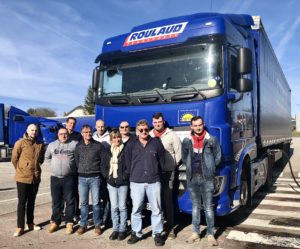
Although America has lost its position on the international market, America's strength in innovation and raw material will continue to be our strength. However the future of manufacturing in America is not what you see today. Instead, it will look more like software and vehicle manufacturing. This article will discuss why American manufacturing is so important and how we can improve it. In this article we will explore the top trends affecting manufacturing in America. Let's get to it!
Trade
U.S. companies' success is dependent on international trade. U.S. manufacturing exports will account for close to half of the sector's production by 2021. Still, manufacturers must do more to take advantage of international trade and sharpen their global competitiveness. Trade agreements that have already broken down trade barriers have produced incredible benefits for U.S. manufacturers. Here are some key factors that will enable U.S. companies to compete in the global marketplace.
Productivity
It is crucial to improve the US manufacturing productivity in order to remain competitive. US productivity has decreased by just 0.7 percent in the last decade. This gap has increased significantly in the last five years, and US manufacturing companies are falling behind their international counterparts. In order for the US manufacturing sector's to remain competitive, it must show step-change productivity improvements. These productivity gains must be substantial - 15% to 20% in key cost areas or 1% to 2 percent per year - and should be sustained by continuous improvement. These gains are vital as they shift the balance of competitiveness from low-cost nations to the US and create a positive cycle.
Safety
The history of the struggle to improve working conditions has been documented. Safety in the workplace has improved because of public outrage as well as organized labor. There have been laws introduced to decrease child labor, reduce workdays and regulate industry. The number of occupational illnesses and injuries has declined over the past few years, though at a slow pace. In the United States, there have been approximately four cases per 100 workers in the last seven years. Despite this being a mere percentage of reported incidents it is an indication that manufacturers take safety very seriously.
Innovation
There are many benefits to the American economy from manufacturing innovation. The manufacturing sector is a source of productivity and new products. New manufacturing processes emerge as technology advances. New products, industries, and jobs are created. Manufacturing can attract both domestic and foreign R&D funding by building a strong R&D network. Innovations in products and processes improve productivity. These benefits are possible with an educational investment. A vibrant manufacturing industry requires innovation in the US.
Exports
Since China joined WTO in 2001 the decline of manufacturing jobs have been accelerated. The US goods trade deficit increased to $350billion during this time due to the increase in imports mainly from China. The stock exchange burst its 14 year-old bubble in 2001. This pushed large parts of the population below the poverty level. In the same time frame, the U.S. Trade deficit grew dramatically, reaching 5.6% of GDP in 2016.
Relative cost advantage
Although it is sometimes assumed that the US has a declining relative cost advantage in manufacturing, the truth is that low-cost economies have held this competitive advantage over U.S. makers for many years. This advantage might be lost in the future with advanced technologies expected to automate roughly 60% of factory processes. This will enable U.S. producers to keep their competitive edge in manufacturing and ensure the highest quality. Here are some ways you can increase U.S. manufacturing's exports.
Imports
We used data from both the U.S. Bureau of Labor Statistics (Census Bureau) to estimate the effect of increased imports on manufacturing jobs. We used the Bureau of Economic Analysis import price indices to convert nominal import data in real 2012 dollars. Manufacturing employment is the dependent variable. The first independent variable is real imports by states.
Costs
Manufacturing in the US is a great option. First, the US can reduce logistics costs. Because products are manufactured closer to the consumer, they can reach them faster. Products made in the USA are more flexible to changing market demands and customer needs. The manufacturing costs in the US are lower than overseas. This study also examines what factors influence the cost of American manufacturing.
FAQ
What are the essential elements of running a logistics firm?
You need to have a lot of knowledge and skills to manage a successful logistic business. Effective communication skills are necessary to work with suppliers and clients. You must be able analyze data and draw out conclusions. You must be able and able to handle stress situations and work under pressure. To improve efficiency, you must be innovative and creative. You must be a strong leader to motivate others and direct them to achieve organizational goals.
You must be organized to meet tight deadlines.
Can certain manufacturing steps be automated?
Yes! Automation has been around since ancient times. The Egyptians discovered the wheel thousands and years ago. Today, robots assist in the assembly of lines.
Actually, robotics can be used in manufacturing for many purposes. These include:
-
Assembly line robots
-
Robot welding
-
Robot painting
-
Robotics inspection
-
Robots that make products
Manufacturing can also be automated in many other ways. For instance, 3D printing allows us make custom products and not have to wait for months or even weeks to get them made.
What is the responsibility for a logistics manager
Logistics managers ensure that goods arrive on time and are unharmed. This is done by using his/her experience and knowledge of the company's products. He/she must also ensure sufficient stock to meet the demand.
What is the distinction between Production Planning or Scheduling?
Production Planning (PP), or production planning, is the process by which you determine what products are needed at any given time. This is done through forecasting demand and identifying production capacities.
Scheduling is the process that assigns dates to tasks so they can get completed within a given timeframe.
Statistics
- In the United States, for example, manufacturing makes up 15% of the economic output. (twi-global.com)
- [54][55] These are the top 50 countries by the total value of manufacturing output in US dollars for its noted year according to World Bank.[56] (en.wikipedia.org)
- You can multiply the result by 100 to get the total percent of monthly overhead. (investopedia.com)
- Job #1 is delivering the ordered product according to specifications: color, size, brand, and quantity. (netsuite.com)
- (2:04) MTO is a production technique wherein products are customized according to customer specifications, and production only starts after an order is received. (oracle.com)
External Links
How To
Six Sigma and Manufacturing
Six Sigma is "the application statistical process control (SPC), techniques for continuous improvement." Motorola's Quality Improvement Department in Tokyo, Japan developed Six Sigma in 1986. Six Sigma's main goal is to improve process quality by standardizing processes and eliminating defects. Many companies have adopted this method in recent years. They believe there is no such thing a perfect product or service. Six Sigma's main objective is to reduce variations from the production average. You can calculate the percentage of deviation from the norm by taking a sample of your product and comparing it to the average. If you notice a large deviation, then it is time to fix it.
Understanding the dynamics of variability within your business is the first step in Six Sigma. Once you understand this, you can then identify the causes of variation. Also, you will need to identify the sources of variation. Random variations are caused by human errors. Systematic variations can be caused by outside factors. For example, if you're making widgets, and some of them fall off the assembly line, those would be considered random variations. If however, you notice that each time you assemble a widget it falls apart in exactly the same spot, that is a problem.
Once you've identified the problem areas you need to find solutions. This could mean changing your approach or redesigning the entire process. Once you have implemented the changes, it is important to test them again to ensure they work. If they don't work you need to rework them and come up a better plan.