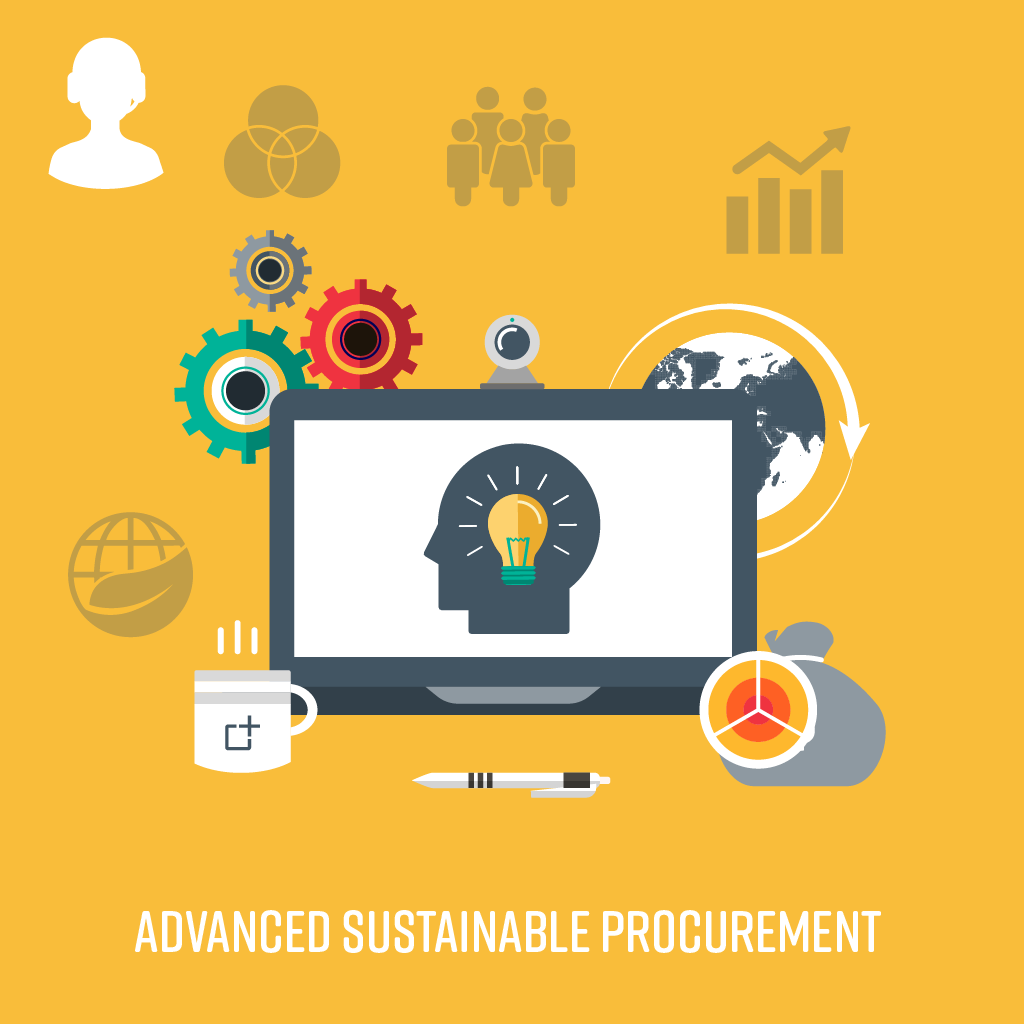
What is supply chain management? It is a cross-functional, multi-functional process that focuses upon the management of all relationships in the supply chain. Supply chain management enhances business performance by improving operations and financial performance. This article will explain the basics of supply chain management, and how it can be used to improve your organization. Let's take a look! What is supply chains management? What is supply chain management? Why is it so important? Here are a few examples of how it can benefit your business.
Management of supply chain relationships is the goal of supply chain management
Companies that produce and sell products need to consider how to obtain raw materials, produce parts, and distribute finished goods. The physical flow of goods begins with a supplier and moves forward through various steps to a manufacturer, distributor, retailer, and finally, the end consumer. While some supply chains skip some steps, the physical goods must still be transported from one place to another, stored for a time and delivered to the customer. This requires organization, planning, and organization.
Successful supply chain management requires integrating all business functions. Vendors and suppliers need to have open communication. Information sharing helps both sides understand each other, reduce costs and improve quality. Collaboration across the supply chain improves communication and collaboration, which in turn benefits both sides. The customer should be informed about the company's processes and the vendor must be prepared to ship emergency materials. When a company sells perishable goods it is especially important to have a lead time.
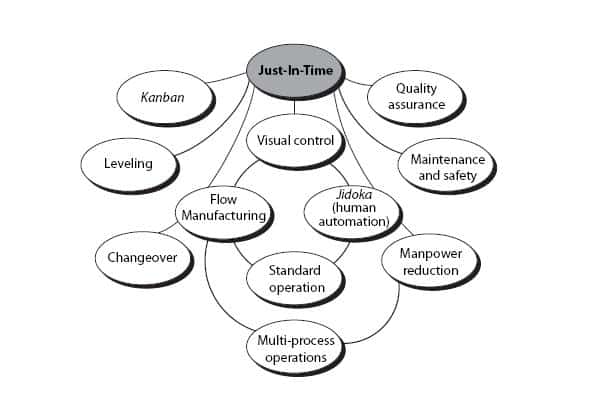
It is a cross-functional business process
When it comes to a company's supply chain, there are many important cross-functional factors that must be considered. In order to ensure a successful supply chain, suppliers must be able to deliver goods on time, which is why it is essential to coordinate with them. Follow these steps to avoid any problems. This will improve efficiency and allow companies to save money.
Management must understand the interdependencies within the supply chain and work towards increasing profitability. While all parties should benefit equally from process improvements, it is important to establish guidelines for how rewards are shared. If the process is not based on a common measurement method, some parties may not be able to see the benefits. If the value is not captured it could be deemed invalid.
It reduces operating and maintenance costs
One of the most effective ways to reduce operating costs is by streamlining your ordering processes. Your employees are less likely to be confused by multiple requisitions and order too much product if you use one software platform. To reduce your operating costs, you can set up approvals to limit the number of goods that you order. A simplified software system will not only eliminate mistakes and confusion, but it will also enable you to keep track of your inventory, order only what you need, and block shipments if they aren't needed.
One way to cut operating costs is to improve the communication between warehouse employees. Start by analyzing the current workflow to identify bottlenecks and improve communication between warehouse employees. If you want to reduce your transportation costs, consider consolidating shipments and using dedicated transportation service providers. This will reduce your operating expenses by a substantial amount. Not only will it reduce transport costs, but it will also allow you to deliver your products faster to customers.
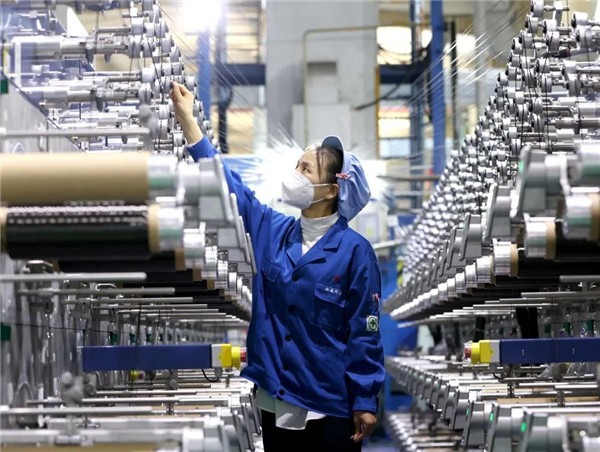
It improves financial position
In many ways, supply chain management can help improve a business’s financial performance. A supply chain manager who is skilled can lower production costs while maximising the benefits from variable costs. The ability to control costs increases profit margins. Improving the cash flow of a company is another major benefit. Customers can be invoiced earlier if products are delivered faster, which reduces the need to buy expensive space. Also, a better supply channel reduces fixed asset costs.
The Statement on Shareholders’ Equity (SSE), which summarizes ownership in a company, is a crucial financial statement. The after-tax cash flow can be increased by about 8.5% by improving a firm's supplier chain. A company can lower its costs up to 10% by improving its supply chain performance and increase customer satisfaction. And when supply chain management improves financial performance, the company can achieve operational efficiencies that result in higher profits.
FAQ
What is the difference between a production planner and a project manager?
The difference between a product planner and project manager is that a planer is typically the one who organizes and plans the entire project. A production planner, however, is mostly involved in the planning stages.
What is production plan?
Production Planning involves developing a plan for all aspects of the production, including scheduling, budgeting, casting, crew, location, equipment, props, etc. This document aims to ensure that everything is planned and ready when you are ready to shoot. You should also have information to ensure the best possible results on set. This includes shooting schedules, locations, cast lists, crew details, and equipment requirements.
The first step is to outline what you want to film. You may have decided where to shoot or even specific locations you want to use. Once you've identified the locations and scenes you want to use, you can begin to plan what elements you need for each scene. One example is if you are unsure of the exact model you want but decide that you require a car. This is where you can look up car models online and narrow down your options by choosing from different makes and models.
After you have chosen the right car, you will be able to begin thinking about accessories. You might need to have people in the front seats. Maybe you need someone to move around in the back. Maybe you want to change the interior color from black to white? These questions will help guide you in determining the ideal look and feel for your car. You can also think about the type of shots you want to get. What type of shots will you choose? Maybe you want to show your engine or the steering wheel. These things will help you to identify the car that you are looking for.
Once you have all the information, you are ready to create a plan. The schedule will show you when to begin shooting and when to stop. Every day will have a time for you to arrive at the location, leave when you are leaving and return home when you are done. Everyone will know what they need and when. If you need to hire extra staff, you can make sure you book them in advance. You should not hire anyone who doesn't show up because of your inaction.
It is important to calculate the amount of filming days when you are creating your schedule. Some projects can be completed in a matter of days or weeks. Others may take several days. While creating your schedule, it is important to remember whether you will require more than one shot per day. Multiplying takes in the same area will result both in increased costs and a longer time. It's better to be safe than sorry and shoot less takes if you're not certain whether you need more takes.
Budget setting is another important aspect in production planning. A realistic budget will help you work within your means. If you have to reduce your budget due to unexpected circumstances, you can always lower it later. It is important to not overestimate how much you will spend. If you underestimate the cost of something, you will have less money left after paying for other items.
Production planning is a very detailed process, but once you understand how everything works together, it becomes easier to plan future projects.
How can I find out more about manufacturing?
Practical experience is the best way of learning about manufacturing. If that is not possible, you could always read books or view educational videos.
Statistics
- It's estimated that 10.8% of the U.S. GDP in 2020 was contributed to manufacturing. (investopedia.com)
- You can multiply the result by 100 to get the total percent of monthly overhead. (investopedia.com)
- In the United States, for example, manufacturing makes up 15% of the economic output. (twi-global.com)
- (2:04) MTO is a production technique wherein products are customized according to customer specifications, and production only starts after an order is received. (oracle.com)
- According to the United Nations Industrial Development Organization (UNIDO), China is the top manufacturer worldwide by 2019 output, producing 28.7% of the total global manufacturing output, followed by the United States, Japan, Germany, and India.[52][53] (en.wikipedia.org)
External Links
How To
How to Use Just-In-Time Production
Just-in time (JIT), is a process that reduces costs and increases efficiency in business operations. It is a process where you get the right amount of resources at the right moment when they are needed. This means that you only pay for what you actually use. Frederick Taylor developed the concept while working as foreman in early 1900s. He observed how workers were paid overtime if there were delays in their work. He then concluded that if he could ensure that workers had enough time to do their job before starting to work, this would improve productivity.
JIT is an acronym that means you need to plan ahead so you don’t waste your money. Look at your entire project, from start to end. Make sure you have enough resources in place to deal with any unexpected problems. You can anticipate problems and have enough equipment and people available to fix them. This will ensure that you don't spend more money on things that aren't necessary.
There are several types of JIT techniques:
-
Demand-driven: This JIT is where you place regular orders for the parts/materials that are needed for your project. This will allow you to track how much material you have left over after using it. This will let you know how long it will be to produce more.
-
Inventory-based: This is a type where you stock the materials required for your projects in advance. This allows one to predict how much they will sell.
-
Project-driven: This method allows you to set aside enough funds for your project. Once you have an idea of how much material you will need, you can purchase the necessary materials.
-
Resource-based: This is the most common form of JIT. You assign certain resources based off demand. For example, if there is a lot of work coming in, you will have more people assigned to them. If there aren't many orders, you will assign fewer people.
-
Cost-based: This is similar to resource-based, except that here you're not just concerned about how many people you have but how much each person costs.
-
Price-based: This is very similar to cost-based, except that instead of looking at how much each individual worker costs, you look at the overall price of the company.
-
Material-based is an alternative to cost-based. Instead of looking at the total cost in the company, this method focuses on the average amount of raw materials that you consume.
-
Time-based: This is another variation of resource-based JIT. Instead of focusing only on how much each employee is costing, you should focus on how long it takes to complete your project.
-
Quality-based JIT: This is another variation of resource based JIT. Instead of thinking about how much each employee costs or how long it takes to manufacture something, you think about how good the quality of your product is.
-
Value-based JIT: One of the most recent forms of JIT. In this scenario, you're not concerned about how products perform or whether customers expect them to meet their expectations. Instead, your focus is on the value you bring to the market.
-
Stock-based: This inventory-based approach focuses on how many items are being produced at any one time. This method is useful when you want to increase production while decreasing inventory.
-
Just-intime (JIT), planning is a combination JIT management and supply chain management. It refers to the process of scheduling the delivery of components as soon as they are ordered. It reduces lead times and improves throughput.