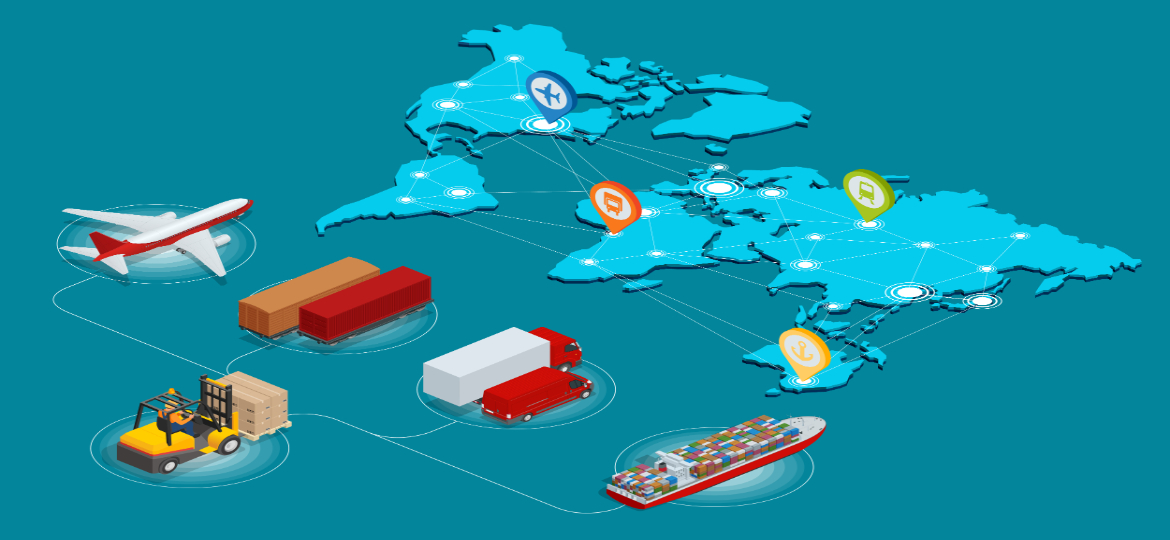
Lean management is an effective way to reduce waste in the workplace. It is based upon the belief that all activities or processes in an organization should add value for its customers. This can be achieved by eliminating any activities that do not add value and working systematically to create more value.
A lean business management system is meant to enhance the performance of any company. This helps ensure that all employees understand the goals and purpose of their job.
In lean system management, the first step is to determine what value is. It involves identifying the value that a customer is looking for and creating a solution to meet that need. To achieve this, it is important to ensure that the entire production process and customer service are efficient and consistent.
Using lean manufacturing principles to make products is an effective way to reduce costs and increase efficiency, but you need to make sure your staff is on board with the changes. Without a strong commitment to the program, the results could be disastrous.
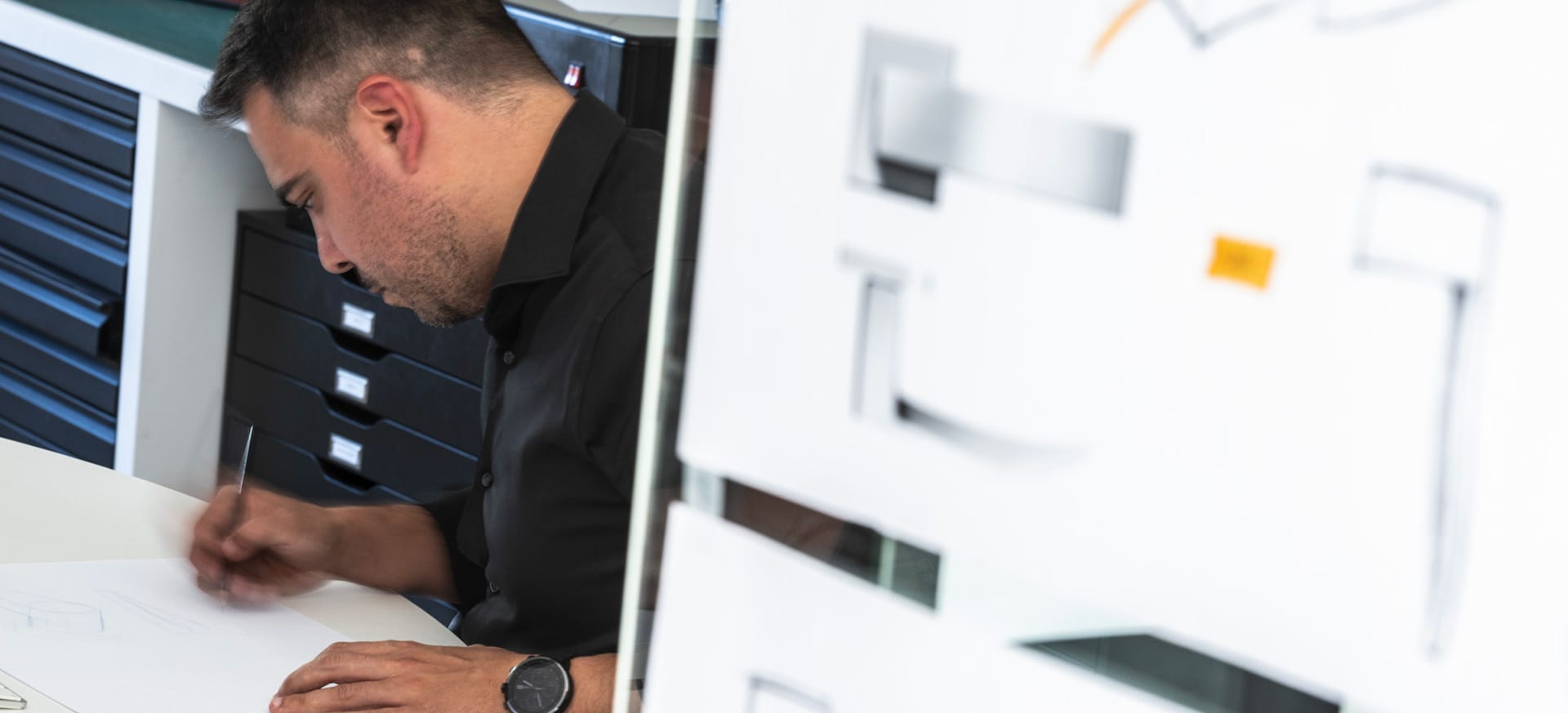
In addition to gaining buy-in from the workforce, you must ensure that your organization has a healthy supply chain. The majority of lean projects require the supply chain be retooled to work properly.
One of the most important things that you can do to help with this is to make sure your staff is properly trained on lean principles. This includes making sure employees understand waste and why it is important to eliminate it.
Teamwork is another aspect to be considered when implementing lean concepts. It may be hard to achieve but is an important aspect of the lean system.
Your team will be able to create better products and services, and your bottom line will increase over time. You can encourage this by giving them a chance to meet with each other regularly and discuss ways to get rid of wastes in their work.
A lean manager will be able to help you by ensuring all your workers are properly trained in these techniques. By keeping your team informed, they can also ensure that production runs smoothly.
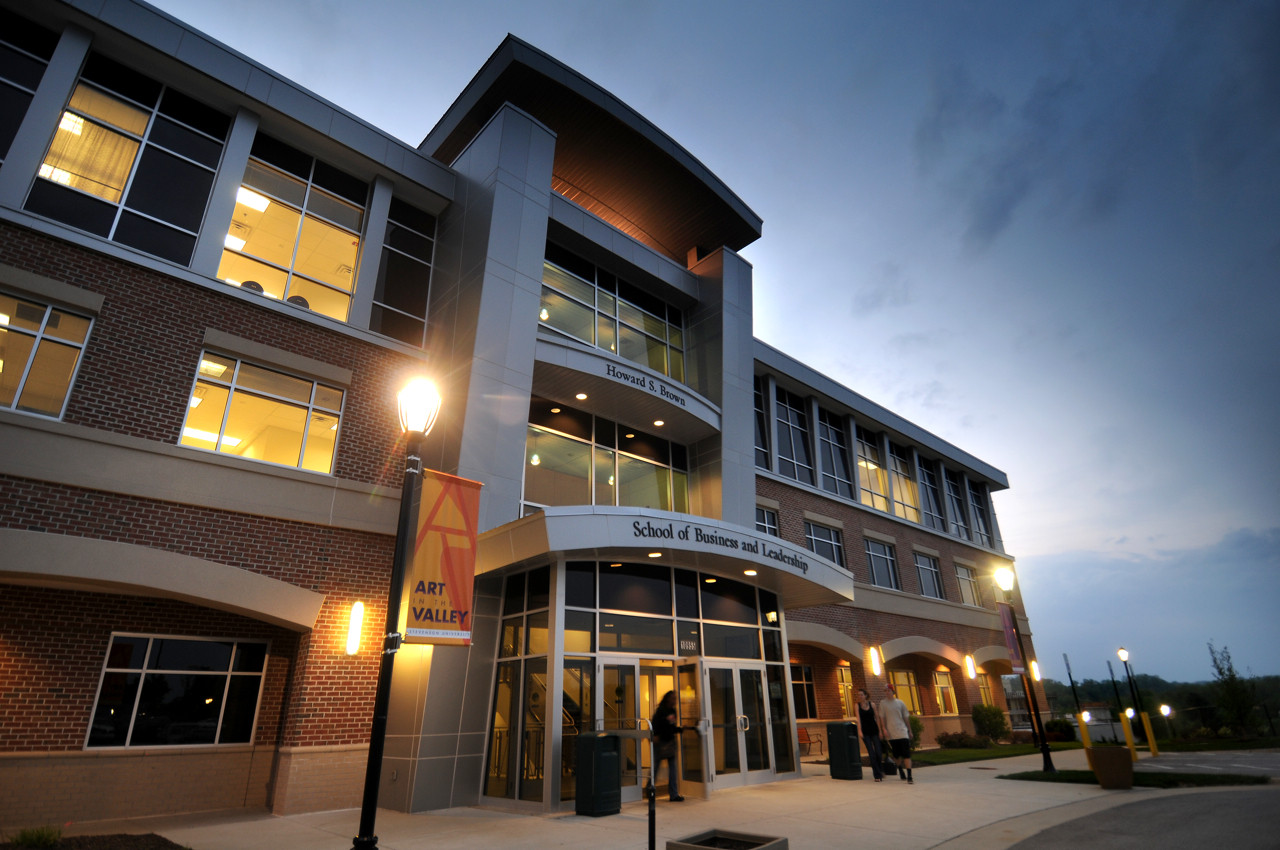
The final stage in lean management is to evaluate and improve the implementation of each procedure. It is possible to do this by monitoring the progress of every project and making sure any changes needed are implemented.
Depending on the level of your organization, you may need to hire someone to manage your lean operations. Searching for lean management positions or job boards can help you find candidates.
FAQ
How can we improve manufacturing efficiency?
The first step is to determine the key factors that impact production time. We then need to figure out how to improve these variables. If you don’t know how to start, look at which factors have the greatest impact upon production time. Once you've identified them all, find solutions to each one.
What does it take for a logistics enterprise to succeed?
It takes a lot of skills and knowledge to run a successful logistics business. Effective communication skills are necessary to work with suppliers and clients. You need to understand how to analyze data and draw conclusions from it. You need to be able work under pressure and manage stressful situations. You need to be innovative and creative to come up with new ways to increase efficiency. Strong leadership qualities are essential to motivate your team and help them achieve their organizational goals.
To meet tight deadlines, you must also be efficient and organized.
What is the importance of logistics in manufacturing?
Logistics are essential to any business. They are essential to any business's success.
Logistics are also important in reducing costs and improving efficiency.
Why automate your warehouse
Modern warehouses are increasingly dependent on automation. With the rise of ecommerce, there is a greater demand for faster delivery times as well as more efficient processes.
Warehouses have to be flexible to meet changing requirements. In order to do this, they need to invest in technology. Automating warehouses is a great way to save money. These are just a few reasons to invest in automation.
-
Increases throughput/productivity
-
Reduces errors
-
Accuracy is improved
-
Safety is boosted
-
Eliminates bottlenecks
-
Companies can scale up more easily
-
Increases efficiency of workers
-
This gives you visibility into what happens in the warehouse
-
Enhances customer experience
-
Improves employee satisfaction
-
Reduces downtime and improves uptime
-
You can be sure that high-quality products will arrive on time
-
Eliminates human error
-
It ensures compliance with regulations
What jobs are available in logistics?
There are different kinds of jobs available in logistics. Some of them are:
-
Warehouse workers – They load, unload and transport pallets and trucks.
-
Transportation drivers – They drive trucks or trailers to transport goods and perform pick-ups.
-
Freight handlers: They sort and package freight in warehouses.
-
Inventory managers - They oversee the inventory of goods in warehouses.
-
Sales representatives - They sell products.
-
Logistics coordinators - They organize and plan logistics operations.
-
Purchasing agents: They are responsible for purchasing goods and services to support company operations.
-
Customer service representatives – They answer emails and phone calls from customers.
-
Shipping clerks: They process shipping requests and issue bills.
-
Order fillers - They fill orders based on what is ordered and shipped.
-
Quality control inspectors: They inspect outgoing and incoming products for any defects.
-
Other - Logistics has many other job opportunities, including transportation supervisors, logistics specialists, and cargo specialists.
How important is automation in manufacturing?
Automation is essential for both manufacturers and service providers. It allows them to offer services faster and more efficiently. It helps them to lower costs by reducing human errors, and improving productivity.
What are the 7 R's of logistics?
The acronym "7R's" of Logistics stands for seven principles that underpin logistics management. It was developed and published by the International Association of Business Logisticians in 2004 as part of the "Seven Principles of Logistics Management".
The following letters form the acronym:
-
Responsible - to ensure that all actions are within the legal requirements and are not detrimental to others.
-
Reliable – have faith in your ability and capability to keep promises.
-
It is reasonable to use resources efficiently and not waste them.
-
Realistic - Consider all aspects of operations, including environmental impact and cost effectiveness.
-
Respectful - show respect and treat others fairly and fairly
-
Responsive - Look for ways to save time and increase productivity.
-
Recognizable provides value-added products and services to customers
Statistics
- According to a Statista study, U.S. businesses spent $1.63 trillion on logistics in 2019, moving goods from origin to end user through various supply chain network segments. (netsuite.com)
- According to the United Nations Industrial Development Organization (UNIDO), China is the top manufacturer worldwide by 2019 output, producing 28.7% of the total global manufacturing output, followed by the United States, Japan, Germany, and India.[52][53] (en.wikipedia.org)
- Many factories witnessed a 30% increase in output due to the shift to electric motors. (en.wikipedia.org)
- In 2021, an estimated 12.1 million Americans work in the manufacturing sector.6 (investopedia.com)
- (2:04) MTO is a production technique wherein products are customized according to customer specifications, and production only starts after an order is received. (oracle.com)
External Links
How To
How to Use 5S to Increase Productivity in Manufacturing
5S stands to stand for "Sort", “Set In Order", “Standardize", and "Store". Toyota Motor Corporation invented the 5S strategy in 1954. It assists companies in improving their work environments and achieving higher efficiency.
This method has the basic goal of standardizing production processes to make them repeatable. This means that every day tasks such cleaning, sorting/storing, packing, and labeling can be performed. Workers can be more productive by knowing what to expect.
There are five steps to implementing 5S, including Sort, Set In Order, Standardize, Separate and Store. Each step requires a different action, which increases efficiency. If you sort items, it makes them easier to find later. When you set items in an order, you put items together. Then, after you separate your inventory into groups, you store those groups in containers that are easy to access. You can also label your containers to ensure everything is properly labeled.
Employees need to reflect on how they do their jobs. Employees should understand why they do the tasks they do, and then decide if there are better ways to accomplish them. They will need to develop new skills and techniques in order for the 5S system to be implemented.
In addition to improving efficiency, the 5S system also increases morale and teamwork among employees. As they begin to see improvements, they feel motivated to continue working towards the goal of achieving higher levels of efficiency.