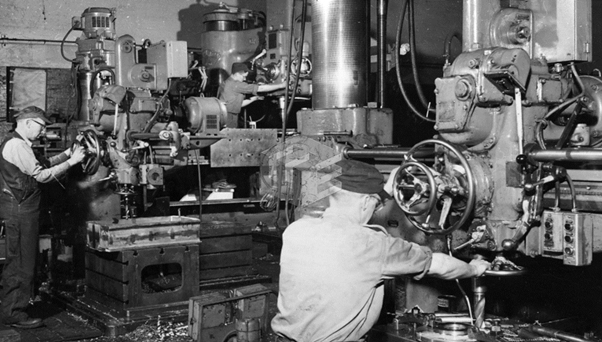
In the United States, chemical manufacturing is a major industry that transforms organic and inorganic raw materials into useful products. It supplies consumer goods and materials for industries ranging from plastics to explosives. Chemical industry also faces many problems. Numerous workers are at high risk for health and safety.
Chemical manufacturing is broken down into two main segments: specialty chemicals (common chemicals) and commodity chemicals (spezial chemicals). These two segments share the same infrastructure and processes. Different types of products exist. Specialty chemical are often designed to be used by customers. Specialty chemical manufacturers are responsible for producing some of the most expensive chemicals. Patents protect many of these chemicals.
While some chemicals can be made at one place, the majority of petrochemicals or commodity chemicals are produced at large-scale facilities. Rotterdam in the Netherlands, Texas and Louisiana are all examples of large-scale chemical plant. Large scale chemical plants often share utilities and other infrastructures, creating economies of scale.
The United States is the second-largest chemical manufacturer in the world behind China. Statista estimates that the annual value of the chemical industry exceeds $4 trillion. About half the industry's revenues are generated by the top 50 US businesses.
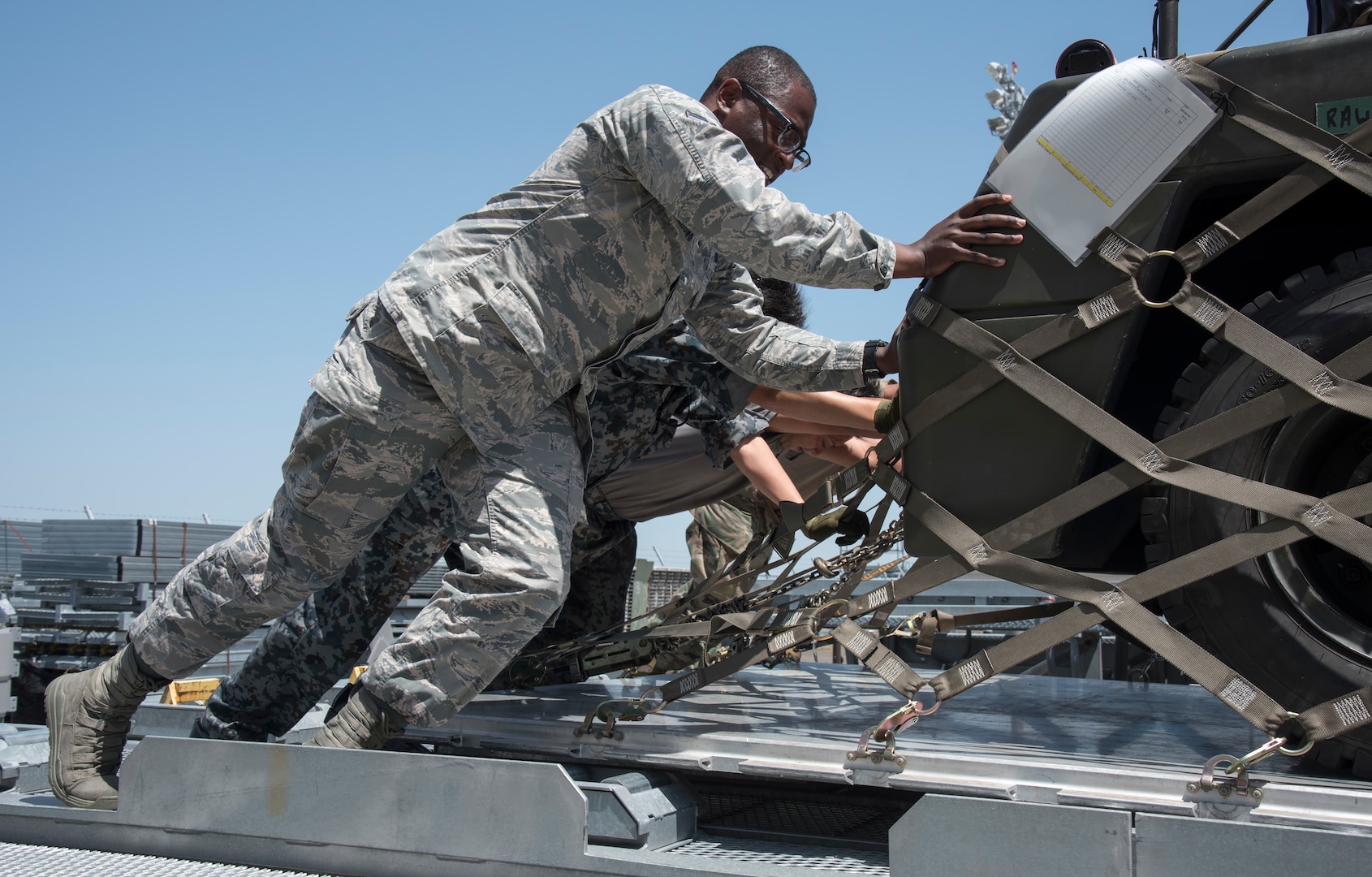
Worldwide, the chemical manufacturing industry employs around 20 million workers. While most of these workers are in large-scale facilities, a small number are part-time or contract employees. The industry's employment situation has been negatively affected by increased competition and technological advances.
The U.S. overall economy is the main driver of chemical demand. The chemical industry is highly regulated. Governing bodies set regulations and standards for the manufacturing process. Companies need to implement sustainable manufacturing practices. Some chemicals manufacturing raw materials are extremely dangerous to extract.
The industry faces difficult procurement challenges. Additionally, raw material costs are very high. To keep costs down, some companies are shifting their operations to locations that have lower overhead. Finally, some companies merge or shift production to developing nations. This will result is the elimination of jobs.
Eighty percent of all jobs were provided by the basic chemical production segment in 2008. This group includes producers of pesticides, dyes and other materials. Pfizer and Dow are among the top manufacturing companies in this sector. Other major players include DuPont, Formosa Plastics, and Sinopec Group.
Large-scale production lines are generally clean. Workers are required to wear safety goggles and work in a temperature-controlled environment. Some workers, however, are replaced with advanced machines and computerized controls. Many of these workers work nights.
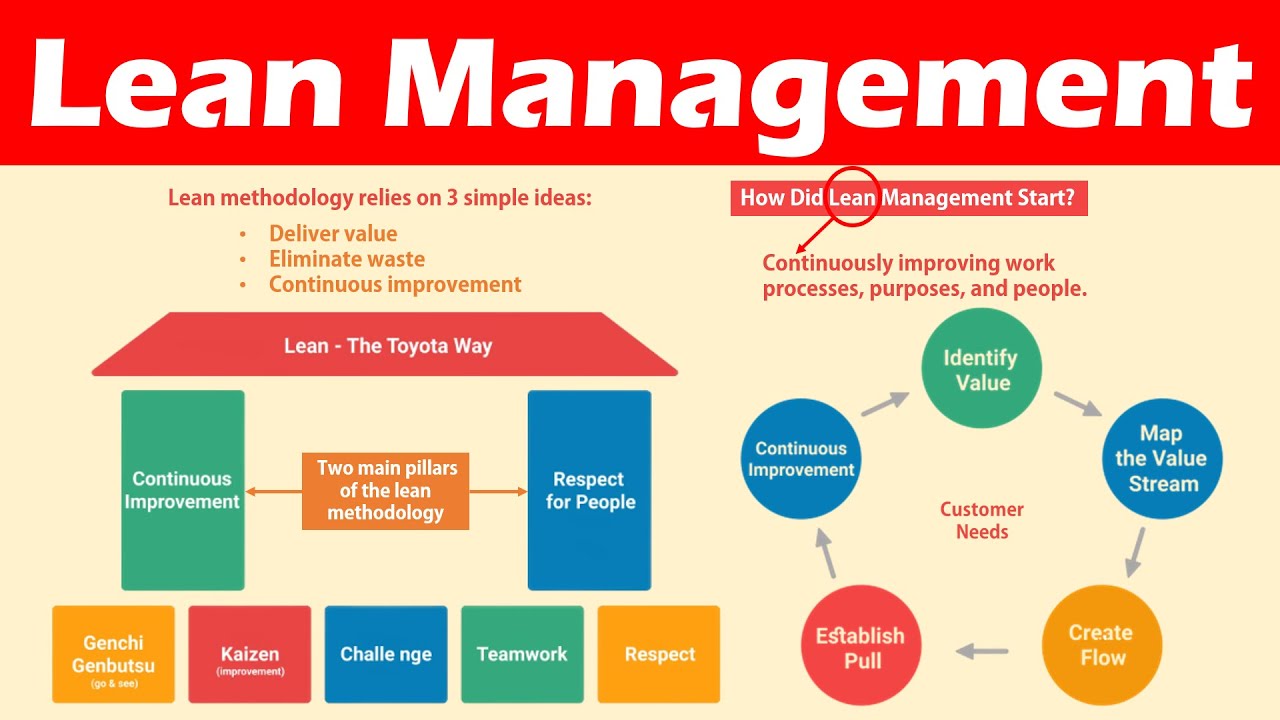
Chemical manufacturing plants may need to be modified to accommodate new production methods. New processes could improve accuracy and reduce labor cost. Nanotechnology will also make chemical manufacturing more efficient. Companies can save energy and reduce waste with nanotechnology.
Other factors that affect the employment in the chemical manufacturing sector include increased foreign competition, technological advances, and concerns about safety and environmental health. In general, the industry's employment will decrease by 13 percent over four years.
FAQ
What are the 4 types of manufacturing?
Manufacturing is the process that transforms raw materials into useful products. It involves many different activities such as designing, building, testing, packaging, shipping, selling, servicing, etc.
What are the 7 Rs of logistics?
The acronym 7R's for Logistics stands to represent the seven basic principles in logistics management. It was developed by International Association of Business Logisticians (IABL), and published as part of their "Seven Principles of Logistics Management Series" in 2004.
The acronym is made up of the following letters:
-
Responsive - ensure all actions are legal and not harmful to others.
-
Reliable - You can have confidence that you will fulfill your promises.
-
Be responsible - Use resources efficiently and avoid wasting them.
-
Realistic - Take into consideration all aspects of operations including cost-effectiveness, environmental impact, and other factors.
-
Respectful - show respect and treat others fairly and fairly
-
Resourceful - look for opportunities to save money and increase productivity.
-
Recognizable - provide customers with value-added services.
What does warehouse mean?
A warehouse is an area where goods are stored before being sold. You can have it indoors or outdoors. In some cases, it may be a combination of both.
How can manufacturing reduce production bottlenecks?
Avoiding production bottlenecks is as simple as keeping all processes running smoothly, from the time an order is received until the product ships.
This includes planning for both capacity requirements and quality control measures.
Continuous improvement techniques like Six Sigma are the best way to achieve this.
Six Sigma management is a system that improves quality and reduces waste within your organization.
It is focused on creating consistency and eliminating variation in your work.
Statistics
- According to a Statista study, U.S. businesses spent $1.63 trillion on logistics in 2019, moving goods from origin to end user through various supply chain network segments. (netsuite.com)
- It's estimated that 10.8% of the U.S. GDP in 2020 was contributed to manufacturing. (investopedia.com)
- [54][55] These are the top 50 countries by the total value of manufacturing output in US dollars for its noted year according to World Bank.[56] (en.wikipedia.org)
- Many factories witnessed a 30% increase in output due to the shift to electric motors. (en.wikipedia.org)
- According to the United Nations Industrial Development Organization (UNIDO), China is the top manufacturer worldwide by 2019 output, producing 28.7% of the total global manufacturing output, followed by the United States, Japan, Germany, and India.[52][53] (en.wikipedia.org)
External Links
How To
How to Use Six Sigma in Manufacturing
Six Sigma is "the application statistical process control (SPC), techniques for continuous improvement." Motorola's Quality Improvement Department in Tokyo, Japan developed Six Sigma in 1986. Six Sigma is a method to improve quality through standardization and elimination of defects. In recent years, many companies have adopted this method because they believe there is no such thing as perfect products or services. Six Sigma's main objective is to reduce variations from the production average. You can calculate the percentage of deviation from the norm by taking a sample of your product and comparing it to the average. If it is too large, it means that there are problems.
Understanding how your business' variability is a key step towards Six Sigma implementation is the first. Once you have this understanding, you will need to identify sources and causes of variation. It is important to identify whether the variations are random or systemic. Random variations are caused by human errors. Systematic variations can be caused by outside factors. You could consider random variations if some widgets fall off the assembly lines. But if you notice that every widget you make falls apart at the exact same place each time, this would indicate that there is a problem.
Once you've identified the problem areas you need to find solutions. This could mean changing your approach or redesigning the entire process. To verify that the changes have worked, you need to test them again. If they don't work, you will need to go back to the drawing boards and create a new plan.