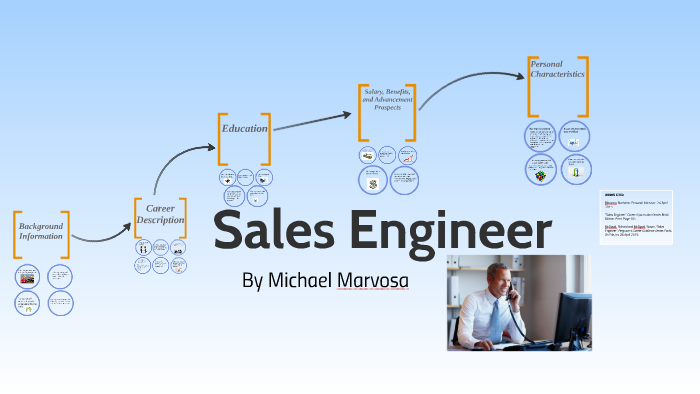
Across the industrial manufacturing industry, the Industrial Products & Services sector is facing intensified global competition, as well as a shortage of skilled workers. The 2020s will be a difficult year for the industrial manufacturing sector due to increased supply chain volatility and intensified competition. To ensure that growth is maximized in existing markets and to maximise growth opportunities in new markets, the Industrial Products & Services industry requires a culture of innovation.
According to Deloitte and Manufacturing Institute studies, the US manufacturing workforce is likely to experience the largest skill shortage in recent history. In fact, it is estimated that 2 million unfilled jobs will occur over the next 10 years. As the industry prepares for the future, manufacturers must decide how they will develop their digital and innovation capabilities. Deloitte's Industrial Manufacturing Team can help manufacturers navigate the landscape of the industry.
As the fourth industrial revolution continues to disrupt the manufacturing sector, the industry must prepare the workforce for a future that will involve networking within the 'internet of things' and digital transformation. The Industrial Manufacturing team has a wealth of industry-specific experience and deep industry knowledge. They are skilled in developing innovative management models. It also provides a wide range of digital transformation services that can help manufacturers to thrive in a world of digital disruption.
The Deloitte study is based on extensive secondary data analysis of labor supply, as well as interviews with executives from manufacturing organizations of all sizes. Economic projections are also included in the research. The findings also highlight the importance of a diverse workforce. Specifically, half of the respondents cited adaptability to company values as a key factor in their job satisfaction. Respondents also reported that more than one third believe employees must have a purpose for being satisfied at work. Furthermore, executives feel that millennials understand the importance of environmental awareness and that Generation Z workers are becoming more involved in climate issues.
Using the Oxford Economic Model, Deloitte predicts that manufacturing GDP will grow at a moderate rate of 1.3 percent in 2020. The study points out that this growth rate is less than half the rate experienced in recent years. This means that companies will need to rethink their approaches to supply chain assurance. Companies will also need to concentrate on wider management initiatives, such as improving operational resilience. According to Deloitte's study, manufacturers will be making decisions regarding work environments and work practices.
Manufacturing companies must create pathways to careers and foster an inclusive culture in order to be ready for the future. Manufacturing efficiency can be improved and waste reduced by increasing resilience. Combining digital technologies with lean principles can help to reduce manufacturing variability.
Deloitte releases a new report about diversity in manufacturing, as the US manufacturing sector continues to develop. Deloitte's "Beyond Reskilling" report discusses how diversity is essential to manufacturing's future, and it highlights the benefits of having a diverse workforce.
FAQ
How important is automation in manufacturing?
Not only are service providers and manufacturers important, but so is automation. It allows them provide faster and more efficient services. In addition, it helps them reduce costs by reducing human errors and improving productivity.
Do we need to know about Manufacturing Processes before learning about Logistics?
No. It doesn't matter if you don't know anything about manufacturing before you learn about logistics. But, being familiar with manufacturing processes will give you a better understanding about how logistics works.
What are the four types in manufacturing?
Manufacturing is the process by which raw materials are transformed into useful products through machines and processes. It involves many different activities such as designing, building, testing, packaging, shipping, selling, servicing, etc.
What are the responsibilities of a manufacturing manager
A manufacturing manager must make sure that all manufacturing processes run smoothly and effectively. They should be alert for any potential problems in the company and react accordingly.
They should also know how to communicate with other departments such as sales and marketing.
They should also be aware of the latest trends in their industry and be able to use this information to help improve productivity and efficiency.
How can overproduction in manufacturing be reduced?
Better inventory management is key to reducing excess production. This would reduce time spent on activities such as purchasing, stocking, and maintaining excess stock. This could help us free up our time for other productive tasks.
This can be done by using a Kanban system. A Kanban board can be used to monitor work progress. Kanban systems allow work items to move through different states until they reach their final destination. Each state is assigned a different priority.
If work is moving from one stage to the other, then the current task can be completed and moved on to the next. It is possible to keep a task in the beginning stages until it gets to the end.
This allows for work to continue moving forward, while also ensuring that there is no work left behind. Managers can monitor the work being done by Kanban boards to see what is happening at any given time. This information allows them to adjust their workflow based on real-time data.
Another way to control inventory levels is to implement lean manufacturing. Lean manufacturing emphasizes eliminating waste in all phases of production. Waste includes anything that does not add value to the product. Here are some examples of common types.
-
Overproduction
-
Inventory
-
Unnecessary packaging
-
Overstock materials
Manufacturers can increase efficiency and decrease costs by implementing these ideas.
Statistics
- You can multiply the result by 100 to get the total percent of monthly overhead. (investopedia.com)
- In the United States, for example, manufacturing makes up 15% of the economic output. (twi-global.com)
- Job #1 is delivering the ordered product according to specifications: color, size, brand, and quantity. (netsuite.com)
- According to the United Nations Industrial Development Organization (UNIDO), China is the top manufacturer worldwide by 2019 output, producing 28.7% of the total global manufacturing output, followed by the United States, Japan, Germany, and India.[52][53] (en.wikipedia.org)
- It's estimated that 10.8% of the U.S. GDP in 2020 was contributed to manufacturing. (investopedia.com)
External Links
How To
Six Sigma in Manufacturing
Six Sigma is "the application statistical process control (SPC), techniques for continuous improvement." Motorola's Quality Improvement Department, Tokyo, Japan, developed it in 1986. Six Sigma's main goal is to improve process quality by standardizing processes and eliminating defects. Many companies have adopted this method in recent years. They believe there is no such thing a perfect product or service. Six Sigma's primary goal is to reduce variation from the average value of production. You can calculate the percentage of deviation from the norm by taking a sample of your product and comparing it to the average. If the deviation is excessive, it's likely that something needs to be fixed.
Understanding how your business' variability is a key step towards Six Sigma implementation is the first. Once you've understood that, you'll want to identify sources of variation. You'll also want to determine whether these variations are random or systematic. Random variations occur when people make mistakes; systematic ones are caused by factors outside the process itself. You could consider random variations if some widgets fall off the assembly lines. But if you notice that every widget you make falls apart at the exact same place each time, this would indicate that there is a problem.
Once you've identified the problem areas you need to find solutions. This could mean changing your approach or redesigning the entire process. Once you have implemented the changes, it is important to test them again to ensure they work. If they don't work, you will need to go back to the drawing boards and create a new plan.