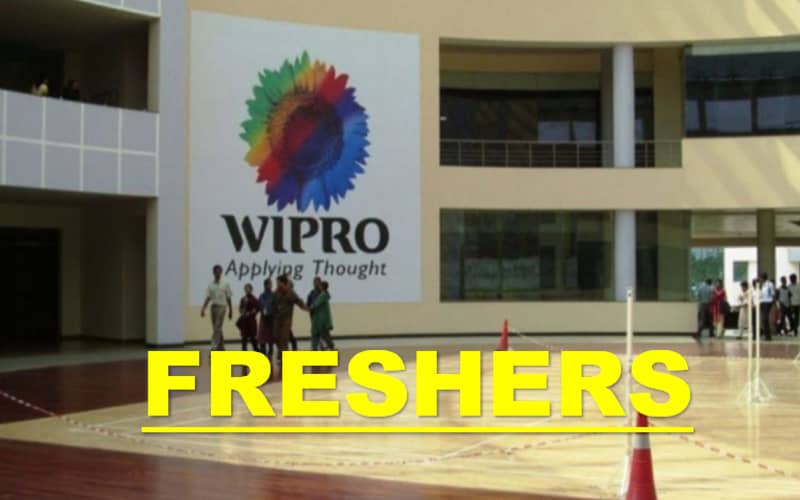
OSHA compliance is equally important, as is experience. There are three things you need to keep in mind when choosing a company for automating your production process.
Experience is important for food manufacturers
A food manufacturer's position often requires a high level of experience in the industry. But, those with no or little experience may still be able to find work. Many food producers prefer to hire within their own ranks. High school education can be beneficial but not essential. As assistants to more skilled workers, entry-level employees begin as such. They learn on the job. Some entry-level tasks are easy and can be completed in as little as a couple of days. You might find common entry-level positions such as operating bread slicers, washing and prepping vegetables, packing the bottles, and hauling carcasses. It is important to have experience in all areas of food manufacturing.
Respect for OSHA regulations
The enforcement process for OSHA regulations for food manufacturers begins with an inspection, which is either triggered by an incident, complaint, or a "programmed inspection." A planned inspection preceded an OSHA enforcement trip to a yogurt factory. In many cases, the citations include multiple violations of the process safety management standard, as well as standards on hazard communication, guarding machinery, stairs and platforms, emergency egress, forklift operation, hearing protection, and more.
Plan development to avoid food safety concerns
Although most businesses must comply with federal regulations, certain businesses may be exempted from these requirements. It is impossible to predict every possible food safety problem, but there are ways to manage and prevent them. Food safety is a serious problem that can not only affect the health of the consumer but also impact the business. Recalls can have a negative impact on both direct operations as well as other members of the supply chain. There are many reasons for recalls, such as adulteration and misbranding. A food manufacturer may have to pay a lot more for recalls than the health risks.
Cost of automation
Food manufacturers face increasing automation costs as utilities rise. As a result, some regions are forced import ingredients to meet local production. Additionally, suppliers face a declining profit margin when they pass on the costs to consumers. However, automation can help lower these costs and increase production efficiency. In this article, we will discuss how automation can improve the overall efficiency of food manufacturers. You can also reach out to us for our industry knowledge.
Competing with established food companies presents challenges
To preserve their market dominance, stop unwanted competition and increase their profit margins, dominant food companies use three broad strategies. The strategies involve acquiring and developing valuable intangible assets, enforcing production and marketing efficiencies, and controlling the supply chain. These strategies, in essence, create barriers to entry. Here are some of the most important challenges faced by emerging food and beverage companies. Let's get into the details of each strategy.
FAQ
What are the 7 R's of logistics?
The acronym "7R's" of Logistics stands for seven principles that underpin logistics management. It was developed and published by the International Association of Business Logisticians in 2004 as part of the "Seven Principles of Logistics Management".
The acronym consists of the following letters:
-
Responsible – ensure that all actions are legal and don't cause harm to anyone else.
-
Reliable: Have faith in your ability or the ability to honor any promises made.
-
Use resources effectively and sparingly.
-
Realistic - Consider all aspects of operations, including environmental impact and cost effectiveness.
-
Respectful - Treat people fairly and equitably
-
Be resourceful: Look for opportunities to save money or increase productivity.
-
Recognizable is a company that provides customers with value-added solutions.
Can some manufacturing processes be automated?
Yes! Automation has been around since ancient times. The Egyptians created the wheel thousands years ago. We now use robots to help us with assembly lines.
Actually, robotics can be used in manufacturing for many purposes. These include:
-
Automated assembly line robots
-
Robot welding
-
Robot painting
-
Robotics inspection
-
Robots that create products
Manufacturing can also be automated in many other ways. For instance, 3D printing allows us make custom products and not have to wait for months or even weeks to get them made.
What are manufacturing & logistics?
Manufacturing refers the process of producing goods from raw materials through machines and processes. Logistics manages all aspects of the supply chain, including procurement, production planning and distribution, inventory control, transportation, customer service, and transport. Sometimes manufacturing and logistics are combined to refer to a wider term that includes both the process of creating products as well as their delivery to customers.
What are the differences between these four types?
Manufacturing is the process of transforming raw materials into useful products using machines and processes. Manufacturing involves many activities, including designing, building, testing and packaging, shipping, selling, service, and so on.
What is the difference between Production Planning, Scheduling and Production Planning?
Production Planning (PP), or production planning, is the process by which you determine what products are needed at any given time. Forecasting and identifying production capacity are two key elements to this process.
Scheduling refers the process by which tasks are assigned dates so that they can all be completed within the given timeframe.
Statistics
- You can multiply the result by 100 to get the total percent of monthly overhead. (investopedia.com)
- According to the United Nations Industrial Development Organization (UNIDO), China is the top manufacturer worldwide by 2019 output, producing 28.7% of the total global manufacturing output, followed by the United States, Japan, Germany, and India.[52][53] (en.wikipedia.org)
- Job #1 is delivering the ordered product according to specifications: color, size, brand, and quantity. (netsuite.com)
- Many factories witnessed a 30% increase in output due to the shift to electric motors. (en.wikipedia.org)
- (2:04) MTO is a production technique wherein products are customized according to customer specifications, and production only starts after an order is received. (oracle.com)
External Links
How To
Six Sigma and Manufacturing
Six Sigma is "the application statistical process control (SPC), techniques for continuous improvement." Motorola's Quality Improvement Department developed it at their Tokyo plant in Japan in 1986. Six Sigma's main goal is to improve process quality by standardizing processes and eliminating defects. In recent years, many companies have adopted this method because they believe there is no such thing as perfect products or services. Six Sigma seeks to reduce variation between the mean production value. This means that if you take a sample of your product, then measure its performance against the average, you can find out what percentage of the time the process deviates from the norm. If you notice a large deviation, then it is time to fix it.
The first step toward implementing Six Sigma is understanding how variability works in your business. Once you have this understanding, you will need to identify sources and causes of variation. These variations can also be classified as random or systematic. Random variations are caused when people make mistakes. While systematic variations are caused outside of the process, they can occur. For example, if you're making widgets, and some of them fall off the assembly line, those would be considered random variations. But if you notice that every widget you make falls apart at the exact same place each time, this would indicate that there is a problem.
Once you identify the problem areas, it is time to create solutions. You might need to change the way you work or completely redesign the process. After implementing the new changes, you should test them again to see if they worked. If they didn't work, then you'll need to go back to the drawing board and come up with another plan.