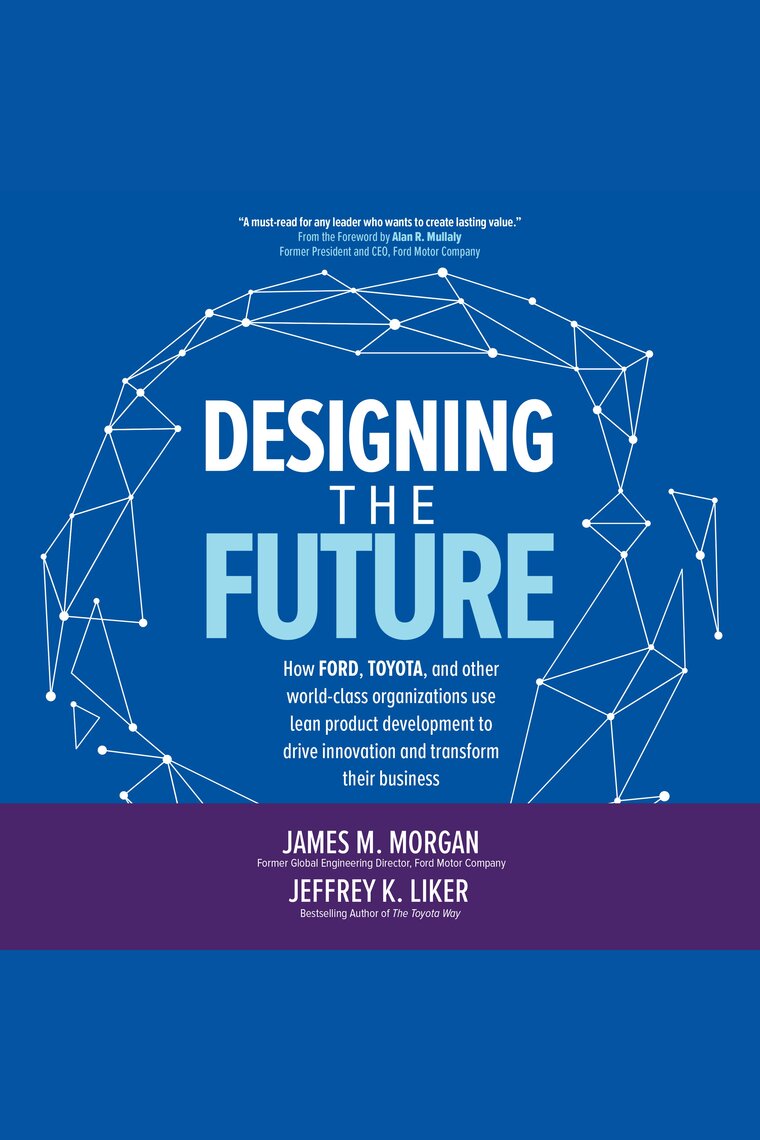
Whether you are running a small business or the enterprise arm of a major corporation, supply chain risk management is a necessary component to maintaining a robust operation. There are many risks that can occur, from the seemingly mundane to the potentially disastrous. Your organization can be protected from losses with a well-planned plan and an effective implementation strategy.
Data sharing is an important part of any supply chain continuity plan. If you rely on one supplier, your organization is more vulnerable to supplier problems and vendor disputes. However, if your company is part of a multi-supplier consortium, you are more likely to avoid supply disruptions. You may also be able to negotiate an alternative supplier.
Also, vendor fraud, duplicate and improper related-party bills are all possible if your company has many contractors. These risks can be mitigated by creating a risk assessment strategy that includes a complete assessment and assessment of all your suppliers, partners, as well other tier-1 components.
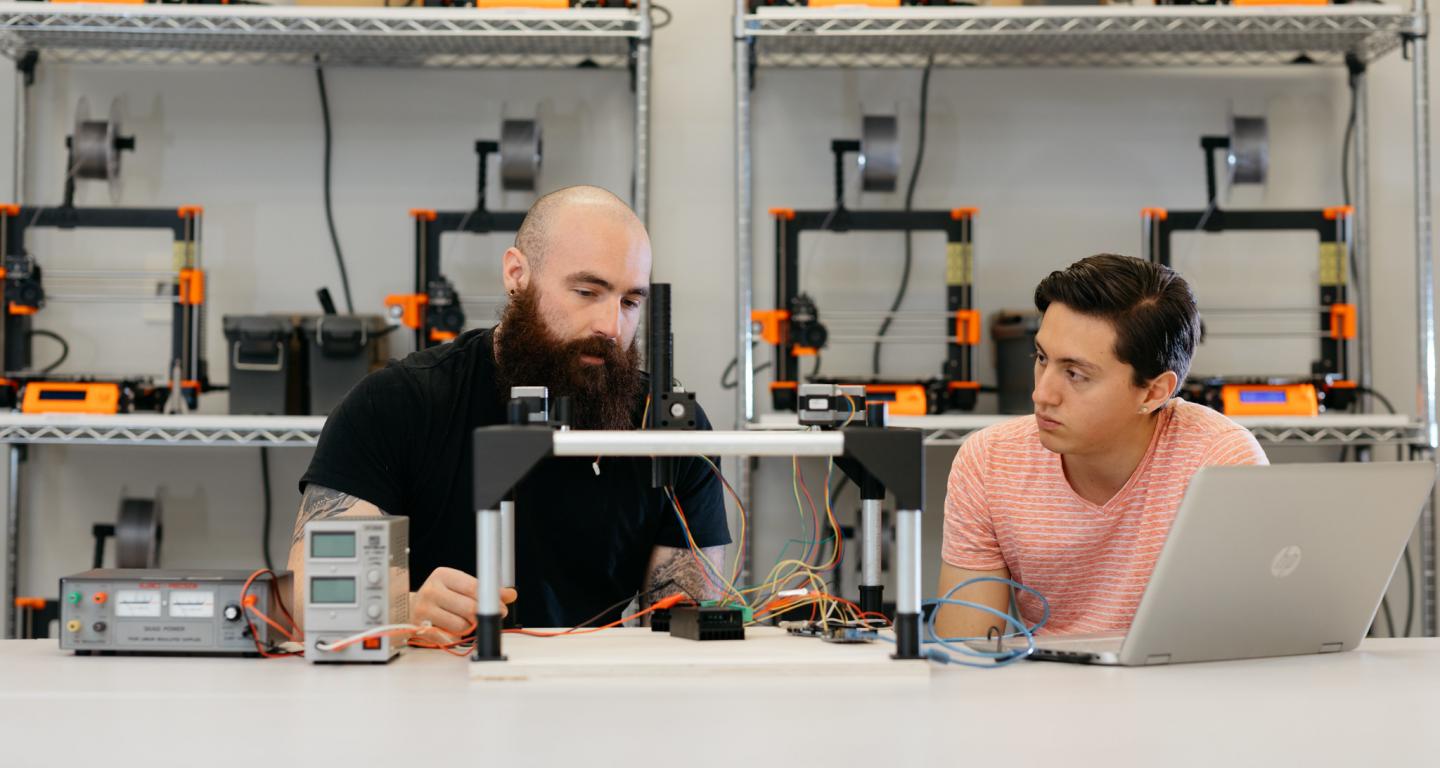
You must first identify the essential elements of a supply supply chain. After that, quantify them and create an action plan. It should include all of the above and a few other items. A proactive monitoring program is essential. A proactive monitoring system is one that gives executives accurate, real-time information about supply chain risks. You can make better decisions and react quickly by monitoring supply risk in real-time.
You must keep in mind that your supply-chain's resilience depends on how well you manage it. It is important to take into account the role of stakeholders. For example, the supplier bankruptcy that led to a supply-chain disruption in the pharmaceutical industry could have been avoided if the company had properly scorecarded its suppliers.
Planning is key to mitigating supply chain crises. Implementing the right contingency plan is difficult. Many businesses neglect to make the effort to have enough contingency planning for every risk they face. The most important potential consequences should be considered when developing these plans.
The PPPR (preventive preparation, response, and recovery) is a standard worldwide for supply chain risk management. This robust approach can help you monitor and respond to supply-chain disruptions. It is often combined with other strategies to protect your company from risk. Using a PPPR as a guide can help you make the right decisions and stay ahead of your competition in today's marketplace.
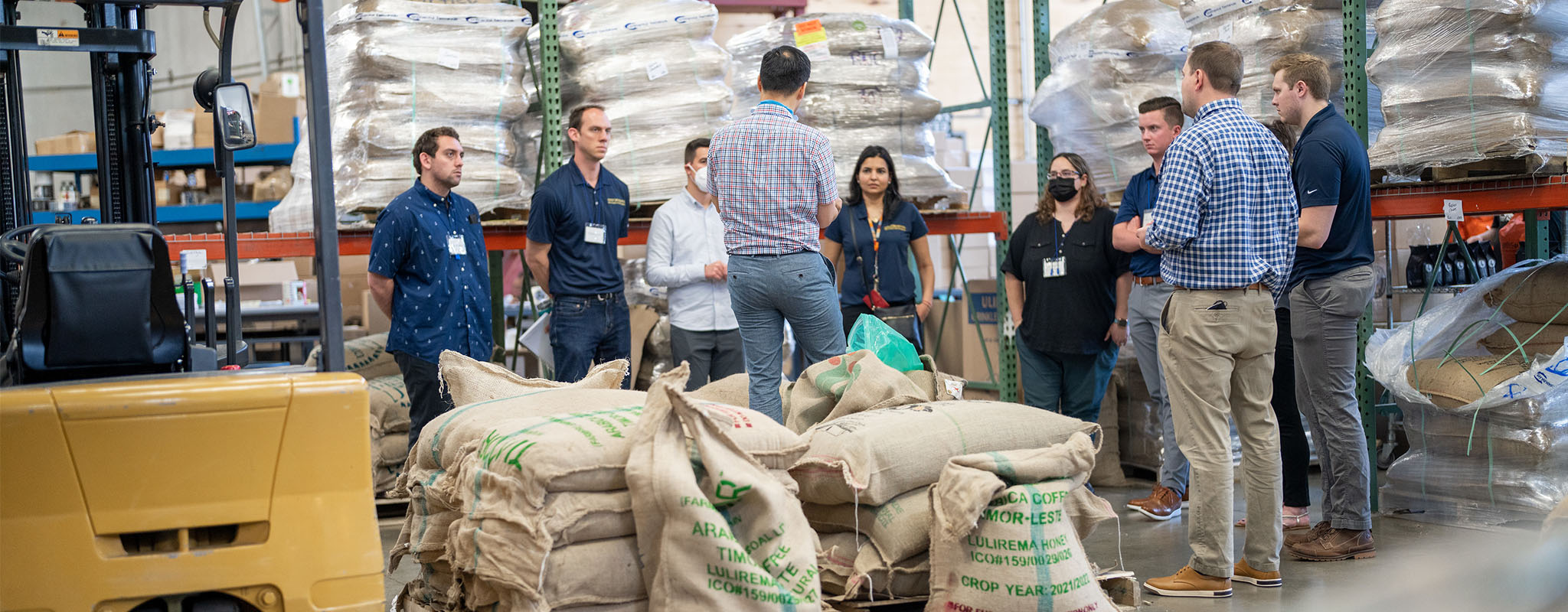
You can learn a lot about your suppliers by getting the right data. This information will help you to make better decisions whether you are trying to increase your sourcing efforts or just tweaking your current processes. You can provide the right risk premiums to your insurers by having reliable data.
FAQ
How can overproduction in manufacturing be reduced?
Improved inventory management is the key to reducing overproduction. This would reduce the amount of time spent on unnecessary activities such as purchasing, storing, and maintaining excess stock. This will allow us to free up resources for more productive tasks.
You can do this by adopting a Kanban method. A Kanban board is a visual display used to track work in progress. Work items are moved through various states to reach their destination in a Kanban system. Each state is assigned a different priority.
For instance, when work moves from one stage to another, the current task is complete enough to be moved to the next stage. It is possible to keep a task in the beginning stages until it gets to the end.
This allows work to move forward and ensures that no work is missed. Managers can view the Kanban board to see how much work they have done. This information allows managers to adjust their workflow based off real-time data.
Lean manufacturing is another way to manage inventory levels. Lean manufacturing works to eliminate waste throughout every stage of the production chain. Any product that isn't adding value can be considered waste. These are some of the most common types.
-
Overproduction
-
Inventory
-
Packaging that is not necessary
-
Materials in excess
These ideas can help manufacturers improve efficiency and reduce costs.
How can we improve manufacturing efficiency?
First, identify the factors that affect production time. Next, we must find ways to improve those factors. If you don't know where to start, then think about which factor(s) have the biggest impact on production time. Once you've identified them all, find solutions to each one.
Are there ways to automate parts of manufacturing?
Yes! Yes. Automation has been around since ancient time. The Egyptians invented the wheel thousands of years ago. Today, robots assist in the assembly of lines.
In fact, there are several applications of robotics in manufacturing today. These include:
-
Robots for assembly line
-
Robot welding
-
Robot painting
-
Robotics inspection
-
Robots that make products
There are many other examples of how manufacturing could benefit from automation. For instance, 3D printing allows us make custom products and not have to wait for months or even weeks to get them made.
How important is automation in manufacturing?
Automating is not just important for manufacturers, but also for service providers. It allows them to offer services faster and more efficiently. It also helps to reduce costs and improve productivity.
How is a production manager different from a producer planner?
The major difference between a Production Planner and a Project Manager is that a Project Manager is often the person responsible for organizing and planning the entire project. While a Production Planner is involved mainly in the planning stage,
What is the job of a manufacturer manager?
The manufacturing manager should ensure that every manufacturing process is efficient and effective. They should be alert for any potential problems in the company and react accordingly.
They should also learn how to communicate effectively with other departments, including sales and marketing.
They must also keep up-to-date with the latest trends in their field and be able use this information to improve productivity and efficiency.
Statistics
- According to the United Nations Industrial Development Organization (UNIDO), China is the top manufacturer worldwide by 2019 output, producing 28.7% of the total global manufacturing output, followed by the United States, Japan, Germany, and India.[52][53] (en.wikipedia.org)
- [54][55] These are the top 50 countries by the total value of manufacturing output in US dollars for its noted year according to World Bank.[56] (en.wikipedia.org)
- Many factories witnessed a 30% increase in output due to the shift to electric motors. (en.wikipedia.org)
- According to a Statista study, U.S. businesses spent $1.63 trillion on logistics in 2019, moving goods from origin to end user through various supply chain network segments. (netsuite.com)
- You can multiply the result by 100 to get the total percent of monthly overhead. (investopedia.com)
External Links
How To
How to use 5S in Manufacturing to Increase Productivity
5S stands as "Sort", Set In Order", Standardize", Separate" and "Store". The 5S methodology was developed at Toyota Motor Corporation in 1954. This methodology helps companies improve their work environment to increase efficiency.
This method aims to standardize production processes so that they are repeatable, measurable and predictable. Cleaning, sorting and packing are all done daily. Workers can be more productive by knowing what to expect.
Implementing 5S involves five steps: Sort, Set in Order, Standardize Separate, Store, and Each step requires a different action to increase efficiency. If you sort items, it makes them easier to find later. When items are ordered, they are put together. After you have divided your inventory into groups you can store them in easy-to-reach containers. You can also label your containers to ensure everything is properly labeled.
Employees will need to be more critical about their work. Employees need to be able understand their motivations and discover alternative ways to do them. To be successful in the 5S system, employees will need to acquire new skills and techniques.
In addition to improving efficiency, the 5S system also increases morale and teamwork among employees. They feel more motivated to work towards achieving greater efficiency as they see the results.