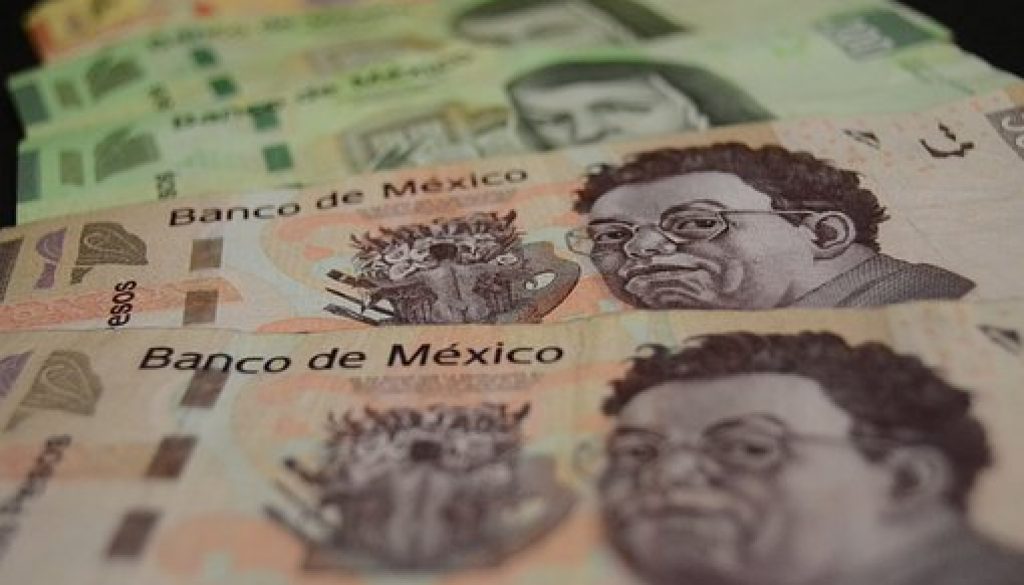
Visual management refers to the act of communicating information using visual signals. This method increases efficiency and clarity by recognizing information immediately. There are several kinds of visual control. Here are some examples. Learn more about visual control and Lean manufacturing. Keep reading to find out more. This method is a great way to get your company on track with lean manufacturing.
Lean manufacturing
One of the many methods used for visual management in lean manufacturing is the use of Andon, a Japanese word for status-display visualization. This helps workers and supervisors view work-in process, process flow and other essential information. Visual management also allows you to label workspaces, materials and parts. It allows for the identification of inefficiencies and simplifies processes. These are just some of the advantages of visual management for lean manufacturing.
Lean methodologies require visible tools for visual control. Supervisors and operators can use visual signals to identify waste, improve process flow and avoid errors. It can also help reduce safety concerns. Forklift drivers can stay in the right areas by looking at floor markings and other visual indicators. Visual management is a key component of lean manufacturing. Workers will be able to work more efficiently if they use visual management. Safety risks can be minimized by visual management.
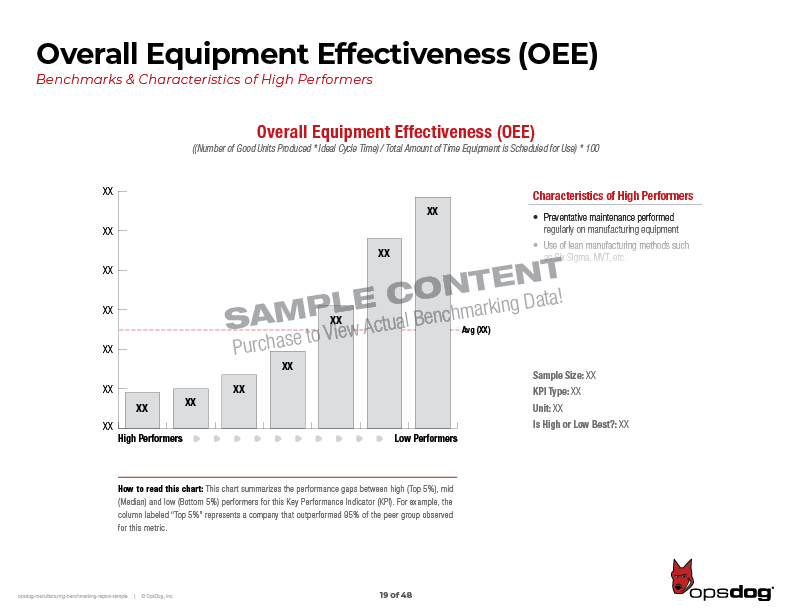
Process control charts
Process control charts can provide a visual tool to help visualize performance metrics, create a baseline, and improve output. They help management, operators, and other stakeholders get on the same page by identifying common causes of variation and setting the correct path for improvement. These charts are particularly helpful for processes that exhibit unusual patterns or variation. These process control charts are useful for visual management. They are easy to create, and can be used as visual indicators to see the status of any process.
A control chart's primary purpose is to monitor the process' performance over time. These charts show the sequence of measurements or samples, which allows a manager to determine if the process has been stable. These charts can be used to identify problems and suggest solutions. A line segment is a segment that connects the centerline of a control chart. This allows an operator to easily compare the process's performance to its baseline. The control limits are usually three standard deviations below and above the centerline.
FIFO lane
FIFO lanes can improve throughput and system utilization. Consider a fast food restaurant or assembly line. Most of us have probably experienced the frustration that comes with standing in long lines to obtain something. The FiFo lane helps you manage the flow of work by establishing priority in queues by using visual management. You can create these lanes by using paint lines, marking roller conveyors or clearly marking shelves. The first job arriving from Process A would go into the first open position of a FIFO lane. The next job would be moved into the next open position.
Time registration is one solution for improving FIFO lane visual management. Employees can record the date and time when carts are loaded into a FIFO lane. Some employees count the products using digital clocks right after putting them into the FIFO lane. Whiteboard stickers can also be used to mark times on carts. These whiteboard stickers can be used to indicate the order of each step.
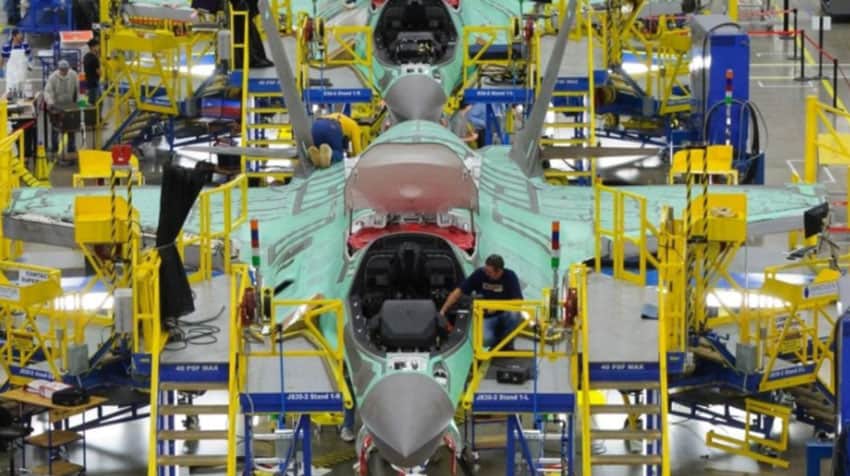
Lean daily management board
A multidisciplinary team was responsible for creating the Lean Daily Management Board. The board is based in part on five predetermined indicators: patient outcomes; documentation adherence; employee engagement and productivity. The team met each day to discuss progress in each area. Each day, the team reviewed progress using a checklist. This included medication compliance and medication falls. They used a problem solving instrument to deal with any unexpected events. The initial data collected in January 2014 noted a medication scan rate of 75% and a fall rate of 1.32/1000 patient days. These data are not applicable to patient care and continuing education.
Daily management allows for a more visible view of the process and allows for managers to address problems as they arise. Poor performers tend to be more flexible than others in order to reduce the amount of work they are asked to do. The poor performers need to be aware of the extra effort and time they spend on their work by making stretching work visible. Even though daily management doesn't have to be harsh, it does help highlight inefficient and ineffective processes. Those who cannot point to a process' failure should be evaluated as people issues.
FAQ
What are the 4 types manufacturing?
Manufacturing refers the process of turning raw materials into useful products with machines and processes. It includes many different activities like designing, building and testing, packaging, shipping and selling, as well as servicing.
What jobs are available in logistics?
There are many types of jobs in logistics. Some examples are:
-
Warehouse workers – They load and unload pallets and trucks.
-
Transportation drivers – They drive trucks or trailers to transport goods and perform pick-ups.
-
Freight handlers, - They sort out and pack freight in warehouses.
-
Inventory managers: They are responsible for the inventory and management of warehouses.
-
Sales representatives: They sell products to customers.
-
Logistics coordinators are responsible for organizing and planning logistics operations.
-
Purchasing agents are those who purchase goods and services for the company.
-
Customer service representatives – They answer emails and phone calls from customers.
-
Shipping clerks – They process shipping orders, and issue bills.
-
Order fillers: They fill orders based off what has been ordered and shipped.
-
Quality control inspectors – They inspect incoming and outgoing products to ensure that there are no defects.
-
Others - There are many types of jobs in logistics such as transport supervisors and cargo specialists.
Is automation necessary in manufacturing?
Automation is essential for both manufacturers and service providers. They can provide services more quickly and efficiently thanks to automation. They can also reduce their costs by reducing human error and improving productivity.
What are the products of logistics?
Logistics involves the transportation of goods from point A and point B.
These include all aspects related to transport such as packaging, loading and transporting, storing, transporting, unloading and warehousing inventory management, customer service. Distribution, returns, recycling are some of the options.
Logisticians ensure that the right product reaches the right place at the right time and under safe conditions. Logisticians help companies improve their supply chain efficiency by providing information about demand forecasts and stock levels, production schedules, as well as availability of raw materials.
They coordinate with vendors and suppliers, keep track of shipments, monitor quality standards and perform inventory and order replenishment.
How can I find out more about manufacturing?
Practical experience is the best way of learning about manufacturing. You can read books, or watch instructional videos if you don't have the opportunity to do so.
Statistics
- Job #1 is delivering the ordered product according to specifications: color, size, brand, and quantity. (netsuite.com)
- In 2021, an estimated 12.1 million Americans work in the manufacturing sector.6 (investopedia.com)
- According to a Statista study, U.S. businesses spent $1.63 trillion on logistics in 2019, moving goods from origin to end user through various supply chain network segments. (netsuite.com)
- (2:04) MTO is a production technique wherein products are customized according to customer specifications, and production only starts after an order is received. (oracle.com)
- Many factories witnessed a 30% increase in output due to the shift to electric motors. (en.wikipedia.org)
External Links
How To
Six Sigma in Manufacturing:
Six Sigma refers to "the application and control of statistical processes (SPC) techniques in order to achieve continuous improvement." Motorola's Quality Improvement Department in Tokyo, Japan developed Six Sigma in 1986. Six Sigma is a method to improve quality through standardization and elimination of defects. Since there are no perfect products, or services, this approach has been adopted by many companies over the years. Six Sigma aims to reduce variation in the production's mean value. This means that you can take a sample from your product and then compare its performance to the average to find out how often the process differs from the norm. If it is too large, it means that there are problems.
Understanding the nature of variability in your business is the first step to Six Sigma. Once you understand that, it is time to identify the sources of variation. This will allow you to decide if these variations are random and systematic. Random variations are caused when people make mistakes. While systematic variations are caused outside of the process, they can occur. You could consider random variations if some widgets fall off the assembly lines. But if you notice that every widget you make falls apart at the exact same place each time, this would indicate that there is a problem.
Once you've identified where the problems lie, you'll want to design solutions to eliminate those problems. You might need to change the way you work or completely redesign the process. You should then test the changes again after they have been implemented. If they fail, you can go back to the drawing board to come up with a different plan.