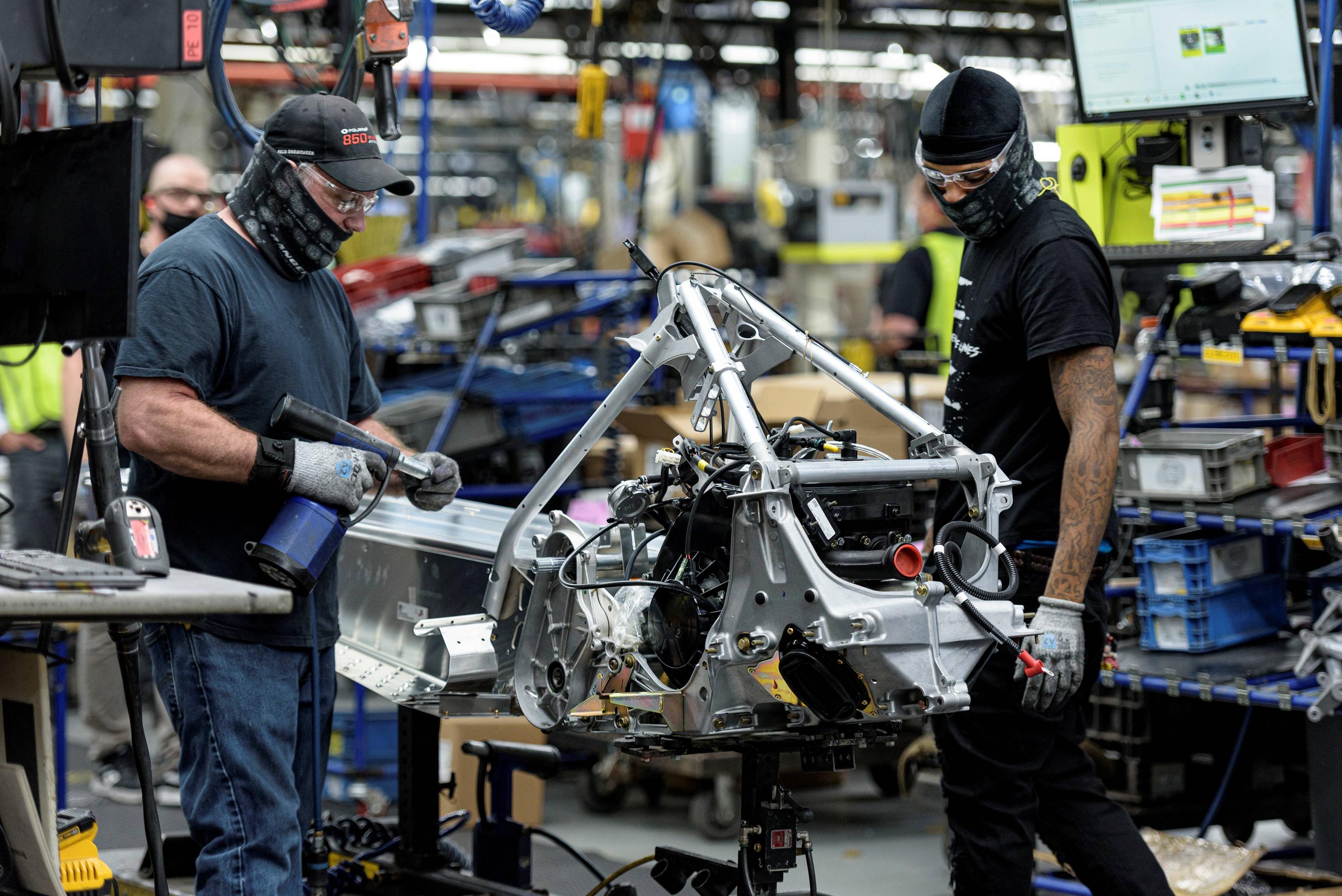
Structural engineers earn one of the highest salaries in comparison to other occupations. The salary of structural engineers is related to the demand for them. A bachelor's degree in structural engineering is the norm. They should also have at least one year of experience in this field. They could work in a building company, utility establishment, consulting firm or engineering firm. Some structural engineers may also start their own company.
Structural Engineers design structures that can withstand severe stresses. They also need to understand the properties of various materials. They may also be asked to participate in competitive bidding. They need to have project management and communication skills. They need to be proficient with computer software. Sometimes they may have to work extra hours to meet deadlines. They may also travel to assist clients in projects outside of their hometown.
Most structure engineers work full-time. They can work weekends and evenings. If they work for a business, they can take advantage of company cars and have extended health insurance benefits. They might also be eligible for an employee stock ownership plan. Changes in employers or advanced degrees can help a structural engineering professional increase their salary. The annual salary range for structural engineers is $59,000 to $108,000.
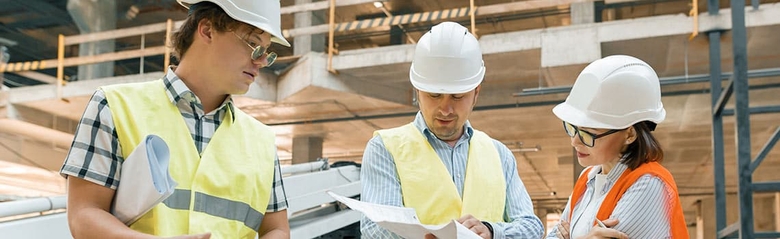
The salaries of structural engineers in the United States vary from one city to another. A structural engineer in San Francisco makes $147,822 per year. District of Columbia offers the second highest median salary of $146,683. Deer Park, CA has the third highest average salary at $111,562.
Norway's Oslo has a median salary of kr 765 026 for structures engineers. However, the average Norwegian salary for structural engineering is 8.8% higher in this city. The cost to live is also associated with the salary of structural engineering engineers.
The typical work hours of structural engineers are Monday through Friday, 9:00 am to 5:00pm. They can also work weekends, nights, and holidays. They may occasionally visit construction sites to check on the work. They will need the ability to communicate their designs with clients. They will also need to know how to use computer-aided modeling (CAD) software to visualize the final parts.
A structural engineer can also work as an assistant to an experienced engineer. He or she will have to complete supervised training before they can work independently. An apprenticeship program can be used to obtain certification as a structural engineer. They must have at least four years of experience in the field. Once they have acquired sufficient experience, they can begin applying directly to employers.
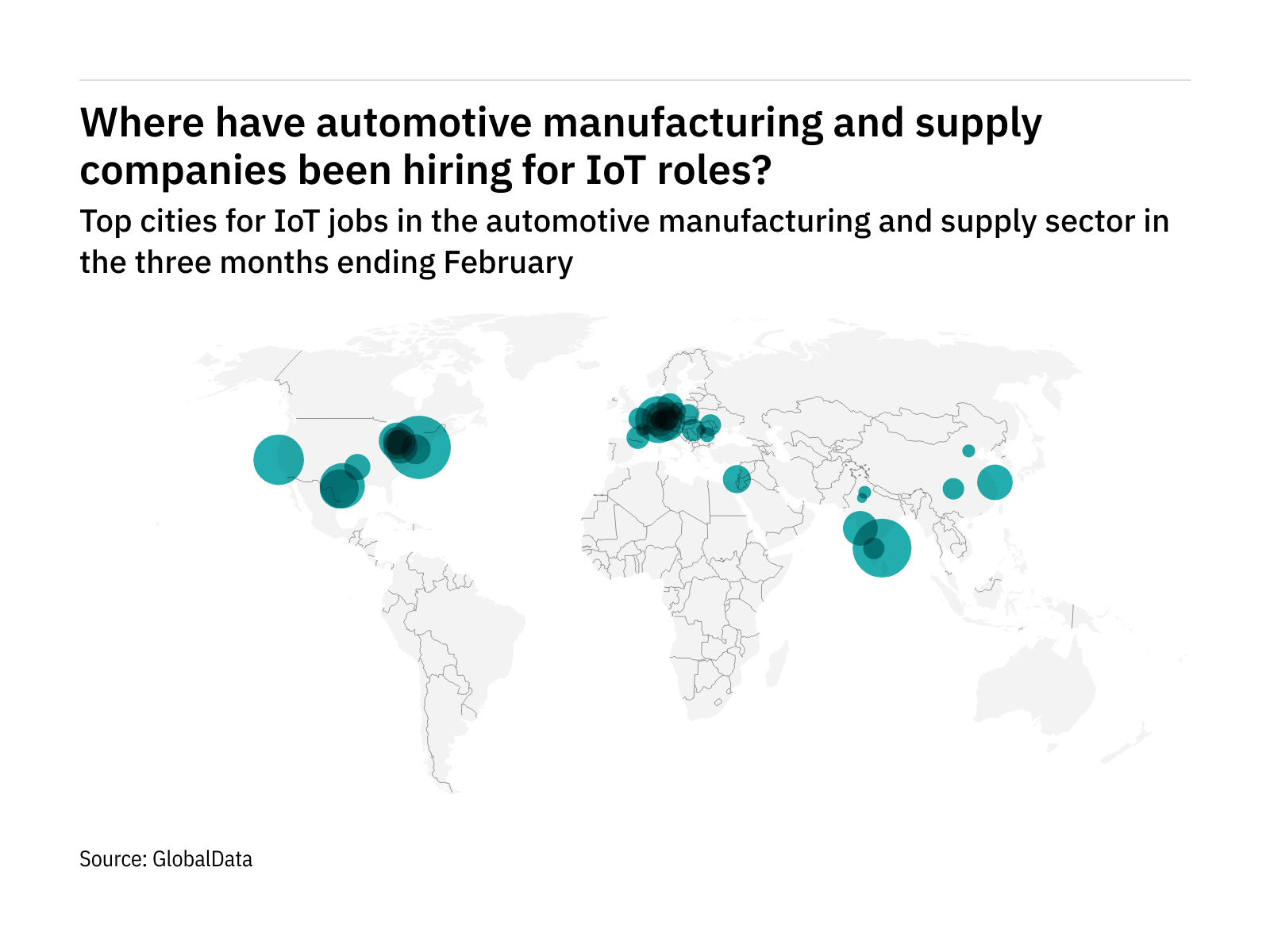
The average hourly salary for structural engineers is $42. If you are a structural engineer, your salary can increase if you work harder and gain experience. Senior structural engineers earn the best salaries. You can also join the Institution of StructE which recognizes excellence within the field.
A structural engineer is paid a total of $3,179 as a salary, plus a bonus and profit sharing. The average bonus paid is $3,179
FAQ
What is the distinction between Production Planning or Scheduling?
Production Planning (PP) refers to the process of determining how much production is needed at any given moment. Forecasting demand is one way to do this.
Scheduling is the process that assigns dates to tasks so they can get completed within a given timeframe.
How can manufacturing avoid production bottlenecks
To avoid production bottlenecks, ensure that all processes run smoothly from the moment you receive your order to the time the product ships.
This includes both quality control and capacity planning.
Continuous improvement techniques such Six Sigma are the best method to accomplish this.
Six Sigma is a management method that helps to improve quality and reduce waste.
It focuses on eliminating variation and creating consistency in your work.
What makes a production planner different from a project manger?
The primary difference between a producer planner and a manager of a project is that the manager usually plans and organizes the whole project, while a production planner is only involved in the planning stage.
What type of jobs is there in logistics
There are many types of jobs in logistics. Some examples are:
-
Warehouse workers – They load, unload and transport pallets and trucks.
-
Transport drivers - These are people who drive trucks and trailers to transport goods or perform pick-ups.
-
Freight handlers - They sort and pack freight in warehouses.
-
Inventory managers - These are responsible for overseeing the stock of goods in warehouses.
-
Sales reps - They sell products and services to customers.
-
Logistics coordinators - They organize and plan logistics operations.
-
Purchasing agents: They are responsible for purchasing goods and services to support company operations.
-
Customer service agents - They answer phone calls and respond to emails.
-
Shipping clerks – They process shipping orders, and issue bills.
-
Order fillers - They fill orders based on what is ordered and shipped.
-
Quality control inspectors: They inspect outgoing and incoming products for any defects.
-
Others - There are many other types of jobs available in logistics, such as transportation supervisors, cargo specialists, etc.
What do you mean by warehouse?
A warehouse, or storage facility, is where goods are stored prior to being sold. It can be either an indoor or outdoor space. Sometimes, it can be both an indoor and outdoor space.
Why is logistics so important in manufacturing?
Logistics are an essential part of any business. Logistics can help you achieve amazing results by helping to manage product flow from raw materials to finished products.
Logistics also play a major role in reducing costs and increasing efficiency.
Statistics
- (2:04) MTO is a production technique wherein products are customized according to customer specifications, and production only starts after an order is received. (oracle.com)
- According to a Statista study, U.S. businesses spent $1.63 trillion on logistics in 2019, moving goods from origin to end user through various supply chain network segments. (netsuite.com)
- You can multiply the result by 100 to get the total percent of monthly overhead. (investopedia.com)
- Many factories witnessed a 30% increase in output due to the shift to electric motors. (en.wikipedia.org)
- According to the United Nations Industrial Development Organization (UNIDO), China is the top manufacturer worldwide by 2019 output, producing 28.7% of the total global manufacturing output, followed by the United States, Japan, Germany, and India.[52][53] (en.wikipedia.org)
External Links
How To
Six Sigma: How to Use it in Manufacturing
Six Sigma is "the application statistical process control (SPC), techniques for continuous improvement." Motorola's Quality Improvement Department created Six Sigma at their Tokyo plant, Japan in 1986. Six Sigma is a method to improve quality through standardization and elimination of defects. This method has been adopted by many companies in recent years as they believe there are no perfect products or services. The main goal of Six Sigma is to reduce variation from the mean value of production. You can calculate the percentage of deviation from the norm by taking a sample of your product and comparing it to the average. If you notice a large deviation, then it is time to fix it.
Understanding how your business' variability is a key step towards Six Sigma implementation is the first. Once you understand that, it is time to identify the sources of variation. You'll also want to determine whether these variations are random or systematic. Random variations are caused when people make mistakes. While systematic variations are caused outside of the process, they can occur. For example, if you're making widgets, and some of them fall off the assembly line, those would be considered random variations. You might notice that your widgets always fall apart at the same place every time you put them together.
Once you identify the problem areas, it is time to create solutions. This could mean changing your approach or redesigning the entire process. Test them again once you've implemented the changes. If they didn't work, then you'll need to go back to the drawing board and come up with another plan.