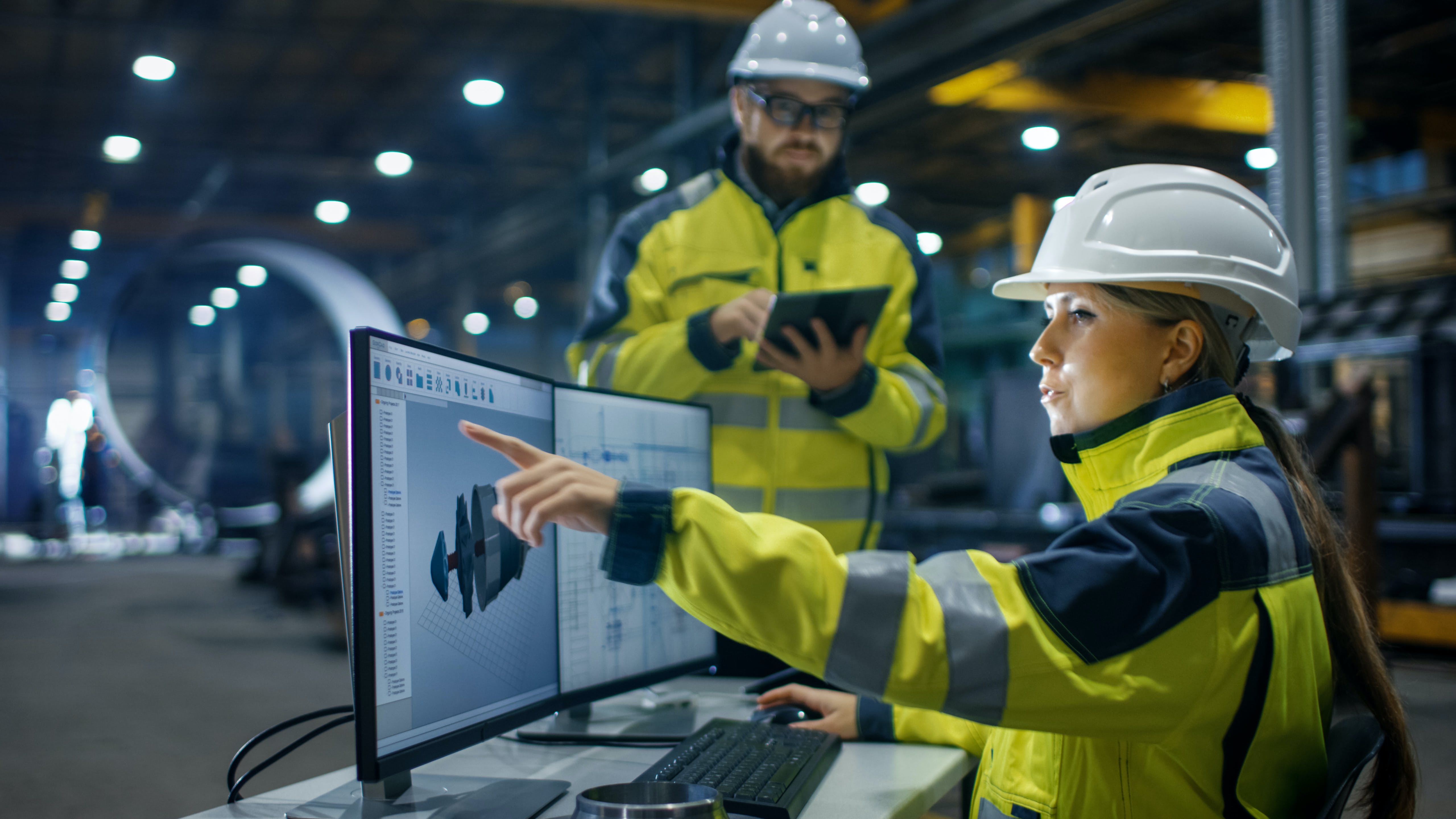
Toyota Motor Manufacturing Indiana Inc. is located in Gibson County Indiana. This plant was the first Toyota plant in America to be completely owned by Toyota. It produces Toyota's full-size pickup trucks including the Avalon, Corolla and Corolla as well as the Sienna minivan. The Toyota RAV4 Hybrid is also produced here, making it the most popular hybrid Toyota has ever made.
The plant was originally intended to make the Toyota Highlander. Instead, it moved to Gibson County, Indiana. Since 2011, the Toyota RAV4 Hybrid compact SUV is produced at this plant. Toyota spent more that $1.33billion at the plant in 2017.
The plant also manufactures the Toyota Safety Sense 2.5+, which features automatic emergency braking. The plant also prepares all of the new 2018 Camry models. New features include a new transmission, greater power and a stylish design. It will cost $25,900
Toyota's Camry production is the largest in America. It is currently the best selling midsize sedan in America, and has been for 15 years. Toyota has produced 10 million Camry vehicles in Kentucky. This is the first hybrid model-producing plant in North America.
Toyota Production System is a collection if practices and techniques that improve quality, efficiency, and productivity. This system includes 600 Toyota engineers. It also houses the Toyota Production Engineering and Manufacturing Center. This center will also be one of the first to manufacture hydrogen fuel cells modules for heavy-duty commercial trucks. This facility can manufacture up to 100,000 vehicles each year.
Toyota has invested $1.5B in the plant over five years. The plant has also been home to 700 additional employees. This investment will create 470,100 jobs in the United States by 2020. Toyota has also invested more than $147 million in Kentucky's nonprofit partners since 1986.
The Toyota Camry is a stylish, reliable car that's also very stylish. It comes with the GAK platform and a completely new transmission. It's also fun to drive. Consumer Reports ranked the Toyota Camry among the top-selling vehicles in America in July 2018.
Toyota's production system incorporates many elements including continuous improvement and just-in time parts delivery. It also includes a sophisticated robotic welding process. The Toyota Production Engineering and Manufacturing Center is a good example of how Toyota has made the most of its investment in Kentucky.
Toyota has made significant savings on its production hall construction and air conditioning costs by using a new design. The building also features a Visitor Center, which includes interactive video displays and exhibits on hybrid technology. During the next 10 years, Toyota will produce up to 2 million vehicles in North America. This is the largest Toyota plant outside of Japan.
Toyota's New Global Architecture marks a major improvement in the company's production systems. This strategy includes a revamped engine and organization of production. It also includes a module that unifies all vehicle components. The new design retains Toyota's innovative spirit while reflecting Toyota's traditional values.
FAQ
What skills are required to be a production manager?
A production planner must be organized, flexible, and able multitask to succeed. Communication skills are essential to ensure that you can communicate effectively with clients, colleagues, and customers.
What makes a production planner different from a project manger?
The difference between a product planner and project manager is that a planer is typically the one who organizes and plans the entire project. A production planner, however, is mostly involved in the planning stages.
What are the responsibilities of a logistic manager?
Logistics managers ensure that goods arrive on time and are unharmed. This is done using his/her knowledge of the company's products. He/she should ensure that sufficient stock is available in order to meet customer demand.
What is production planning?
Production planning is the process of creating a plan that covers all aspects of production. This includes scheduling, budgeting and crew, location, equipment, props, and more. This document aims to ensure that everything is planned and ready when you are ready to shoot. This document should also include information on how to get the best result on set. This includes information on shooting times, locations, cast lists and crew details.
The first step in filming is to define what you want. You may have already chosen the location you want, or there are locations or sets you prefer. Once you have determined your scenes and locations, it is time to start figuring out the elements that you will need for each scene. Perhaps you have decided that you need to buy a car but aren't sure which model. To narrow your options, you can search online for available models.
After you've found the perfect car, it's time to start thinking about adding extras. Do you have people who need to be seated in the front seat? Or perhaps you need someone walking around the back of the car? Maybe you'd like to change the interior from black to a white color. These questions will help to determine the style and feel of your car. The type of shots that you are looking for is another thing to consider. Do you want to film close-ups, or wider angles? Perhaps you want to show the engine or the steering wheel? These factors will help you determine which car style you want to film.
Once you've determined the above, it is time to start creating a calendar. You will know when you should start and when you should finish shooting. Each day will include the time when you need to arrive at the location, when you need to leave and when you need to return home. So everyone is clear about what they need to do. Hire extra staff by booking them ahead of time. You don't want to hire someone who won't show up because he didn't know.
You will need to factor in the days that you have to film when creating your schedule. Some projects take only a few days while others can last several weeks. It is important to consider whether you require more than one photo per day when you create your schedule. Shooting multiple takes over the same location will increase costs and take longer to complete. It is better to be cautious and take fewer shots than you risk losing money if you are not sure if multiple takes are necessary.
Budget setting is another important aspect in production planning. As it will allow you and your team to work within your financial means, setting a realistic budget is crucial. Keep in mind that you can always reduce your budget if you face unexpected difficulties. However, you shouldn't overestimate the amount of money you will spend. Underestimating the cost will result in less money after you have paid for other items.
Production planning is a very detailed process, but once you understand how everything works together, it becomes easier to plan future projects.
How can manufacturing reduce production bottlenecks?
To avoid production bottlenecks, ensure that all processes run smoothly from the moment you receive your order to the time the product ships.
This includes both quality control and capacity planning.
Continuous improvement techniques such Six Sigma are the best method to accomplish this.
Six Sigma management is a system that improves quality and reduces waste within your organization.
It focuses on eliminating variation and creating consistency in your work.
What are the 7 Rs of logistics.
The acronym 7R's for Logistics stands to represent the seven basic principles in logistics management. It was published in 2004 by the International Association of Business Logisticians as part of their "Seven Principles of Logistics Management" series.
The following letters make up the acronym:
-
Responsible - to ensure that all actions are within the legal requirements and are not detrimental to others.
-
Reliable – have faith in your ability and capability to keep promises.
-
Reasonable - use resources efficiently and don't waste them.
-
Realistic - Consider all aspects of operations, including environmental impact and cost effectiveness.
-
Respectful - treat people fairly and equitably.
-
You are resourceful and look for ways to save money while increasing productivity.
-
Recognizable: Provide customers with value-added service
Statistics
- Job #1 is delivering the ordered product according to specifications: color, size, brand, and quantity. (netsuite.com)
- Many factories witnessed a 30% increase in output due to the shift to electric motors. (en.wikipedia.org)
- [54][55] These are the top 50 countries by the total value of manufacturing output in US dollars for its noted year according to World Bank.[56] (en.wikipedia.org)
- According to a Statista study, U.S. businesses spent $1.63 trillion on logistics in 2019, moving goods from origin to end user through various supply chain network segments. (netsuite.com)
- You can multiply the result by 100 to get the total percent of monthly overhead. (investopedia.com)
External Links
How To
How to Use 5S to Increase Productivity in Manufacturing
5S stands for "Sort", 'Set In Order", 'Standardize', & Separate>. Toyota Motor Corporation developed the 5S method in 1954. It improves the work environment and helps companies to achieve greater efficiency.
This approach aims to standardize production procedures, making them predictable, repeatable, and easily measurable. This means that daily tasks such as cleaning and sorting, storage, packing, labeling, and packaging are possible. Through these actions, workers can perform their jobs more efficiently because they know what to expect from them.
Implementing 5S involves five steps: Sort, Set in Order, Standardize Separate, Store, and Each step is a different action that leads to greater efficiency. For example, when you sort things, you make them easy to find later. Once you have placed items in an ordered fashion, you will put them together. After you have divided your inventory into groups you can store them in easy-to-reach containers. Finally, label all containers correctly.
Employees must be able to critically examine their work practices. Employees need to understand the reasons they do certain jobs and determine if there is a better way. They must learn new skills and techniques in order to implement the 5S system.
The 5S method not only increases efficiency but also boosts morale and teamwork. They feel more motivated to work towards achieving greater efficiency as they see the results.