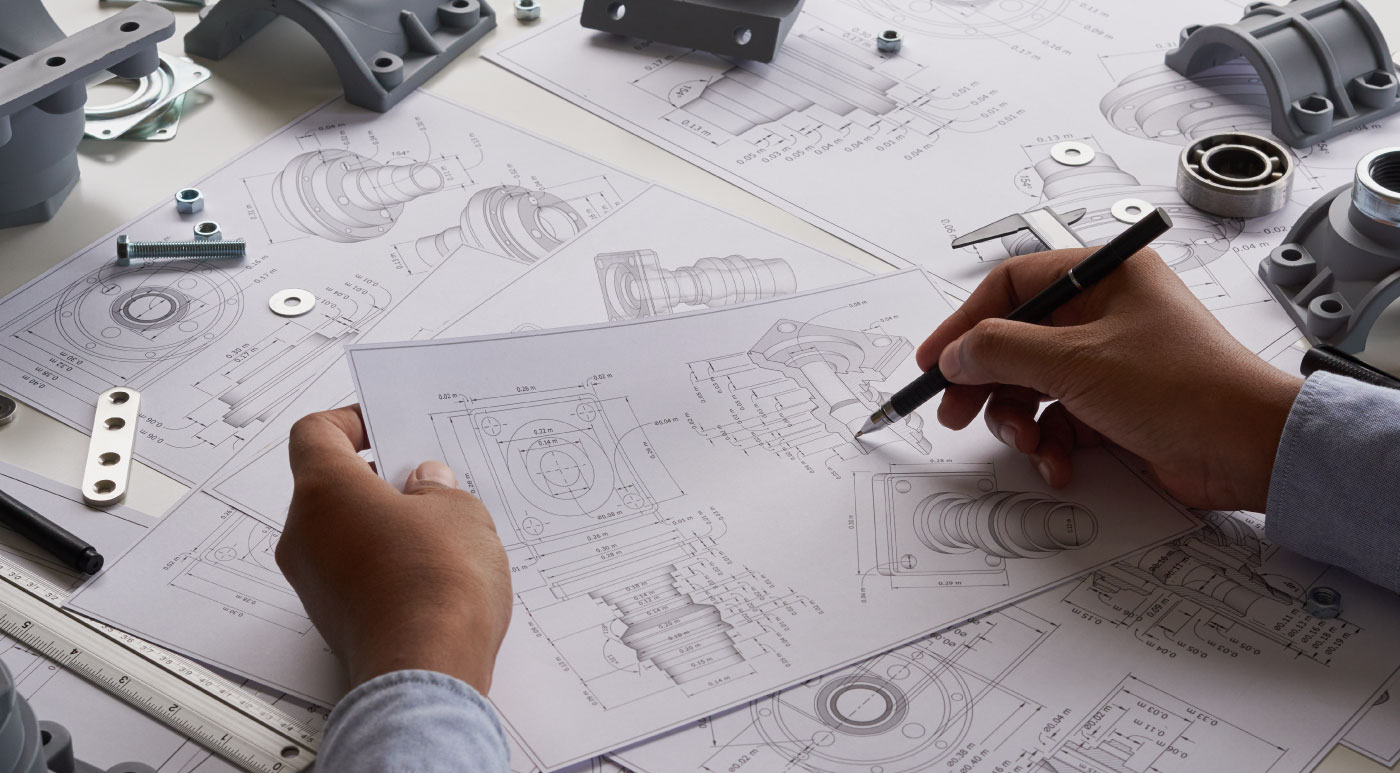
Heijunka was first developed by Toyota Japan to improve efficiency in multi-step production. It reduces the amount of waste in the production process by ensuring that the production schedule is consistent with customer demand. The production schedule is consistent with customer demand, which reduces waste. Heijunka aids manufacturers to satisfy customer demands and increase their profits.
Heijunka refers to the coordination of small production batches across multiple manufacturing lines. It helps to increase efficiency in multi-step production, especially when justin-time principles are applied. It is also part of Toyota Production System. It reduces waste by leveling production and mixing products. Also, it minimizes batch sizes.
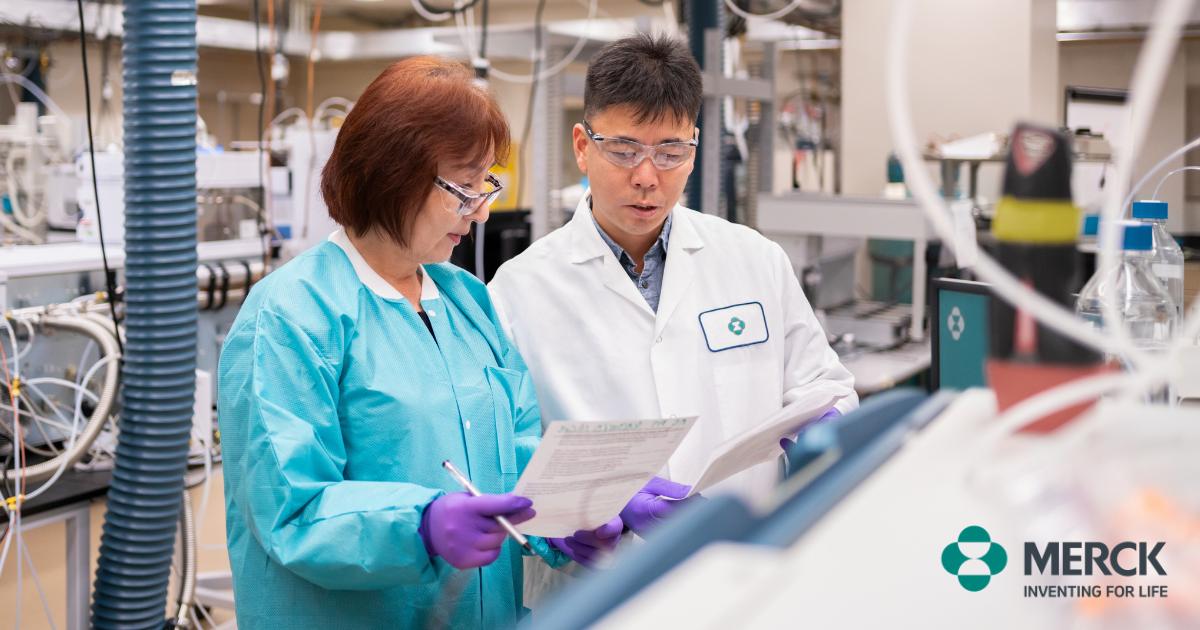
There are two ways you can implement Heijunka. One option is the use a "heijunka" box. This is a grid of small boxes which are mounted or fixed to a wall. It allows production personnel visualize the production process and schedules them. Magnetic cards can also be used to implement Heijunka.
Toyota dealers use Heijunka to increase their changeover time. It is also a key method of Toyota's Lean framework. Heijunka is a way for manufacturers to increase their production and reduce their inventory. Heijunka allows for better utilization of equipment and labor. It facilitates a lean production system, which reduces waste. Customers will receive better products because of it.
You must be able to understand the takt time (also known as the customer purchasing rate) before you can use heijunka. This is how long it takes to make a product that meets customer demand. Heijunka uses the time to decide the production pace. The takt time can be used to determine how much product you need to produce and how fast customers will purchase your products. The takt time is also used in back office settings to help determine the pace at which customers buy the company's products.
Production staff can visually plan and schedule their production using the heijunka boxes. The heijunka container can also be used on the shop floor to visualize production processes. The heijunka box is made up of rows and columns which represent each product type or component. The columns of boxes represent the different time periods, and the rows are for each product type.
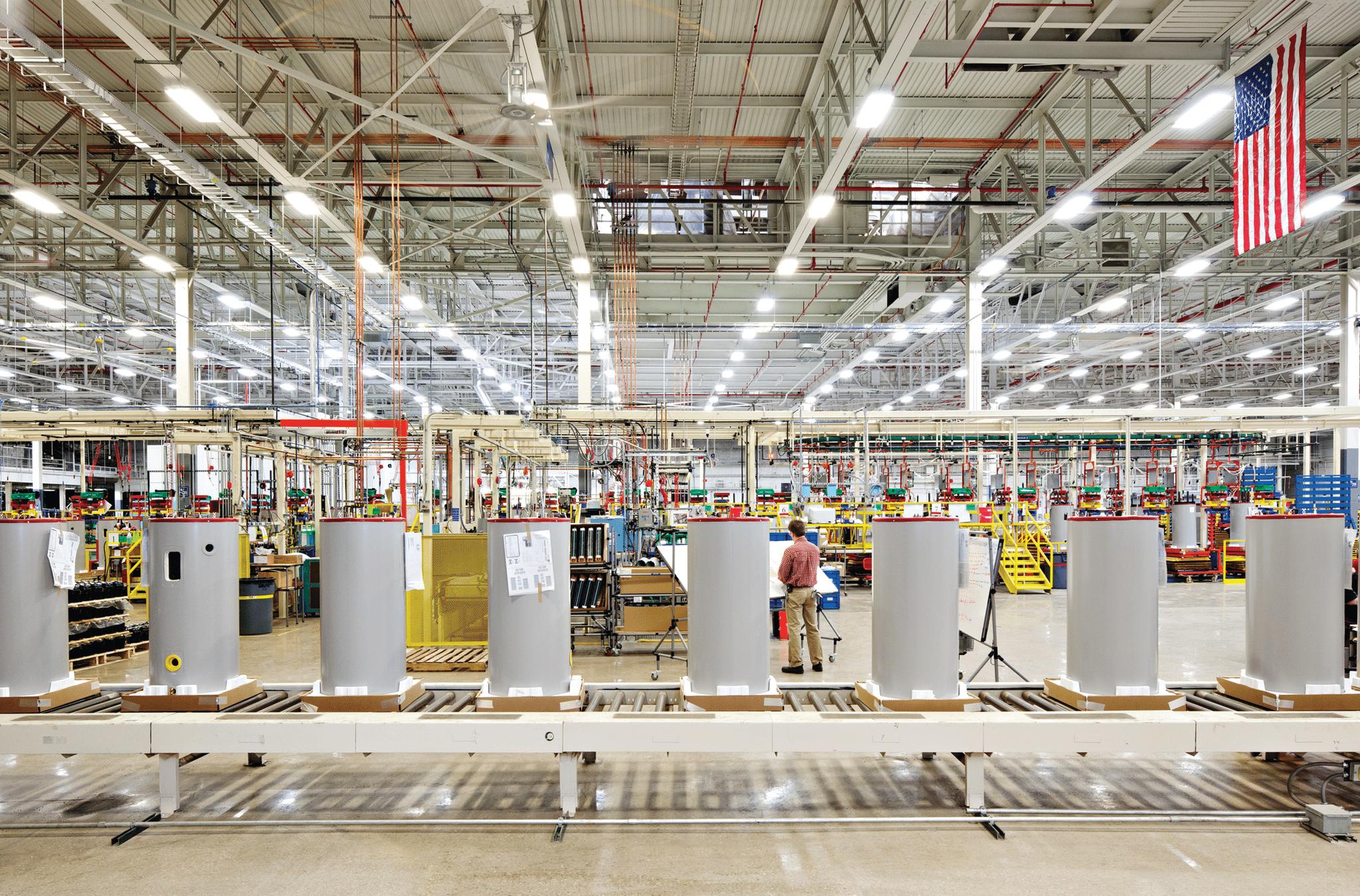
Heijunka Box, one of the most popular visual management tools in production, is also a common tool. This tool shows the relationships between component, product and production. This tool provides visual representations of the production workload for each week. It is used in conjunction with kanban cards, which are colored cards that represent the amount of product required for a specific production step. Kanban cards are typically taken from the heijunka at a specific time and delivered to the relevant production area.
FAQ
What does it take to run a logistics business?
A successful logistics business requires a lot more than just knowledge. Good communication skills are essential to effectively communicate with your suppliers and clients. It is important to be able to analyse data and draw conclusions. You must be able to work well under pressure and handle stressful situations. To improve efficiency, you must be innovative and creative. To motivate and guide your team towards reaching organizational goals, you must have strong leadership skills.
You must be organized to meet tight deadlines.
Why automate your warehouse
Modern warehouses have become more dependent on automation. Increased demand for efficient and faster delivery has resulted in a rise in e-commerce.
Warehouses need to adapt quickly to meet changing needs. In order to do this, they need to invest in technology. Automation warehouses can bring many benefits. Here are some of the reasons automation is worth your investment:
-
Increases throughput/productivity
-
Reduces errors
-
Improves accuracy
-
Safety increases
-
Eliminates bottlenecks
-
Allows companies to scale more easily
-
This makes workers more productive
-
Gives you visibility into all that is happening in your warehouse
-
Enhances customer experience
-
Improves employee satisfaction
-
This reduces downtime while increasing uptime
-
High quality products delivered on-time
-
Removing human error
-
This helps to ensure compliance with regulations
Can some manufacturing processes be automated?
Yes! Since ancient times, automation has been in existence. The Egyptians discovered the wheel thousands and years ago. Today, robots assist in the assembly of lines.
Actually, robotics can be used in manufacturing for many purposes. These include:
-
Robots for assembly line
-
Robot welding
-
Robot painting
-
Robotics inspection
-
Robots that produce products
Automation could also be used to improve manufacturing. 3D printing, for example, allows us to create custom products without waiting for them to be made.
What skills is required for a production planner?
You must be flexible and organized to become a productive production planner. Communication skills are essential to ensure that you can communicate effectively with clients, colleagues, and customers.
What is the role and responsibility of a Production Planner?
Production planners ensure all aspects of the project are delivered within time and budget. They also ensure the quality of the product and service meets the client's requirements.
What is manufacturing and logistics?
Manufacturing refers to the process of making goods using raw materials and machines. Logistics manages all aspects of the supply chain, including procurement, production planning and distribution, inventory control, transportation, customer service, and transport. Logistics and manufacturing are often referred to as one thing. It encompasses both the creation of products and their delivery to customers.
What is the importance of automation in manufacturing?
Not only are service providers and manufacturers important, but so is automation. It enables them to provide services faster and more efficiently. It reduces human errors and improves productivity, which in turn helps them lower their costs.
Statistics
- Job #1 is delivering the ordered product according to specifications: color, size, brand, and quantity. (netsuite.com)
- [54][55] These are the top 50 countries by the total value of manufacturing output in US dollars for its noted year according to World Bank.[56] (en.wikipedia.org)
- In 2021, an estimated 12.1 million Americans work in the manufacturing sector.6 (investopedia.com)
- (2:04) MTO is a production technique wherein products are customized according to customer specifications, and production only starts after an order is received. (oracle.com)
- It's estimated that 10.8% of the U.S. GDP in 2020 was contributed to manufacturing. (investopedia.com)
External Links
How To
How to Use the 5S to Increase Productivity In Manufacturing
5S stands as "Sort", Set In Order", Standardize", Separate" and "Store". Toyota Motor Corporation was the first to develop the 5S approach in 1954. It helps companies achieve higher levels of efficiency by improving their work environment.
This method has the basic goal of standardizing production processes to make them repeatable. It means tasks like cleaning, sorting or packing, labeling, and storing are done every day. This knowledge allows workers to be more efficient in their work because they are aware of what to expect.
Implementing 5S involves five steps: Sort, Set in Order, Standardize Separate, Store, and Each step involves a different action which leads to increased efficiency. If you sort items, it makes them easier to find later. When you arrange items, you place them together. After you have divided your inventory into groups you can store them in easy-to-reach containers. You can also label your containers to ensure everything is properly labeled.
Employees must be able to critically examine their work practices. Employees should understand why they do the tasks they do, and then decide if there are better ways to accomplish them. To implement the 5S system, employees must acquire new skills and techniques.
The 5S Method not only improves efficiency, but it also helps employees to be more productive and happier. They feel more motivated to work towards achieving greater efficiency as they see the results.