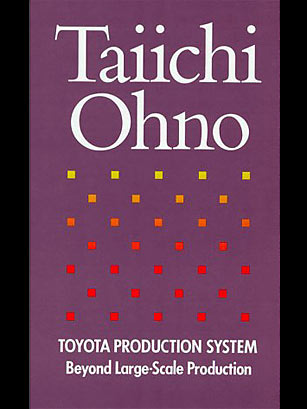
Consider lean manufacturing if you are looking to reduce costs, speed up lead times, minimize setup time, and maximize turnaround time. Lean manufacturing offers many benefits. It reduces costs and leads time, while improving customer satisfaction. These improvements make lean manufacturing the best way to boost your business. You might still be skeptical, but here are three reasons it is the best way to produce products and reduce costs.
Lowers costs
Lean manufacturing can bring significant savings. Manufacturers can save money on direct labor costs by reducing defects or rework. This makes labor costs less motivating in decision-making. The elimination of hazardous waste is another benefit. Direct labor costs are below 15% in many industries. It is difficult to justify outsourcing manufacturing to low cost locations. This can lower overall manufacturing costs and improve customer services.
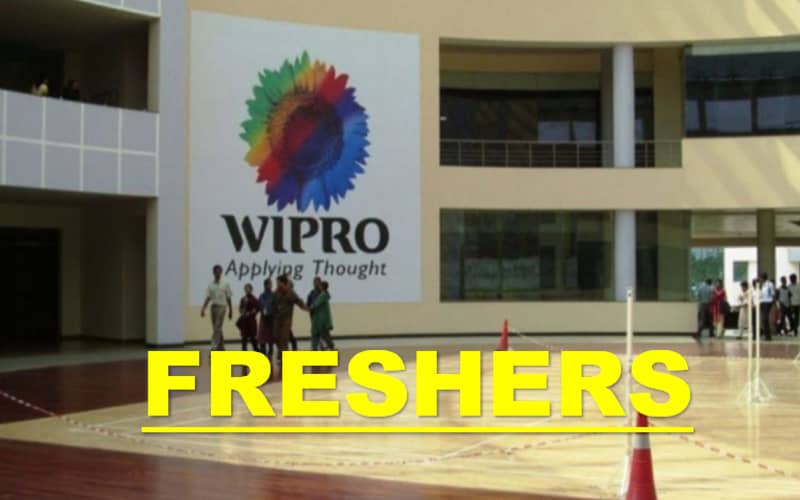
Improves lead times
Lean manufacturing has many benefits, including the ability reduce waste and increase lead times. It is a philosophy based on continuous improvement, or kaizen. It is a system that combines the talents and encourages employee collaboration. The process can decrease lead times by as high as 20% Lean manufacturing is about making small adjustments frequently to improve product quality.
Shortens set-up times
Reducing set-up times is one way to decrease the time needed to produce a product. Setup time refers to the amount of time required to switch from the last item on a previous order to the first good item on the next. The setup time includes preparation, replacement, as well as location activities. These activities may be external or internal. Although internal activities are inactive, such as moving a machine or putting an item in its place, external setup activities can still be completed while the process remains operational.
Shortens lead time to market
The concept of Lean manufacturing, or the process of continuous improvement, was developed in Japan during the rebuilding period after World War II. It was developed to improve competition and reduce lead time. Companies can be more responsive to customers and increase profits by reducing the time it takes a product reach the market. This method of production can not only increase efficiency in the manufacturing process but also make the entire facility more effective.
Improves product quality
Lean manufacturing's success depends on the ability to reduce waste, improve product quality, and minimize costs. It has been used by many companies, large and small. It can lower lead times, costs, labor, and other expenses. Continue reading to learn more about how lean manufacturing can help your business. Here are some of these key areas. Embracing lean principles can reduce lead times by 90%, improve product quality, and reduce your costs.
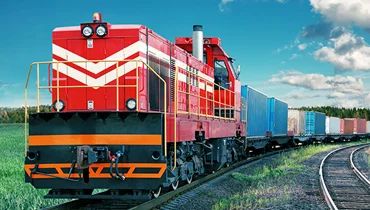
This reduces indirect labor costs
In lean manufacturing, the low hanging fruit is reducing indirect labor costs. Lean companies focus less on direct labor efficiency and look instead for ways to lower indirect labor costs. This includes eliminating management, material handling, inspection and management jobs as well as pushing production decisions to the floor. This is the same method used by Toyota and other lean manufacturing firms. In this article, we'll examine how lean production can lower indirect labor expenses.
FAQ
Is automation important for manufacturing?
Automation is essential for both manufacturers and service providers. It allows them provide faster and more efficient services. In addition, it helps them reduce costs by reducing human errors and improving productivity.
What skills should a production planner have?
You must be flexible and organized to become a productive production planner. You must also be able to communicate effectively with clients and colleagues.
What does warehouse refer to?
A warehouse, or storage facility, is where goods are stored prior to being sold. It can be an indoor space or an outdoor area. Sometimes, it can be both an indoor and outdoor space.
What are the main products of logistics?
Logistics involves the transportation of goods from point A and point B.
They include all aspects associated with transport including packaging, loading transporting, unloading storage, warehousing inventory management customer service, distribution returns and recycling.
Logisticians make sure that the right product arrives at the right place at the correct time and in safe conditions. Logisticians help companies improve their supply chain efficiency by providing information about demand forecasts and stock levels, production schedules, as well as availability of raw materials.
They can also track shipments in transit and monitor quality standards.
What are the four types in manufacturing?
Manufacturing is the process by which raw materials are transformed into useful products through machines and processes. It can involve many activities like designing, manufacturing, testing packaging, shipping, selling and servicing.
Statistics
- Job #1 is delivering the ordered product according to specifications: color, size, brand, and quantity. (netsuite.com)
- [54][55] These are the top 50 countries by the total value of manufacturing output in US dollars for its noted year according to World Bank.[56] (en.wikipedia.org)
- You can multiply the result by 100 to get the total percent of monthly overhead. (investopedia.com)
- In the United States, for example, manufacturing makes up 15% of the economic output. (twi-global.com)
- (2:04) MTO is a production technique wherein products are customized according to customer specifications, and production only starts after an order is received. (oracle.com)
External Links
How To
How to use 5S in Manufacturing to Increase Productivity
5S stands in for "Sort", the "Set In Order", "Standardize", or "Separate". Toyota Motor Corporation created the 5S methodology in 1954. It allows companies to improve their work environment, thereby achieving greater efficiency.
This method has the basic goal of standardizing production processes to make them repeatable. It means tasks like cleaning, sorting or packing, labeling, and storing are done every day. Through these actions, workers can perform their jobs more efficiently because they know what to expect from them.
There are five steps that you need to follow in order to implement 5S. Each step requires a different action, which increases efficiency. By sorting, for example, you make it easy to find the items later. When you set items in an order, you put items together. You then organize your inventory in groups. Finally, when you label your containers, you ensure everything is labeled correctly.
This process requires employees to think critically about how they do their job. Employees need to understand the reasons they do certain jobs and determine if there is a better way. They will need to develop new skills and techniques in order for the 5S system to be implemented.
The 5S Method not only improves efficiency, but it also helps employees to be more productive and happier. As they begin to see improvements, they feel motivated to continue working towards the goal of achieving higher levels of efficiency.