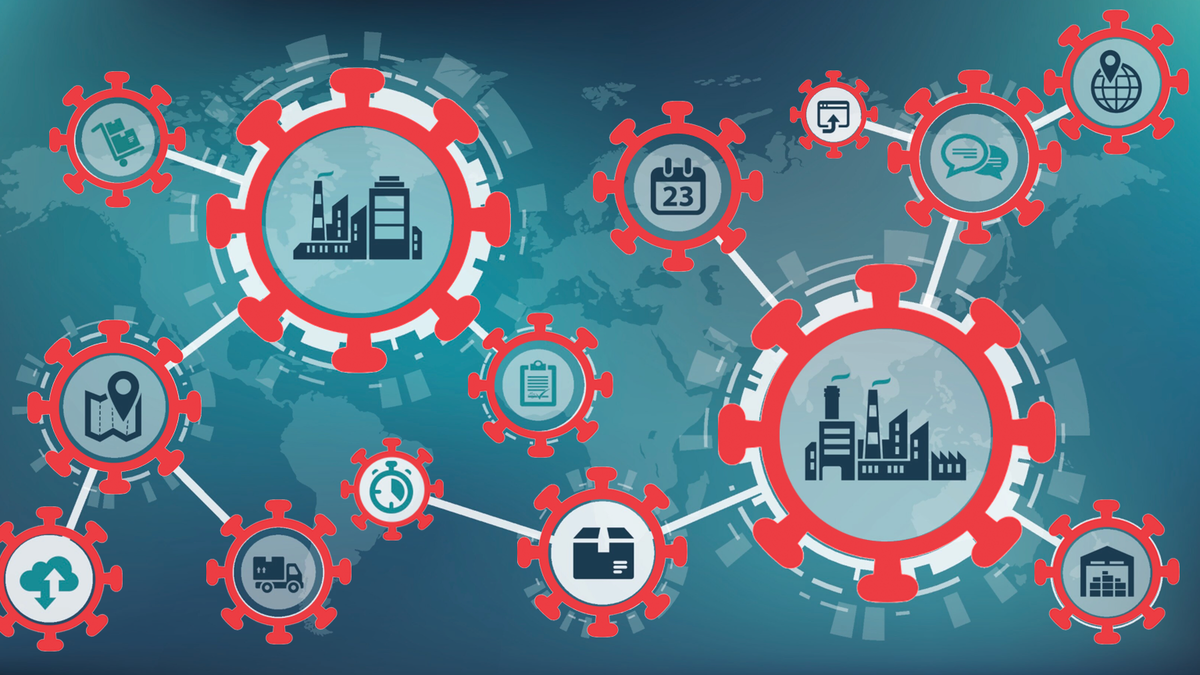
Managers, regardless of company size, must be present at the shop floor to help identify areas for improvement. Managers must also develop training modules and familiarize staff with new digital tools. These tools, including 5S (visual management), improve visual management.
Finally, it is important to develop and communicate a clear vision for the implementation of lean manufacturing. This vision should outline the responsibilities of employees and include a schedule to implement lean. It also includes a method for measuring success.
FAQ
What are the four types in manufacturing?
Manufacturing is the process of transforming raw materials into useful products using machines and processes. It can involve many activities like designing, manufacturing, testing packaging, shipping, selling and servicing.
How can we improve manufacturing efficiency?
First, identify the factors that affect production time. The next step is to identify the most important factors that affect production time. If you aren't sure where to begin, think about the factors that have the greatest impact on production time. Once you identify them, look for solutions.
Why automate your warehouse
Modern warehouses have become more dependent on automation. The rise of e-commerce has led to increased demand for faster delivery times and more efficient processes.
Warehouses need to adapt quickly to meet changing needs. Technology is essential for warehouses to be able to adapt quickly to changing needs. Automation warehouses can bring many benefits. These are some of the benefits that automation can bring to warehouses:
-
Increases throughput/productivity
-
Reduces errors
-
Increases accuracy
-
Safety enhancements
-
Eliminates bottlenecks
-
Allows companies scale more easily
-
Makes workers more efficient
-
This gives you visibility into what happens in the warehouse
-
Enhances customer experience
-
Improves employee satisfaction
-
It reduces downtime, and increases uptime
-
High quality products delivered on-time
-
Removes human error
-
It helps ensure compliance with regulations
Statistics
- Job #1 is delivering the ordered product according to specifications: color, size, brand, and quantity. (netsuite.com)
- Many factories witnessed a 30% increase in output due to the shift to electric motors. (en.wikipedia.org)
- It's estimated that 10.8% of the U.S. GDP in 2020 was contributed to manufacturing. (investopedia.com)
- In the United States, for example, manufacturing makes up 15% of the economic output. (twi-global.com)
- (2:04) MTO is a production technique wherein products are customized according to customer specifications, and production only starts after an order is received. (oracle.com)
External Links
How To
How to use the Just-In Time Method in Production
Just-intime (JIT), which is a method to minimize costs and maximize efficiency in business process, is one way. It allows you to get the right amount resources at the right time. This means you only pay what you use. Frederick Taylor first coined this term while working in the early 1900s as a foreman. He observed how workers were paid overtime if there were delays in their work. He decided that workers would be more productive if they had enough time to complete their work before they started to work.
JIT is about planning ahead. You should have all the necessary resources ready to go so that you don’t waste money. You should also look at the entire project from start to finish and make sure that you have sufficient resources available to deal with any problems that arise during the course of your project. You can anticipate problems and have enough equipment and people available to fix them. This way, you won't end up paying extra money for things that weren't really necessary.
There are many JIT methods.
-
Demand-driven: This type of JIT allows you to order the parts/materials required for your project on a regular basis. This will allow for you to track the material that you have left after using it. It will also allow you to predict how long it takes to produce more.
-
Inventory-based: You stock materials in advance to make your projects easier. This allows you to predict how much you can expect to sell.
-
Project-driven : This is a method where you make sure that enough money is set aside to pay the project's cost. When you know how much you need, you'll purchase the appropriate amount of materials.
-
Resource-based JIT : This is probably the most popular type of JIT. You assign certain resources based off demand. You might assign more people to help with orders if there are many. If there aren't many orders, you will assign fewer people.
-
Cost-based: This is the same as resource-based except that you don't care how many people there are but how much each one of them costs.
-
Price-based: This is a variant of cost-based. However, instead of focusing on the individual workers' costs, this looks at the total price of the company.
-
Material-based - This is a variant of cost-based. But instead of looking at the total company cost, you focus on how much raw material you spend per year.
-
Time-based JIT: A variation on resource-based JIT. Instead of focusing solely on the amount each employee costs, focus on how long it takes for the project to be completed.
-
Quality-based JIT - This is another form of resource-based JIT. Instead of worrying about the costs of each employee or how long it takes for something to be made, you should think about how quality your product is.
-
Value-based JIT is the newest form of JIT. In this instance, you are not concerned about the product's performance or meeting customer expectations. Instead, you are focused on adding value to the marketplace.
-
Stock-based: This is an inventory-based method that focuses on the actual number of items being produced at any given time. This is used to increase production and minimize inventory.
-
Just-in-time (JIT) planning: This is a combination of JIT and supply chain management. It is the process of scheduling components' delivery as soon as they have been ordered. It's important as it reduces leadtimes and increases throughput.