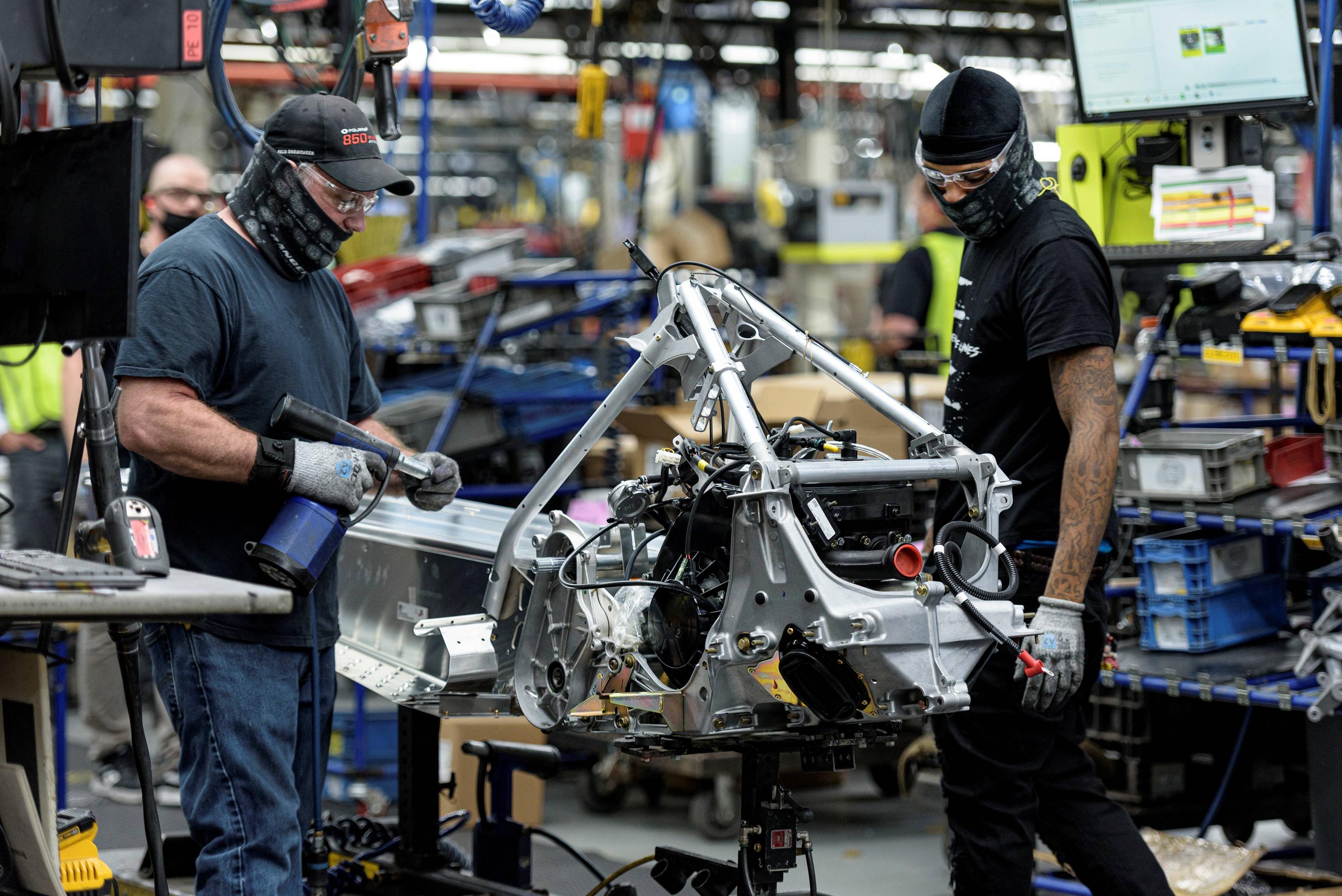
Biochemist salaries are the most lucrative among all jobs in the healthcare industry at $84,365. These professionals research drugs and the effects they have on living organisms. They also create new chemical compounds. They could work in a company, or be a professor at a college.
The education requirements for a biochemist vary depending on the type of job and the employer. Many employers prefer candidates with advanced degrees. Some employers require only a bachelor’s degree. For positions in biophysics (the study of biological phenomena and physical laws), a master's degree is sometimes required.
Biochemists do research on new chemical compounds. They also devise quality control methods for materials. Biochemists are often paired with biophysicists who study the relationships between biological phenomena and physical laws. They may also be associated with chemical biologists, who are responsible to prepare samples and develop medicinal-chemistry strategies.
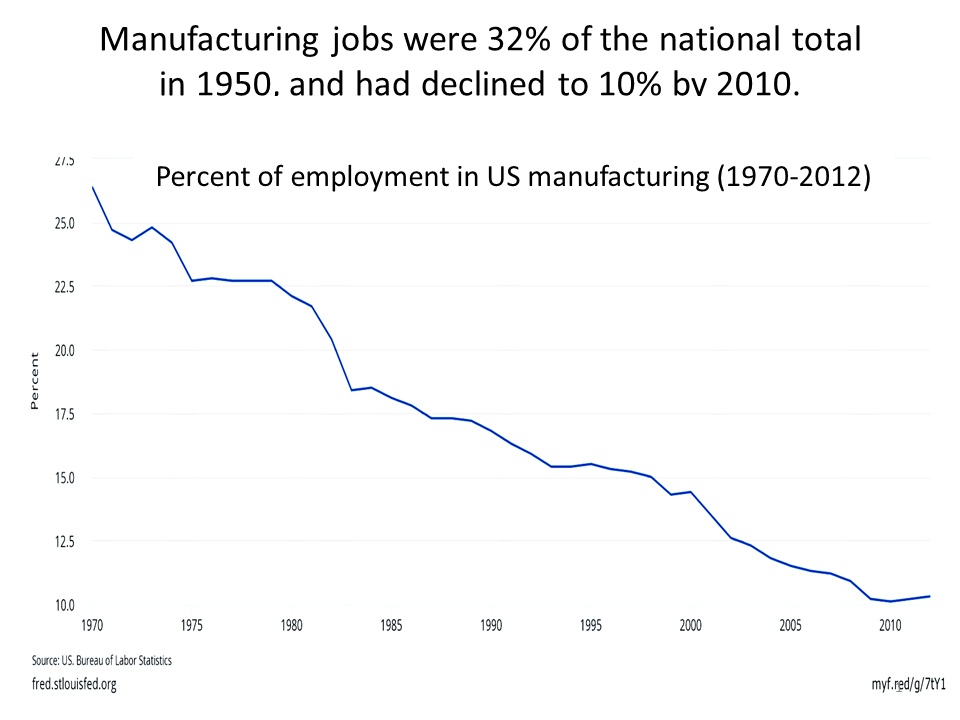
Biochemists could work in the pharmaceutical and manufacturing industries. Pfizer, GlaxoSmithkline and Amgen are some of the most prominent employers. These companies are known to pay high salaries but it can be hard for people to get jobs at these companies. Companies such as Genentech are also difficult to secure, although their salaries are comparable. Eurofins and Siemens Healthineers also have biochemist jobs.
A biochemist may also serve as a professor at a college. These professionals educate students about biology, and other organisms. They may also play a role in environmental restoration. They may be involved in the development of new chemical compounds or formulations for environmental problems. Biochemists also may study the effects that hormones and other drugs have on living organisms.
Many biochemists support the study and practice of biochemistry. Advocates can receive degrees from universities such Western Illinois University (Trinity University), Western Illinois University (Kean University) and others. They may also have internships at research labs. These internships will help students make connections in the field as well as gain real-world experience. They may be eligible to become a researcher associate or lecturer.
Biochemists generally have a bachelor’s degree and a Doctorate. These degrees will be required for entry-level roles in biochemistry. It is possible for biochemists to earn a license even if they do not go to college. A license may be required for jobs that involve contact with patients. Certain positions such as medical assistants may also require a license. These positions are often part of a small staff, but can offer potential for advancement.
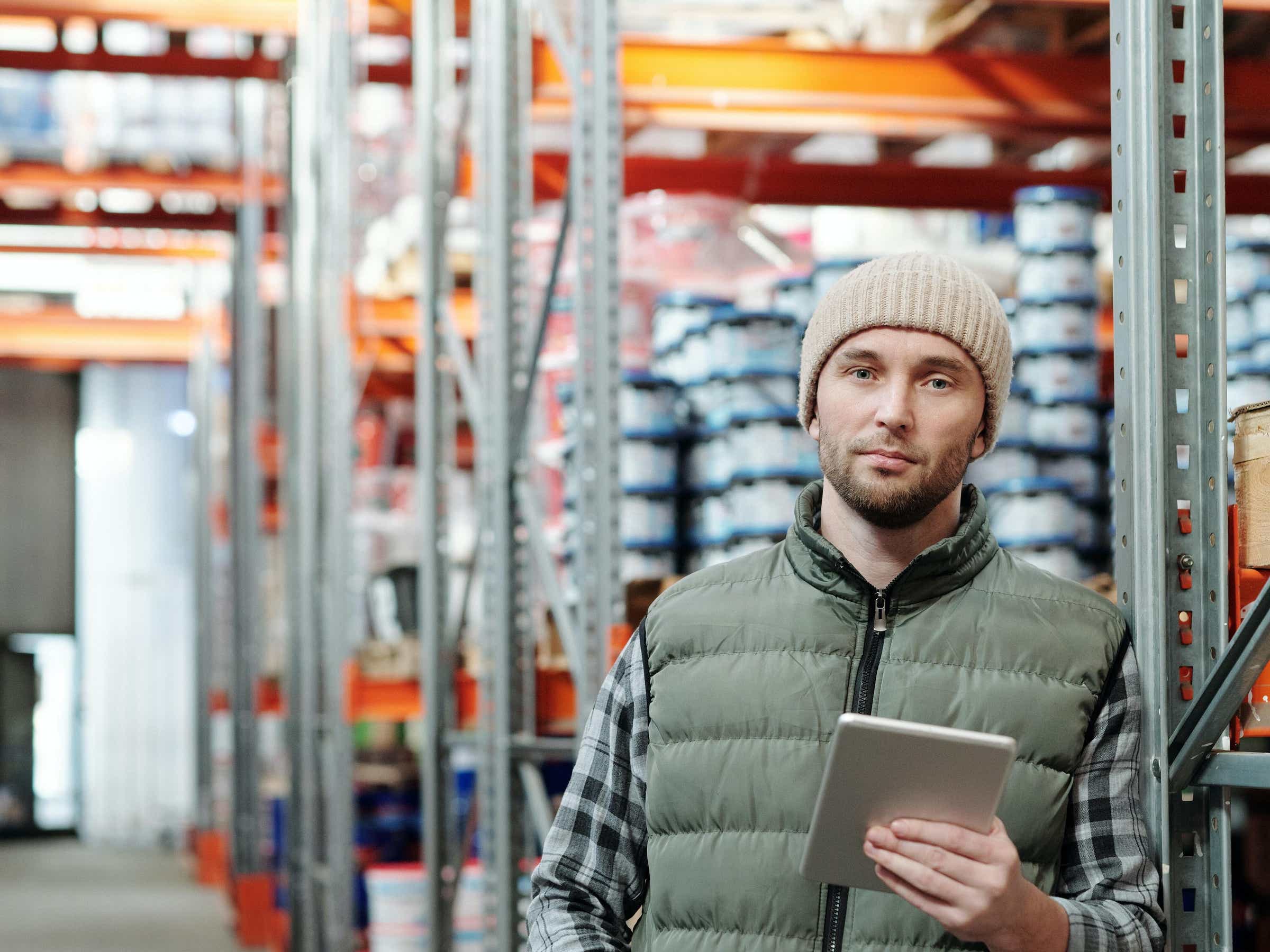
Salaries for biochemists vary widely. The median annual income is $76,806; the average salary, $95,998, is $95,998. The salary of biochemists will rise by 2020. The top employers in the health care industry, such as Pfizer, Eurofins, and Amgen, all pay their employees a high salary. GlaxoSmithkline as well as Siemens Healthineers offer biochemist salaries comparable to other professionals.
Many biochemists are chemical biologists. These professionals analyse samples and prepare reports. They also oversee lab operations. They must have strong experimental skills to be able prepare samples and present findings for stakeholders.
FAQ
What are the products and services of logistics?
Logistics refers to the movement of goods from one place to another.
They include all aspects associated with transport including packaging, loading transporting, unloading storage, warehousing inventory management customer service, distribution returns and recycling.
Logisticians ensure that products reach the right destination at the right moment and under safe conditions. Logisticians help companies improve their supply chain efficiency by providing information about demand forecasts and stock levels, production schedules, as well as availability of raw materials.
They keep track and monitor the transit of shipments, maintain quality standards, order replenishment and inventories, coordinate with suppliers, vendors, and provide support for sales and marketing.
What are the responsibilities of a logistic manager?
Logistics managers are responsible for ensuring that all goods arrive in perfect condition and on time. This is done using his/her knowledge of the company's products. He/she should also ensure enough stock is available to meet demand.
What are the 4 types manufacturing?
Manufacturing refers to the transformation of raw materials into useful products by using machines and processes. It involves many different activities such as designing, building, testing, packaging, shipping, selling, servicing, etc.
What skills should a production planner have?
You must be flexible and organized to become a productive production planner. Communication skills are essential to ensure that you can communicate effectively with clients, colleagues, and customers.
Why automate your warehouse
Automation has become increasingly important in modern warehousing. E-commerce has increased the demand for quicker delivery times and more efficient processes.
Warehouses must adapt quickly to meet changing customer needs. Technology is essential for warehouses to be able to adapt quickly to changing needs. Automating warehouses has many benefits. Here are some reasons why it's worth investing in automation:
-
Increases throughput/productivity
-
Reduces errors
-
Accuracy is improved
-
Safety Boosts
-
Eliminates bottlenecks
-
Allows companies scale more easily
-
Increases efficiency of workers
-
Provides visibility into everything that happens in the warehouse
-
Enhances customer experience
-
Improves employee satisfaction
-
Reducing downtime and increasing uptime
-
This ensures that quality products are delivered promptly
-
Eliminates human error
-
Helps ensure compliance with regulations
What is manufacturing and logistics?
Manufacturing is the process of creating goods from raw materials by using machines and processes. Logistics manages all aspects of the supply chain, including procurement, production planning and distribution, inventory control, transportation, customer service, and transport. Logistics and manufacturing are often referred to as one thing. It encompasses both the creation of products and their delivery to customers.
Statistics
- (2:04) MTO is a production technique wherein products are customized according to customer specifications, and production only starts after an order is received. (oracle.com)
- You can multiply the result by 100 to get the total percent of monthly overhead. (investopedia.com)
- According to a Statista study, U.S. businesses spent $1.63 trillion on logistics in 2019, moving goods from origin to end user through various supply chain network segments. (netsuite.com)
- In the United States, for example, manufacturing makes up 15% of the economic output. (twi-global.com)
- Job #1 is delivering the ordered product according to specifications: color, size, brand, and quantity. (netsuite.com)
External Links
How To
How to Use Six Sigma in Manufacturing
Six Sigma refers to "the application and control of statistical processes (SPC) techniques in order to achieve continuous improvement." Motorola's Quality Improvement Department created Six Sigma at their Tokyo plant, Japan in 1986. Six Sigma's core idea is to improve the quality of processes by standardizing and eliminating defects. Many companies have adopted this method in recent years. They believe there is no such thing a perfect product or service. The main goal of Six Sigma is to reduce variation from the mean value of production. This means that you can take a sample from your product and then compare its performance to the average to find out how often the process differs from the norm. If there is a significant deviation from the norm, you will know that something needs to change.
Understanding how variability works in your company is the first step to Six Sigma. Once you understand this, you can then identify the causes of variation. These variations can also be classified as random or systematic. Random variations happen when people make errors; systematic variations are caused externally. These are, for instance, random variations that occur when widgets are made and some fall off the production line. But if you notice that every widget you make falls apart at the exact same place each time, this would indicate that there is a problem.
Once you've identified the problem areas you need to find solutions. That solution might involve changing the way you do things or redesigning the process altogether. Once you have implemented the changes, it is important to test them again to ensure they work. If they don't work, you will need to go back to the drawing boards and create a new plan.