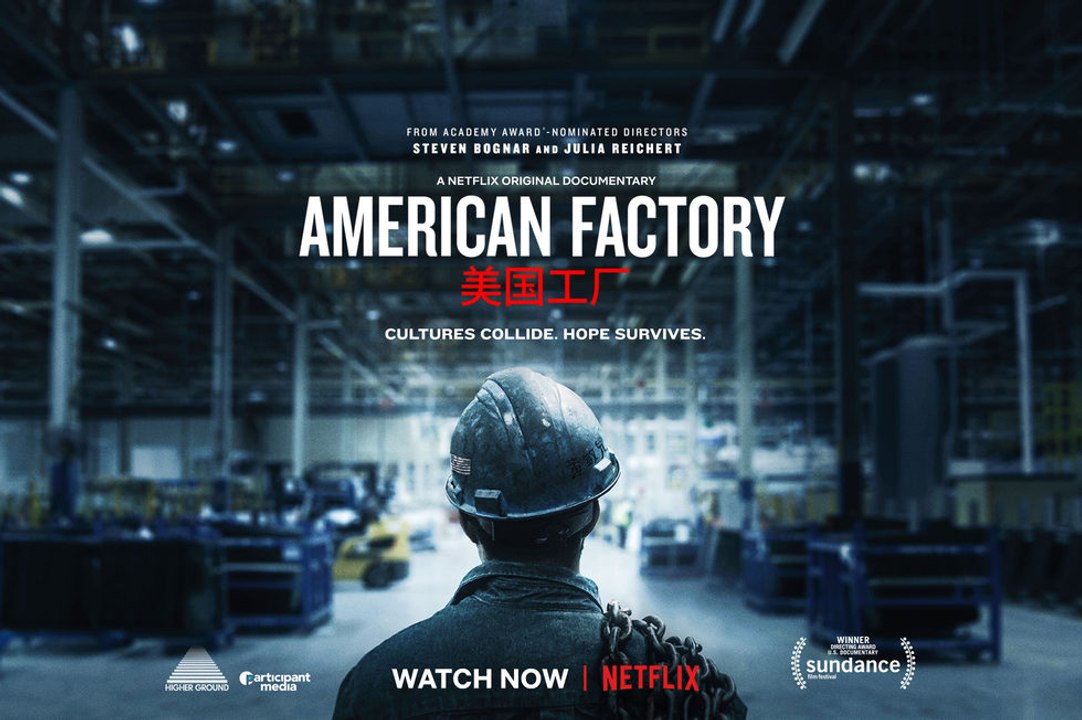
Whether you are running a small business or the enterprise arm of a major corporation, supply chain risk management is a necessary component to maintaining a robust operation. There are many risks that can occur, from the seemingly mundane to the potentially disastrous. You can prevent losses by creating a plan and following the implementation strategy.
Data sharing is an essential part of a supply chain continuity program. You are more likely to have supplier disputes or vendor failures if your company relies solely on one supplier. If your company is part a multi-supplier consortium you are more likely not to experience supply disruptions. You may also have the ability to negotiate with another supplier.
A complex network of contractors can also increase your risk of vendor fraud and duplicate billing. To help mitigate these risks, you can develop a risk assessment methodology, which can include a comprehensive assessment of your suppliers, partners, and other tier one components.
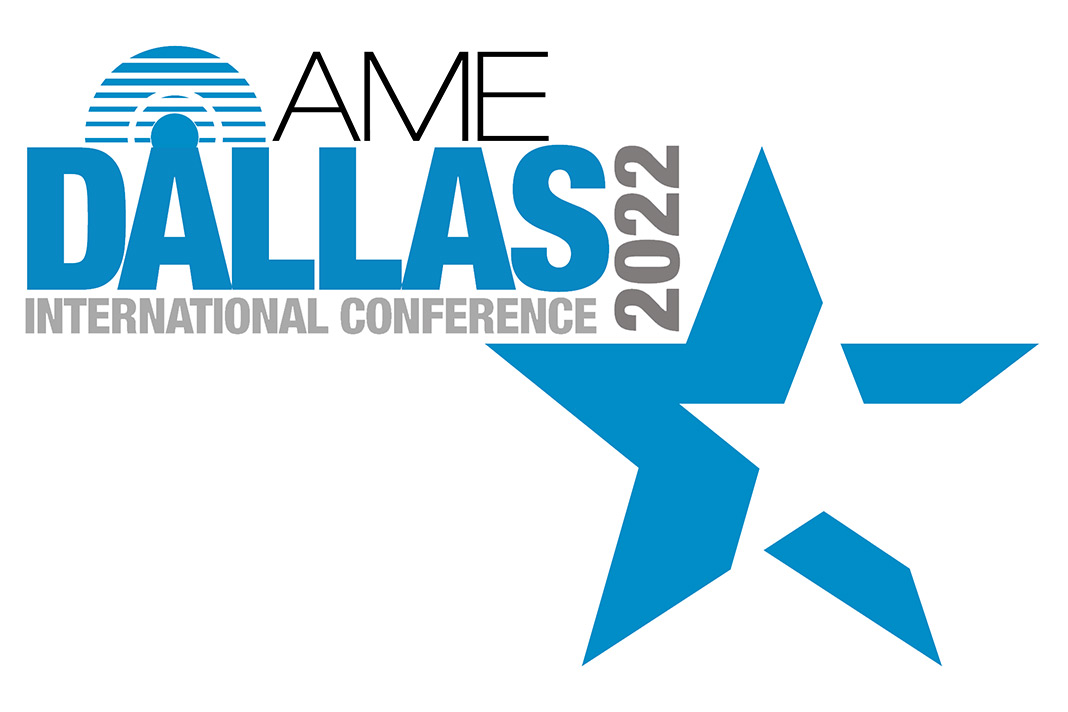
To develop a supply chain risk management program that is effective, it is important to first identify the key elements of a supply chain. Next, quantify and measure these elements and then create an action plan. This should involve the aforementioned items, plus a few more. Proactive monitoring systems are the most important aspect. Your executives need to have real-time, accurate data about supply chain risk. By tracking supply risks in real time, you are better equipped to make informed decisions and to react in a timely manner.
It is important to remember that the resilience of your supply chains is dependent on governance as you assess and quantify your risks. Consider the role of all stakeholders. The supplier bankruptcy that caused disruption in the supply chain of the pharmaceutical industry could have easily been avoided if the company had correctly scoredcarded all its suppliers.
A well-planned plan is essential for minimizing supply chain crises. However, implementing the right contingency plans is not always easy. Many businesses neglect to make the effort to have enough contingency planning for every risk they face. These plans should be designed to have the highest possible impact.
The PPPR (preventive, preparedness and response) method is an internationally recognized standard in supply chain risk management. This is a strong approach that will help improve your ability monitor and respond to disruptions in supply chains. It can also be used in conjunction other strategies to protect your business from potential risks. Using a PPPR guide to your organization can mean the difference between survival and success in today's market.
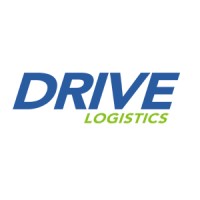
Getting the right data from your suppliers can help you to understand their history and what they have to offer. This information can help you make informed decisions, regardless of whether you're looking to expand your sourcing efforts and/or improve your existing processes. Information that is reliable can help you offer the right risk premiums for your insurers.
FAQ
What are manufacturing and logistics?
Manufacturing is the act of producing goods from raw materials using machines and processes. Logistics includes all aspects related to supply chain management, such as procurement, distribution planning, inventory control and transportation. Manufacturing and logistics are often considered together as a broader term that encompasses both the process of creating products and delivering them to customers.
What are the responsibilities of a logistic manager?
A logistics manager ensures that all goods are delivered on time and without damage. This is done through his/her expertise and knowledge about the company's product range. He/she should also ensure enough stock is available to meet demand.
How can manufacturing efficiency improved?
The first step is to identify the most important factors affecting production time. We then need to figure out how to improve these variables. If you don’t know where to begin, consider which factors have the largest impact on production times. Once you have identified them, it is time to identify solutions.
Statistics
- You can multiply the result by 100 to get the total percent of monthly overhead. (investopedia.com)
- [54][55] These are the top 50 countries by the total value of manufacturing output in US dollars for its noted year according to World Bank.[56] (en.wikipedia.org)
- Job #1 is delivering the ordered product according to specifications: color, size, brand, and quantity. (netsuite.com)
- According to a Statista study, U.S. businesses spent $1.63 trillion on logistics in 2019, moving goods from origin to end user through various supply chain network segments. (netsuite.com)
- In the United States, for example, manufacturing makes up 15% of the economic output. (twi-global.com)
External Links
How To
How to use the Just In-Time Production Method
Just-intime (JIT), which is a method to minimize costs and maximize efficiency in business process, is one way. It's a way to ensure that you get the right resources at just the right time. This means that only what you use is charged to your account. The term was first coined by Frederick Taylor, who developed his theory while working as a foreman in the early 1900s. Taylor observed that overtime was paid to workers if they were late in working. He decided to ensure workers have enough time to do their jobs before starting work to improve productivity.
JIT teaches you to plan ahead and prepare everything so you don’t waste time. Look at your entire project, from start to end. Make sure you have enough resources in place to deal with any unexpected problems. If you expect problems to arise, you will be able to provide the necessary equipment and personnel to address them. This will prevent you from spending extra money on unnecessary things.
There are many JIT methods.
-
Demand-driven JIT: You order the parts and materials you need for your project every other day. This will allow to track how much material has been used up. It will also allow you to predict how long it takes to produce more.
-
Inventory-based: This allows you to store the materials necessary for your projects in advance. This allows one to predict how much they will sell.
-
Project-driven: This method allows you to set aside enough funds for your project. Knowing how much money you have available will help you purchase the correct amount of materials.
-
Resource-based JIT: This is the most popular form of JIT. You allocate resources based on the demand. You will, for example, assign more staff to deal with large orders. If you don't have many orders, you'll assign fewer people to handle the workload.
-
Cost-based: This is a similar approach to resource-based but you are not only concerned with how many people you have, but also how much each one costs.
-
Price-based: This is a variant of cost-based. However, instead of focusing on the individual workers' costs, this looks at the total price of the company.
-
Material-based - This is a variant of cost-based. But instead of looking at the total company cost, you focus on how much raw material you spend per year.
-
Time-based: Another variation of resource-based JIT. Instead of focusing on the cost of each employee, you will focus on the time it takes to complete a project.
-
Quality-based JIT: This is another variation of resource based JIT. Instead of focusing on the cost of each worker or how long it takes, think about how high quality your product is.
-
Value-based JIT is the newest form of JIT. You don't worry about whether the products work or if they meet customer expectations. Instead, you're focused on how much value you add to the market.
-
Stock-based: This inventory-based approach focuses on how many items are being produced at any one time. It's used when you want to maximize production while minimizing inventory.
-
Just-intime (JIT), planning is a combination JIT management and supply chain management. It refers to the process of scheduling the delivery of components as soon as they are ordered. It's important because it reduces lead times and increases throughput.