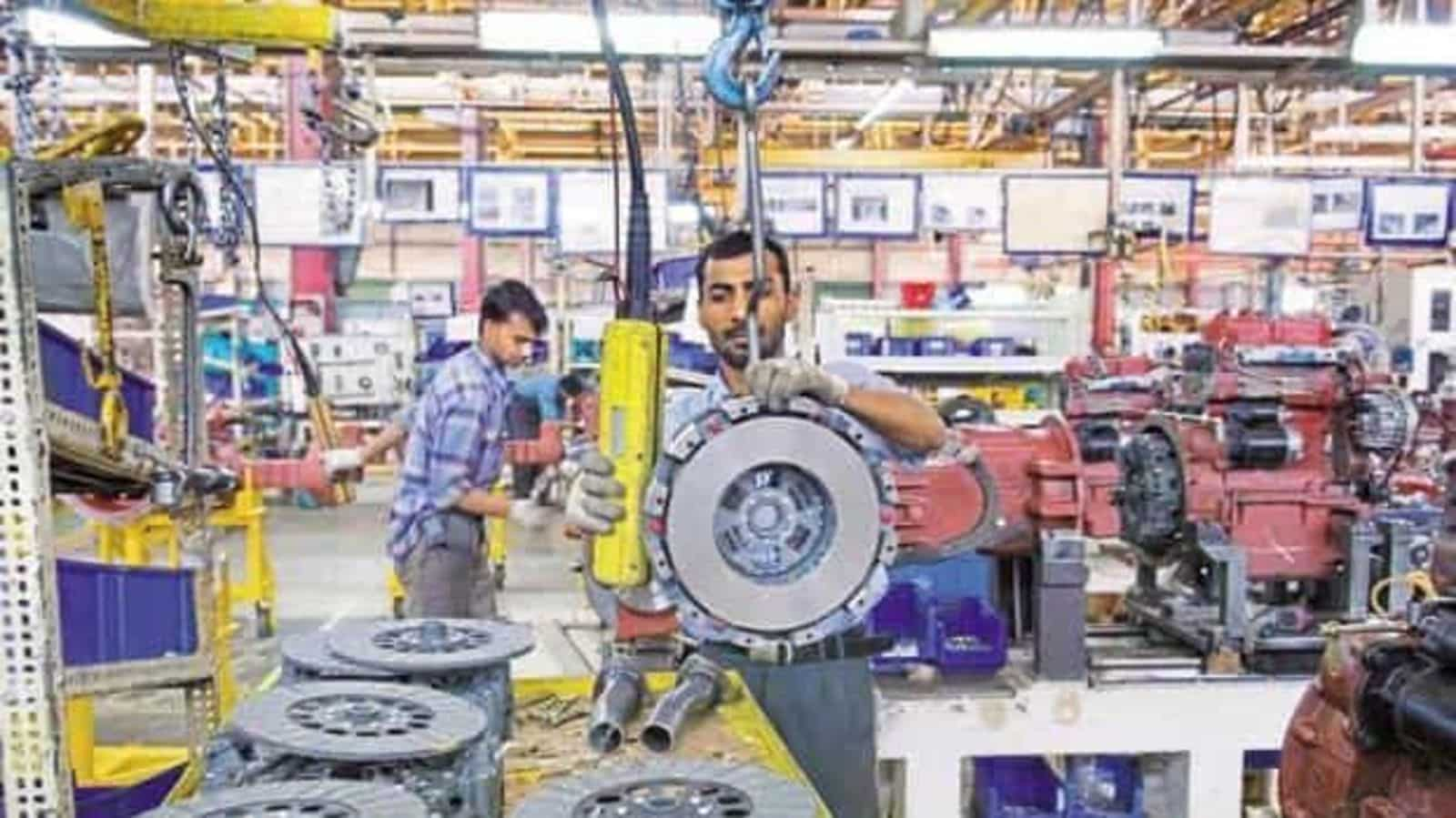
Lean manufacturing can be a cost-saving and time-saving tool. It also reduces setup and turnaround times. Lean manufacturing offers many benefits. It reduces costs and leads time, while improving customer satisfaction. These improvements make lean manufacturing the best way to boost your business. If you're still not convinced, read on for three reasons why it's the best way to make products and cut costs:
Reduces costs
Lean manufacturing can result in significant cost savings. Through reducing defects, rework and direct labor costs, manufacturers can make savings. In this way, labor costs are less motivating for decision-making. Eliminating hazardous waste is another advantage. Many industries have a lower cost of direct labor than 15%. This makes it difficult to justify outsourcing manufacturing to low-cost countries. This can reduce overall manufacturing costs and improve customer service.
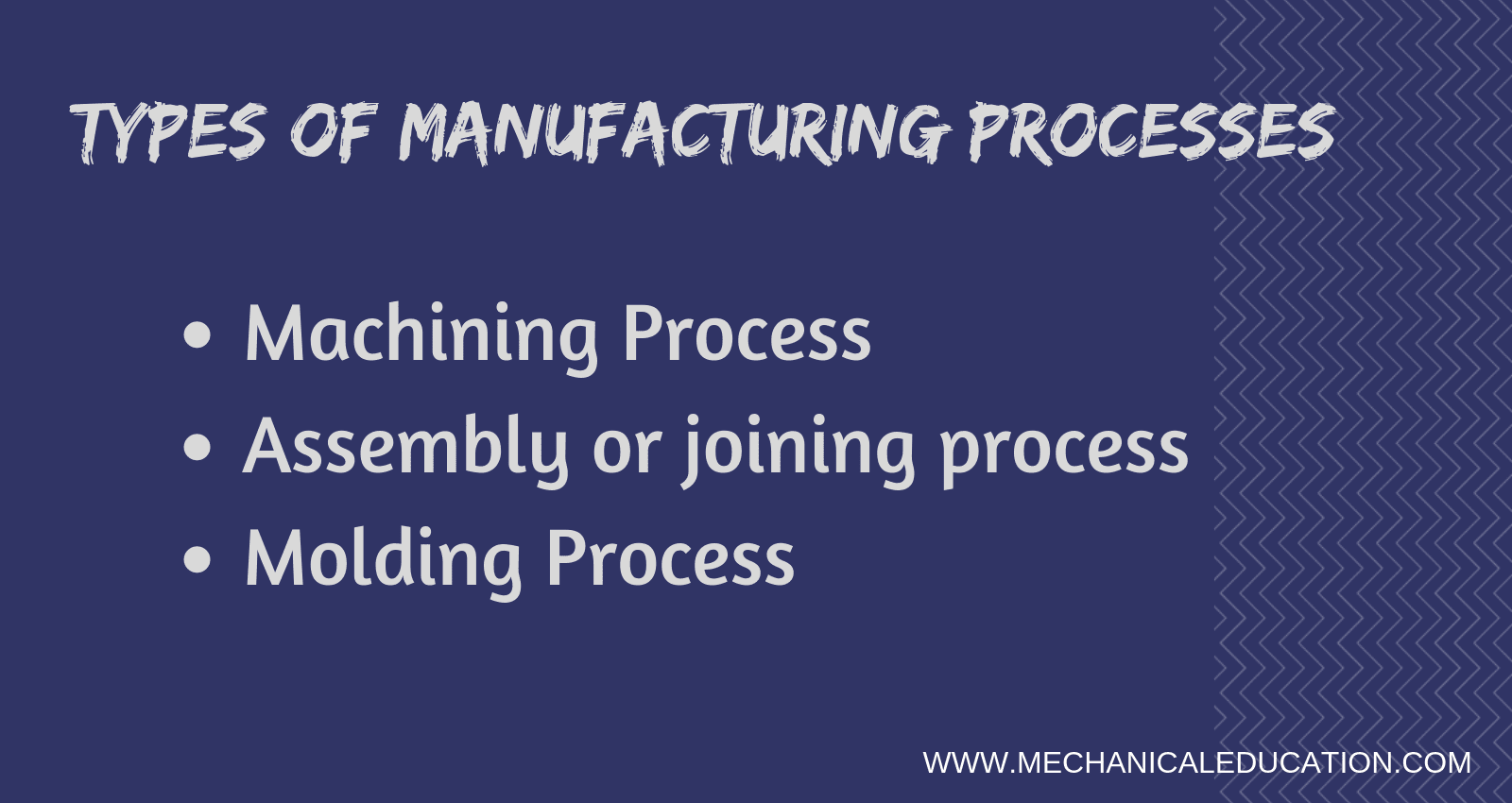
This improves lead times
There are many benefits to using lean manufacturing. These include the ability to reduce waste, improve lead times and lower costs. It is a philosophy of continuous improvement, also known as kaizen. It aggregates the talents of employees and promotes employee accountability and collaboration. The process can improve lead times by as much as 20%. The key aspect of lean manufacturing, however, is the ability to make small improvements often in order to improve the product's quality and efficiency.
Shortens set-up times
Reducing set-up times is one way to decrease the time needed to produce a product. Setup time is the time taken to move from the last product on an order to the next good item. Setting up time covers preparation, replacement, location, and other activities. These activities may be external or internal. Although internal activities are inactive, such as moving a machine or putting an item in its place, external setup activities can still be completed while the process remains operational.
Reduces time it takes to get to market
The concept of Lean manufacturing, or the process of continuous improvement, was developed in Japan during the rebuilding period after World War II. It was intended to improve market competitiveness and shorten lead times. Companies can be more responsive to customers and increase profits by reducing the time it takes a product reach the market. This method of production not only increases efficiency but also makes the facility more productive.
Improves product quality
Lean manufacturing's success depends on the ability to reduce waste, improve product quality, and minimize costs. It has been used by large manufacturers and smaller companies alike. It decreases lead times, costs, and labor. You can learn more about the benefits of lean manufacturing for your business by reading this article. Here are a few of the key areas to focus on. Lean principles can help reduce lead time by 90%, improve product quality and lower your costs.
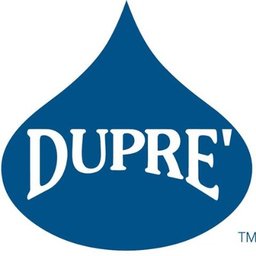
Lower indirect labor costs
In lean manufacturing, the low hanging fruit is reducing indirect labor costs. Lean companies don't pay much attention to direct labor efficiency, but instead focus on ways to reduce indirect labor costs. This means eliminating material handling and inspection jobs. Toyota and other lean manufacturing companies use the same approach. In this article we will take a closer look into how lean manufacturing can lower indirect labor cost.
FAQ
What does it mean to warehouse?
Warehouses and storage facilities are where goods are kept before being sold. You can have it indoors or outdoors. In some cases, it may be a combination of both.
How important is automation in manufacturing?
Automation is essential for both manufacturers and service providers. Automation allows them to deliver services quicker and more efficiently. It reduces human errors and improves productivity, which in turn helps them lower their costs.
What are the 7 Rs of logistics.
The acronym 7Rs of Logistics refers to the seven core principles of logistics management. It was developed and published by the International Association of Business Logisticians in 2004 as part of the "Seven Principles of Logistics Management".
The following letters form the acronym:
-
Responsible - to ensure that all actions are within the legal requirements and are not detrimental to others.
-
Reliable: Have faith in your ability or the ability to honor any promises made.
-
It is reasonable to use resources efficiently and not waste them.
-
Realistic – consider all aspects of operations, from cost-effectiveness to environmental impact.
-
Respectful - Treat people fairly and equitably
-
Be resourceful: Look for opportunities to save money or increase productivity.
-
Recognizable: Provide customers with value-added service
What are the responsibilities of a manufacturing manager
A manufacturing manager must ensure that all manufacturing processes are efficient and effective. They should also be aware of any problems within the company and act accordingly.
They should also learn how to communicate effectively with other departments, including sales and marketing.
They must also keep up-to-date with the latest trends in their field and be able use this information to improve productivity and efficiency.
What is the job of a logistics manger?
Logistics managers make sure all goods are delivered on schedule and without damage. This is accomplished by using the experience and knowledge gained from working with company products. He/she should also ensure enough stock is available to meet demand.
What does it mean to be a manufacturer?
Manufacturing Industries are those businesses that make products for sale. These products are sold to consumers. This is accomplished by using a variety of processes, including production, distribution and retailing. They make goods from raw materials with machines and other equipment. This includes all types and varieties of manufactured goods, such as food items, clothings, building supplies, furnitures, toys, electronics tools, machinery vehicles, pharmaceuticals medical devices, chemicals, among others.
Statistics
- According to a Statista study, U.S. businesses spent $1.63 trillion on logistics in 2019, moving goods from origin to end user through various supply chain network segments. (netsuite.com)
- (2:04) MTO is a production technique wherein products are customized according to customer specifications, and production only starts after an order is received. (oracle.com)
- Job #1 is delivering the ordered product according to specifications: color, size, brand, and quantity. (netsuite.com)
- You can multiply the result by 100 to get the total percent of monthly overhead. (investopedia.com)
- According to the United Nations Industrial Development Organization (UNIDO), China is the top manufacturer worldwide by 2019 output, producing 28.7% of the total global manufacturing output, followed by the United States, Japan, Germany, and India.[52][53] (en.wikipedia.org)
External Links
How To
Six Sigma: How to Use it in Manufacturing
Six Sigma can be described as "the use of statistical process control (SPC), techniques to achieve continuous improvement." Motorola's Quality Improvement Department developed it at their Tokyo plant in Japan in 1986. Six Sigma's core idea is to improve the quality of processes by standardizing and eliminating defects. This method has been adopted by many companies in recent years as they believe there are no perfect products or services. Six Sigma aims to reduce variation in the production's mean value. If you take a sample and compare it with the average, you will be able to determine how much of the production process is different from the norm. If you notice a large deviation, then it is time to fix it.
Understanding how your business' variability is a key step towards Six Sigma implementation is the first. Once you have this understanding, you will need to identify sources and causes of variation. It is important to identify whether the variations are random or systemic. Random variations happen when people make errors; systematic variations are caused externally. If you make widgets and some of them end up on the assembly line, then those are considered random variations. But if you notice that every widget you make falls apart at the exact same place each time, this would indicate that there is a problem.
Once you've identified the problem areas you need to find solutions. That solution might involve changing the way you do things or redesigning the process altogether. After implementing the new changes, you should test them again to see if they worked. If they didn't work, then you'll need to go back to the drawing board and come up with another plan.