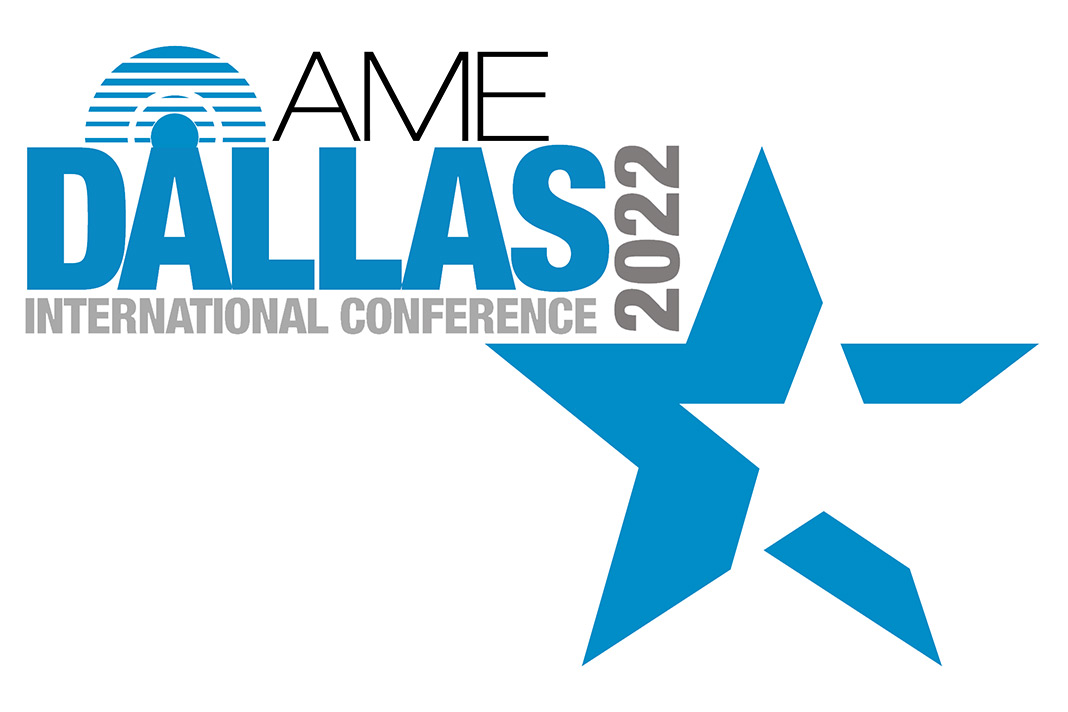
If you want to attract the best transport and logistics job candidates, make sure the job description contains all the duties. These duties can include filling company paperwork and ordering raw materials. Although it may make the job description sound more attractive, hiring the wrong person can lead to misplaced hires. This can cause problems for your business and customers. It can also mean that you need to spend time and money training new employees.
Job description
To move people and goods between points A and B, logistics professionals are employed in a variety of industries. Some work in the field of shipping, while others may be involved in road maintenance. This work includes monitoring traffic congestion and the safety of products. The job requires employees to adapt to changing business demands and work in various places.
A job description must be specific and focussed on the training and skills required to do the job. The job description should also reflect the culture and values of the company. It should indicate whether the job is permanent, interim, or self-employed.
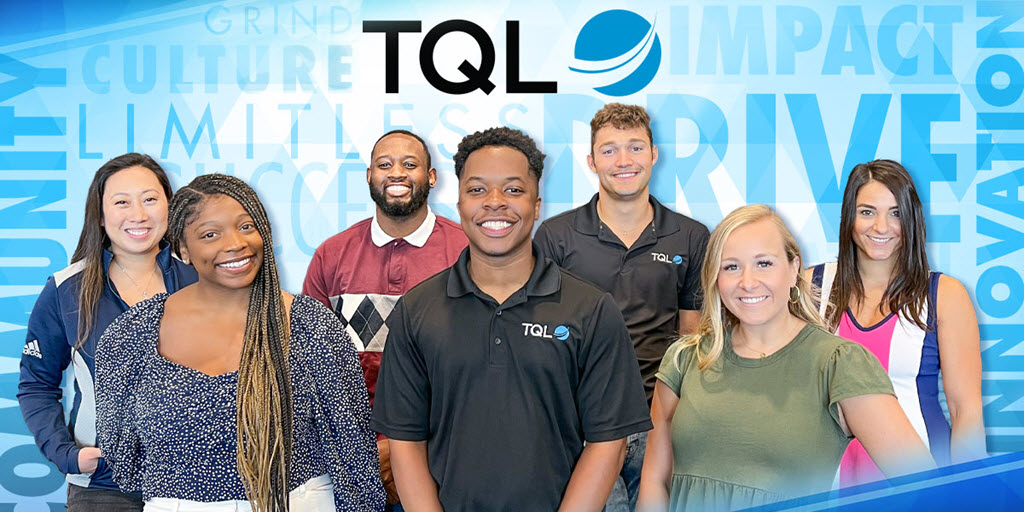
Salary
You can find a wide range of jobs in transportation and logistics, starting at entry level to more senior positions. Salary levels can vary depending on experience and industry. Entry-level positions typically start at around $40,000 per a year. These salaries are not guaranteed to be the highest, but there is always room for growth.
You have many options when it comes to salary for logistics or transportation jobs. Some are more lucrative than some. Although entry-level salary may be lower than for other professions, it is possible to earn much more if your experience level is high. Many companies offer training in-house or pay for graduate-level education.
Requirements
Transportation and logistics jobs are highly valued in many industries and require a high level of competence. These jobs focus on ensuring that goods are delivered safely, promptly, and at the best possible price. Companies must ensure that they hire the right people with the right skills. Although junior staff may not need training, they should have the qualifications to become a Supply Chain Practitioner Advanced Apprenticeship. Chartered Institute of Logistics and Transport accredited certifications are also required for those seeking senior positions.
A degree in transportation and logistics is an important step to take if you want to pursue a career in this field. There are many courses that will help you expand your knowledge and improve your skills. The Chartered Institute of Logistics and Transport UK has a Level 2 Certificate for Transport and Logistics. This course is great for those just starting out in this field. Graduate recruitment schemes are offered by many logistics companies and can give you valuable experience.
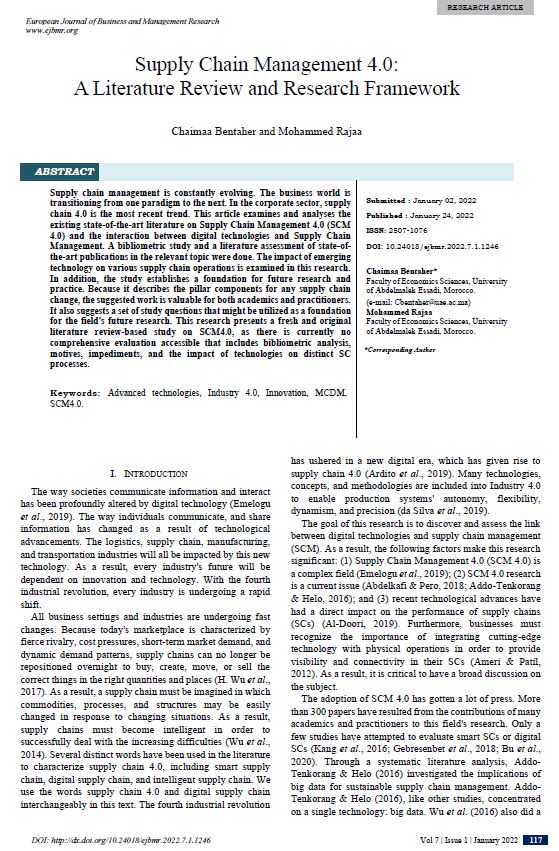
Locations
The career opportunities in logistics and transport are varied. These careers often require you to plan and assess different distribution methods. These jobs require an excellent level of analytical thinking and the ability manage complex data. You must also have excellent communication skills. Some jobs will require you to travel to remote locations. Graduate training schemes in transport and logistics are available, and they provide you with the skills needed to succeed in the field. Many of these programs will offer paid internships.
Transport and logistics occupations are in great demand. They are expected to increase by 3% from 2019-2029, the same as the national median. However, certain jobs are expected to see higher growth than the average, such as commercial and airline pilots. Driver/sales employees and drivers of delivery trucks are also available in this sector.
FAQ
What are the requirements to start a logistics business?
It takes a lot of skills and knowledge to run a successful logistics business. For clients and suppliers to be successful, you need to have excellent communication skills. It is important to be able to analyse data and draw conclusions. You must be able and able to handle stress situations and work under pressure. To increase efficiency and creativity, you need to be creative. Strong leadership qualities are essential to motivate your team and help them achieve their organizational goals.
To meet tight deadlines, you must also be efficient and organized.
What is the responsibility of a logistics manager?
Logistics managers are responsible for ensuring that all goods arrive in perfect condition and on time. This is done by using his/her experience and knowledge of the company's products. He/she should ensure that sufficient stock is available in order to meet customer demand.
What are the 4 types of manufacturing?
Manufacturing is the process of transforming raw materials into useful products using machines and processes. It can involve many activities like designing, manufacturing, testing packaging, shipping, selling and servicing.
What are the products of logistics?
Logistics refers to all activities that involve moving goods from A to B.
They include all aspects associated with transport including packaging, loading transporting, unloading storage, warehousing inventory management customer service, distribution returns and recycling.
Logisticians ensure that the right product reaches the right place at the right time and under safe conditions. Logisticians help companies improve their supply chain efficiency by providing information about demand forecasts and stock levels, production schedules, as well as availability of raw materials.
They keep track and monitor the transit of shipments, maintain quality standards, order replenishment and inventories, coordinate with suppliers, vendors, and provide support for sales and marketing.
Statistics
- According to a Statista study, U.S. businesses spent $1.63 trillion on logistics in 2019, moving goods from origin to end user through various supply chain network segments. (netsuite.com)
- [54][55] These are the top 50 countries by the total value of manufacturing output in US dollars for its noted year according to World Bank.[56] (en.wikipedia.org)
- In 2021, an estimated 12.1 million Americans work in the manufacturing sector.6 (investopedia.com)
- Job #1 is delivering the ordered product according to specifications: color, size, brand, and quantity. (netsuite.com)
- Many factories witnessed a 30% increase in output due to the shift to electric motors. (en.wikipedia.org)
External Links
How To
Six Sigma and Manufacturing
Six Sigma is defined by "the application SPC (statistical process control) techniques to achieve continuous improvements." Motorola's Quality Improvement Department developed it at their Tokyo plant in Japan in 1986. Six Sigma is a method to improve quality through standardization and elimination of defects. Many companies have adopted this method in recent years. They believe there is no such thing a perfect product or service. Six Sigma's primary goal is to reduce variation from the average value of production. You can calculate the percentage of deviation from the norm by taking a sample of your product and comparing it to the average. If this deviation is too big, you know something needs fixing.
Understanding how variability works in your company is the first step to Six Sigma. Once you understand that, it is time to identify the sources of variation. You'll also want to determine whether these variations are random or systematic. Random variations are caused by human errors. Systematic variations can be caused by outside factors. Random variations would include, for example, the failure of some widgets to fall from the assembly line. However, if you notice that every time you assemble a widget, it always falls apart at exactly the same place, then that would be a systematic problem.
Once you have identified the problem, you can design solutions. The solution could involve changing how you do things, or redesigning your entire process. After implementing the new changes, you should test them again to see if they worked. If they don't work you need to rework them and come up a better plan.