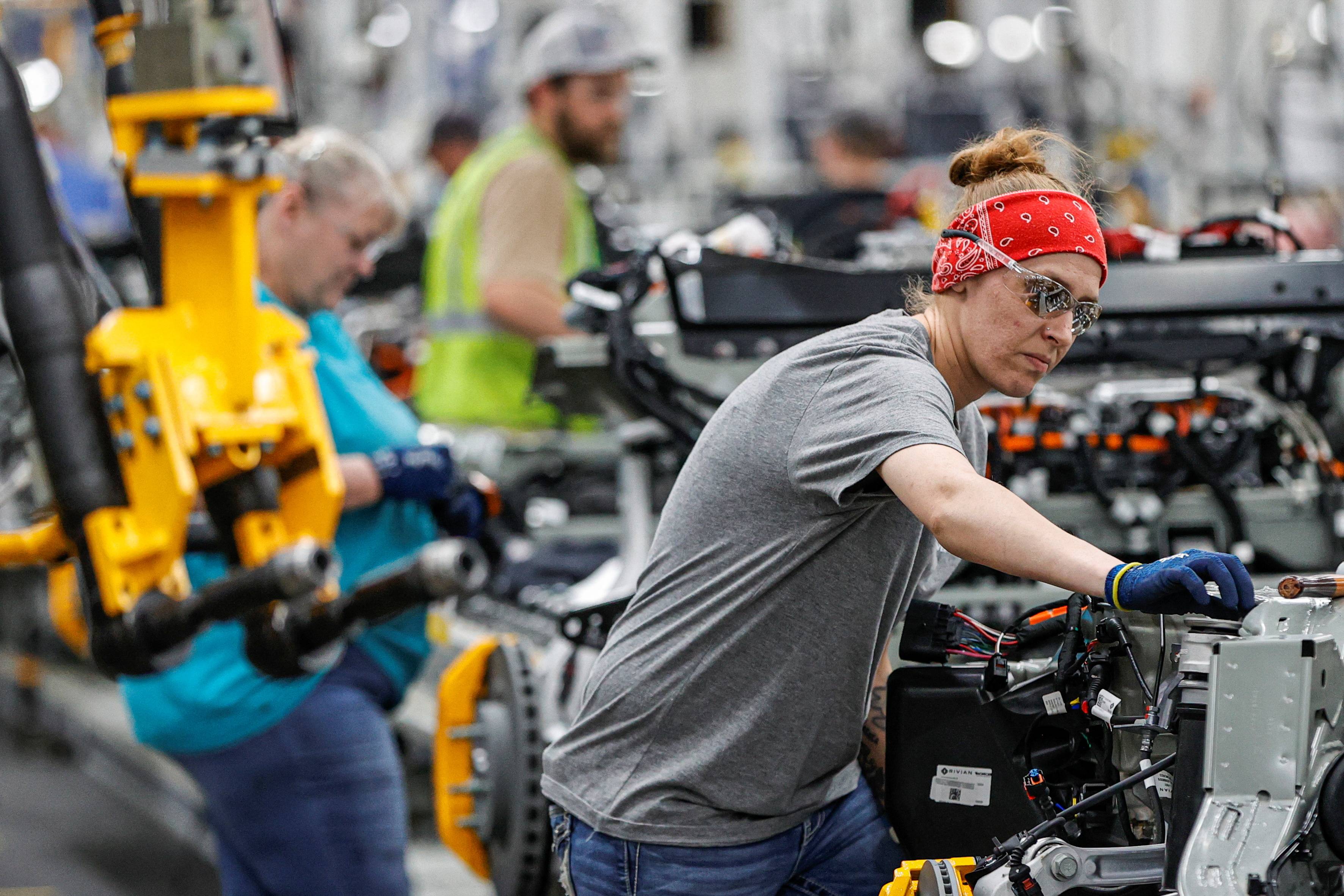
Introducing kaizen into manufacturing processes may not be as easy as some may imagine. It takes time to obtain inventory and ensure everyone is present. The amount of time needed to improve the manufacturing process depends on the level of participation, the problem area, and the firm. Be sure to follow the right methods of implementation and gather the necessary resources in order to make your manufacturing improvement initiative a success. To make this strategy work, create a culture within your company that promotes continuous improvement.
Establishing a culture of improvement in your company
According to a Gallup poll, only 32% of employees in the United States are engaged in their job. Of those, 17.2% were actively disengaged. Implementing a Kaizen culture will encourage employee engagement, which will ultimately improve processes, reduce turnover, and encourage innovation. Engaged employees are more likely than others to share ideas and invent, leading to greater productivity and customer satisfaction. Kaizen culture offers more benefits than reducing waste, increasing productivity, and increasing customer satisfaction.
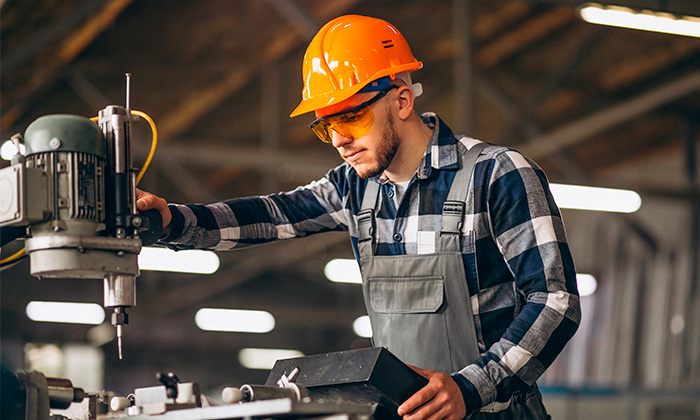
Kaizen is a philosophy that encourages continuous improvement in every area of a business. Kaizen isn't about making huge, unproductive changes. It's about incremental improvement. Kaizen can help reduce costs, increase productivity, improve quality, and improve customer satisfaction when implemented properly. It can also improve communication and morale among employees.
There are many obstacles to implementing Kaizen in manufacturing
Although there are many benefits to implementing kaizen, there are also some drawbacks. First, implementing kaizen requires significant changes in a business's management system. It can be difficult to reverse any changes made once the changes have been made. Second, many businesses find it difficult to change existing work practices, which may pose a barrier to the implementation of kaizen.
Another problem is that many manufacturers work on a "feast-or-famine" basis. If there is not enough demand for their products, a machine shop can run into problems. They will have to fire employees and close the shop. Implementing kaizen (continuous improvement) will keep these machine shops from falling into the "feast or feast" cycle. Kaizen can increase shop efficiency and allow shops to produce more.
Kaizen implementation success rate in manufacturing
Statistics show that the success rate of Kaizen implementation in the manufacturing sector is relatively low. Only 10% of manufacturing companies reported positive results following implementation Kaizen. But this does not mean that the implementation process is worthless. Implementing Kaizen is an integral part of lean manufacturing. Here are some tips that will help you increase the success of your manufacturing business.
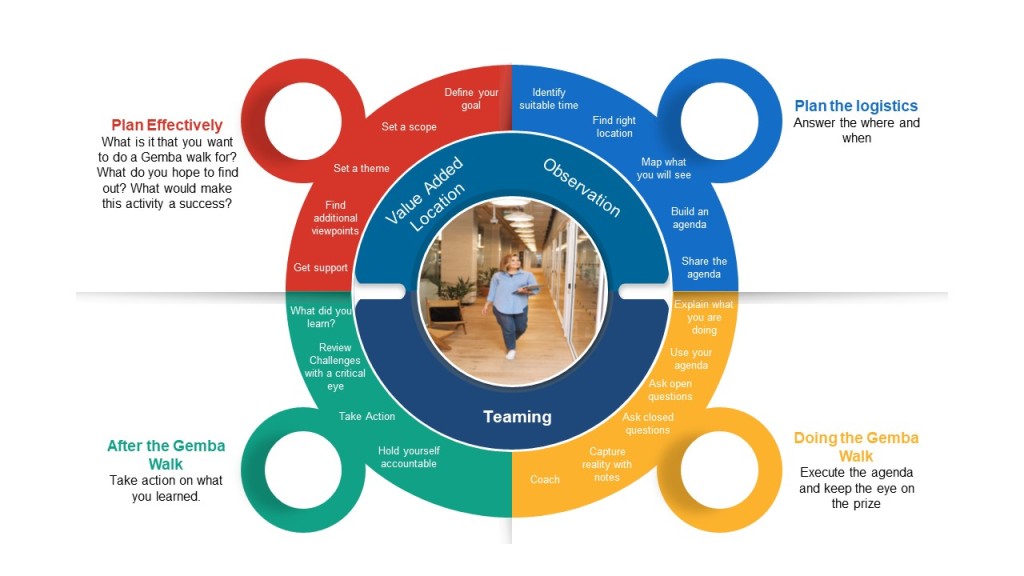
Understanding the state of the world is essential to kaizen. The first step involves collecting data and analysing it to determine the top priorities. Then, improvements are tested and verified by doing a before-and-after comparison. The benefit-to–cost analysis can be used to evaluate the effect of any improvement or the entire process. To assess the program's effectiveness, it is crucial to monitor the results for 60 to 90 days.
FAQ
How can manufacturing avoid production bottlenecks
To avoid production bottlenecks, ensure that all processes run smoothly from the moment you receive your order to the time the product ships.
This includes both planning for capacity and quality control.
Continuous improvement techniques such Six Sigma are the best method to accomplish this.
Six Sigma is a management system used to improve quality and reduce waste in every aspect of your organization.
It focuses on eliminating variation and creating consistency in your work.
What are the logistics products?
Logistics refers to the movement of goods from one place to another.
They include all aspects of transport, including packaging, loading, transporting, unloading, storing, warehousing, inventory management, customer service, distribution, returns, and recycling.
Logisticians ensure that products reach the right destination at the right moment and under safe conditions. They help companies manage their supply chain efficiency by providing information on demand forecasts, stock levels, production schedules, and availability of raw materials.
They can also track shipments in transit and monitor quality standards.
What kind of jobs are there in logistics?
Logistics can offer many different jobs. Some of them are:
-
Warehouse workers – They load and unload pallets and trucks.
-
Transportation drivers – These drivers drive trucks and wagons to transport goods and pick up the goods.
-
Freight handlers: They sort and package freight in warehouses.
-
Inventory managers – They manage the inventory in warehouses.
-
Sales representatives: They sell products to customers.
-
Logistics coordinators are responsible for organizing and planning logistics operations.
-
Purchasing agents - They purchase goods and services needed for company operations.
-
Customer service representatives – They answer emails and phone calls from customers.
-
Shipping clerks – They process shipping orders, and issue bills.
-
Order fillers - They fill orders based on what is ordered and shipped.
-
Quality control inspectors – They inspect incoming and outgoing products to ensure that there are no defects.
-
Others - There are many other types of jobs available in logistics, such as transportation supervisors, cargo specialists, etc.
What are the responsibilities for a manufacturing manager
A manufacturing manager must ensure that all manufacturing processes are efficient and effective. They must also be alert to any potential problems and take appropriate action.
They should also be able communicate with other departments, such as sales or marketing.
They should be informed about industry trends and be able make use of this information to improve their productivity and efficiency.
What are the four types in manufacturing?
Manufacturing is the process that transforms raw materials into useful products. It involves many different activities such as designing, building, testing, packaging, shipping, selling, servicing, etc.
What are the responsibilities of a logistic manager?
A logistics manager makes sure that all goods are delivered on-time and in good condition. This is done by using his/her experience and knowledge of the company's products. He/she should ensure that sufficient stock is available in order to meet customer demand.
Is it possible to automate certain parts of manufacturing
Yes! Yes. Automation has been around since ancient time. The wheel was invented by the Egyptians thousands of years ago. We now use robots to help us with assembly lines.
There are many uses of robotics today in manufacturing. These include:
-
Line robots
-
Robot welding
-
Robot painting
-
Robotics inspection
-
Robots that produce products
Manufacturing could also benefit from automation in other ways. 3D printing, for example, allows us to create custom products without waiting for them to be made.
Statistics
- In 2021, an estimated 12.1 million Americans work in the manufacturing sector.6 (investopedia.com)
- [54][55] These are the top 50 countries by the total value of manufacturing output in US dollars for its noted year according to World Bank.[56] (en.wikipedia.org)
- Job #1 is delivering the ordered product according to specifications: color, size, brand, and quantity. (netsuite.com)
- According to the United Nations Industrial Development Organization (UNIDO), China is the top manufacturer worldwide by 2019 output, producing 28.7% of the total global manufacturing output, followed by the United States, Japan, Germany, and India.[52][53] (en.wikipedia.org)
- (2:04) MTO is a production technique wherein products are customized according to customer specifications, and production only starts after an order is received. (oracle.com)
External Links
How To
How to Use Six Sigma in Manufacturing
Six Sigma is "the application statistical process control (SPC), techniques for continuous improvement." Motorola's Quality Improvement Department, Tokyo, Japan, developed it in 1986. Six Sigma's main goal is to improve process quality by standardizing processes and eliminating defects. Since there are no perfect products, or services, this approach has been adopted by many companies over the years. Six Sigma's primary goal is to reduce variation from the average value of production. This means that you can take a sample from your product and then compare its performance to the average to find out how often the process differs from the norm. If you notice a large deviation, then it is time to fix it.
Understanding the nature of variability in your business is the first step to Six Sigma. Once you understand this, you can then identify the causes of variation. These variations can also be classified as random or systematic. Random variations are caused by human errors. Systematic variations can be caused by outside factors. You could consider random variations if some widgets fall off the assembly lines. However, if you notice that every time you assemble a widget, it always falls apart at exactly the same place, then that would be a systematic problem.
Once you've identified where the problems lie, you'll want to design solutions to eliminate those problems. It might mean changing the way you do business or redesigning it entirely. After implementing the new changes, you should test them again to see if they worked. If they don’t work, you’ll need to go back and rework the plan.