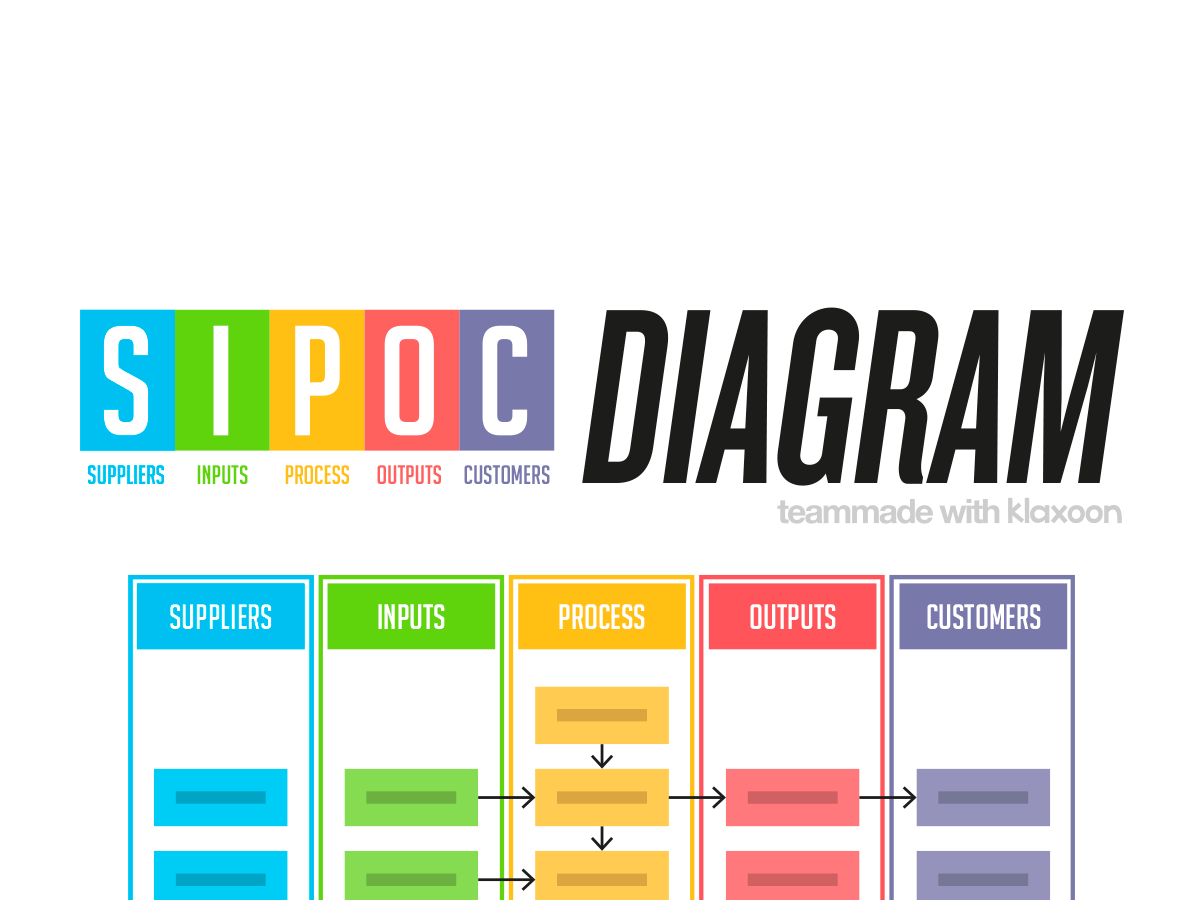
To ensure your business succeeds, it is crucial to manage your supply chains. The goal is to improve the efficiency of your processes, reduce costs, and improve customer satisfaction. These benefits are not the only ones. Managing your supply chain can help you increase revenue and give you a competitive edge in the market. Eight of ten companies have higher revenue growth than the industry average because they have a strong supply chains management program.
It is important to keep track and monitor the status of your inventory in order manage your supply chains. You also need to know the availability of your products, the prices of your products, and the lead time of your products.
The supply chain is a network of interdependent people, companies, technologies, and resources that works together to produce and transport goods and services. This network enables organizations to produce and deliver goods faster, better, and more efficiently. It also reduces production costs and increases purchasing efficiency. It is vital for the production and delivery health care products, electronics, as well as other goods used in daily life.
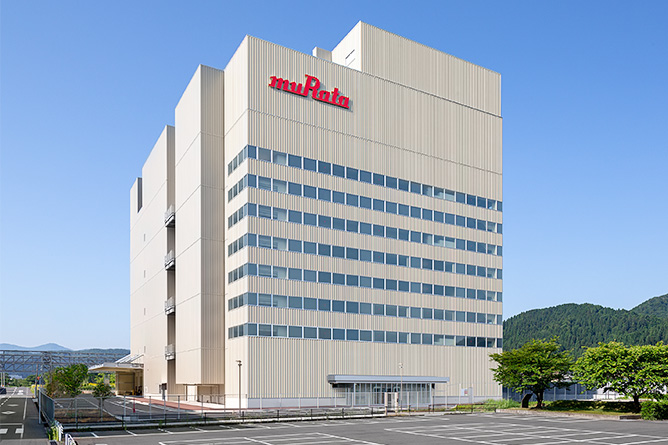
Supply chain management involves the planning and execution of the processes that transport goods from their raw materials to the final consumer. It involves coordination of many different activities such as sales, marketing, production, and distribution. It also includes a system of managing returns for defective products.
Supply chain complexity rises as global competition grows. Part price fluctuations, offshoring and talent attrition all contribute to this increase in complexity. In addition, your organization may have multiple suppliers, which can add redundancy to your supply chain.
Supply chain management is a complex process that involves many departments in your organization. These include finance, sales and operations.
In order to manage your supply network effectively, you must be skilled in all five elements. These include the design of a supply chain plan, the selection and management suppliers, the management supplier relationships, inventory management and coordination.
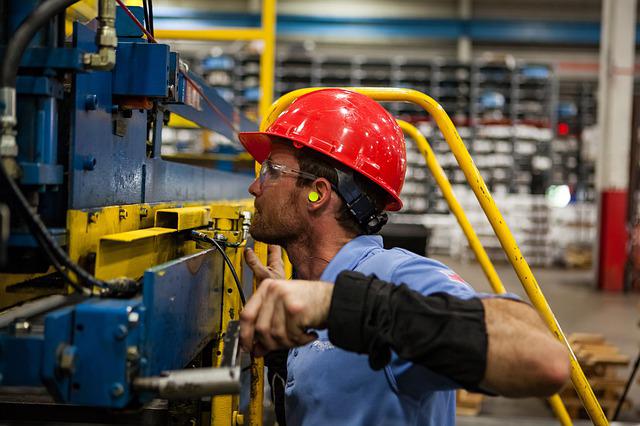
When designing your supply-chain plan, you must create a detailed plan. It will outline how your organization will implement that strategy. It also provides a breakdown on the steps required to achieve the plan. You might decide to outsource manufacturing. This includes packaging and distribution. You might also have to inspect finished products and collect payments from your customers.
Management of supplier relationships should be considered when creating your supply chain strategy. You might choose to work with vendors who have a track record of delivering products on time. You might also prefer a vendor that is flexible to allow you to obtain emergency materials when necessary.
You can also reduce the wear and tear of your equipment by managing your supply chain. It can help you stay in touch with your customers and reduce quality issues.
FAQ
How can we improve manufacturing efficiency?
First, determine which factors have the greatest impact on production time. The next step is to identify the most important factors that affect production time. You can start by identifying the most important factors that impact production time. Once you identify them, look for solutions.
What skills should a production planner have?
To become a successful production planner, you need to be organized, flexible, and able to multitask. It is also important to be able communicate with colleagues and clients.
Are there ways to automate parts of manufacturing?
Yes! Yes. Automation has been around since ancient time. The Egyptians invent the wheel thousands of year ago. Robots are now used to assist us in assembly lines.
Actually, robotics can be used in manufacturing for many purposes. These include:
-
Automated assembly line robots
-
Robot welding
-
Robot painting
-
Robotics inspection
-
Robots that make products
Automation can be applied to manufacturing in many other ways. 3D printing is a way to make custom products quickly and without waiting weeks or months for them to be manufactured.
Statistics
- Job #1 is delivering the ordered product according to specifications: color, size, brand, and quantity. (netsuite.com)
- Many factories witnessed a 30% increase in output due to the shift to electric motors. (en.wikipedia.org)
- (2:04) MTO is a production technique wherein products are customized according to customer specifications, and production only starts after an order is received. (oracle.com)
- According to the United Nations Industrial Development Organization (UNIDO), China is the top manufacturer worldwide by 2019 output, producing 28.7% of the total global manufacturing output, followed by the United States, Japan, Germany, and India.[52][53] (en.wikipedia.org)
- It's estimated that 10.8% of the U.S. GDP in 2020 was contributed to manufacturing. (investopedia.com)
External Links
How To
How to Use the Just In Time Method in Production
Just-intime (JIT), which is a method to minimize costs and maximize efficiency in business process, is one way. This is where you have the right resources at the right time. This means that you only pay for what you actually use. Frederick Taylor first coined this term while working in the early 1900s as a foreman. After observing how workers were paid overtime for late work, he realized that overtime was a common practice. He realized that workers should have enough time to complete their jobs before they begin work. This would help increase productivity.
JIT is a way to plan ahead and make sure you don't waste any money. It is important to look at your entire project from beginning to end and ensure that you have enough resources to handle any issues that may arise. You'll be prepared to handle any potential problems if you know in advance. This way, you won't end up paying extra money for things that weren't really necessary.
There are several types of JIT techniques:
-
Demand-driven JIT: This is a JIT that allows you to regularly order the parts/materials necessary for your project. This will allow you to track how much material you have left over after using it. You'll also be able to estimate how long it will take to produce more.
-
Inventory-based : You can stock the materials you need in advance. This allows you predict the amount you can expect to sell.
-
Project-driven: This is an approach where you set aside enough funds to cover the cost of your project. If you know the amount you require, you can buy the materials you need.
-
Resource-based: This is the most common form of JIT. This is where you assign resources based upon demand. If you have many orders, you will assign more people to manage them. If you don’t have many orders you will assign less people to the work.
-
Cost-based : This is similar in concept to resource-based. But here, you aren't concerned about how many people your company has but how much each individual costs.
-
Price-based: This is a variant of cost-based. However, instead of focusing on the individual workers' costs, this looks at the total price of the company.
-
Material-based - This is a variant of cost-based. But instead of looking at the total company cost, you focus on how much raw material you spend per year.
-
Time-based JIT: This is another variant of resource-based JIT. Instead of worrying about how much each worker costs, you can focus on how long the project takes.
-
Quality-based JIT: Another variation on resource-based JIT. Instead of thinking about how much each employee costs or how long it takes to manufacture something, you think about how good the quality of your product is.
-
Value-based JIT : This is the newest type of JIT. In this scenario, you're not concerned about how products perform or whether customers expect them to meet their expectations. Instead, you are focused on adding value to the marketplace.
-
Stock-based. This method is inventory-based and focuses only on the actual production at any given point. This is used to increase production and minimize inventory.
-
Just-intime planning (JIT), is a combination JIT/sales chain management. This refers to the scheduling of the delivery of components as soon after they are ordered. It reduces lead times and improves throughput.