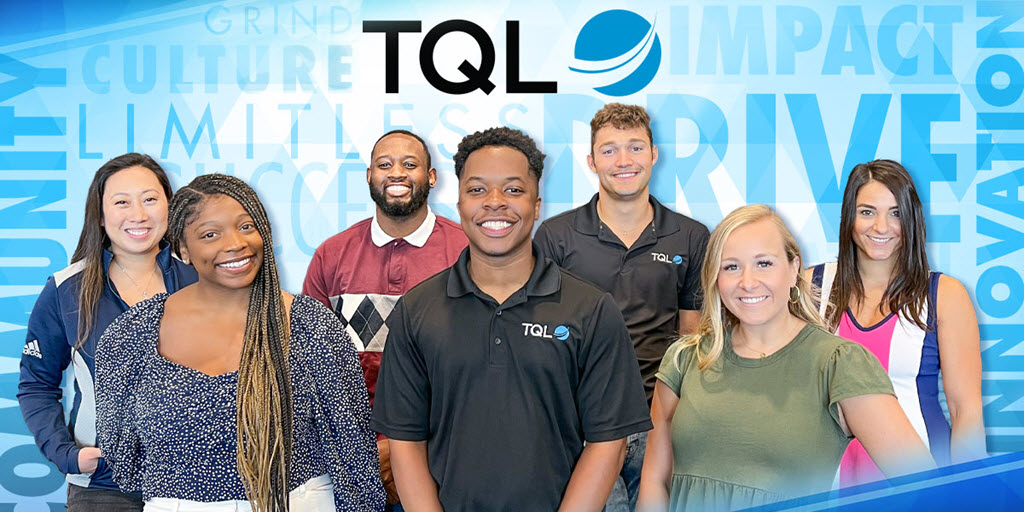
Whether you are running a large corporation or a small business, supply chain management software can help you streamline your processes and improve your efficiency. These systems allow you to view your entire supply chain from one place, making it easier to plan production, shipment plans, and deliver routes. These systems allow you to automate and streamline your processes, allowing your employees to concentrate on other aspects of the business. Every organization that manages shipping and manufacturing is going to need supply chain management software.
To choose the best supply-chain management software, consider several features and capabilities. These include scalability. ease of use. And integration with other programs. You should also consider the provider's reputation and the features they offer. You should also consider your budget when choosing a solution. No matter if you're looking for a SaaS service or a full-service package, be flexible to meet your evolving needs.
E2open, one of the most trusted supply chain management software companies, specializes in cloud-based solution that improves demand forecasting and operations management. The company offers advanced features as well as a technology platform. Software is available for businesses in many industries including manufacturing, retail, and transportation.
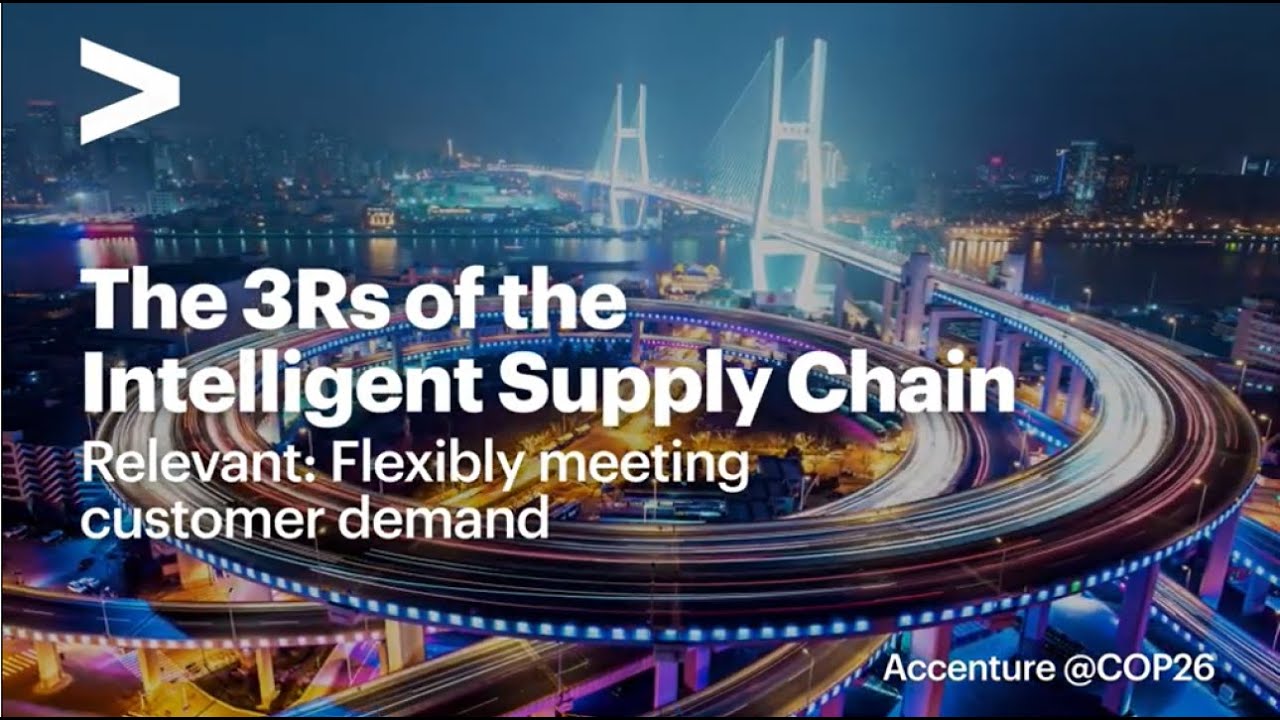
A key feature of supply chain management software is real-time visibility. This allows you to monitor your inventory and track your products. This helps ensure your customers always have the right product at the right time. It allows you to create long-term plans for managing demand-supply imbalance.
Kinaxis is a comprehensive supply chain management software solution that breaks down silos and streamlines processes. It combines human-machine intelligence to enable you to make better decision. It can also help you plan inventory and capacity, so you can better respond to opportunities.
You can use sales forecasting software to analyze historical sales, sales cycles, seasonality, and other factors. It also makes use of machine learning to predict future sales. This software predicts sales and helps to prepare sales teams for the future. This software also allows you to access data from many sources, making it easier to view the entire picture of your operation.
The main competitor to supply chain management software is Descartes Systems Group. They are the top vendor for many organizations. This company has over 13,000 active users, and its products compete with SAP SCM, Megaventory, JDA, and Logility.
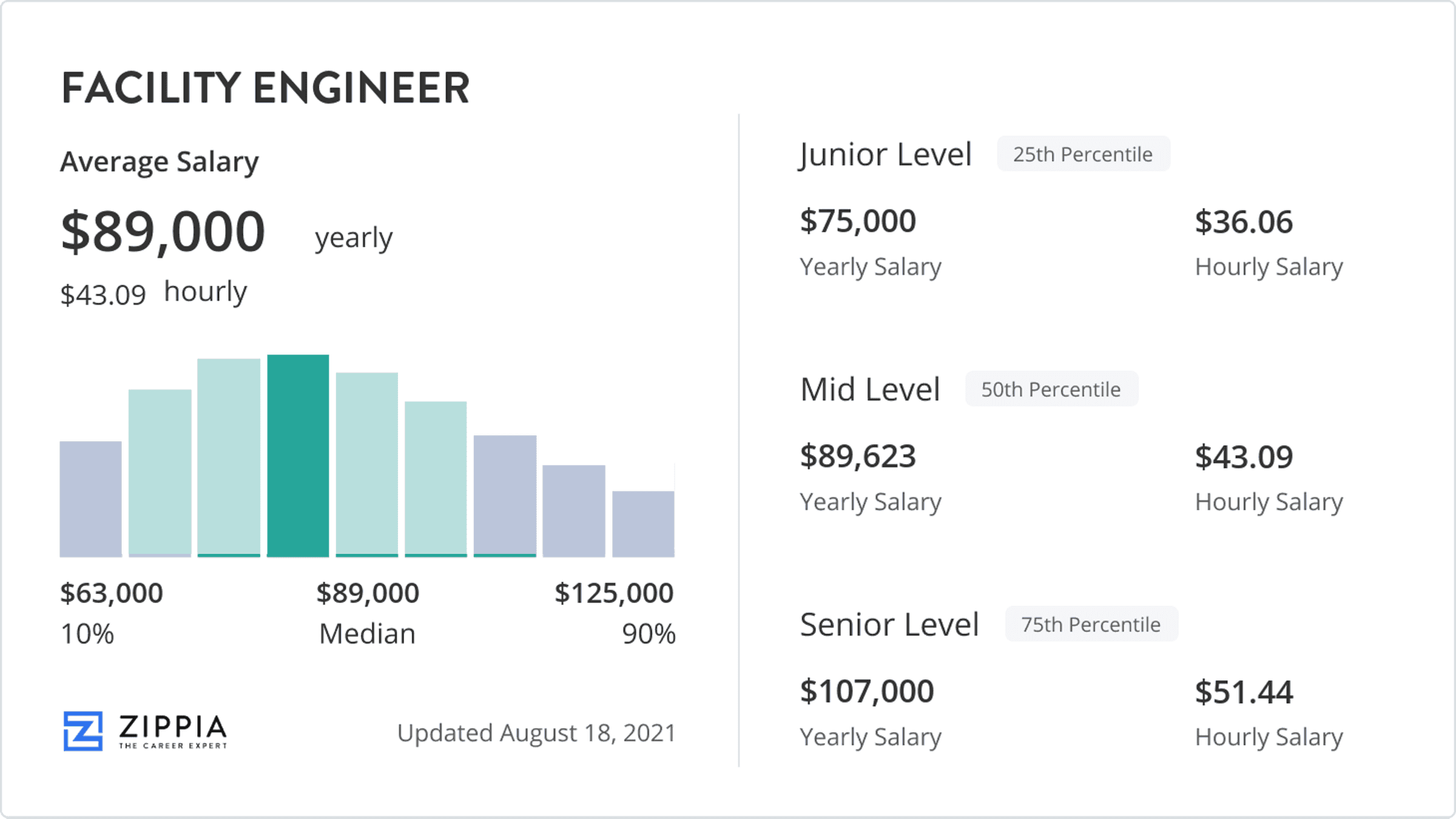
Another major competitor to supply chain management software is Manhattan Associates. Manhattan Associates has approximately $617.5 million in revenue and thousands of customers. Eddie Capel runs the company. This company competes in the market against Logility, JDA, and Infor SCM.
Infor SCM, a supply chain management software platform, is one of the most popular. It's a great solution for small and large businesses. It is a cloud-based software that unifies enterprise processes from end to end. It also provides analytics at the heart, which can help optimize your end to-end supply chain.
FAQ
Why should you automate your warehouse?
Modern warehousing has seen automation take center stage. With the rise of ecommerce, there is a greater demand for faster delivery times as well as more efficient processes.
Warehouses should be able adapt quickly to new needs. To do so, they must invest heavily in technology. Automation of warehouses offers many benefits. Here are some of the reasons automation is worth your investment:
-
Increases throughput/productivity
-
Reduces errors
-
Increases accuracy
-
Safety enhancements
-
Eliminates bottlenecks
-
Allows companies scale more easily
-
Increases efficiency of workers
-
It gives visibility to everything that happens inside the warehouse
-
Enhances customer experience
-
Improves employee satisfaction
-
It reduces downtime, and increases uptime
-
This ensures that quality products are delivered promptly
-
Removes human error
-
It helps ensure compliance with regulations
Why is logistics important for manufacturing?
Logistics are essential to any business. Logistics can help you achieve amazing results by helping to manage product flow from raw materials to finished products.
Logistics are also important in reducing costs and improving efficiency.
What are my options for learning more about manufacturing
Experience is the best way for you to learn about manufacturing. You can also read educational videos or take classes if this isn't possible.
Can we automate some parts of manufacturing?
Yes! Automation has been around since ancient times. The Egyptians invent the wheel thousands of year ago. To help us build assembly lines, we now have robots.
There are many uses of robotics today in manufacturing. These include:
-
Line robots
-
Robot welding
-
Robot painting
-
Robotics inspection
-
Robots create products
Manufacturing can also be automated in many other ways. 3D printing makes it possible to produce custom products in a matter of days or weeks.
What is it like to manage a logistics company?
To be a successful businessman in logistics, you will need many skills and knowledge. Effective communication skills are necessary to work with suppliers and clients. You need to understand how to analyze data and draw conclusions from it. You need to be able work under pressure and manage stressful situations. To improve efficiency, you must be innovative and creative. To motivate and guide your team towards reaching organizational goals, you must have strong leadership skills.
It is also important to be efficient and well organized in order meet deadlines.
What is the job of a production plan?
A production planner makes sure all project elements are delivered on schedule, within budget, as well as within the agreed scope. They also ensure the quality of the product and service meets the client's requirements.
Statistics
- Job #1 is delivering the ordered product according to specifications: color, size, brand, and quantity. (netsuite.com)
- According to the United Nations Industrial Development Organization (UNIDO), China is the top manufacturer worldwide by 2019 output, producing 28.7% of the total global manufacturing output, followed by the United States, Japan, Germany, and India.[52][53] (en.wikipedia.org)
- In the United States, for example, manufacturing makes up 15% of the economic output. (twi-global.com)
- You can multiply the result by 100 to get the total percent of monthly overhead. (investopedia.com)
- According to a Statista study, U.S. businesses spent $1.63 trillion on logistics in 2019, moving goods from origin to end user through various supply chain network segments. (netsuite.com)
External Links
How To
Six Sigma in Manufacturing:
Six Sigma is defined by "the application SPC (statistical process control) techniques to achieve continuous improvements." Motorola's Quality Improvement Department, Tokyo, Japan, developed it in 1986. Six Sigma's main goal is to improve process quality by standardizing processes and eliminating defects. Many companies have adopted Six Sigma in recent years because they believe that there are no perfect products and services. Six Sigma's main objective is to reduce variations from the production average. It is possible to measure the performance of your product against an average and find the percentage of time that it differs from the norm. If this deviation is too big, you know something needs fixing.
Understanding the nature of variability in your business is the first step to Six Sigma. Once you understand this, you can then identify the causes of variation. Also, you will need to identify the sources of variation. Random variations are caused when people make mistakes. While systematic variations are caused outside of the process, they can occur. These are, for instance, random variations that occur when widgets are made and some fall off the production line. But if you notice that every widget you make falls apart at the exact same place each time, this would indicate that there is a problem.
Once you've identified where the problems lie, you'll want to design solutions to eliminate those problems. You might need to change the way you work or completely redesign the process. To verify that the changes have worked, you need to test them again. If they don’t work, you’ll need to go back and rework the plan.