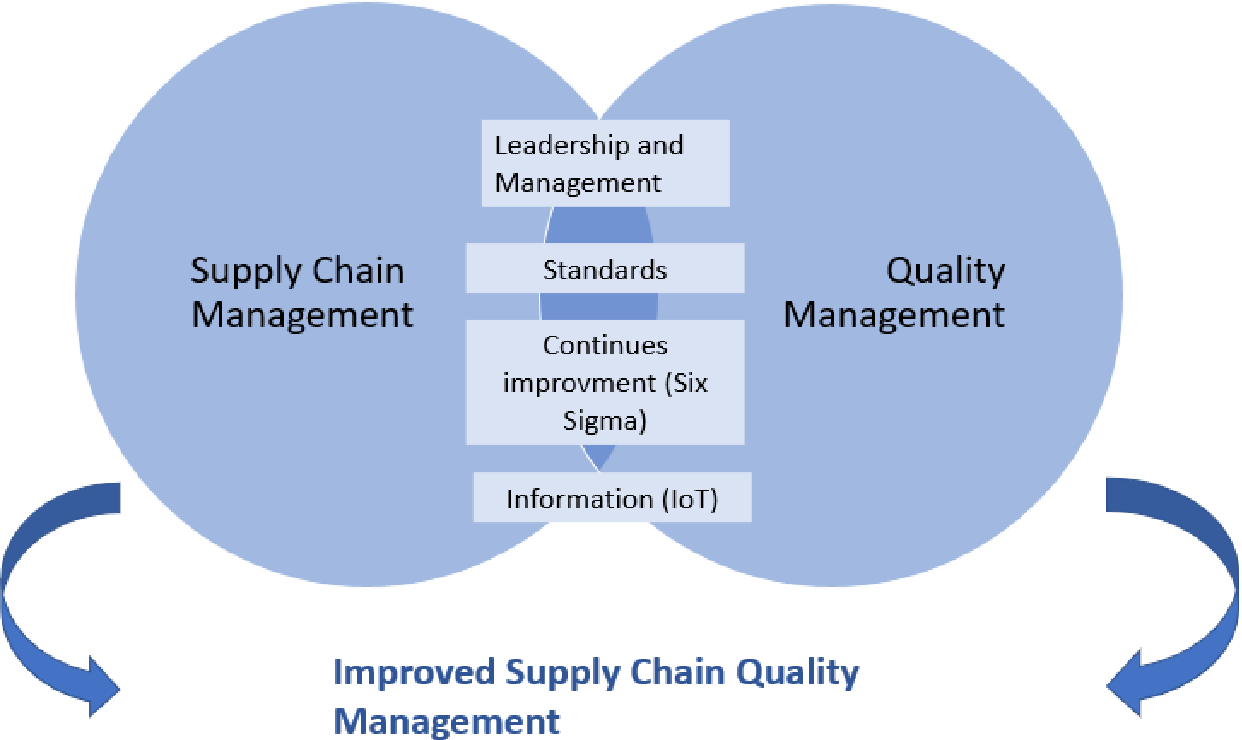
When looking at the economics of consumer goods, there are two categories: durable goods and non-durable goods. Durable goods do not wear down quickly and have a long lifespan, whereas non-durables are short lived and require frequent replacement.
Cars and clothes are examples of durable goods that last a very long time. This makes durable goods more expensive, but they are also considered to be safer because they can't be worn out as easily or consumed as quickly as non-durables.
This distinction between durables and non-durables is important to both investors and economists, because it helps them understand the economy quickly. When the economy is expanding, households and businesses are more likely to purchase durable goods, while during a recession they tend to hold back on these purchases.
The durable goods report is a monthly economic indicator that provides an insight into the U.S. manufacturing sector and the economy as a whole.
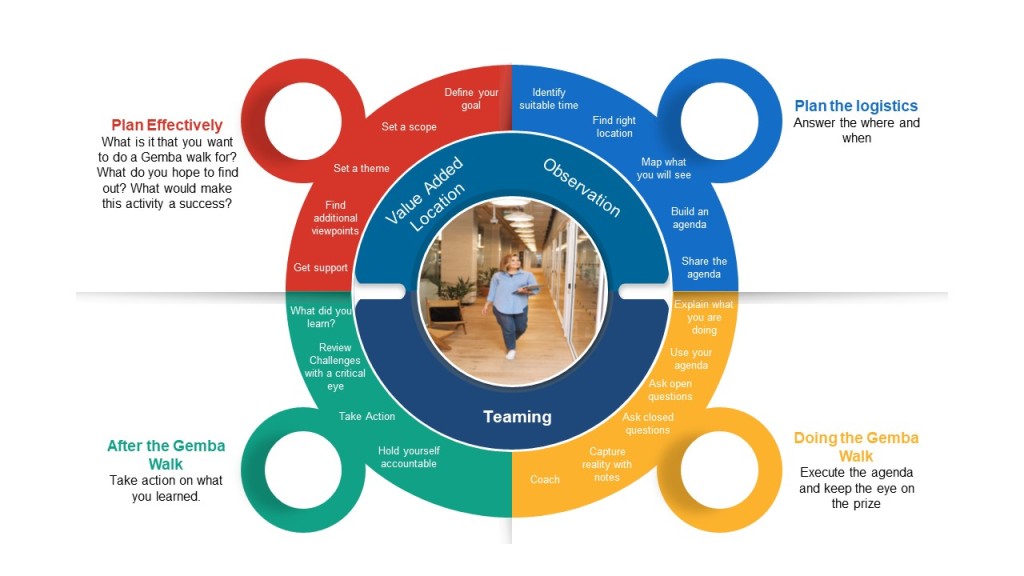
The manufacturing industry will expect to grow in the future if the volume of durable good orders increases. This can lead to an increase in the number of workers employed by manufacturers, thereby strengthening the overall economy. On the other hand, when the durable goods orders report decreases, it suggests that manufacturers aren't as optimistic about the future.
Durable goods are tangible products that don't wear out quickly, breakdown or rot. It's not as frequently replaced and it can be used many times before its value fades.
Appliances, clothes, computers, furnishings, and cars are all examples of durables. These durable goods can be used repeatedly before they begin to degrade.
Investing in durable goods is important for the economy. These purchases are an indication that companies and people are looking forward to a better economy.
They can also increase employment which will increase productivity over time and reduce costs. Durable goods are also more environmentally friendly than non-durables because they use less energy.

The durable goods orders report is a monthly economic indicator that measures the demand for U.S.-manufactured durable goods, domestically and internationally. It is published by United States Census Bureau as a leading economy indicator.
The durable goods order report is used by investors and economists to determine the state of the economic system. When the durable goods orders report increases, it indicates that consumers are more interested in purchasing products and services that will last longer than three years.
The decline in durable goods orders indicates that consumers don't want to buy products or services that are expected to last less than three years.
The durable goods survey is a monthly economy report that measures durable goods demand, which includes items that will last for more than 3 years. This report is an important economic indicator, as it gives a clear picture about how businesses are faring and what the future holds.
FAQ
How can excess manufacturing production be reduced?
In order to reduce excess production, you need to develop better inventory management methods. This would reduce time spent on activities such as purchasing, stocking, and maintaining excess stock. This could help us free up our time for other productive tasks.
Kanban systems are one way to achieve this. A Kanbanboard is a visual tool that allows you to keep track of the work being done. Work items are moved through various states to reach their destination in a Kanban system. Each state represents a different priority level.
For instance, when work moves from one stage to another, the current task is complete enough to be moved to the next stage. However, if a task is still at the beginning stages, it will remain so until it reaches the end of the process.
This keeps work moving and ensures no work is lost. Managers can monitor the work being done by Kanban boards to see what is happening at any given time. This data allows them adjust their workflow based upon real-time data.
Lean manufacturing is another option to control inventory levels. Lean manufacturing focuses on eliminating waste throughout the entire production chain. Waste includes anything that does not add value to the product. Here are some examples of common types.
-
Overproduction
-
Inventory
-
Unnecessary packaging
-
Overstock materials
These ideas will help manufacturers increase efficiency and lower costs.
What does "warehouse" mean?
A warehouse or storage facility is where goods are stored before they are sold. You can have it indoors or outdoors. It could be one or both.
What do we need to know about Manufacturing Processes in order to learn more about Logistics?
No. No. It is important to know about the manufacturing processes in order to understand how logistics works.
What is the role of a manager in manufacturing?
Manufacturing managers must ensure that manufacturing processes are efficient, effective, and cost-effective. They should be aware of any issues within the company and respond accordingly.
They should also be able and comfortable communicating with other departments like sales and marketing.
They should be up to date on the latest trends and be able apply this knowledge to increase productivity and efficiency.
Statistics
- Many factories witnessed a 30% increase in output due to the shift to electric motors. (en.wikipedia.org)
- [54][55] These are the top 50 countries by the total value of manufacturing output in US dollars for its noted year according to World Bank.[56] (en.wikipedia.org)
- According to a Statista study, U.S. businesses spent $1.63 trillion on logistics in 2019, moving goods from origin to end user through various supply chain network segments. (netsuite.com)
- According to the United Nations Industrial Development Organization (UNIDO), China is the top manufacturer worldwide by 2019 output, producing 28.7% of the total global manufacturing output, followed by the United States, Japan, Germany, and India.[52][53] (en.wikipedia.org)
- (2:04) MTO is a production technique wherein products are customized according to customer specifications, and production only starts after an order is received. (oracle.com)
External Links
How To
How to use the Just In-Time Production Method
Just-intime (JIT), which is a method to minimize costs and maximize efficiency in business process, is one way. It's the process of obtaining the right amount and timing of resources when you need them. This means that your only pay for the resources you actually use. Frederick Taylor was the first to coin this term. He developed it while working as a foreman during the early 1900s. He noticed that workers were often paid overtime when they had to work late. He then concluded that if he could ensure that workers had enough time to do their job before starting to work, this would improve productivity.
JIT is a way to plan ahead and make sure you don't waste any money. Also, you should look at the whole project from start-to-finish and make sure you have the resources necessary to address any issues. If you anticipate that there might be problems, you'll have enough people and equipment to fix them. This way you won't be spending more on things that aren’t really needed.
There are many JIT methods.
-
Demand-driven: This type of JIT allows you to order the parts/materials required for your project on a regular basis. This will allow you to track how much material you have left over after using it. This will allow to you estimate the time it will take for more to be produced.
-
Inventory-based: This is a type where you stock the materials required for your projects in advance. This allows you to forecast how much you will sell.
-
Project-driven: This approach involves setting aside sufficient funds to cover your project's costs. When you know how much you need, you'll purchase the appropriate amount of materials.
-
Resource-based JIT is the most widespread form. This is where you assign resources based upon demand. You will, for example, assign more staff to deal with large orders. If there aren't many orders, you will assign fewer people.
-
Cost-based : This is similar in concept to resource-based. But here, you aren't concerned about how many people your company has but how much each individual costs.
-
Price-based: This approach is very similar to the cost-based method except that you don't look at individual workers costs but the total cost of the company.
-
Material-based: This is very similar to cost-based but instead of looking at total costs of the company you are concerned with how many raw materials you use on an average.
-
Time-based JIT: This is another variant of resource-based JIT. Instead of focusing solely on the amount each employee costs, focus on how long it takes for the project to be completed.
-
Quality-based JIT is another variant of resource-based JIT. Instead of looking at the labor costs and time it takes to make a product, think about its quality.
-
Value-based JIT: One of the most recent forms of JIT. In this instance, you are not concerned about the product's performance or meeting customer expectations. Instead, you focus on the added value that you provide to your market.
-
Stock-based: This inventory-based approach focuses on how many items are being produced at any one time. It is used when production goals are met while inventory is kept to a minimum.
-
Just-in-time planning (JIT): This is a combination JIT and supply-chain management. It refers to the process of scheduling the delivery of components as soon as they are ordered. It's important because it reduces lead times and increases throughput.