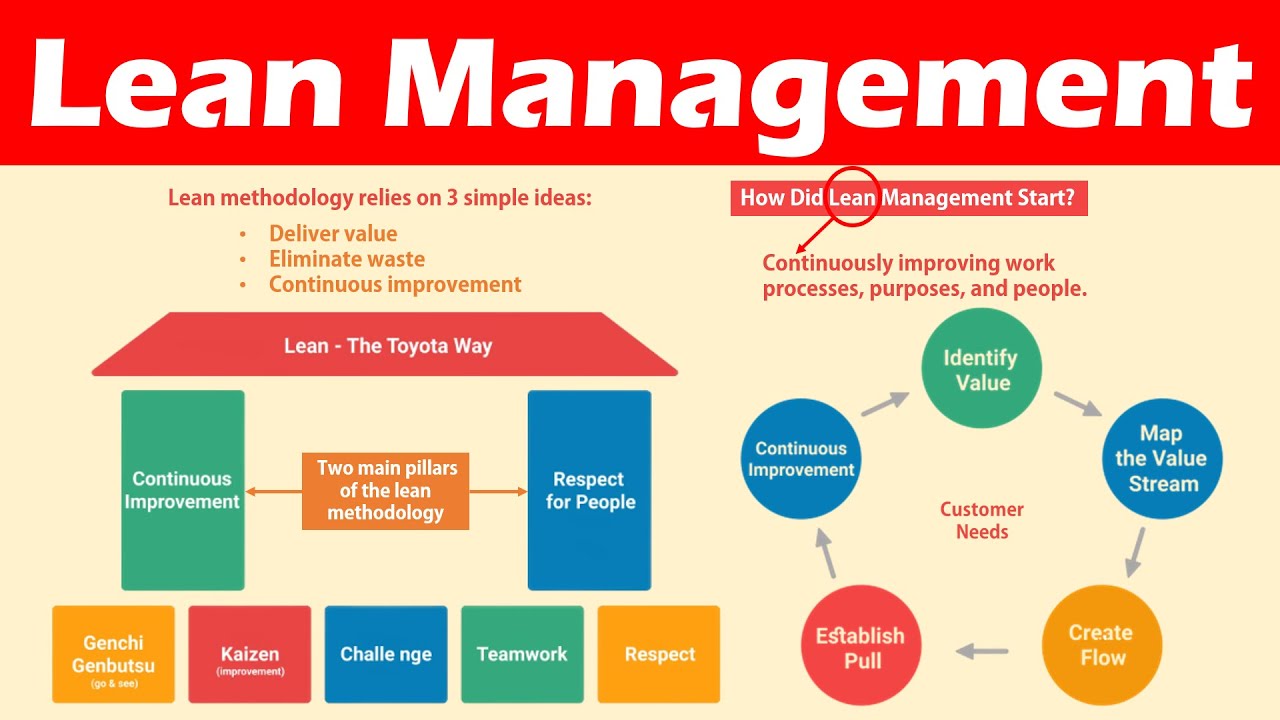
In advanced manufacturing, companies employ innovative technologies to make better products. These technologies are often referred to as cutting-edge, innovative, and advanced. These technologies are being integrated into more companies' operations. Some of these technologies are: Robotics, Material deposition, and Additive manufacturing. These technologies can be found out more.
Additive manufacturing
Advanced manufacturing through additive manufacturing is the future for many manufacturing businesses. This type involves additive manufacturing technologies also known as 3D printers. This type of manufacturing has several advantages, including increased flexibility and lower inventory costs. It also reduces the need to import labor-intensive components and parts.
Innovations in additive manufacturing technology have greatly increased the speed of manufacturing. They allow businesses to respond quickly to supply-chain disruptions. They can produce custom parts in hours or days. This process is particularly useful in industries that suffer from supply-chain bottlenecks. Advanced manufacturing is capable of producing parts with complex geometries.
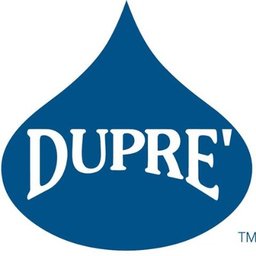
It also allows manufacturers to produce very small quantities of a product. For example, additive manufacturing can be used to produce custom dental appliances. Additionally, complex structures can be manufactured using the additive manufacturing process, including internal heat channels. Advanced manufacturing through additive manufacturing helps reduce the inventory requirements and makes it possible to produce specialized components. It can reduce material costs by ninety per cent and reduce energy consumption by half.
Robotics
Most industrial producers have recognized the potential for advanced robotics and are looking to implement them in their factories. They are not satisfied with the performance or progress they have made. Many of them blame the limitations of current technology and its high costs for limiting their ability to deploy more widely. They lack key enablers that will allow them to fully deploy advanced robots in their factories.
In order to successfully integrate advanced robots, manufacturers must examine their system architecture. These systems must include infrastructure, analytics, and data and workflow management. After these capabilities are established, companies can select strategic robotics vendors. These partners will assist the company in determining which technologies and processes work best for them. In the case of robotics, this can be accomplished with the use of simulation models.
Advanced robotics is rapidly changing across many industries. Robotic automation can be applied in many areas, such as aerospace, medical and automotive manufacturing. This technology has transformed the manufacturing sector. Robotic automation can reduce human labor costs and save energy. It works 24 hours per day without the need to turn on lights.
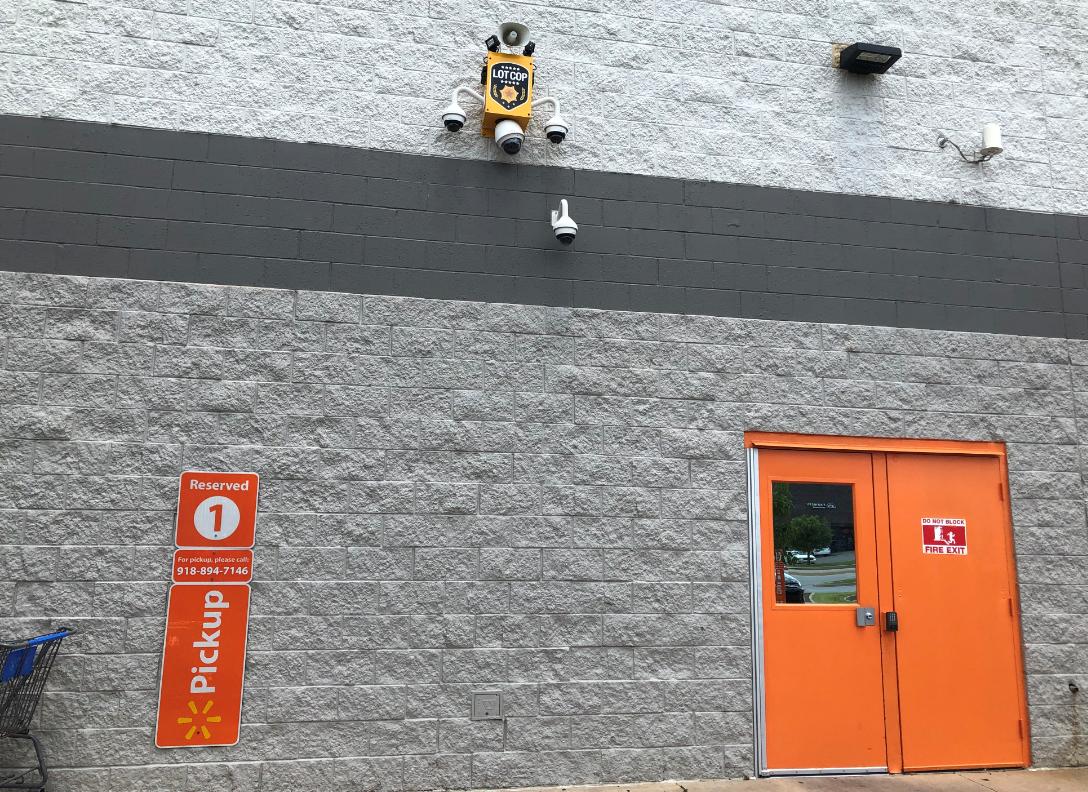
Material deposition
Material deposition plays an important role in advanced manufacturing. The process involves using a combination of laser beams and arc plasma energies to deposit thin films of a material on a target. The substrate is typically made of powder or wire. Deposition happens in an inert gases or vacuum. Other energy sources can also be used.
Plasma metal deposition is one of the most promising direct energy deposition techniques. It uses a plasma source for metals to be deposited. The process allows for the use of wire, powder, or both as feedstock, and can create large, complex parts. This process has many benefits, including a reduced amount of machining and a shorter lead-time.
This process can be applied to ceramics, polymers, and metals. Metals are usually used in either wire or powder form.
FAQ
How does a production planner differ from a project manager?
A production planner is more involved in the planning phase of the project than a project manger.
Why automate your warehouse
Automation has become increasingly important in modern warehousing. The rise of e-commerce has led to increased demand for faster delivery times and more efficient processes.
Warehouses need to adapt quickly to meet changing needs. Technology investment is necessary to enable warehouses to respond quickly to changing demands. Automating warehouses has many benefits. These are some of the benefits that automation can bring to warehouses:
-
Increases throughput/productivity
-
Reduces errors
-
Increases accuracy
-
Boosts safety
-
Eliminates bottlenecks
-
Allows companies to scale more easily
-
Workers are more productive
-
Provides visibility into everything that happens in the warehouse
-
Enhances customer experience
-
Improves employee satisfaction
-
Reduces downtime and improves uptime
-
Quality products delivered on time
-
Eliminates human error
-
Helps ensure compliance with regulations
What does it take for a logistics enterprise to succeed?
To run a successful logistics company, you need a lot knowledge and skills. To communicate effectively with clients and suppliers, you must be able to communicate well. You should be able analyse data and draw inferences. You must be able and able to handle stress situations and work under pressure. You must be creative and innovative to develop new ideas to improve efficiency. You will need strong leadership skills to motivate and direct your team members towards achieving their organizational goals.
You should also be organized and efficient to meet tight deadlines.
What is the responsibility of a manufacturing manager?
A manufacturing manager must make sure that all manufacturing processes run smoothly and effectively. They must also be alert to any potential problems and take appropriate action.
They should also know how to communicate with other departments such as sales and marketing.
They should also be aware of the latest trends in their industry and be able to use this information to help improve productivity and efficiency.
How can manufacturing excess production be decreased?
It is essential to find better ways to manage inventory to reduce overproduction. This would reduce the amount of time spent on unnecessary activities such as purchasing, storing, and maintaining excess stock. This could help us free up our time for other productive tasks.
This can be done by using a Kanban system. A Kanbanboard is a visual tool that allows you to keep track of the work being done. Work items are moved through various states to reach their destination in a Kanban system. Each state is assigned a different priority.
When work is completed, it can be transferred to the next stage. A task that is still in the initial stages of a process will be considered complete until it moves on to the next stage.
This allows you to keep work moving along while making sure that no work gets neglected. With a Kanban board, managers can see exactly how much work is being done at any given moment. This information allows them to adjust their workflow based on real-time data.
Another way to control inventory levels is to implement lean manufacturing. Lean manufacturing seeks to eliminate waste from every step of the production cycle. Waste includes anything that does not add value to the product. These are some of the most common types.
-
Overproduction
-
Inventory
-
Unnecessary packaging
-
Overstock materials
Manufacturers can reduce their costs and improve their efficiency by using these ideas.
Can we automate some parts of manufacturing?
Yes! Yes. Automation has been around since ancient time. The Egyptians discovered the wheel thousands and years ago. Robots are now used to assist us in assembly lines.
There are many uses of robotics today in manufacturing. They include:
-
Assembly line robots
-
Robot welding
-
Robot painting
-
Robotics inspection
-
Robots that produce products
Manufacturing could also benefit from automation in other ways. 3D printing, for example, allows us to create custom products without waiting for them to be made.
Why is logistics important in manufacturing?
Logistics are an integral part any business. They can help you achieve great success by helping you manage product flow from raw material to finished goods.
Logistics are also important in reducing costs and improving efficiency.
Statistics
- Many factories witnessed a 30% increase in output due to the shift to electric motors. (en.wikipedia.org)
- It's estimated that 10.8% of the U.S. GDP in 2020 was contributed to manufacturing. (investopedia.com)
- You can multiply the result by 100 to get the total percent of monthly overhead. (investopedia.com)
- [54][55] These are the top 50 countries by the total value of manufacturing output in US dollars for its noted year according to World Bank.[56] (en.wikipedia.org)
- According to the United Nations Industrial Development Organization (UNIDO), China is the top manufacturer worldwide by 2019 output, producing 28.7% of the total global manufacturing output, followed by the United States, Japan, Germany, and India.[52][53] (en.wikipedia.org)
External Links
How To
How to Use 5S to Increase Productivity in Manufacturing
5S stands as "Sort", Set In Order", Standardize", Separate" and "Store". Toyota Motor Corporation created the 5S methodology in 1954. It assists companies in improving their work environments and achieving higher efficiency.
The idea behind standardizing production processes is to make them repeatable and measurable. This means that daily tasks such as cleaning and sorting, storage, packing, labeling, and packaging are possible. This knowledge allows workers to be more efficient in their work because they are aware of what to expect.
There are five steps to implementing 5S, including Sort, Set In Order, Standardize, Separate and Store. Each step involves a different action which leads to increased efficiency. For example, when you sort things, you make them easy to find later. When you arrange items, you place them together. Then, after you separate your inventory into groups, you store those groups in containers that are easy to access. Finally, label all containers correctly.
This process requires employees to think critically about how they do their job. Employees must understand why they do certain tasks and decide if there's another way to accomplish them without relying on the old ways of doing things. To be successful in the 5S system, employees will need to acquire new skills and techniques.
In addition to increasing efficiency, the 5S method also improves morale and teamwork among employees. They feel more motivated to work towards achieving greater efficiency as they see the results.