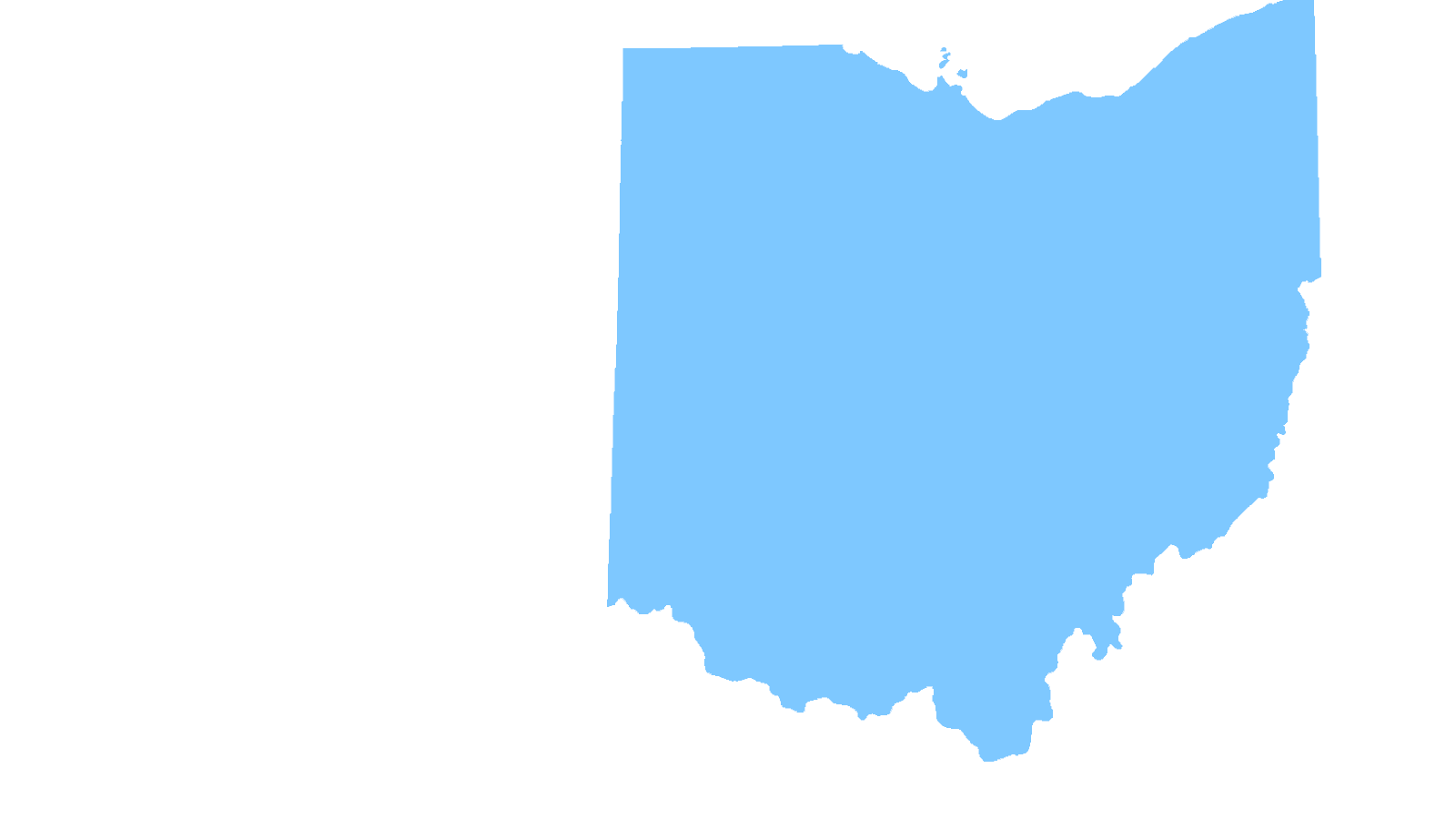
DFSS (Design for Six Sigma), a design methodology, uses a variety of methods to design a product or service. It is intended to reduce waste, improve quality and increase market share. This is a proven method to improve your products or services.
DFSS allows customers to be included in the design process. This helps ensure that your product or service is the most suitable for your customers' needs. It ensures that your product meets high standards when it is launched to the marketplace. DFSS is often used for the design of a product or a service. It can also be used in the design of products and/or services to replace or enhance existing products.
The DFSS team will determine what the customer wants and needs in the initial phase. This can involve gathering information, interviewing customers, or surveying customers. In order to find the best product or design, the design team reviews other products and designs. This includes the development or modification of substitute ideas and defining functional requirements. Additional steps may be required depending on how complex the project is.
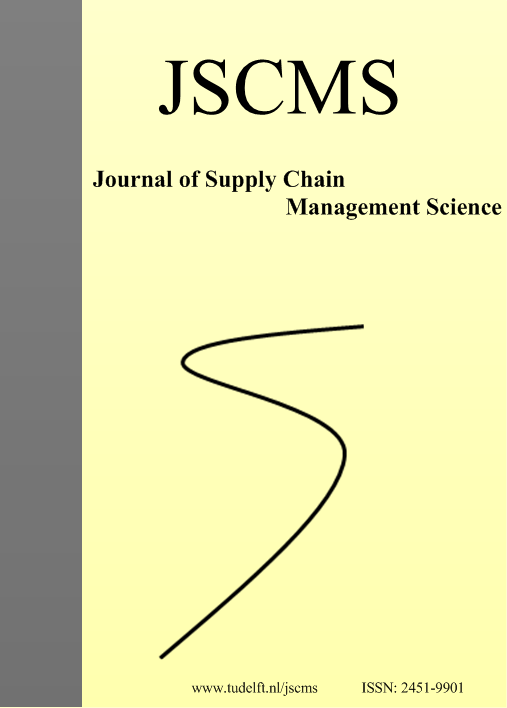
DFSS is a design method that allows companies to design products and services efficiently. It's also used to identify potential problems and prevent them from becoming serious issues. It also reduces waste and increases the profitability of your company. It is intended to increase the effectiveness a product, or service by identifying its process parameters that make it more successful.
There are many methods to implement DFSS. DMADV, which follows a 5-step process, is the most common method for implementing DFSS. It starts with defining the customer, identifying their needs, and developing a design concept. This method has a solid engineering foundation and is frequently used to develop new products or services. This includes a measurement phase and an analysis phase to determine the product's effectiveness.
The second phase involves the optimization step. This involves evaluating the product's performance across multiple performance levels. This step is crucial for the development of new business procedures. This stage has two goals: to reduce variability, and to ensure the product is stable over time.
The final stage of the verification process is where the product is verified to be stable. This is also used to confirm that the product's capabilities have been tested and verified over time. The process will also include validation testing. Validation testing is typically completed once the design has been approved.
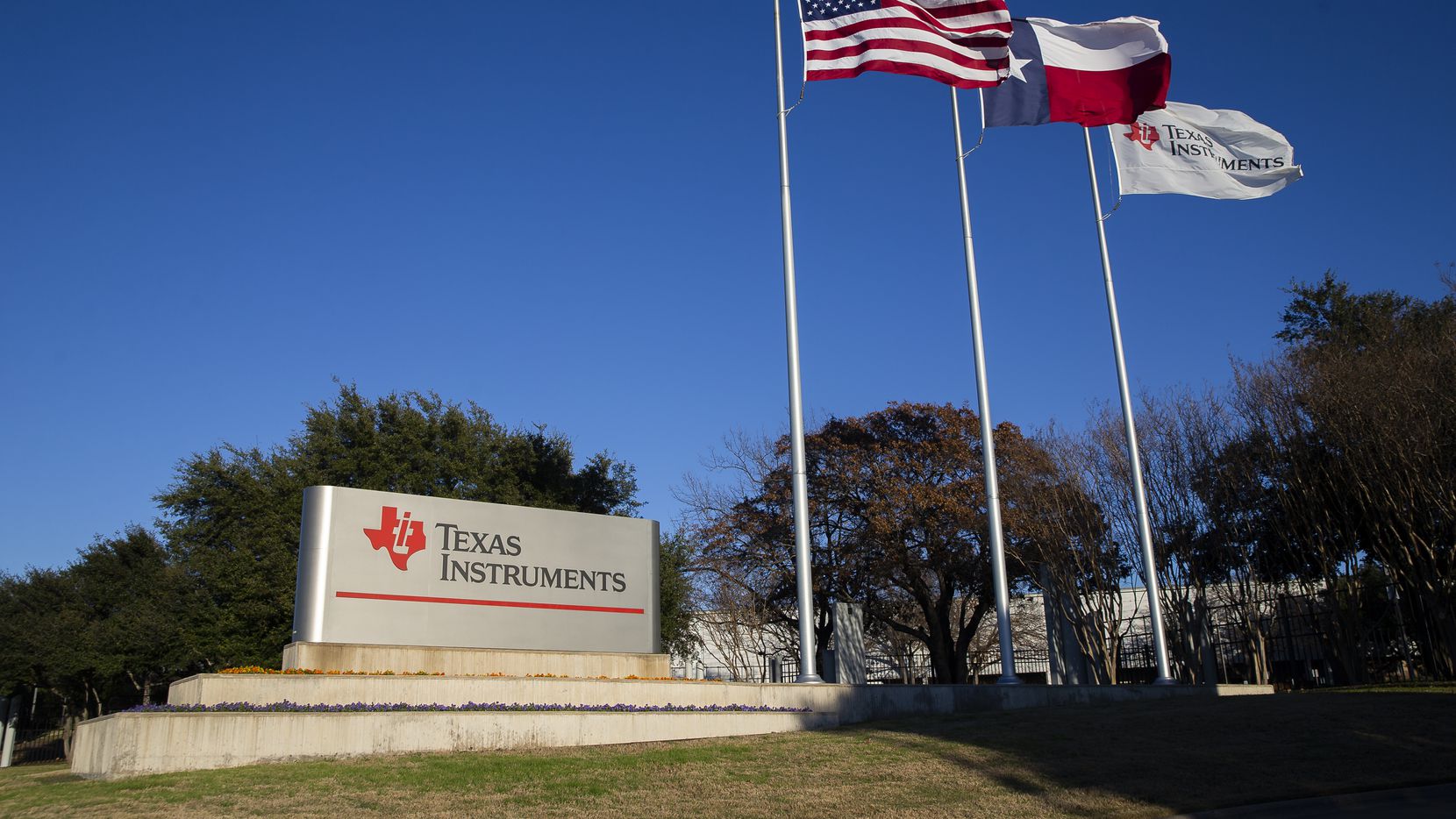
You will be able to implement DFSS successfully if you have a detailed process diagram that shows all the steps involved in the design. A detailed process map should contain information about resources, timeframes, milestones, as well as details about the budget. You must also be able pinpoint any external involvement required. To make sure that the product meets all customers' needs, it may be necessary to develop prototypes. It is important to establish clear rewards for achieving project goals when implementing DFSS.
FAQ
What jobs are available in logistics?
Logistics can offer many different jobs. Some examples are:
-
Warehouse workers - They load trucks and pallets.
-
Transport drivers - These are people who drive trucks and trailers to transport goods or perform pick-ups.
-
Freight handlers are people who sort and pack freight into warehouses.
-
Inventory managers – These people oversee inventory at warehouses.
-
Sales representatives - They sell products.
-
Logistics coordinators - They organize and plan logistics operations.
-
Purchasing agents - They purchase goods and services needed for company operations.
-
Customer service representatives - They answer calls and emails from customers.
-
Shippers clerks - They process shipping order and issue bills.
-
Order fillers - These people fill orders based on what has been ordered.
-
Quality control inspectors: They inspect outgoing and incoming products for any defects.
-
Other - Logistics has many other job opportunities, including transportation supervisors, logistics specialists, and cargo specialists.
How can overproduction in manufacturing be reduced?
Better inventory management is key to reducing excess production. This would reduce the time spent on unproductive activities like purchasing, storing and maintaining excess stock. By doing this, we could free up resources for other productive tasks.
One way to do this is to adopt a Kanban system. A Kanban Board is a visual display that tracks work progress. Work items are moved through various states to reach their destination in a Kanban system. Each state represents an individual priority level.
For instance, when work moves from one stage to another, the current task is complete enough to be moved to the next stage. A task that is still in the initial stages of a process will be considered complete until it moves on to the next stage.
This helps to keep work moving forward while ensuring that no work is left behind. Managers can see how much work has been done and the status of each task at any time with a Kanban Board. This allows them to adjust their workflows based on real-time information.
Lean manufacturing, another method to control inventory levels, is also an option. Lean manufacturing emphasizes eliminating waste in all phases of production. Anything that doesn't add value to the product is considered waste. There are several types of waste that you might encounter:
-
Overproduction
-
Inventory
-
Unnecessary packaging
-
Excess materials
These ideas will help manufacturers increase efficiency and lower costs.
Can we automate some parts of manufacturing?
Yes! Yes! Automation has existed since ancient times. The Egyptians invented the wheel thousands of years ago. Nowadays, we use robots for assembly lines.
There are many uses of robotics today in manufacturing. These include:
-
Robots for assembly line
-
Robot welding
-
Robot painting
-
Robotics inspection
-
Robots that create products
Manufacturing can also be automated in many other ways. For instance, 3D printing allows us make custom products and not have to wait for months or even weeks to get them made.
What is production planning?
Production Planning includes planning for all aspects related to production. This document aims to ensure that everything is planned and ready when you are ready to shoot. It should also provide information about how best to produce the best results while on set. This includes location information, crew details, equipment specifications, and casting lists.
The first step in filming is to define what you want. You may have decided where to shoot or even specific locations you want to use. Once you have identified your locations and scenes, you can start working out which elements you require for each scene. You might decide you need a car, but not sure what make or model. To narrow your options, you can search online for available models.
After you've found the perfect car, it's time to start thinking about adding extras. Are you looking for people to sit in the front seats? Maybe you need someone to move around in the back. You might want to change your interior color from black and white. These questions can help you decide the right look for your car. You can also think about the type of shots you want to get. You will be filming close-ups and wide angles. Maybe the engine or steering wheel is what you are looking to film. These things will help you to identify the car that you are looking for.
Once you have determined all of the above, you can move on to creating a schedule. You will know when you should start and when you should finish shooting. Each day will include the time when you need to arrive at the location, when you need to leave and when you need to return home. So everyone is clear about what they need to do. If you need to hire extra staff, you can make sure you book them in advance. You don't want to hire someone who won't show up because he didn't know.
It is important to calculate the amount of filming days when you are creating your schedule. Some projects take only a few days while others can last several weeks. It is important to consider whether you require more than one photo per day when you create your schedule. Shooting multiple takes over the same location will increase costs and take longer to complete. It is better to be cautious and take fewer shots than you risk losing money if you are not sure if multiple takes are necessary.
Budgeting is another crucial aspect of production plan. As it will allow you and your team to work within your financial means, setting a realistic budget is crucial. If you have to reduce your budget due to unexpected circumstances, you can always lower it later. It is important to not overestimate how much you will spend. You'll end up with less money after paying for other things if the cost is underestimated.
Production planning is a detailed process. But, once you understand the workings of everything, it becomes easier for future projects to be planned.
What does it mean to be a manufacturer?
Manufacturing Industries are companies that manufacture products. Consumers are those who purchase these products. These companies use a variety processes such as distribution, retailing and management to accomplish their purpose. They manufacture goods from raw materials using machines and other equipment. This includes all types of manufactured goods, including food items, clothing, building supplies, furniture, toys, electronics, tools, machinery, vehicles, pharmaceuticals, medical devices, chemicals, and many others.
What are the logistics products?
Logistics is the process of moving goods from one point to another.
They include all aspects of transport, including packaging, loading, transporting, unloading, storing, warehousing, inventory management, customer service, distribution, returns, and recycling.
Logisticians ensure that products reach the right destination at the right moment and under safe conditions. They help companies manage their supply chain efficiency by providing information on demand forecasts, stock levels, production schedules, and availability of raw materials.
They can also track shipments in transit and monitor quality standards.
What are the responsibilities of a logistic manager?
A logistics manager ensures that all goods are delivered on time and without damage. This is done through his/her expertise and knowledge about the company's product range. He/she also needs to ensure adequate stock to meet demand.
Statistics
- You can multiply the result by 100 to get the total percent of monthly overhead. (investopedia.com)
- (2:04) MTO is a production technique wherein products are customized according to customer specifications, and production only starts after an order is received. (oracle.com)
- Many factories witnessed a 30% increase in output due to the shift to electric motors. (en.wikipedia.org)
- According to a Statista study, U.S. businesses spent $1.63 trillion on logistics in 2019, moving goods from origin to end user through various supply chain network segments. (netsuite.com)
- [54][55] These are the top 50 countries by the total value of manufacturing output in US dollars for its noted year according to World Bank.[56] (en.wikipedia.org)
External Links
How To
Six Sigma: How to Use it in Manufacturing
Six Sigma is defined as "the application of statistical process control (SPC) techniques to achieve continuous improvement." Motorola's Quality Improvement Department in Tokyo, Japan developed Six Sigma in 1986. Six Sigma's basic concept is to improve quality and eliminate defects through standardization. This method has been adopted by many companies in recent years as they believe there are no perfect products or services. The main goal of Six Sigma is to reduce variation from the mean value of production. This means that you can take a sample from your product and then compare its performance to the average to find out how often the process differs from the norm. If this deviation is too big, you know something needs fixing.
The first step toward implementing Six Sigma is understanding how variability works in your business. Once you have a good understanding of the basics, you can identify potential sources of variation. You'll also want to determine whether these variations are random or systematic. Random variations occur when people do mistakes. Symmetrical variations are caused due to factors beyond the process. You could consider random variations if some widgets fall off the assembly lines. You might notice that your widgets always fall apart at the same place every time you put them together.
Once you have identified the problem, you can design solutions. This could mean changing your approach or redesigning the entire process. To verify that the changes have worked, you need to test them again. If they don't work, you will need to go back to the drawing boards and create a new plan.