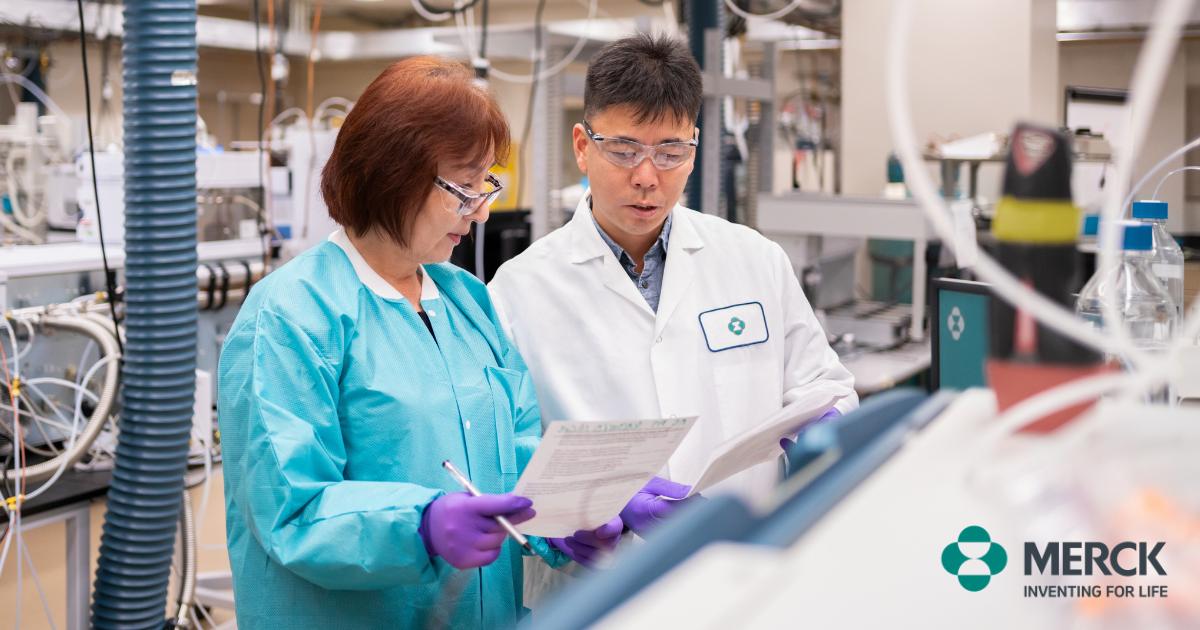
Murata Manufacturing Co. Ltd. is located in Kyoto Japan and can be a great choice for an electronics component manufacturer. The company's name alone will tell you that it has been in existence for over 100 years. There are other companies you should know about. Below are details about their products. This company produces electronic parts that can be used in many different kinds of electronics.
Murata Manufacturing Co., Ltd.
Murata Manufacturing Co., Ltd., a Japanese manufacturer of electronic components, is located in Kyoto, Japan. It produces electronic components such a circuit board, transistors, as well as LEDs. Continue reading to learn more about the company’s products. Learn more about Murata's manufacturing process. You can also view the most popular Murata products. For more information, visit Murata's website.
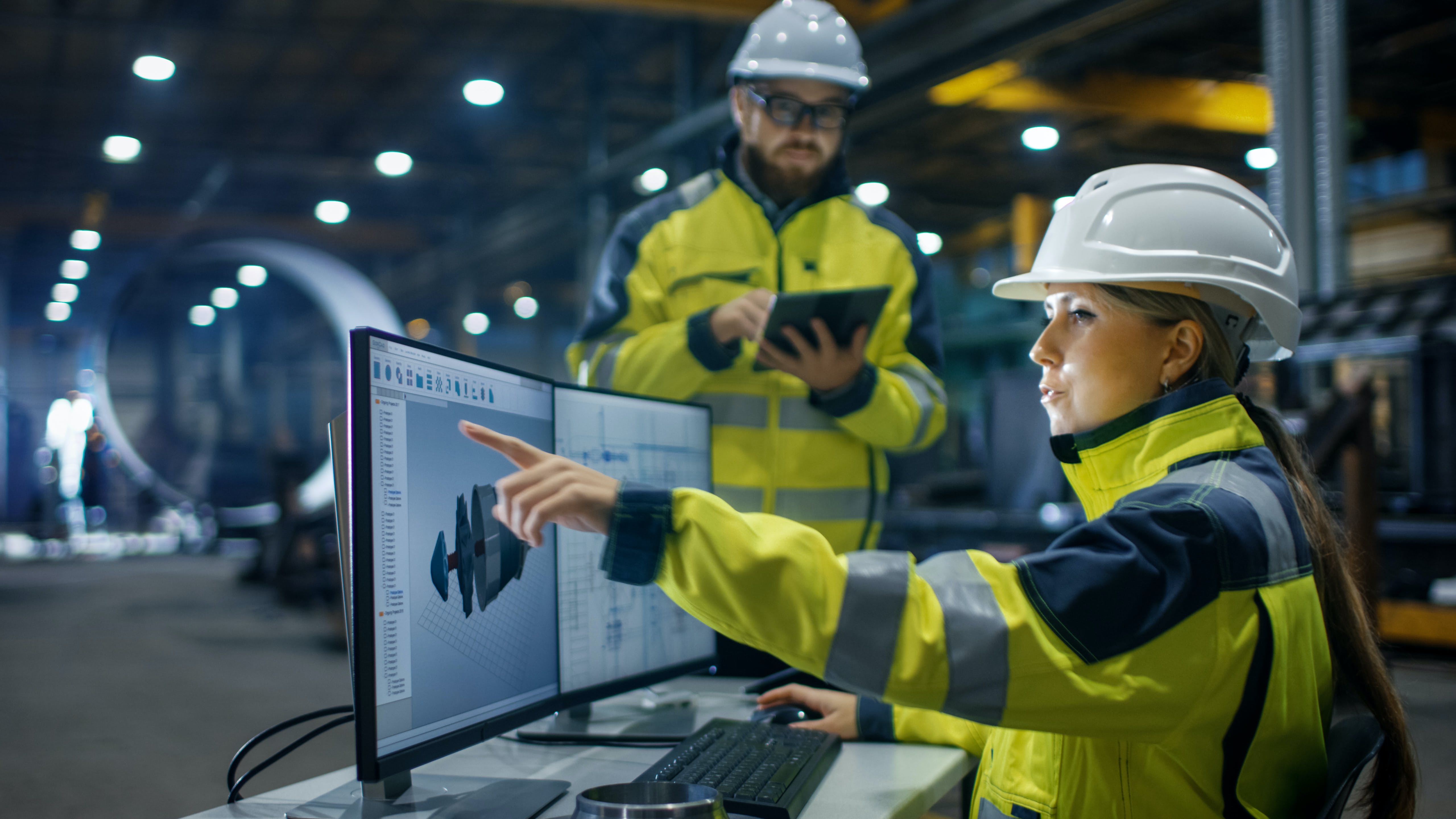
Murata Energy Device Singapore Pte Ltd
The company's name translates to "Making Primary Batteries." This is a subsidiary of the Japanese company Murata Manufacturing Co. Ltd., which is headquartered in Nagaokakyo. Murata Singapore, which was founded in 1972, is the oldest Murata factory outside Japan. Its mission, is to fulfill the South East Asia electronics market demand. Murata acquired Sony Energy Devices Corporation, in 2017. The company's headquarters is located at 1 Tuas Road, Singapore.
Murata Electronics Trading (Tianjin) Co. Ltd
Since 2007, the Murata Electronics Trading Corporation (METC), has been in Tianjin. MEC is originally from Japan. It focuses its efforts on supplying high quality electronic parts to global markets. The company has been expanding its business to include the sale of components that reduce EMI over the last few years. The company also offers technical support services to solve EMC issues for customers.
Murata Vios
Murata Vios medical technology is moving onto hospital floors. Japanese company is developing a system to detect signs of early clinical decline. The system is wireless and works with Hicuity Health, which provides clinical care oversight and engages specialists and bedside clinicians in response to potential patient deterioration. Murata Vios combines these two technologies to offer a new service for care providers and clinicians.
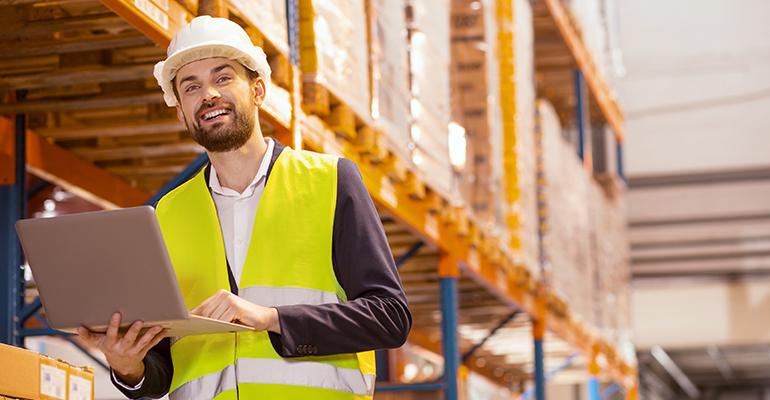
PointClickCare Integration with Murata Vios
Murata, Inc. recently integrated the Vios Monitoring System with PointClickCare, cloud-based senior care program vendor. This integration eliminates transcription errors as well as data entry lags. It also increases clinician efficiency. Vios Monitoring System gathers information such as heart beat, oxygen levels, pulse rate, respiratory rate, and posture data. These data are vital for the implementation of a patient-centric care program.
FAQ
What are manufacturing and logistics?
Manufacturing is the act of producing goods from raw materials using machines and processes. Logistics is the management of all aspects of supply chain activities, including procurement, production planning, distribution, warehousing, inventory control, transportation, and customer service. Manufacturing and logistics are often considered together as a broader term that encompasses both the process of creating products and delivering them to customers.
What is the difference between Production Planning, Scheduling and Production Planning?
Production Planning (PP) refers to the process of determining how much production is needed at any given moment. This can be done by forecasting demand and identifying production capabilities.
Scheduling refers to the process of allocating specific dates to tasks in order that they can be completed within a specified timeframe.
What are the differences between these four types?
Manufacturing refers to the transformation of raw materials into useful products by using machines and processes. It involves many different activities such as designing, building, testing, packaging, shipping, selling, servicing, etc.
What does it mean to be a manufacturer?
Manufacturing Industries are businesses that produce products for sale. Consumers are the people who purchase these products. These companies employ many processes to achieve this purpose, such as production and distribution, retailing, management and so on. They produce goods from raw materials by using machines and other machinery. This includes all types if manufactured goods.
What are the responsibilities for a manufacturing manager
A manufacturing manager must ensure that all manufacturing processes are efficient and effective. They should also be aware of any problems within the company and act accordingly.
They must also be able to communicate with sales and marketing departments.
They should be up to date on the latest trends and be able apply this knowledge to increase productivity and efficiency.
Statistics
- According to the United Nations Industrial Development Organization (UNIDO), China is the top manufacturer worldwide by 2019 output, producing 28.7% of the total global manufacturing output, followed by the United States, Japan, Germany, and India.[52][53] (en.wikipedia.org)
- According to a Statista study, U.S. businesses spent $1.63 trillion on logistics in 2019, moving goods from origin to end user through various supply chain network segments. (netsuite.com)
- Job #1 is delivering the ordered product according to specifications: color, size, brand, and quantity. (netsuite.com)
- It's estimated that 10.8% of the U.S. GDP in 2020 was contributed to manufacturing. (investopedia.com)
- In 2021, an estimated 12.1 million Americans work in the manufacturing sector.6 (investopedia.com)
External Links
How To
Six Sigma in Manufacturing
Six Sigma is defined as "the application of statistical process control (SPC) techniques to achieve continuous improvement." Motorola's Quality Improvement Department in Tokyo, Japan developed Six Sigma in 1986. The basic idea behind Six Sigma is to improve quality by improving processes through standardization and eliminating defects. In recent years, many companies have adopted this method because they believe there is no such thing as perfect products or services. The main goal of Six Sigma is to reduce variation from the mean value of production. It is possible to measure the performance of your product against an average and find the percentage of time that it differs from the norm. If the deviation is excessive, it's likely that something needs to be fixed.
Understanding the dynamics of variability within your business is the first step in Six Sigma. Once you have this understanding, you will need to identify sources and causes of variation. It is important to identify whether the variations are random or systemic. Random variations are caused by human errors. Systematic variations can be caused by outside factors. You could consider random variations if some widgets fall off the assembly lines. It would be considered a systematic problem if every widget that you build falls apart at the same location each time.
Once you identify the problem areas, it is time to create solutions. The solution could involve changing how you do things, or redesigning your entire process. Test them again once you've implemented the changes. If they fail, you can go back to the drawing board to come up with a different plan.