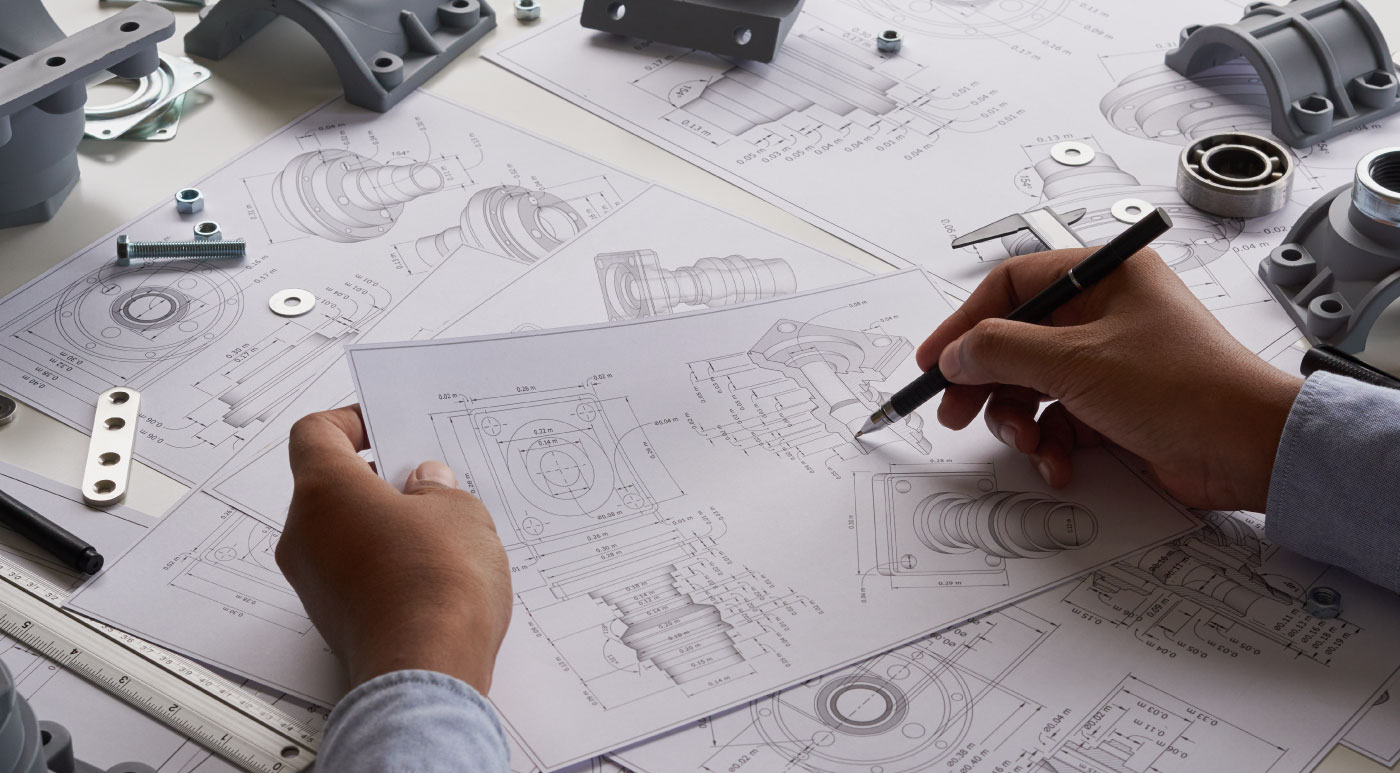
What is supply chain management? Supply chain management is a cross-functional process that manages relationships across the entire supply chain. By improving operations and financial performance, supply chain management improves overall business performance. This article will explain the basics of supply chain management, and how it can be used to improve your organization. Let's get started! What is supply chain management? Why is supply management so important? Here are a few examples of how it can benefit your business.
Management of supply chain relationships is the goal of supply chain management
When selling products, companies need to know how to source raw materials and produce parts. The physical flow is initiated by a supplier. From there, it moves on to various stages, including a distributor, manufacturer, retailer, and finally to the consumer. While some supply chains skip some steps, the physical goods must still be transported from one place to another, stored for a time and delivered to the customer. This process requires planning and organization.
Successful supply chain management requires integrating all business functions. Clear communication is essential for suppliers and vendors. Information sharing helps both parties understand what to expect, reduce costs, and improve quality. Collaboration improves communication across the supply chains and helps both parties. Customers should know about the company's operations and vendors must be able to deliver emergency supplies. Perishable goods are more sensitive than usual.
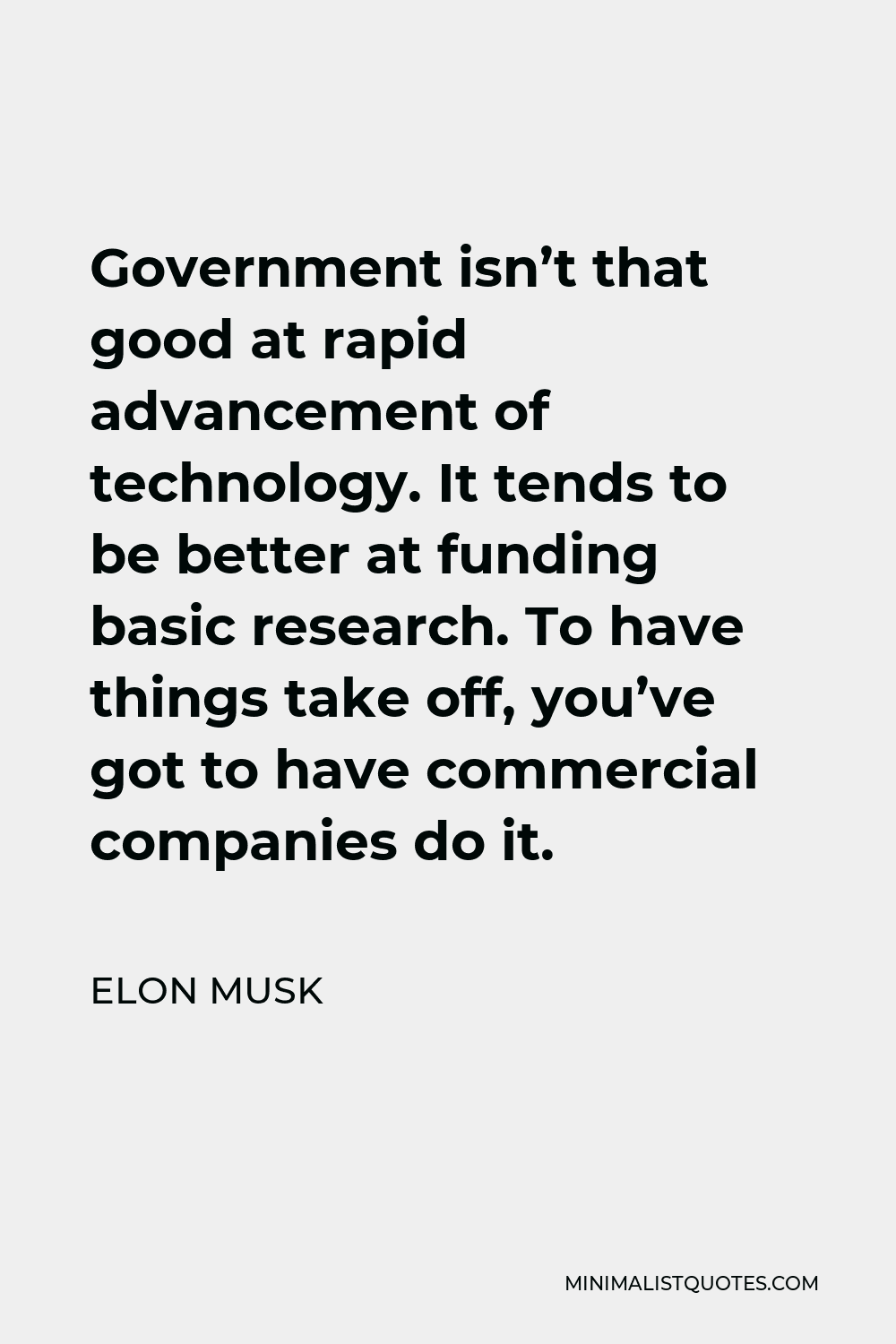
It is cross-functional and business-related.
There are many cross-functional factors that need to be considered when a company is looking at its supply chain. To ensure a successful supply-chain, suppliers must be able and willing to deliver the goods on time. It is therefore essential to coordinate with them. If companies follow the steps of Supply Chain Management, they can avoid many problems. This will not only improve efficiency but also save them money.
Management must understand the interdependencies within the supply chain and work towards increasing profitability. All parties should be able to benefit equally from improvements in process, but it is important that there are guidelines about how the rewards will be shared. Some parties to the supply chain might not see the benefits of a better process unless they are based upon a common measurement system. It may be deemed uneffective if the value cannot be captured.
It reduces operating and maintenance costs
One of the most effective ways to reduce operating costs is by streamlining your ordering processes. Your employees will be more likely to use one software system for all requisitions. To reduce your operating costs, you can set up approvals to limit the number of goods that you order. In addition to eliminating errors and confusion, a streamlined software system will allow you to monitor your inventory, order only the quantities you need, and prevent shipments from being made if they are not needed.
An alternative method to reduce operating expenses is improving communication among warehouse employees. You should first examine your current workflow and identify any bottlenecks. Consolidating or using dedicated transport services can help reduce transportation costs. If you're able to do this, your operating costs will drop by a significant amount. This will help you not only lower your transport costs but also speed up the delivery of your products.
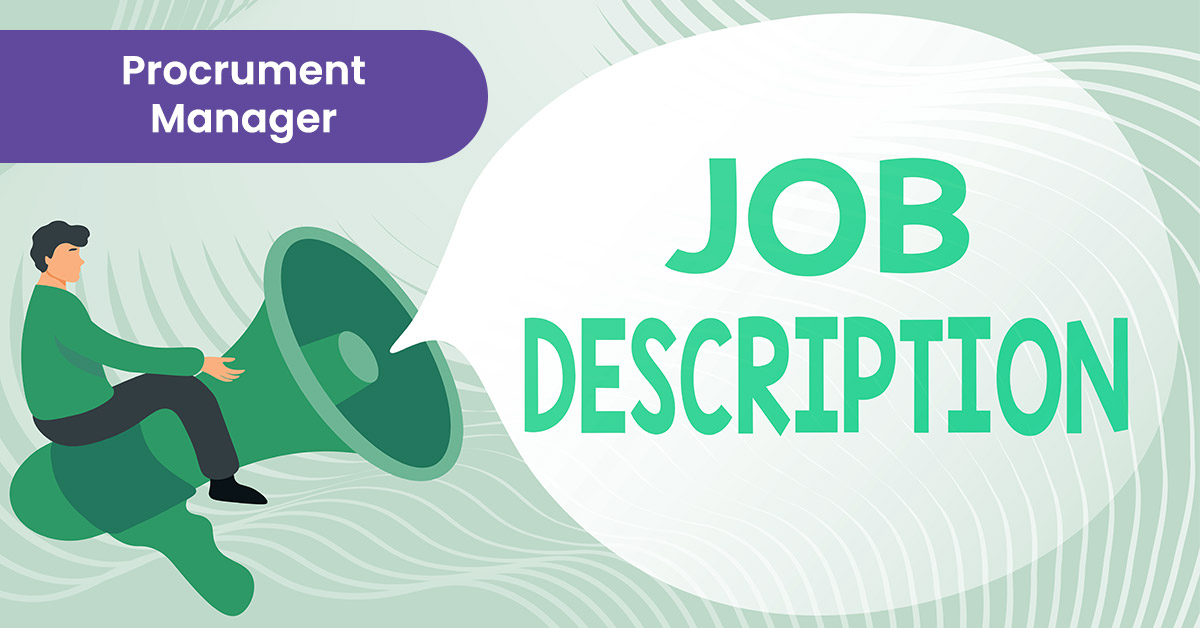
It improves your financial position
The financial performance of a company can be improved in several ways by good supply chain management. A supply chain manager who is skilled can lower production costs while maximising the benefits from variable costs. Increased profit margins are possible when costs can be controlled. A major benefit of improving cash flow is maximizing profit margins. A faster delivery of products to the customer can help it invoice its customers earlier, reducing the need to purchase expensive building space. Additionally, a better supply network reduces the costs of fixed assets.
The Statement of Shareholders' Equity (SSE) is a key financial statement that summarizes the ownership portion of a company. Improving a firm’s supply chain can boost after-tax liquidity by 8.5%. A company can improve its supply chain performance to reduce its costs and increase its customer satisfaction. The company can also achieve higher operational efficiencies through better supply chain management, which will result in greater profits.
FAQ
What does it mean to be a manufacturer?
Manufacturing Industries are companies that manufacture products. The people who buy these products are called consumers. To accomplish this goal, these companies employ a range of processes including distribution, sales, management, and production. They produce goods from raw materials by using machines and other machinery. This includes all types and varieties of manufactured goods, such as food items, clothings, building supplies, furnitures, toys, electronics tools, machinery vehicles, pharmaceuticals medical devices, chemicals, among others.
What is the role of a production manager?
A production planner makes sure all project elements are delivered on schedule, within budget, as well as within the agreed scope. They also ensure that the product/service meets the client’s needs.
Why is logistics important in manufacturing
Logistics are an essential part of any business. They help you achieve great results by helping you manage all aspects of product flow, from raw materials to finished goods.
Logistics are also important in reducing costs and improving efficiency.
What are the four types in manufacturing?
Manufacturing refers to the transformation of raw materials into useful products by using machines and processes. It includes many different activities like designing, building and testing, packaging, shipping and selling, as well as servicing.
What skills should a production planner have?
Production planners must be flexible, organized, and able handle multiple tasks. You must also be able to communicate effectively with clients and colleagues.
What is the difference between Production Planning, Scheduling and Production Planning?
Production Planning (PP) refers to the process of determining how much production is needed at any given moment. Forecasting demand is one way to do this.
Scheduling involves the assignment of dates and times to tasks in order to complete them within the timeframe.
Are there ways to automate parts of manufacturing?
Yes! Automation has been around since ancient times. The Egyptians created the wheel thousands years ago. To help us build assembly lines, we now have robots.
There are many applications for robotics in manufacturing today. These include:
-
Line robots
-
Robot welding
-
Robot painting
-
Robotics inspection
-
Robots that create products
Automation can be applied to manufacturing in many other ways. For instance, 3D printing allows us make custom products and not have to wait for months or even weeks to get them made.
Statistics
- Many factories witnessed a 30% increase in output due to the shift to electric motors. (en.wikipedia.org)
- You can multiply the result by 100 to get the total percent of monthly overhead. (investopedia.com)
- [54][55] These are the top 50 countries by the total value of manufacturing output in US dollars for its noted year according to World Bank.[56] (en.wikipedia.org)
- In the United States, for example, manufacturing makes up 15% of the economic output. (twi-global.com)
- In 2021, an estimated 12.1 million Americans work in the manufacturing sector.6 (investopedia.com)
External Links
How To
How to use Lean Manufacturing in the production of goods
Lean manufacturing (or lean manufacturing) is a style of management that aims to increase efficiency, reduce waste and improve performance through continuous improvement. It was developed in Japan between 1970 and 1980 by Taiichi Ohno. TPS founder Kanji Tyoda gave him the Toyota Production System, or TPS award. Michael L. Watkins published the "The Machine That Changed the World", the first book about lean manufacturing. It was published in 1990.
Lean manufacturing refers to a set of principles that improve the quality, speed and costs of products and services. It emphasizes eliminating waste and defects throughout the value stream. Lean manufacturing is called just-in-time (JIT), zero defect, total productive maintenance (TPM), or 5S. Lean manufacturing emphasizes reducing non-value-added activities like inspection, rework and waiting.
Lean manufacturing improves product quality and costs. It also helps companies reach their goals quicker and decreases employee turnover. Lean manufacturing has been deemed one of the best ways to manage the entire value-chain, including customers, distributors as well retailers and employees. Lean manufacturing can be found in many industries. For example, Toyota's philosophy underpins its success in automobiles, electronics, appliances, healthcare, chemical engineering, aerospace, paper, food, etc.
Lean manufacturing includes five basic principles:
-
Define value - Find out what your business contributes to society, and what makes it different from other competitors.
-
Reduce Waste - Eliminate any activity that doesn't add value along the supply chain.
-
Create Flow - Ensure work moves smoothly through the process without interruption.
-
Standardize and simplify – Make processes as repeatable and consistent as possible.
-
Build Relationships- Develop personal relationships with both internal as well as external stakeholders.
Lean manufacturing, although not new, has seen renewed interest in the economic sector since 2008. Many businesses have adopted lean production techniques to make them more competitive. Many economists believe lean manufacturing will play a major role in economic recovery.
Lean manufacturing has many benefits in the automotive sector. These include improved customer satisfaction, reduced inventory levels, lower operating costs, increased productivity, and better overall safety.
You can apply Lean Manufacturing to virtually any aspect of your organization. It is especially useful for the production aspect of an organization, as it ensures that every step in the value chain is efficient and effective.
There are three types of lean manufacturing.
-
Just-in-Time Manufacturing: Also known as "pull systems", this type of lean manufacturing uses just-in-time manufacturing (JIT). JIT is a method in which components are assembled right at the moment of use, rather than being manufactured ahead of time. This approach reduces lead time, increases availability and reduces inventory.
-
Zero Defects Manufacturing - ZDM: ZDM focuses its efforts on making sure that no defective units leave a manufacturing facility. You should repair any part that needs to be repaired during an assembly line. This is true even for finished products that only require minor repairs prior to shipping.
-
Continuous Improvement (CI): CI aims to improve the efficiency of operations by continuously identifying problems and making changes in order to eliminate or minimize waste. Continuous Improvement (CI) involves continuous improvement in processes, people, tools, and infrastructure.