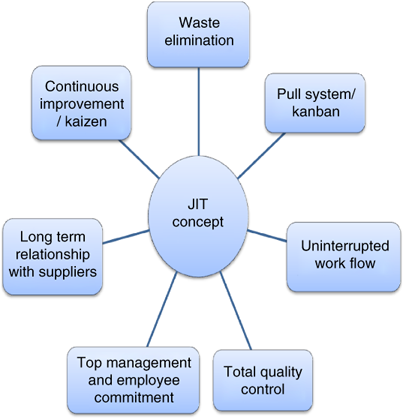
There are many reasons supply chain disruptions could occur. Examples include natural disasters as well as product recalls or transportation delays. These interruptions can result in price increases and margin reductions. To continue production, some companies may need a change in their sourcing strategies. To prepare for the next disruption, many companies will need a re-evaluate or diversify their supply network.
Many industries have experienced disruptions in their supply chains, including transportation, electronics, as well as pharmaceuticals. Sometimes, disruptions occurred due to internal problems at a company. But in other cases, it was caused as a result of a global emergency. For example, a pandemic caused widespread health disruptions in several countries. It also affected the retail industry. The pandemic forced governments into adopting policies to stop the spread of the disease.
A pandemic could affect the workforce, distribution and manufacturing processes of a company. Companies will need to adjust their supply and production chains and reevaluate the impact on production. Depending on how severe the disruption is, the impact could last from weeks to months. Businesses will need an inventory review and capital reallocation if a pandemic happens.
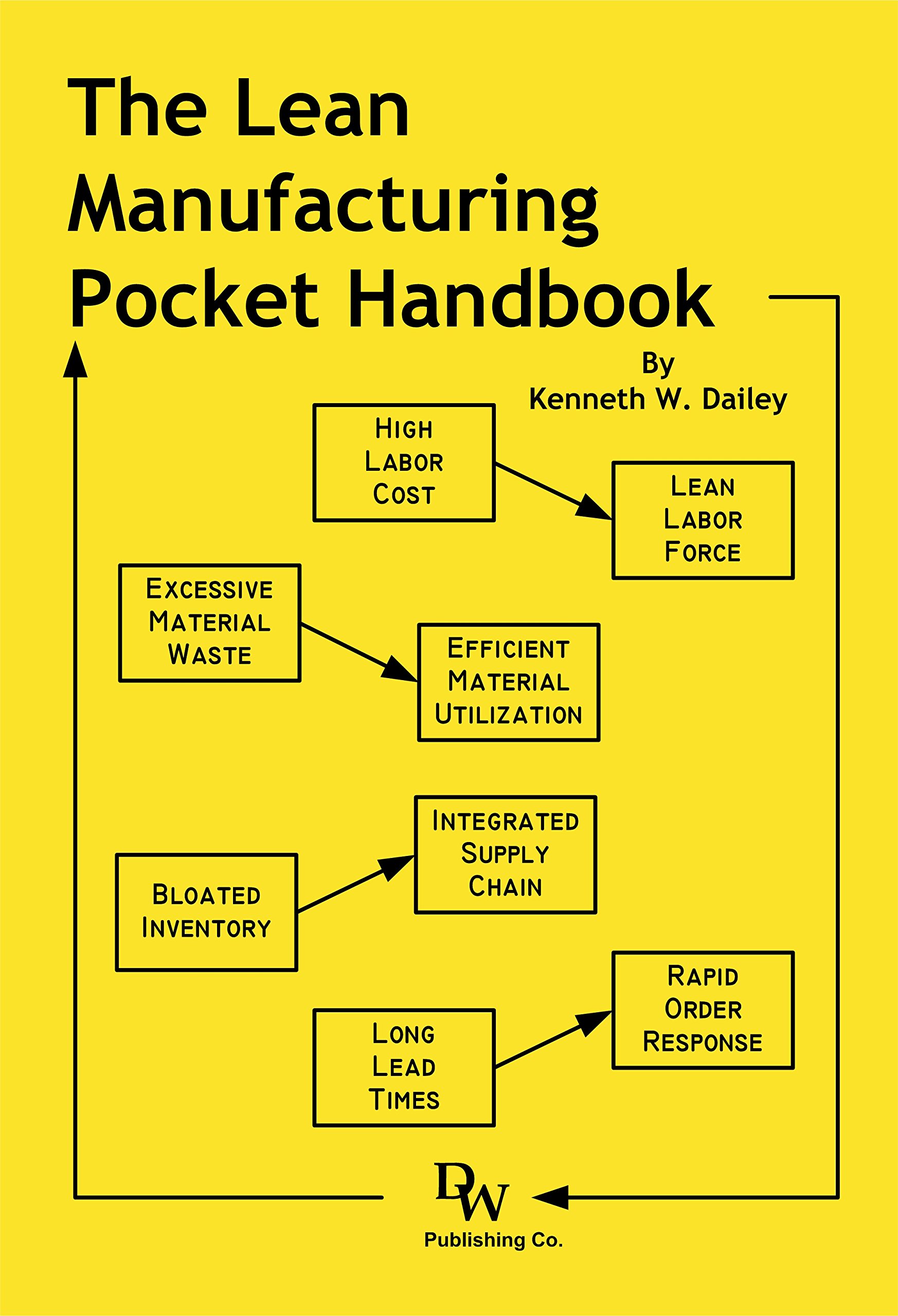
Disruption in any part of the supply chains can occur. In most instances, the demand side will be more affected than the supply side. But if the supply side is affected by a pandemic, it will have a ripple effect on the entire economy.
Supply chain disruptions may have serious consequences for businesses and can be difficult to predict. While seasonal fluctuations are easy to spot, it's more difficult to predict the rapid shifts in consumer behavior. These risks can be mitigated by using predictive analytics to spot potential problems.
A labor shortage is another common reason for supply chain disruption. Inability to obtain equipment or parts from trusted suppliers can lead to productivity losses for companies. A machine failure can also disrupt an entire operation.
Natural disasters, market fluctuations, geopolitical stability, and other factors are all common causes of supply-chain disruptions. Natural disasters are costly and have the potential to disrupt the global supply network. Other causes of supply chain disruption include a power outage, telecommunications blackout, and border closures. Businesses may also be required to store large quantities stock in order protect their business.
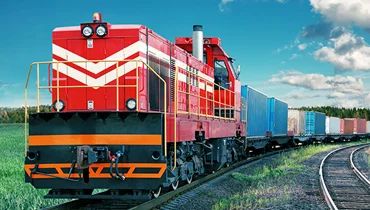
Supply chain disruptions have a relatively low impact, according to general rule. Companies will need help if they discover a disruption. A majority of them will do so. Avoiding conflict by identifying issues early is a good idea.
Ernest & Young LLP surveyed 72 percent of companies that experienced disruptions in the past year. 57 per cent reported adverse effects. While many of these issues can be fixed quickly, others require a more strategic approach.
FAQ
What do you mean by warehouse?
A warehouse is a place where goods are stored until they are sold. It can be an outdoor or indoor area. It may also be an indoor space or an outdoor area.
How can we increase manufacturing efficiency?
First, we need to identify which factors are most critical in affecting production times. Next, we must find ways to improve those factors. You can start by identifying the most important factors that impact production time. Once you have identified them, it is time to identify solutions.
Why is logistics important in manufacturing
Logistics are an integral part any business. They enable you to achieve outstanding results by helping manage product flow from raw materials through to finished goods.
Logistics play a key role in reducing expenses and increasing efficiency.
Statistics
- You can multiply the result by 100 to get the total percent of monthly overhead. (investopedia.com)
- [54][55] These are the top 50 countries by the total value of manufacturing output in US dollars for its noted year according to World Bank.[56] (en.wikipedia.org)
- In 2021, an estimated 12.1 million Americans work in the manufacturing sector.6 (investopedia.com)
- According to a Statista study, U.S. businesses spent $1.63 trillion on logistics in 2019, moving goods from origin to end user through various supply chain network segments. (netsuite.com)
- Job #1 is delivering the ordered product according to specifications: color, size, brand, and quantity. (netsuite.com)
External Links
How To
How to Use 5S to Increase Productivity in Manufacturing
5S stands for "Sort", "Set In Order", "Standardize", "Separate" and "Store". The 5S methodology was developed at Toyota Motor Corporation in 1954. It improves the work environment and helps companies to achieve greater efficiency.
This approach aims to standardize production procedures, making them predictable, repeatable, and easily measurable. This means that tasks such as cleaning, sorting, storing, packing, and labeling are performed daily. Workers can be more productive by knowing what to expect.
Five steps are required to implement 5S: Sort, Set In Order, Standardize. Separate. Each step is a different action that leads to greater efficiency. For example, when you sort things, you make them easy to find later. When you arrange items, you place them together. You then organize your inventory in groups. Finally, when you label your containers, you ensure everything is labeled correctly.
Employees will need to be more critical about their work. Employees need to be able understand their motivations and discover alternative ways to do them. In order to use the 5S system effectively, they must be able to learn new skills.
The 5S Method not only improves efficiency, but it also helps employees to be more productive and happier. Once they start to notice improvements, they are motivated to keep working towards their goal of increasing efficiency.