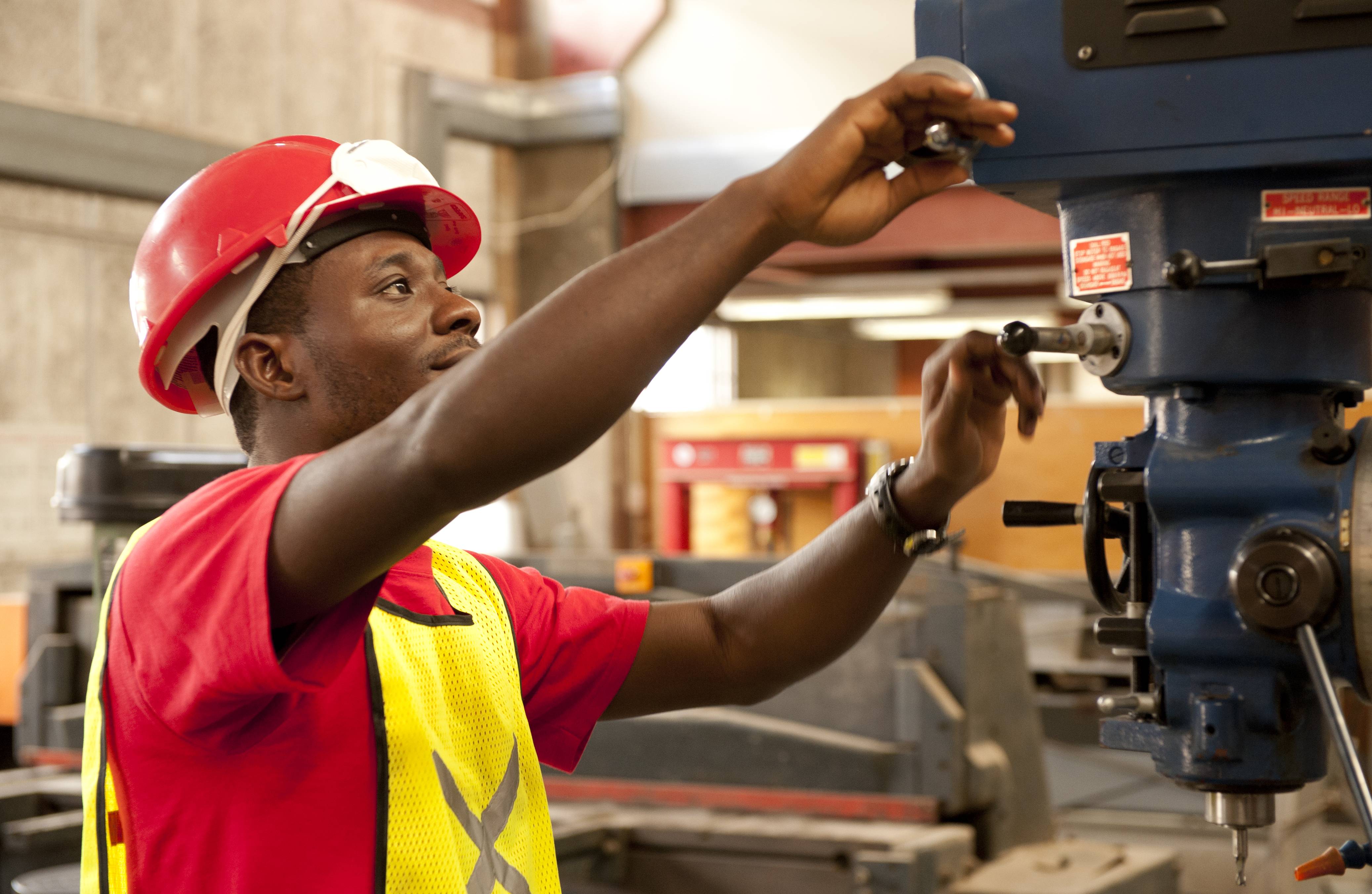
Advanced manufacturing is the application of new technology to improve products and processes. You can classify the technology used to achieve these results as "advanced", “innovative" or "cutting-edge". These industries are integrating innovative technologies into their manufacturing processes as they increase the number of advanced manufacturing companies. Here are some examples from advanced manufacturing. Below are some of most used technologies for advanced manufacturing.
Continuous production
The earliest description of continuous manufacturing dates back to the 1700s when it was used to make pig iron in blast furnaces. This concept has spread to many industries such as the automotive, food oil and refining industries, chemical industries, and pulp and papers industries. Today, continuous manufacturing has gained considerable traction in the biopharmaceutical industry, capturing the attention of leading CMOs and big pharma players.
Recent commentary by the FDA and its partner organizations discussed the benefits that continuous manufacturing can bring to the production of therapeutic protein. The legislation will create national centers that can help advance the field and create standards for companies. It is designed to assist the medical industry in improving the process of creating and utilizing medical products. Further, it would also encourage companies to use continuous manufacturing to develop and improve products. But it is essential to ensure that continuous manufacture processes are safe.
Automated processes
It is hard to overstate the benefits of automation in advanced manufacturing. Automation can be used to make the most out of floor space, while increasing production efficiency. Utilizing automation technologies and data collection, manufacturers can lower costs and increase productivity through better equipment use. Automation in the process industry also helps to save time and money. It is possible to invest a lot initially, but eventually it will improve the bottom line of a manufacturing firm.

Modern companies combine advanced manufacturing processes and automated processes. Audi is one example. They use automated welding and bonding processes to reduce their production time while also saving energy and weight. Advanced manufacturing systems, such as regenerative brakes in conveyor systems, are also used by them. 3D printing is the most recent advancement in manufacturing. Although it has been around since 1980s, it has just recently become mainstream. Why is 3D printing so appealing for manufacturers?
Internet of Things (IoT).
The IIoT revolution is transforming manufacturing through the use of sensors to monitor machines and their processes. These sensors collect data in different areas of the manufacturing process to feed into a central hub. Data is then analysed to aid in optimizing processes and eliminating waste. Advanced manufacturers have already begun to use IIoT sensors in order to optimize production processes. The IIoT industrial version is connected key fobs.
IIoT deployment needs a detailed roadmap and development capabilities in order to deploy use cases efficiently and scale effectively. This road map is from an automaker and shows three waves of deployment.
Cost-effectiveness
Advanced manufacturing is not always cheaper than traditional production. It is more likely that the traditional cost-benefit model is insufficient to assess economic benefits. A holistic model that includes both the costs and benefits of technology is possible to help identify new benefits and speed up decision-making. Munker and Schroer have developed a cost-benefit model that addresses key issues in AMS implementation.
Information technology advancements are quickly changing the face of manufacturing. Manufacturing systems are becoming more connected and intelligent. Meanwhile, cost pressure is putting increased focus on productivity and a company's ability to respond to customer needs. The adoption of modern manufacturing technologies will accelerate the development of new technologies and increase their cost-effectiveness. Further, the adoption of such technologies will likely accelerate as the industry continues to digitize.
Human error reduction
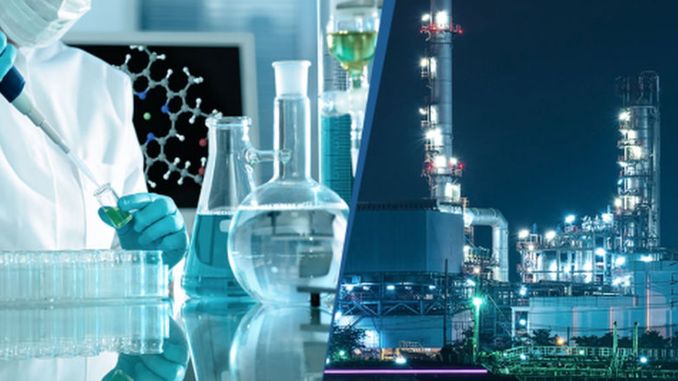
Even though humans are human, mistakes can still be made. The process of producing a product is often designed to prevent them from making any. Human error can happen when employees don't read or understand instructions. Pharmaceutical laboratories, for example, have to follow very specific procedures when they are making drugs. Sometimes, employees might believe that they have learned the process and are familiar with the precise amounts of ingredients. So they start to make the mixture, without ever consulting the written instructions.
Communication between senior and junior employees can help reduce human error. People will make mistakes if they are treated badly. Managers must not punish employees for asking questions. Employees should feel comfortable asking question and will not hesitate to ask for clarification if they are uncomfortable. Maintain a healthy dialog between junior and senior employees and resolve communication problems in a professional and courteous manner.
FAQ
What is the responsibility for a logistics manager
A logistics manager makes sure that all goods are delivered on-time and in good condition. This is done through his/her expertise and knowledge about the company's product range. He/she must also ensure sufficient stock to meet the demand.
Is automation necessary in manufacturing?
Not only are service providers and manufacturers important, but so is automation. Automation allows them to deliver services quicker and more efficiently. It helps them to lower costs by reducing human errors, and improving productivity.
What is the importance of logistics in manufacturing?
Logistics are an integral part any business. They can help you achieve great success by helping you manage product flow from raw material to finished goods.
Logistics play a key role in reducing expenses and increasing efficiency.
Statistics
- According to a Statista study, U.S. businesses spent $1.63 trillion on logistics in 2019, moving goods from origin to end user through various supply chain network segments. (netsuite.com)
- Many factories witnessed a 30% increase in output due to the shift to electric motors. (en.wikipedia.org)
- It's estimated that 10.8% of the U.S. GDP in 2020 was contributed to manufacturing. (investopedia.com)
- (2:04) MTO is a production technique wherein products are customized according to customer specifications, and production only starts after an order is received. (oracle.com)
- Job #1 is delivering the ordered product according to specifications: color, size, brand, and quantity. (netsuite.com)
External Links
How To
How to Use the 5S to Increase Productivity In Manufacturing
5S stands for "Sort", "Set In Order", "Standardize", "Separate" and "Store". Toyota Motor Corporation developed the 5S method in 1954. It assists companies in improving their work environments and achieving higher efficiency.
This method has the basic goal of standardizing production processes to make them repeatable. This means that tasks such as cleaning, sorting, storing, packing, and labeling are performed daily. These actions allow workers to perform their job more efficiently, knowing what to expect.
There are five steps to implementing 5S, including Sort, Set In Order, Standardize, Separate and Store. Each step requires a different action to increase efficiency. If you sort items, it makes them easier to find later. When you set items in an order, you put items together. Next, organize your inventory into categories and store them in containers that are easily accessible. Labeling your containers will ensure that everything is correctly labeled.
Employees will need to be more critical about their work. Employees must be able to see why they do what they do and find a way to achieve them without having to rely on their old methods. To be successful in the 5S system, employees will need to acquire new skills and techniques.
In addition to improving efficiency, the 5S system also increases morale and teamwork among employees. They are more motivated to achieve higher efficiency levels as they start to see improvement.