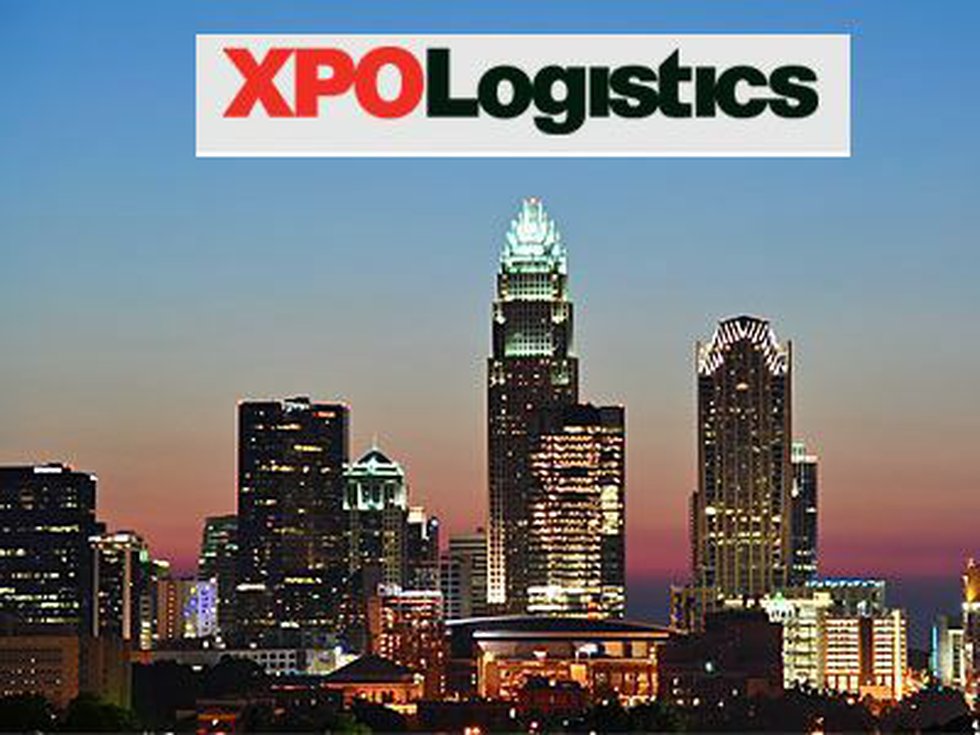
Part-time and full-time logistics jobs in federal and state governments are available. There are many advantages to working in these jobs. These include stable income, good benefits, and good income. The government can be a great place to get experience in this industry.
For example, a Logistics Management Specialist is responsible for managing the supply chain. They monitor deliveries, manage contracts and perform audits. They also work to identify deficiencies in supply chains and develop contingency plans. This position requires communication skills, typing abilities, and knowledge regarding government procurement regulations.
Supply Chain Management officers can work for the Department of Veterans Affairs as well as the Department of Homeland Security. The first role requires an understanding of federal procurement regulations. In the second, the position requires management of logistics operations and sourcing materials. Candidates need to have a bachelor’s degree or above depending on the job. Candidates must have a good understanding of the business culture and regulations in the state where they will be applying. Some positions require security clearances. Candidates may need to pass a background screening.
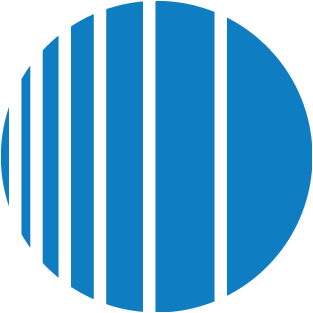
Other tasks for government logistics professionals include quickly deploying materials after an incident. A distribution role in disaster logistics is offered by the North Carolina Department of Public Safety. Candidates should have at least four years of relevant experience. Candidats must have the ability to work in stressful conditions, as the position requires them to manage personnel.
Logistics Management Specialists are also needed at the departmental level. The role of a logistics specialist closely mirrors that of Federal Aviation Administration. Qualifications include an advanced degree, specialized experience in operations or project management, and a background in logistics management.
If you're interested in a career as a government logistics coordinator, you'll need to know how to manage a large volume of international travel. You'll also need to have a background in managing procurement negotiations and making supplier bids. Candidates should have at least two years' relevant experience.
There are also a variety of other supply chain management roles that you can apply for in the federal government. These are positions in air, road, warehousing and distribution. The federal government offers nearly 25% of these jobs, while the states offer an additional 8%.
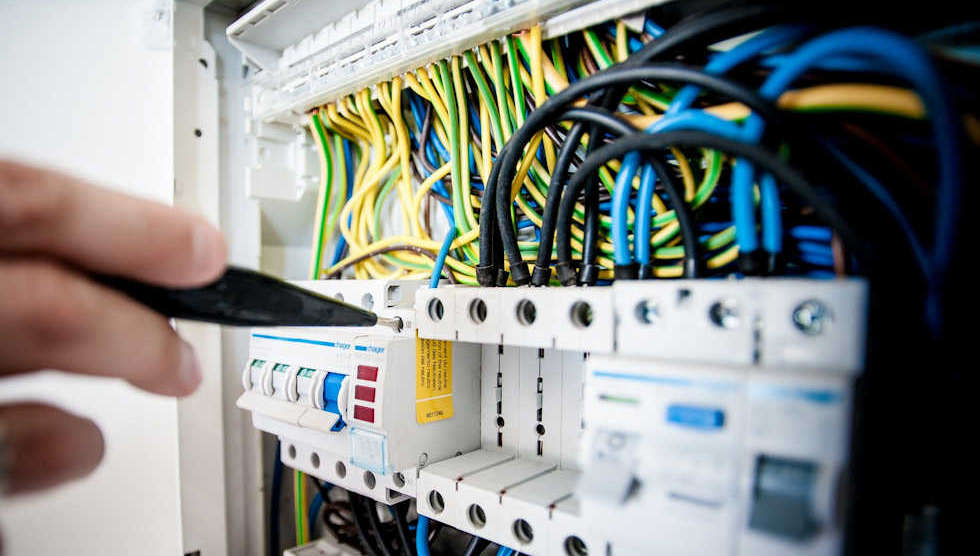
Browse the USAJOBS website to discover many opportunities for employment. You can also search by degree type and title. These positions usually require at least a bachelor’s degree. However, some may require a master’s. Smaller organizations also have supply chain specialists jobs. Supply chain professionals typically need to have at least one year of experience before they can apply.
Data scientists can choose from a variety of positions. Data Scientists assist with the development of strategic plans as well as supporting government programs.
FAQ
How does manufacturing avoid bottlenecks in production?
You can avoid bottlenecks in production by making sure that everything runs smoothly throughout the production cycle, from the moment you receive an order to the moment the product is shipped.
This includes planning for both capacity requirements and quality control measures.
Continuous improvement techniques such Six Sigma are the best method to accomplish this.
Six Sigma management is a system that improves quality and reduces waste within your organization.
It emphasizes consistency and eliminating variance in your work.
Why automate your warehouse
Modern warehousing has seen automation take center stage. E-commerce has increased the demand for quicker delivery times and more efficient processes.
Warehouses must adapt quickly to meet changing customer needs. In order to do this, they need to invest in technology. Automating warehouses is a great way to save money. Here are some of the reasons automation is worth your investment:
-
Increases throughput/productivity
-
Reduces errors
-
Increases accuracy
-
Safety is boosted
-
Eliminates bottlenecks
-
Allows companies to scale more easily
-
Makes workers more efficient
-
Provides visibility into everything that happens in the warehouse
-
Enhances customer experience
-
Improves employee satisfaction
-
This reduces downtime while increasing uptime
-
Ensures quality products are delivered on time
-
Eliminates human error
-
This helps to ensure compliance with regulations
How can we increase manufacturing efficiency?
First, identify the factors that affect production time. We must then find ways that we can improve these factors. If you don't know where to start, then think about which factor(s) have the biggest impact on production time. Once you've identified them all, find solutions to each one.
What is the role of a manager in manufacturing?
The manufacturing manager should ensure that every manufacturing process is efficient and effective. They must also be alert to any potential problems and take appropriate action.
They should also be able communicate with other departments, such as sales or marketing.
They should also be knowledgeable about the latest trends in the industry so they can use this information for productivity and efficiency improvements.
What does warehouse refer to?
Warehouses and storage facilities are where goods are kept before being sold. It can be an indoor space or an outdoor area. It may also be an indoor space or an outdoor area.
Statistics
- (2:04) MTO is a production technique wherein products are customized according to customer specifications, and production only starts after an order is received. (oracle.com)
- Many factories witnessed a 30% increase in output due to the shift to electric motors. (en.wikipedia.org)
- It's estimated that 10.8% of the U.S. GDP in 2020 was contributed to manufacturing. (investopedia.com)
- According to the United Nations Industrial Development Organization (UNIDO), China is the top manufacturer worldwide by 2019 output, producing 28.7% of the total global manufacturing output, followed by the United States, Japan, Germany, and India.[52][53] (en.wikipedia.org)
- In the United States, for example, manufacturing makes up 15% of the economic output. (twi-global.com)
External Links
How To
Six Sigma and Manufacturing
Six Sigma is "the application statistical process control (SPC), techniques for continuous improvement." It was developed by Motorola's Quality Improvement Department at their plant in Tokyo, Japan, in 1986. Six Sigma's main goal is to improve process quality by standardizing processes and eliminating defects. Since there are no perfect products, or services, this approach has been adopted by many companies over the years. The main goal of Six Sigma is to reduce variation from the mean value of production. This means that you can take a sample from your product and then compare its performance to the average to find out how often the process differs from the norm. If there is a significant deviation from the norm, you will know that something needs to change.
Understanding the dynamics of variability within your business is the first step in Six Sigma. Once you've understood that, you'll want to identify sources of variation. Also, you will need to identify the sources of variation. Random variations are caused when people make mistakes. While systematic variations are caused outside of the process, they can occur. These are, for instance, random variations that occur when widgets are made and some fall off the production line. It would be considered a systematic problem if every widget that you build falls apart at the same location each time.
Once you identify the problem areas, it is time to create solutions. You might need to change the way you work or completely redesign the process. Once you have implemented the changes, it is important to test them again to ensure they work. If they don’t work, you’ll need to go back and rework the plan.