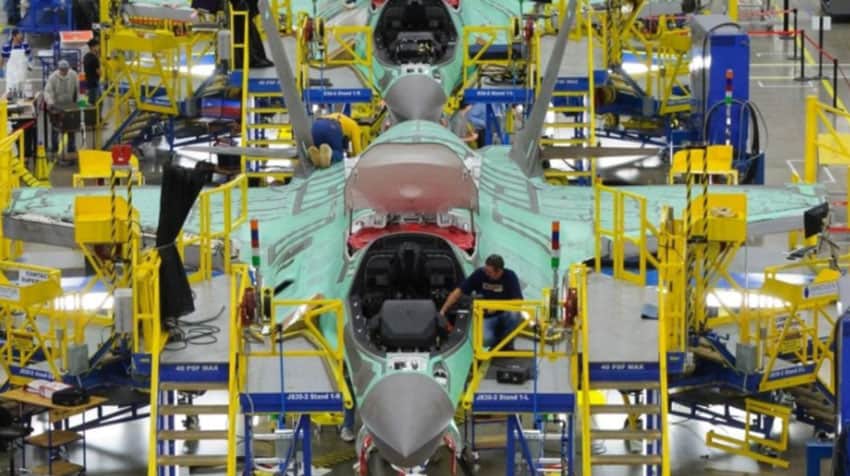
Supply chain management software will help you improve your efficiency and streamline your processes, no matter if you work for a large corporation or small business. These systems can give you a central view to your entire supply network, allowing for planning production, shipment planning, as well as delivery routes. These systems allow you to automate and streamline your processes, allowing your employees to concentrate on other aspects of the business. Every organization that manages shipping and manufacturing is going to need supply chain management software.
You should consider several capabilities and features when choosing the right supply chain management software. These include scalability, ease of use, and integration with other apps. It is also important to evaluate the reputation of the provider as well as the features available. Additionally, it is important to find a solution within your budget. No matter if you're looking for a SaaS service or a full-service package, be flexible to meet your evolving needs.
E2open Software is a top provider of supply chain management solutions. They specialize in cloud-based software that delivers better demand forecasting. The company also offers advanced features and a technology platform. This software is suitable for companies in various industries such as retail, transportation, manufacturing.
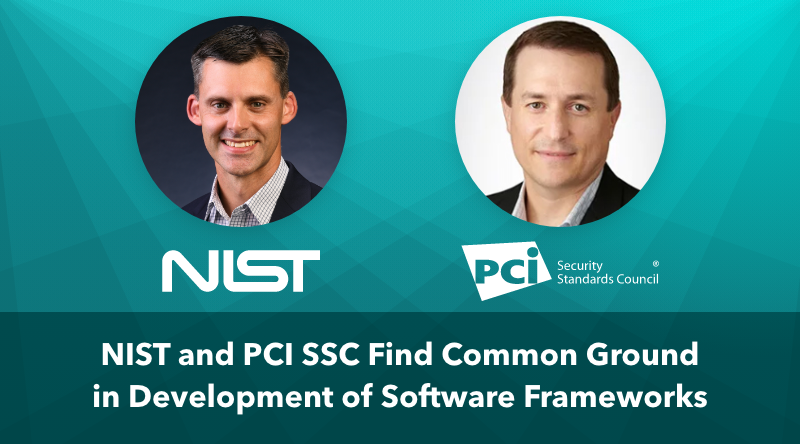
Real-time visibility is a key feature in supply chain management software. This helps you monitor your inventory, as well as shipments, to keep track of your products. It helps you ensure that your customers have what they need when they need it. It helps you to develop long-term strategies that manage demand-supply balancing.
Kinaxis provides a comprehensive supply-chain management software solution. It breaks down silos to streamline processes. It combines machine and human intelligence to help you make better business decisions. It can also assist you in planning inventory and capacity so that you can better react to opportunities.
The sales forecasting software helps you better understand past sales, sales cycles and seasonality. It also uses machine-learning to help you predict sales. This software predicts sales and helps to prepare sales teams for the future. This software also allows you to access data from many sources, making it easier to view the entire picture of your operation.
Descartes Systems Group is the largest competitor in supply-chain management software. They are the most preferred vendor for many organizations. The company boasts over 13,000 users and competes with SAP SCM and Megaventory as well as JDA and Logility.
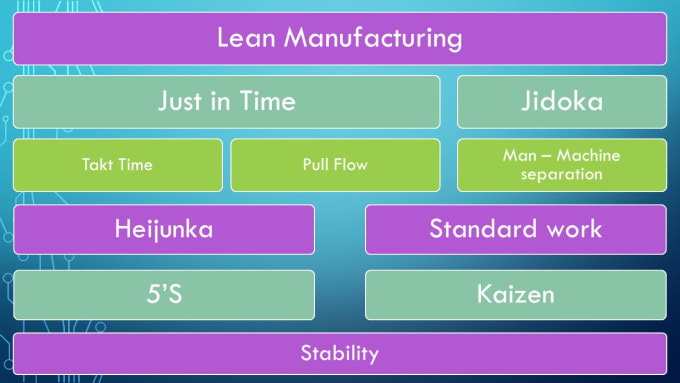
Manhattan Associates is another major competitor in supply chain management software. Manhattan Associates, which has around $617.5 Million in annual revenue, is another software company that has thousands of users. It is currently run by Eddie Capel. This company competes with JDA, Logility and Infor SCM.
Infor SCM is a top-rated supply chain management platform. It is ideal for all types of businesses, and it is one the most popular supply chain management tools. It's a cloud-based application that unifies all enterprise processes. It also includes analytics at the core, which can help you optimize your end-to-end supply chain.
FAQ
What are the four types of manufacturing?
Manufacturing is the process of transforming raw materials into useful products using machines and processes. Manufacturing can include many activities such as designing and building, testing, packaging shipping, selling, servicing, and other related activities.
How can manufacturing excess production be decreased?
Better inventory management is key to reducing excess production. This would reduce the time needed to manage inventory. We could use these resources to do other productive tasks.
A Kanban system is one way to achieve this. A Kanbanboard is a visual tool that allows you to keep track of the work being done. In a Kanban system, work items move through a sequence of states until they reach their final destination. Each state is assigned a different priority.
When work is completed, it can be transferred to the next stage. A task that is still in the initial stages of a process will be considered complete until it moves on to the next stage.
This allows work to move forward and ensures that no work is missed. A Kanban board allows managers to monitor how much work is being completed at any given moment. This information allows managers to adjust their workflow based off real-time data.
Lean manufacturing can also be used to reduce inventory levels. Lean manufacturing emphasizes eliminating waste in all phases of production. Waste includes anything that does not add value to the product. Some common types of waste include:
-
Overproduction
-
Inventory
-
Unnecessary packaging
-
Material surplus
These ideas will help manufacturers increase efficiency and lower costs.
What is it like to manage a logistics company?
A successful logistics business requires a lot more than just knowledge. Good communication skills are essential to effectively communicate with your suppliers and clients. You will need to know how to interpret data and draw conclusions. You need to be able work under pressure and manage stressful situations. You need to be innovative and creative to come up with new ways to increase efficiency. You will need strong leadership skills to motivate and direct your team members towards achieving their organizational goals.
You should also be organized and efficient to meet tight deadlines.
How can manufacturing efficiency improved?
First, identify the factors that affect production time. We must then find ways that we can improve these factors. If you don’t know how to start, look at which factors have the greatest impact upon production time. Once you've identified them all, find solutions to each one.
Statistics
- Job #1 is delivering the ordered product according to specifications: color, size, brand, and quantity. (netsuite.com)
- In the United States, for example, manufacturing makes up 15% of the economic output. (twi-global.com)
- According to a Statista study, U.S. businesses spent $1.63 trillion on logistics in 2019, moving goods from origin to end user through various supply chain network segments. (netsuite.com)
- In 2021, an estimated 12.1 million Americans work in the manufacturing sector.6 (investopedia.com)
- Many factories witnessed a 30% increase in output due to the shift to electric motors. (en.wikipedia.org)
External Links
How To
Six Sigma in Manufacturing
Six Sigma can be described as "the use of statistical process control (SPC), techniques to achieve continuous improvement." It was developed by Motorola's Quality Improvement Department at their plant in Tokyo, Japan, in 1986. The basic idea behind Six Sigma is to improve quality by improving processes through standardization and eliminating defects. This method has been adopted by many companies in recent years as they believe there are no perfect products or services. Six Sigma seeks to reduce variation between the mean production value. You can calculate the percentage of deviation from the norm by taking a sample of your product and comparing it to the average. If there is a significant deviation from the norm, you will know that something needs to change.
Understanding how your business' variability is a key step towards Six Sigma implementation is the first. Once you understand that, it is time to identify the sources of variation. This will allow you to decide if these variations are random and systematic. Random variations happen when people make errors; systematic variations are caused externally. These are, for instance, random variations that occur when widgets are made and some fall off the production line. If however, you notice that each time you assemble a widget it falls apart in exactly the same spot, that is a problem.
Once you've identified the problem areas you need to find solutions. That solution might involve changing the way you do things or redesigning the process altogether. To verify that the changes have worked, you need to test them again. If they don’t work, you’ll need to go back and rework the plan.