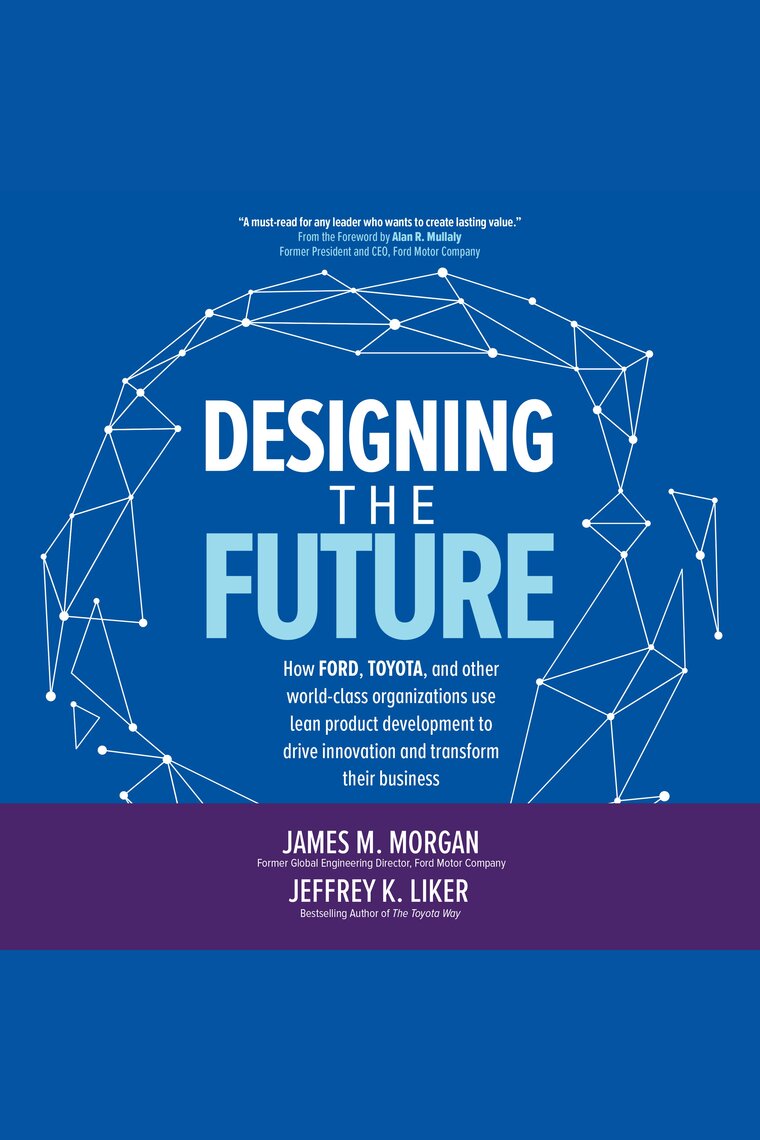
You need to consider manufacturing cost when making sure you produce a product that is financially viable. If you plan to sell wooden tabletop furniture, then you will need to purchase adhesives, wood, and other materials. For your products to last, you will need to be able find reliable suppliers of high quality raw materials. You could end up with a damaged item or lost revenue if you don't use the best quality raw materials.
The best way to determine manufacturing cost is to break it up into three main categories. Each of these costs will have an effect on the final cost of the product you are selling. One of the most important components in a manufacturing cost is its unit cost. This is the price it takes to produce an item. This number is a good way to begin, but it is not easy to determine.
When deciding the most cost-effective manufacturing method for your company, you can use either the units-per hour or unit-per–unit ratio as a guide. You can calculate the time it takes to create 5,000 wooden tables by taking the units-per-hour or unit-per–unit ratio.
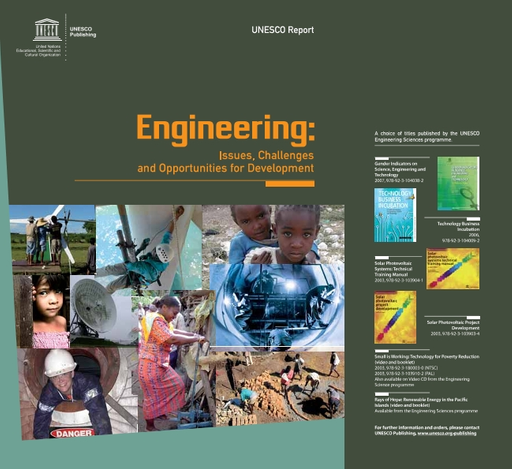
Budgeting for administrative and general expenses is essential in addition to direct labor costs and equipment manufacturing. Advertising costs, office supplies and rent are all possible. To comply with regulatory requirements, you will need to spend significant amounts of money. However, you can minimize the cost of these expenses by using online inventory control software to track production and forecast production.
Direct labor costs include wages paid to factory workers and employees involved in the preparation of goods for manufacturing. These may also include bookkeepers, sanitation personnel, maintenance staff, and other employees. In general, direct labor costs about $150 an hour.
Indirect costs, which are part manufacturing, include utilities bills and equipment maintenance. When calculating the unit-per-hour, you will need to calculate the costs of preparing the material, the work involved in assembling the items, and the costs for delivering the finished product to the customer. An overhead account for manufacturing will allow you to calculate your total costs and provide an estimate of your overhead for the upcoming fiscal year.
Consider the direct and indirect materials used to make a product. The materials used to manufacture a product include thread, wood, and cotton. Using low quality materials can lead to an inferior final product, and if you are a food manufacturer in certain parts of the world, you'll need to test your products to make sure they are safe to eat.
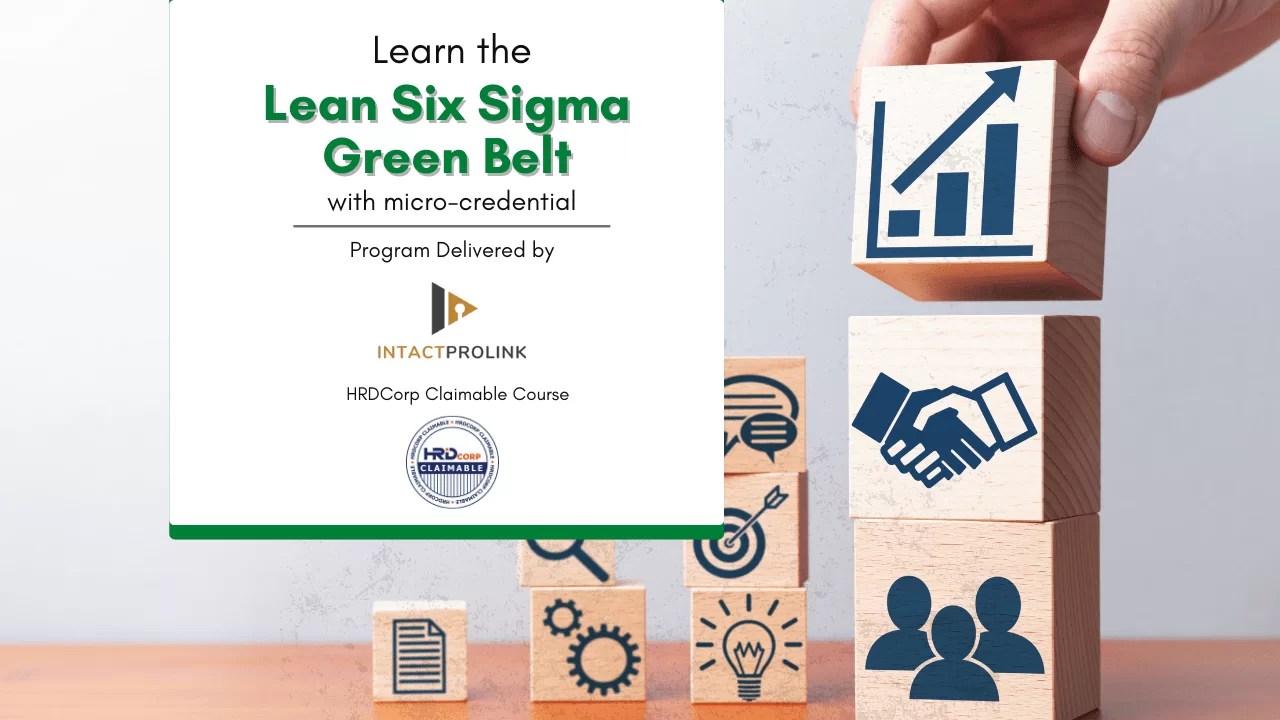
To determine whether you should produce a new product, you will need to know the unit-per–unit ratio and the manufacturing costs. It's also a good idea to know how much to charge for your products so that you can increase the profitability of your business.
FAQ
What does "warehouse" mean?
Warehouses and storage facilities are where goods are kept before being sold. You can have it indoors or outdoors. It could be one or both.
Why automate your factory?
Modern warehousing is becoming more automated. With the rise of ecommerce, there is a greater demand for faster delivery times as well as more efficient processes.
Warehouses need to adapt quickly to meet changing needs. In order to do this, they need to invest in technology. Automating warehouses has many benefits. These are some of the benefits that automation can bring to warehouses:
-
Increases throughput/productivity
-
Reduces errors
-
Improves accuracy
-
Safety enhancements
-
Eliminates bottlenecks
-
Companies can scale more easily
-
Workers are more productive
-
This gives you visibility into what happens in the warehouse
-
Enhances customer experience
-
Improves employee satisfaction
-
Minimizes downtime and increases uptime
-
You can be sure that high-quality products will arrive on time
-
Removes human error
-
Helps ensure compliance with regulations
How is a production manager different from a producer planner?
The difference between a product planner and project manager is that a planer is typically the one who organizes and plans the entire project. A production planner, however, is mostly involved in the planning stages.
What is the role of a production manager?
A production planner makes sure all project elements are delivered on schedule, within budget, as well as within the agreed scope. They also ensure that the product/service meets the client’s needs.
What are manufacturing and logistic?
Manufacturing refers to the process of making goods using raw materials and machines. Logistics covers all aspects involved in managing supply chains, including procurement and production planning. Sometimes manufacturing and logistics are combined to refer to a wider term that includes both the process of creating products as well as their delivery to customers.
Statistics
- In the United States, for example, manufacturing makes up 15% of the economic output. (twi-global.com)
- You can multiply the result by 100 to get the total percent of monthly overhead. (investopedia.com)
- In 2021, an estimated 12.1 million Americans work in the manufacturing sector.6 (investopedia.com)
- According to the United Nations Industrial Development Organization (UNIDO), China is the top manufacturer worldwide by 2019 output, producing 28.7% of the total global manufacturing output, followed by the United States, Japan, Germany, and India.[52][53] (en.wikipedia.org)
- Many factories witnessed a 30% increase in output due to the shift to electric motors. (en.wikipedia.org)
External Links
How To
Six Sigma in Manufacturing:
Six Sigma is defined as "the application of statistical process control (SPC) techniques to achieve continuous improvement." Motorola's Quality Improvement Department developed it at their Tokyo plant in Japan in 1986. Six Sigma's basic concept is to improve quality and eliminate defects through standardization. This method has been adopted by many companies in recent years as they believe there are no perfect products or services. Six Sigma aims to reduce variation in the production's mean value. This means that if you take a sample of your product, then measure its performance against the average, you can find out what percentage of the time the process deviates from the norm. If this deviation is too big, you know something needs fixing.
Understanding the dynamics of variability within your business is the first step in Six Sigma. Once you've understood that, you'll want to identify sources of variation. This will allow you to decide if these variations are random and systematic. Random variations occur when people do mistakes. Symmetrical variations are caused due to factors beyond the process. For example, if you're making widgets, and some of them fall off the assembly line, those would be considered random variations. If however, you notice that each time you assemble a widget it falls apart in exactly the same spot, that is a problem.
Once you've identified the problem areas you need to find solutions. It might mean changing the way you do business or redesigning it entirely. You should then test the changes again after they have been implemented. If they don't work, you will need to go back to the drawing boards and create a new plan.