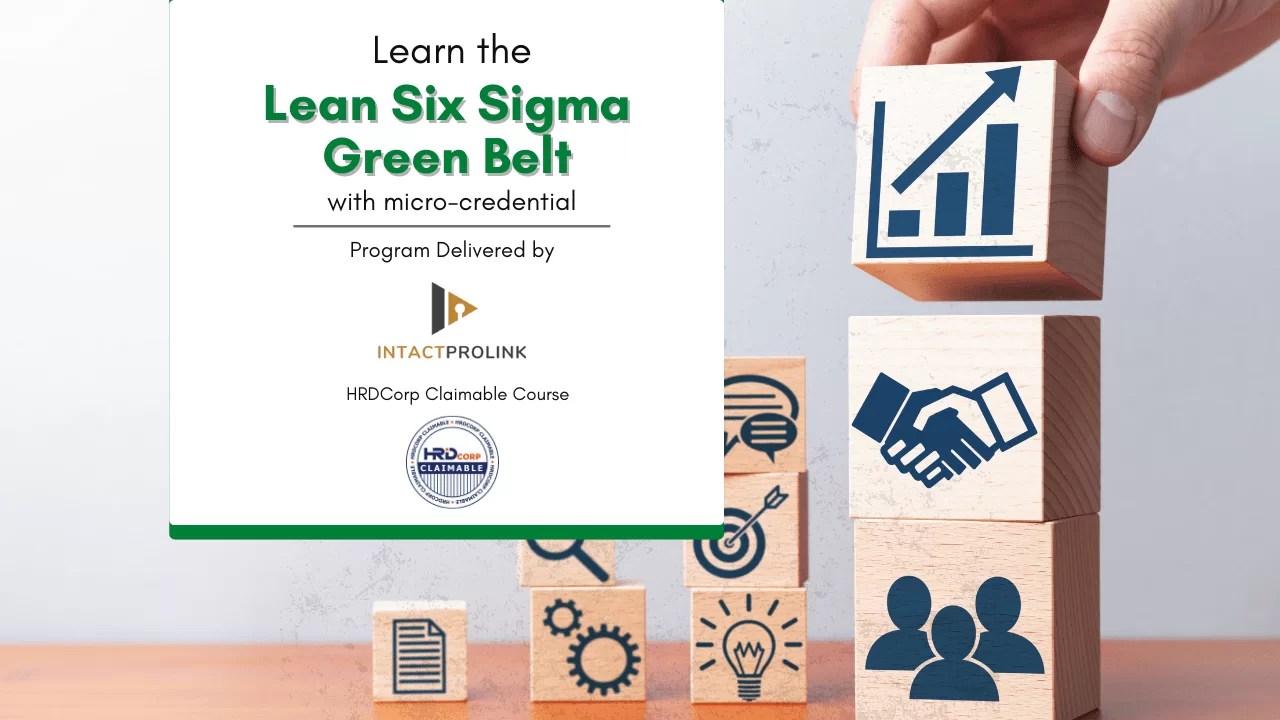
The Defense Industrial Base (DIB), a network of over 200,000 companies that provide goods and services for the Department of Defense, is more than 200,000. It includes small businesses as well as large corporations and startups. The Government Accountability Office has released a new report that highlights the risks and challenges facing the DIB, as well its efforts to address these.
The defense industrial base has seen a decline of nearly 40 percent over the past 10 years. As a result, the Department of Defense has struggled to attract new entrants into the sector. The Defense Department has made a number of attempts to encourage businesses to join the sector. Despite these efforts, many small firms are being left behind. This has created a growing national security risk.
Multiple DOD offices currently work to mitigate the risks associated with the DIB. However, there is no comprehensive strategy in place to assess and manage these risk. GAO reviewed several reports and interviewed DOD personnel to determine areas that could be improved. GAO identified five components that could help the department meet its goals.
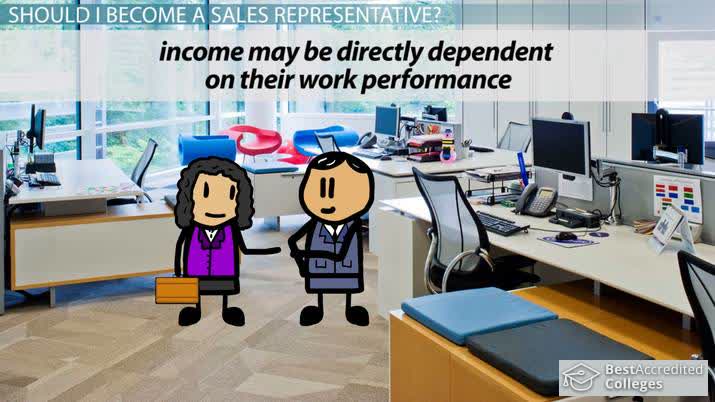
The loss of commercial suppliers is a major concern. Many of these businesses provide parts for weapon systems used by the Pentagon. The industry has seen a decrease in small businesses over the past 10 years. However, it is difficult to measure how many new firms are entering the market.
Other problems include material shortages as well as reliance on foreign vendors. In addition, intellectual property restrictions can slow down the military’s acquisition process. Additionally, there is no standard for what constitutes "new enter" into the defense industrial basis.
GAO recommended that Defense review its policy regarding mitigating risk in the DIB. The GAO recommended that the Department of Defense continue to engage traditional defense contractors as well as implement tools to make it easier for private technology providers to access the DoD market. These recommendations should be part of an overall strategy for addressing industrial base concerns.
As part this strategy, the Defense Department needs to think about how it can use its OTAs as well as CSOs to accelerate acquisition strategy creation. By using the right people, processes, and technologies, the supply chain can be restructured to deliver dynamic outcomes.
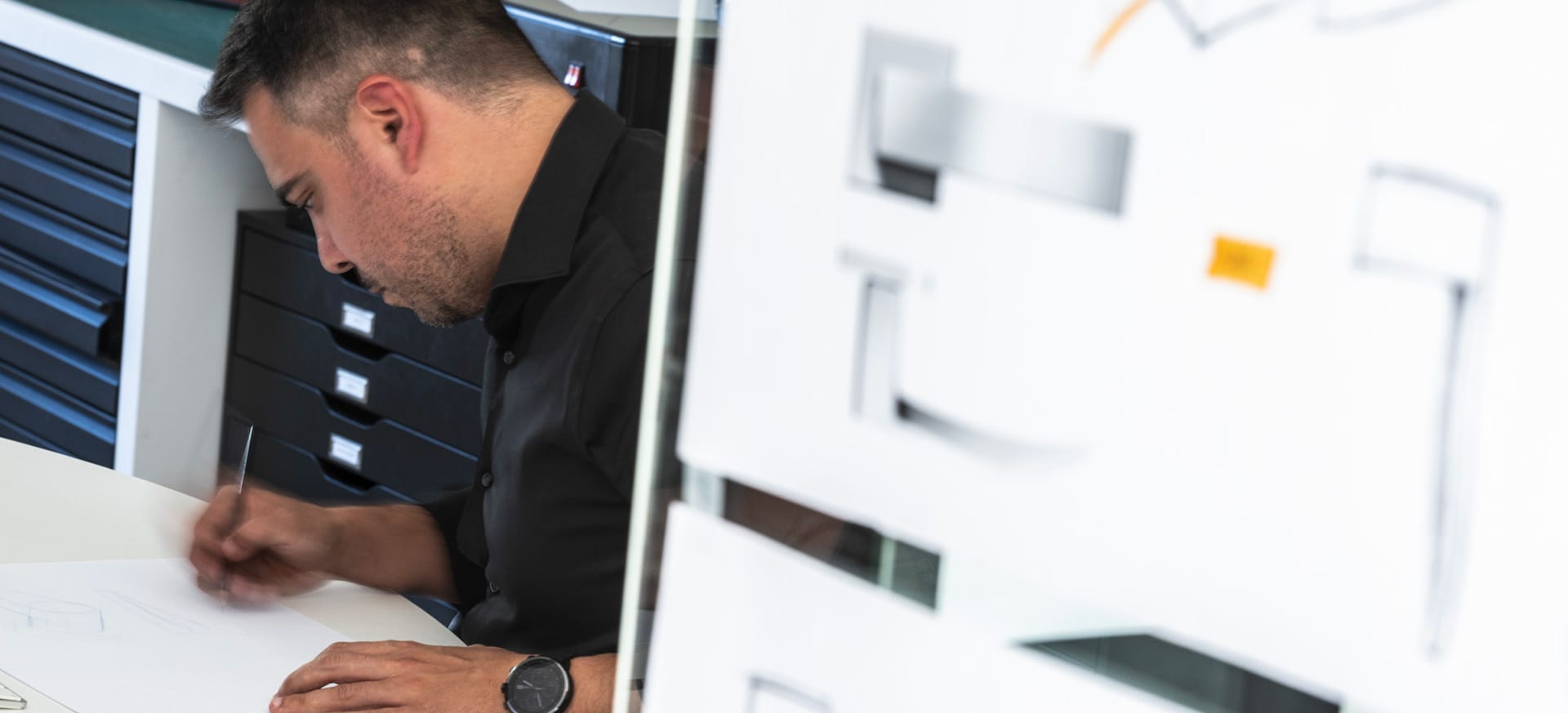
Despite the fact that the number has dropped over the past decade in defense industry, it is still developing. Many companies do not feel comfortable with the Federal Acquisition Regulation (FAR). A current landscape might make it more difficult for small businesses compete.
Small businesses and startups are crucial for innovation in the defense industrial base. Resilient DIB members can help support National Security and allow the Department of Defense develop better military equipment.
The defense industrial base is complex and requires a comprehensive strategy in order to ensure that the resources are available for the military's needs. In the meantime, it is essential that the Department of Defense learn more about best practices for integrating technology into its business processes, which will allow for more efficient and innovative products and services.
FAQ
Why is logistics important in manufacturing
Logistics is an integral part of every business. They can help you achieve great success by helping you manage product flow from raw material to finished goods.
Logistics are also important in reducing costs and improving efficiency.
What kind of jobs are there in logistics?
Logistics can offer many different jobs. Here are some:
-
Warehouse workers – They load and unload pallets and trucks.
-
Transport drivers - These are people who drive trucks and trailers to transport goods or perform pick-ups.
-
Freight handlers are people who sort and pack freight into warehouses.
-
Inventory managers: They are responsible for the inventory and management of warehouses.
-
Sales reps - They sell products and services to customers.
-
Logistics coordinators: They plan and manage logistics operations.
-
Purchasing agents – They buy goods or services necessary to run a company.
-
Customer service agents - They answer phone calls and respond to emails.
-
Shippers clerks - They process shipping order and issue bills.
-
Order fillers - These people fill orders based on what has been ordered.
-
Quality control inspectors: They inspect outgoing and incoming products for any defects.
-
Others - There are many types of jobs in logistics such as transport supervisors and cargo specialists.
What are the responsibilities of a manufacturing manager
A manufacturing manager must make sure that all manufacturing processes run smoothly and effectively. They must also be alert to any potential problems and take appropriate action.
They should also learn how to communicate effectively with other departments, including sales and marketing.
They must also keep up-to-date with the latest trends in their field and be able use this information to improve productivity and efficiency.
How can we improve manufacturing efficiency?
The first step is to determine the key factors that impact production time. We must then find ways that we can improve these factors. You can start by identifying the most important factors that impact production time. Once you identify them, look for solutions.
Why should you automate your warehouse?
Modern warehousing is becoming more automated. Increased demand for efficient and faster delivery has resulted in a rise in e-commerce.
Warehouses need to adapt quickly to meet changing needs. In order to do this, they need to invest in technology. Automation warehouses can bring many benefits. These are some of the benefits that automation can bring to warehouses:
-
Increases throughput/productivity
-
Reduces errors
-
Increases accuracy
-
Safety increases
-
Eliminates bottlenecks
-
Companies can scale up more easily
-
It makes workers more efficient
-
Provides visibility into everything that happens in the warehouse
-
Enhances customer experience
-
Improves employee satisfaction
-
This reduces downtime while increasing uptime
-
Quality products delivered on time
-
Human error can be eliminated
-
This helps to ensure compliance with regulations
Statistics
- Many factories witnessed a 30% increase in output due to the shift to electric motors. (en.wikipedia.org)
- Job #1 is delivering the ordered product according to specifications: color, size, brand, and quantity. (netsuite.com)
- [54][55] These are the top 50 countries by the total value of manufacturing output in US dollars for its noted year according to World Bank.[56] (en.wikipedia.org)
- According to the United Nations Industrial Development Organization (UNIDO), China is the top manufacturer worldwide by 2019 output, producing 28.7% of the total global manufacturing output, followed by the United States, Japan, Germany, and India.[52][53] (en.wikipedia.org)
- According to a Statista study, U.S. businesses spent $1.63 trillion on logistics in 2019, moving goods from origin to end user through various supply chain network segments. (netsuite.com)
External Links
How To
Six Sigma in Manufacturing
Six Sigma is defined as "the application of statistical process control (SPC) techniques to achieve continuous improvement." Motorola's Quality Improvement Department in Tokyo, Japan developed Six Sigma in 1986. Six Sigma's core idea is to improve the quality of processes by standardizing and eliminating defects. This method has been adopted by many companies in recent years as they believe there are no perfect products or services. Six Sigma's main objective is to reduce variations from the production average. If you take a sample and compare it with the average, you will be able to determine how much of the production process is different from the norm. If you notice a large deviation, then it is time to fix it.
Understanding how your business' variability is a key step towards Six Sigma implementation is the first. Once you have a good understanding of the basics, you can identify potential sources of variation. It is important to identify whether the variations are random or systemic. Random variations are caused by human errors. Systematic variations can be caused by outside factors. You could consider random variations if some widgets fall off the assembly lines. However, if you notice that every time you assemble a widget, it always falls apart at exactly the same place, then that would be a systematic problem.
Once you identify the problem areas, it is time to create solutions. This could mean changing your approach or redesigning the entire process. Test them again once you've implemented the changes. If they don't work, you will need to go back to the drawing boards and create a new plan.