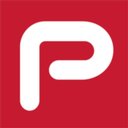
Production workers have a key role to play in the manufacturing industry. They are responsible for getting products to customers. From operating machinery to working in warehouses, these employees help make sure all of the components that go into creating a product are properly made and packaged for shipping.
The average manufacturing wage is higher than many other industries, with the wage premium generally ranging from 10 percent to more than 15 percent (Langdon and Lehrman 2012). The compensation premium for the past few years has been significantly lower. This suggests that those advocating for the expansion of manufacturing cannot take the benefit for granted.
Pay by Experience for Production Workers
You are more likely to earn higher salaries as a production employee if you have good skills and experience. Switching employers, gaining additional experience, or moving to a management position can all increase your earning power.
Create Effective Workplace Strategy
If you are a worker in manufacturing, it is important to consider ways that your workplace can be more efficient while maintaining quality. This includes identifying slow areas and finding solutions that speed up production. It is important to work with supervisors as well as other members of the team in order to implement and measure these efficiency improvements.
Safety at Work. As a production worker you are responsible for keeping the workplace safe. You should adhere to all safety and health guidelines. You should keep your equipment clean, prevent accidents, and report any injuries or accidents to your supervisor.
Maintaining Production Standards. As a production worker you have the responsibility of producing high quality products that meet strict standards in manufacturing and quality. For this to happen, you will need to monitor and operate the machines for defects and maintain a consistent speed.
Cleaning the Workplace. This is to prevent contamination and ensure a more productive environment.
Monitoring Product Quality - As a worker in production, you will conduct daily checks to ensure the output meets the specifications of the company. This includes checking for faulty items and recording them on your production report.
You can improve productivity by using new technologies. As a worker in the manufacturing industry, you have the opportunity to implement innovative and new processes into your factory. You might adopt a completely different method of packaging, or design a brand new way to assemble your products.
These improvements could increase the productivity and earnings of your business as well as the production workers. These improvements include things like robotics or automation.
Earnings for Manufacturing Workers
As a manufacturing employee, you should keep track of the wages other workers earn in your sector and try to compete. You can do this by seeking new positions in other companies, earning advanced degrees or certifications and managing your experience to qualify you for promotions.
FAQ
What are the requirements to start a logistics business?
A successful logistics business requires a lot more than just knowledge. You must have good communication skills to interact effectively with your clients and suppliers. You must be able analyze data and draw out conclusions. You must be able to work well under pressure and handle stressful situations. You need to be innovative and creative to come up with new ways to increase efficiency. Strong leadership qualities are essential to motivate your team and help them achieve their organizational goals.
To meet tight deadlines, you must also be efficient and organized.
Why is logistics important in manufacturing
Logistics is an integral part of every business. They enable you to achieve outstanding results by helping manage product flow from raw materials through to finished goods.
Logistics are also important in reducing costs and improving efficiency.
What is the role of a logistics manager
Logistics managers ensure that goods arrive on time and are unharmed. This is done by using his/her experience and knowledge of the company's products. He/she should ensure that sufficient stock is available in order to meet customer demand.
Statistics
- [54][55] These are the top 50 countries by the total value of manufacturing output in US dollars for its noted year according to World Bank.[56] (en.wikipedia.org)
- (2:04) MTO is a production technique wherein products are customized according to customer specifications, and production only starts after an order is received. (oracle.com)
- It's estimated that 10.8% of the U.S. GDP in 2020 was contributed to manufacturing. (investopedia.com)
- According to a Statista study, U.S. businesses spent $1.63 trillion on logistics in 2019, moving goods from origin to end user through various supply chain network segments. (netsuite.com)
- According to the United Nations Industrial Development Organization (UNIDO), China is the top manufacturer worldwide by 2019 output, producing 28.7% of the total global manufacturing output, followed by the United States, Japan, Germany, and India.[52][53] (en.wikipedia.org)
External Links
How To
How to use the Just In-Time Production Method
Just-intime (JIT), which is a method to minimize costs and maximize efficiency in business process, is one way. It allows you to get the right amount resources at the right time. This means that only what you use is charged to your account. The term was first coined by Frederick Taylor, who developed his theory while working as a foreman in the early 1900s. After observing how workers were paid overtime for late work, he realized that overtime was a common practice. He realized that workers should have enough time to complete their jobs before they begin work. This would help increase productivity.
JIT teaches you to plan ahead and prepare everything so you don’t waste time. Look at your entire project, from start to end. Make sure you have enough resources in place to deal with any unexpected problems. If you anticipate that there might be problems, you'll have enough people and equipment to fix them. This will ensure that you don't spend more money on things that aren't necessary.
There are many JIT methods.
-
Demand-driven JIT: This is a JIT that allows you to regularly order the parts/materials necessary for your project. This will allow to track how much material has been used up. This will allow you to calculate how long it will take to make more.
-
Inventory-based: This is a type where you stock the materials required for your projects in advance. This allows you predict the amount you can expect to sell.
-
Project-driven: This approach involves setting aside sufficient funds to cover your project's costs. Knowing how much money you have available will help you purchase the correct amount of materials.
-
Resource-based JIT: This type of JIT is most commonly used. This is where you assign resources based upon demand. If you have many orders, you will assign more people to manage them. If you don't receive many orders, then you'll assign fewer employees to handle the load.
-
Cost-based: This is similar to resource-based, except that here you're not just concerned about how many people you have but how much each person costs.
-
Price-based: This is similar to cost-based but instead of looking at individual workers' salaries, you look at the total company price.
-
Material-based: This approach is similar to cost-based. However, instead of looking at the total cost for the company, you look at how much you spend on average on raw materials.
-
Time-based: This is another variation of resource-based JIT. Instead of focusing on how much each employee costs, you focus on how long it takes to complete the project.
-
Quality-based JIT: Another variation on resource-based JIT. Instead of worrying about the costs of each employee or how long it takes for something to be made, you should think about how quality your product is.
-
Value-based JIT : This is the newest type of JIT. In this instance, you are not concerned about the product's performance or meeting customer expectations. Instead, your goal is to add value to the market.
-
Stock-based: This inventory-based approach focuses on how many items are being produced at any one time. It's useful when you want maximum production and minimal inventory.
-
Just-in-time (JIT) planning: This is a combination of JIT and supply chain management. It's the process of scheduling delivery of components immediately after they are ordered. It's important as it reduces leadtimes and increases throughput.