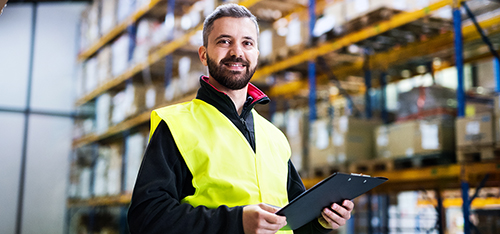
Facilities engineers are also known as maintenance engineers. They provide support in the engineering and construction of buildings and operations. You will find their tasks include planning and implementing procedures, making recommendations for repairs and upgrades, and organizing routine and emergency maintenance. They can be involved in a variety of engineering disciplines including plumbing, electrical, and mechanical. In addition to their technical expertise, they also have a solid understanding of construction law, safety standards, and other regulatory requirements.
As a career, facilities engineers typically begin at the entry level, and can quickly advance to more senior positions. The best way to stand out in the field is to build a strong portfolio, which may include engineering projects, research, and articles. Facilities engineers need to continue learning about their field. This will allow them to stand out when applying to a new position.
Even though certification is not necessary for all facilities engineers it can make a difference when you apply for a new job. A professional engineer should have an extensive knowledge of engineering principles. For example, a facility engineer should have experience with predictive maintenance, asset reliability-centered maintenance strategies, and the design of facilities.
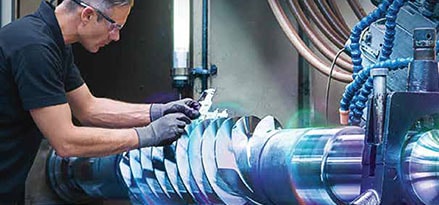
Facilities engineers can work in office, construction, manufacturing, or other settings. They plan and execute processes to ensure that utilities are running safely and efficiently. Facilities engineers work closely with managers and other engineers. This helps to make work more efficient and resolves any problems.
The specific type of facility an engineer is working in will determine the responsibilities. The job requires good time management skills and problem-solving skills. It also requires the ability to work well in a team environment. In a typical day, a facility engineer can perform hundreds of tasks. The engineer is usually responsible for fixing or troubleshooting problems with electrical, mechanical or plumbing equipment.
Many websites offer information and news about the field, including the Association of Facility Engineers' (AFE) website. These websites contain information about the profession, including a sample resume.
You can also find articles and books on facilities engineering, as well as training courses and networking opportunities. For a successful facility engineer to succeed, you need to have organizational skills and a solid understanding about building and safety codes.
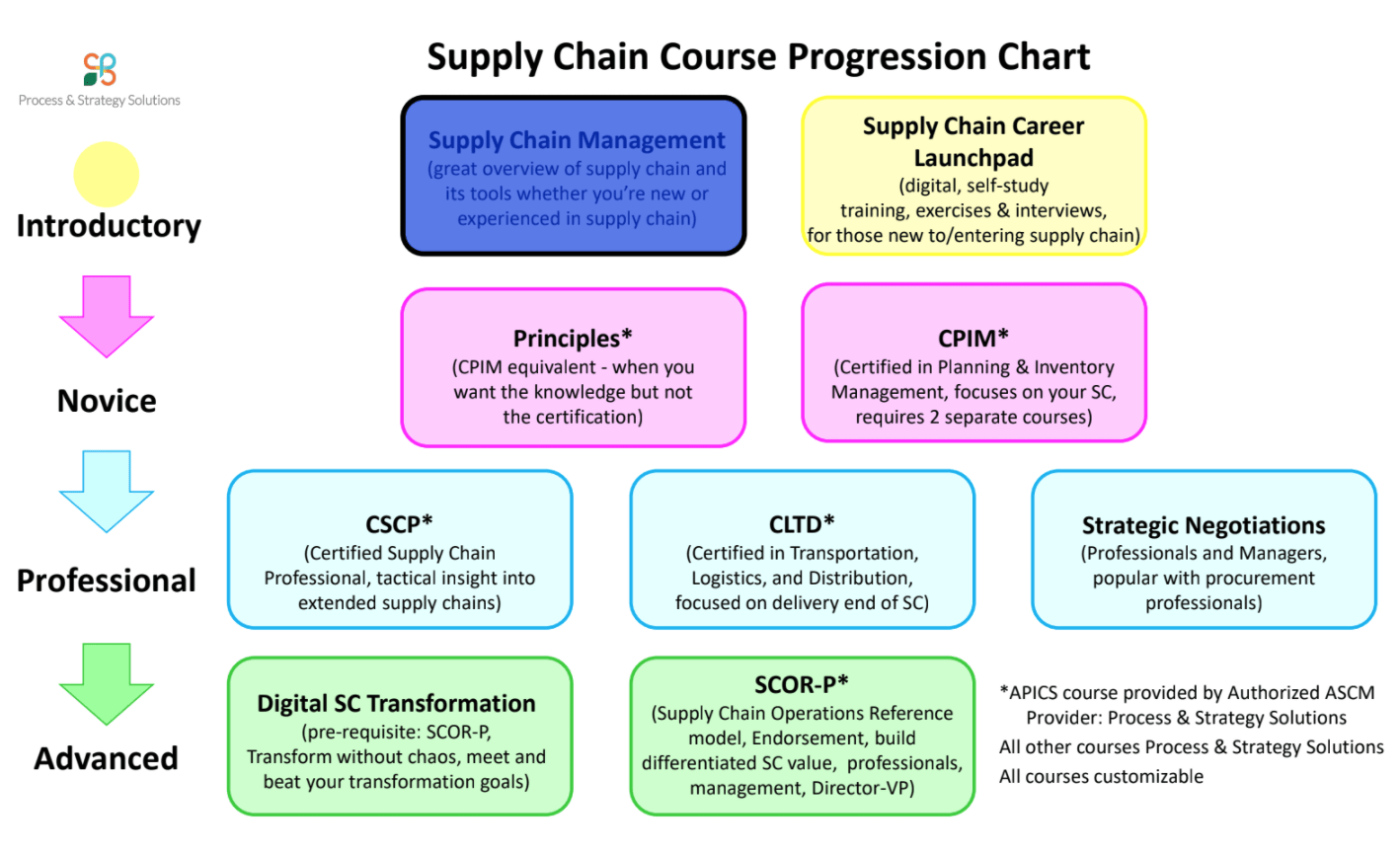
It's important to note that some of the most advanced facilities engineers are able to analyze data and perform a number of tasks at once. This requires a working knowledge in AutoCAD as well as construction techniques such as the CAM. The skills of project management, critical thought, and problem-solving are also beneficial.
One of the biggest advantages of a facilities engineer job is the chance to work with a large array of people. These engineers can work with many different materials and coordinate other engineers' work.
FAQ
What skills does a production planner need?
Production planners must be flexible, organized, and able handle multiple tasks. Communication skills are essential to ensure that you can communicate effectively with clients, colleagues, and customers.
What is the importance of automation in manufacturing?
Automating is not just important for manufacturers, but also for service providers. It allows them provide faster and more efficient services. They can also reduce their costs by reducing human error and improving productivity.
What are the jobs in logistics?
There are different kinds of jobs available in logistics. Some of them are:
-
Warehouse workers: They load and unload trucks, pallets, and other cargo.
-
Transport drivers - These are people who drive trucks and trailers to transport goods or perform pick-ups.
-
Freight handlers - They sort and pack freight in warehouses.
-
Inventory managers – These people oversee inventory at warehouses.
-
Sales reps are people who sell products to customers.
-
Logistics coordinators: They plan and manage logistics operations.
-
Purchasing agents - They buy goods and services that are necessary for company operations.
-
Customer service agents - They answer phone calls and respond to emails.
-
Shipping clerks – They process shipping orders, and issue bills.
-
Order fillers: They fill orders based off what has been ordered and shipped.
-
Quality control inspectors - They check incoming and outgoing products for defects.
-
Others - There are many types of jobs in logistics such as transport supervisors and cargo specialists.
How can manufacturing reduce production bottlenecks?
Production bottlenecks can be avoided by ensuring that processes are running smoothly during the entire production process, starting with the receipt of an order and ending when the product ships.
This includes both quality control and capacity planning.
The best way to do this is to use continuous improvement techniques such as Six Sigma.
Six Sigma management is a system that improves quality and reduces waste within your organization.
It is focused on creating consistency and eliminating variation in your work.
What is it like to manage a logistics company?
To be a successful businessman in logistics, you will need many skills and knowledge. To communicate effectively with clients and suppliers, you must be able to communicate well. You need to understand how to analyze data and draw conclusions from it. You must be able manage stress and pressure under pressure. To increase efficiency and creativity, you need to be creative. Strong leadership qualities are essential to motivate your team and help them achieve their organizational goals.
You should also be organized and efficient to meet tight deadlines.
What can I do to learn more about manufacturing?
The best way to learn about manufacturing is through hands-on experience. However, if that's not possible, you can always read books or watch educational videos.
What is meant by manufacturing industries?
Manufacturing Industries are companies that manufacture products. Consumers are those who purchase these products. These companies use a variety processes such as distribution, retailing and management to accomplish their purpose. They manufacture goods from raw materials using machines and other equipment. This includes all types if manufactured goods.
Statistics
- (2:04) MTO is a production technique wherein products are customized according to customer specifications, and production only starts after an order is received. (oracle.com)
- According to a Statista study, U.S. businesses spent $1.63 trillion on logistics in 2019, moving goods from origin to end user through various supply chain network segments. (netsuite.com)
- According to the United Nations Industrial Development Organization (UNIDO), China is the top manufacturer worldwide by 2019 output, producing 28.7% of the total global manufacturing output, followed by the United States, Japan, Germany, and India.[52][53] (en.wikipedia.org)
- It's estimated that 10.8% of the U.S. GDP in 2020 was contributed to manufacturing. (investopedia.com)
- In the United States, for example, manufacturing makes up 15% of the economic output. (twi-global.com)
External Links
How To
Six Sigma and Manufacturing
Six Sigma is defined as "the application of statistical process control (SPC) techniques to achieve continuous improvement." Motorola's Quality Improvement Department developed it at their Tokyo plant in Japan in 1986. Six Sigma's main goal is to improve process quality by standardizing processes and eliminating defects. Many companies have adopted this method in recent years. They believe there is no such thing a perfect product or service. Six Sigma's primary goal is to reduce variation from the average value of production. This means that if you take a sample of your product, then measure its performance against the average, you can find out what percentage of the time the process deviates from the norm. If this deviation is too big, you know something needs fixing.
Understanding the nature of variability in your business is the first step to Six Sigma. Once you have a good understanding of the basics, you can identify potential sources of variation. This will allow you to decide if these variations are random and systematic. Random variations occur when people make mistakes; systematic ones are caused by factors outside the process itself. For example, if you're making widgets, and some of them fall off the assembly line, those would be considered random variations. However, if you notice that every time you assemble a widget, it always falls apart at exactly the same place, then that would be a systematic problem.
Once you've identified the problem areas you need to find solutions. You might need to change the way you work or completely redesign the process. Once you have implemented the changes, it is important to test them again to ensure they work. If they didn't work, then you'll need to go back to the drawing board and come up with another plan.