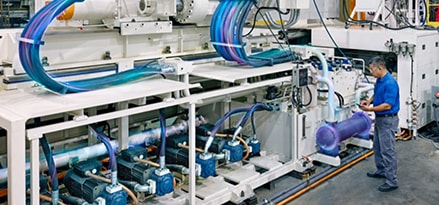
They are responsible for all aspects of purchasing, including sourcing and coordination. They interact with suppliers, vendors, and other purchasing agents. They need to be familiar with the company's buying process and how they can improve it. They should also be able negotiate the best deals on behalf of the company.
A purchasing manager also needs to have accurate and current records regarding purchases. They evaluate the price trends, analyze financial reports, and analyze customer needs. They also coordinate purchasing activities with other departments. They might be required to work extra hours if supplies are needed from overseas markets.
Purchasing managers also coordinate and manage inventory and logistics. They make decisions about the best way to purchase products and ensure they meet company quality standards. They coordinate with staff to manage their budgets and ensure that purchases are made at the lowest possible price. They also work to find the best vendors and negotiate contracts.
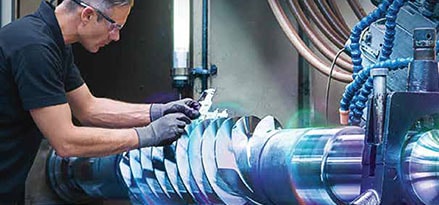
All purchasing employees are monitored and managed by Purchasing Managers. They also evaluate the quality of goods purchased, their speed of delivery and how much they cost. They also contact sellers and suppliers and visit their distribution centers. They also check that suppliers are adhering to the terms of the contract. They may also have responsibility for team building and disciplinary issues.
Purchasing Managers must have excellent communication skills, analytical abilities, and strategic thinking skills. They need to be able analyse the effects of various products on the company. They must be able manage suppliers and their relationships. They should also be able take business decisions and increase sales. They should also be able handle complex purchases. They must be able assess new vendors, evaluate their capabilities and determine the best vendor for the company.
Most purchasing managers have to have a bachelor's degree in business or a related field. It is helpful to have some experience in supply chain management and inventory management. They will also need to be proficient in Microsoft Office as well as other programs.
The best purchasing managers should be able find the best deals and negotiate favorable contracts. They should also have the ability to coordinate all purchasing activities. Manage inventories and track vendor and supplier performance. They should also be capable of managing a team consisting of purchasing agents.
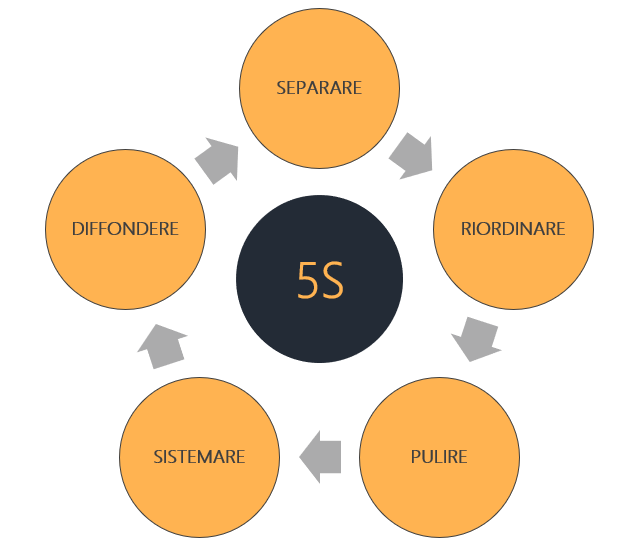
The purchase manager job description should also be able to mention how purchasing is essential to the company's success. It should also mention how important it is for the company to stay ahead of the curve. It should also mention how the company values its employees' work-life balance. It should include a call for action to encourage applicants.
Sometimes, the Purchasing Manager may be required to work overtime in order to purchase equipment and materials for an international marketplace. They may also have to deal with vendors and sellers and attend trade shows.
FAQ
What is the responsibility of a production planner?
A production planner ensures all aspects of the project are delivered on time, within budget, and within scope. They also ensure that the product/service meets the client’s needs.
What is the difference between Production Planning and Scheduling?
Production Planning (PP) refers to the process of determining how much production is needed at any given moment. This is done through forecasting demand and identifying production capacities.
Scheduling is the process that assigns dates to tasks so they can get completed within a given timeframe.
What are the 7 Rs of logistics management?
The 7R's of Logistics is an acronym for the seven basic principles of logistics management. It was developed by International Association of Business Logisticians (IABL), and published as part of their "Seven Principles of Logistics Management Series" in 2004.
The acronym is composed of the following letters.
-
Responsive - ensure all actions are legal and not harmful to others.
-
Reliable - have confidence in the ability to deliver on commitments made.
-
Be responsible - Use resources efficiently and avoid wasting them.
-
Realistic - Take into consideration all aspects of operations including cost-effectiveness, environmental impact, and other factors.
-
Respectful: Treat others with fairness and equity
-
You are resourceful and look for ways to save money while increasing productivity.
-
Recognizable - provide customers with value-added services.
How can manufacturing reduce production bottlenecks?
Production bottlenecks can be avoided by ensuring that processes are running smoothly during the entire production process, starting with the receipt of an order and ending when the product ships.
This includes planning for capacity requirements as well as quality control measures.
Continuous improvement techniques like Six Sigma are the best way to achieve this.
Six Sigma management is a system that improves quality and reduces waste within your organization.
It's all about eliminating variation and creating consistency in work.
What are the requirements to start a logistics business?
To run a successful logistics company, you need a lot knowledge and skills. For clients and suppliers to be successful, you need to have excellent communication skills. You should be able analyse data and draw inferences. You will need to be able handle pressure well and work in stressful situations. You must be creative and innovative to develop new ideas to improve efficiency. You must be a strong leader to motivate others and direct them to achieve organizational goals.
It is important to be organized and efficient in order to meet tight deadlines.
What does manufacturing mean?
Manufacturing Industries are companies that manufacture products. The people who buy these products are called consumers. This is accomplished by using a variety of processes, including production, distribution and retailing. They produce goods from raw materials by using machines and other machinery. This covers all types of manufactured goods including clothing, food, building supplies and furniture, as well as electronics, tools, machinery, vehicles and pharmaceuticals.
Is there anything we should know about Manufacturing Processes prior to learning about Logistics.
No. No. Knowing about manufacturing processes will help you understand how logistics works.
Statistics
- (2:04) MTO is a production technique wherein products are customized according to customer specifications, and production only starts after an order is received. (oracle.com)
- According to a Statista study, U.S. businesses spent $1.63 trillion on logistics in 2019, moving goods from origin to end user through various supply chain network segments. (netsuite.com)
- Job #1 is delivering the ordered product according to specifications: color, size, brand, and quantity. (netsuite.com)
- [54][55] These are the top 50 countries by the total value of manufacturing output in US dollars for its noted year according to World Bank.[56] (en.wikipedia.org)
- In the United States, for example, manufacturing makes up 15% of the economic output. (twi-global.com)
External Links
How To
How to use the Just In-Time Production Method
Just-intime (JIT), which is a method to minimize costs and maximize efficiency in business process, is one way. It is a process where you get the right amount of resources at the right moment when they are needed. This means you only pay what you use. Frederick Taylor first coined this term while working in the early 1900s as a foreman. He observed how workers were paid overtime if there were delays in their work. He concluded that if workers were given enough time before they start work, productivity would increase.
The idea behind JIT is that you should plan ahead and have everything ready so you don't waste money. You should also look at the entire project from start to finish and make sure that you have sufficient resources available to deal with any problems that arise during the course of your project. You will have the resources and people to solve any problems you anticipate. You won't have to pay more for unnecessary items.
There are many JIT methods.
-
Demand-driven JIT: You order the parts and materials you need for your project every other day. This will allow you to track how much material you have left over after using it. This will allow to you estimate the time it will take for more to be produced.
-
Inventory-based: This is a type where you stock the materials required for your projects in advance. This allows for you to anticipate how much you can sell.
-
Project-driven : This is a method where you make sure that enough money is set aside to pay the project's cost. You will be able to purchase the right amount of materials if you know what you need.
-
Resource-based JIT : This is probably the most popular type of JIT. Here you can allocate certain resources based purely on demand. If you have many orders, you will assign more people to manage them. You'll have fewer orders if you have fewer.
-
Cost-based: This approach is very similar to resource-based. However, you don't just care about the number of people you have; you also need to consider how much each person will cost.
-
Price-based: This is similar to cost-based but instead of looking at individual workers' salaries, you look at the total company price.
-
Material-based: This is quite similar to cost-based, but instead of looking at the total cost of the company, you're concerned with how much raw materials you spend on average.
-
Time-based: Another variation of resource-based JIT. Instead of focusing on how much each employee costs, you focus on how long it takes to complete the project.
-
Quality-based: This is yet another variation of resource-based JIT. Instead of thinking about the cost of each employee or the time it takes to produce something, you focus on how good your product quality.
-
Value-based: This is one of the newest forms of JIT. In this instance, you are not concerned about the product's performance or meeting customer expectations. Instead, you are focused on adding value to the marketplace.
-
Stock-based: This stock-based method focuses on the actual quantity of products being made at any given time. This is used to increase production and minimize inventory.
-
Just-intime (JIT), planning is a combination JIT management and supply chain management. It refers to the process of scheduling the delivery of components as soon as they are ordered. This is important as it reduces lead time and increases throughput.