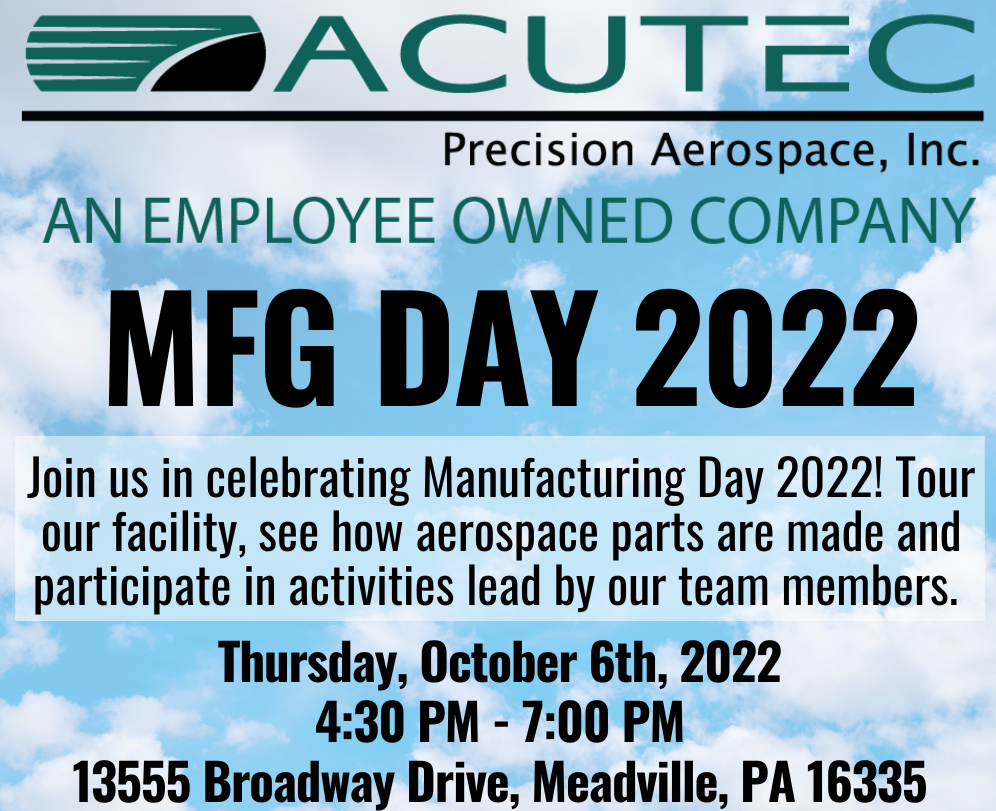
Many companies offer part-time or full-time work from home logistics jobs. These jobs can help you increase your earnings. Some companies are even adopting new technologies to better serve their workers. If you use the latest technology correctly, it can make your job much easier and more precise.
Work from home jobs in logistics are available in many industries. One of the most lucrative jobs is in BPO, which has a lot of talent from India. Many multinational companies are interested in bringing Indians into their ranks. One industry that is looking for Indian talent is the logistics industry. Many benefits are offered by logistics companies, such as competitive salaries and flexible work hours. It can be difficult for people to decide which company is right for them. It's a smart idea to contact several companies to determine the best fit.
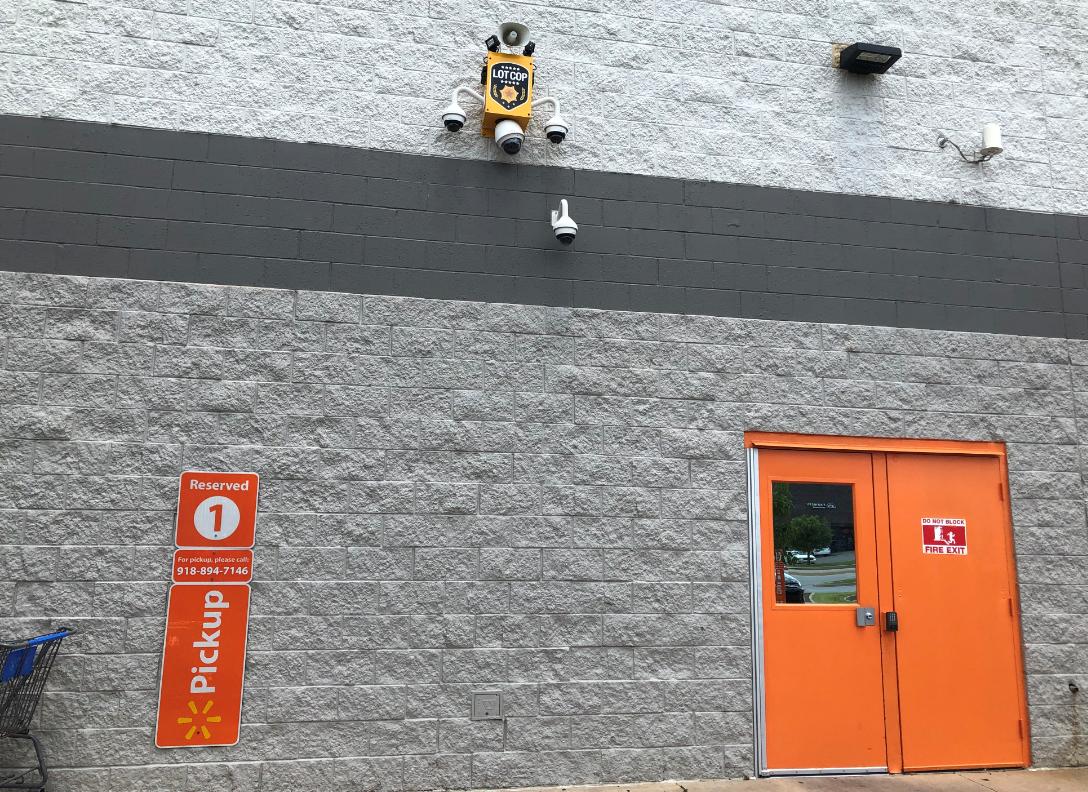
The logistics industry is no stranger to technology. The internet is a great place to begin if you are looking to join a modern, efficient logistics company. There are many great examples, such as Uss-Express. They offer competitive salaries and many other perks including flexible work hours and a quick on-boarding process. The ecommerce industry is a vast and complex field. You will learn everything from shipping to delivery. Logistics jobs are a highly-sought after profession.
Working in the logistics industry has many benefits, including flexibility. One example is that you can work from your home and still receive regular raises. This means that you don't have to commute to the office and you can do other things while you are at it. Another advantage is that you can choose the conditions you prefer. You can, for example, work remotely but only when you want. This is a great benefit for families with young or elderly children.
The best thing about work-from-home logistics jobs is that you can earn good money while still maintaining your sanity. Companies that offer great benefits and incentives are the best to work for. Also, the best companies are known for transparency and fairness. If you're careful, you can make sure that you don’t get ripped off or manipulated by your employer. There are many companies to choose from. But it is important to do the right thing to protect your family and yourself.
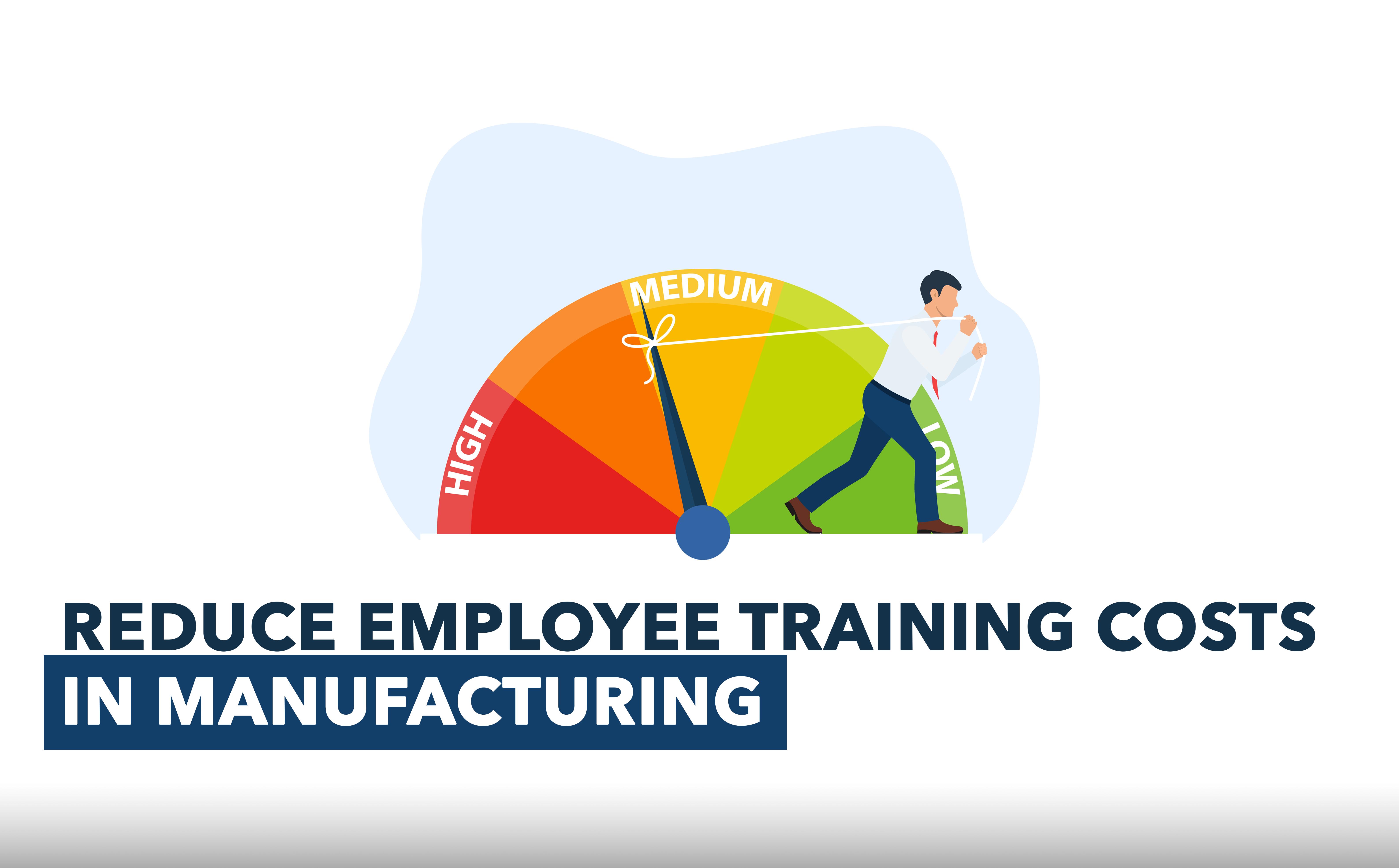
There are many other options for work at home logistics jobs, such as that of a quality manager. This role is responsible for inspecting the quality of packaging materials, and then delivering the goods. They are critical as they can either make or break products. There is more to the quality manager role than meets the eye. Customers may have questions about the product's quality.
FAQ
How is a production manager different from a producer planner?
The primary difference between a producer planner and a manager of a project is that the manager usually plans and organizes the whole project, while a production planner is only involved in the planning stage.
How can overproduction in manufacturing be reduced?
In order to reduce excess production, you need to develop better inventory management methods. This would reduce the time needed to manage inventory. We could use these resources to do other productive tasks.
One way to do this is to adopt a Kanban system. A Kanban Board is a visual display that tracks work progress. Kanban systems allow work items to move through different states until they reach their final destination. Each state represents an individual priority level.
As an example, if work is progressing from one stage of the process to another, then the current task is complete and can be transferred to the next. A task that is still in the initial stages of a process will be considered complete until it moves on to the next stage.
This allows for work to continue moving forward, while also ensuring that there is no work left behind. Managers can view the Kanban board to see how much work they have done. This allows them to adjust their workflows based on real-time information.
Lean manufacturing, another method to control inventory levels, is also an option. Lean manufacturing works to eliminate waste throughout every stage of the production chain. Anything that does nothing to add value to a product is waste. The following are examples of common waste types:
-
Overproduction
-
Inventory
-
Unnecessary packaging
-
Material surplus
Manufacturers can reduce their costs and improve their efficiency by using these ideas.
What does the term manufacturing industries mean?
Manufacturing Industries are those businesses that make products for sale. These products are sold to consumers. These companies use various processes such as production, distribution, retailing, management, etc., to fulfill this purpose. These companies produce goods using raw materials and other equipment. This covers all types of manufactured goods including clothing, food, building supplies and furniture, as well as electronics, tools, machinery, vehicles and pharmaceuticals.
What are my options for learning more about manufacturing
The best way to learn about manufacturing is through hands-on experience. But if that is not possible you can always read books and watch educational videos.
What is the responsibility of a production planner?
Production planners make sure that every aspect of the project is delivered on-time, within budget, and within schedule. A production planner ensures that the service and product meet the client's expectations.
Statistics
- You can multiply the result by 100 to get the total percent of monthly overhead. (investopedia.com)
- Job #1 is delivering the ordered product according to specifications: color, size, brand, and quantity. (netsuite.com)
- According to the United Nations Industrial Development Organization (UNIDO), China is the top manufacturer worldwide by 2019 output, producing 28.7% of the total global manufacturing output, followed by the United States, Japan, Germany, and India.[52][53] (en.wikipedia.org)
- Many factories witnessed a 30% increase in output due to the shift to electric motors. (en.wikipedia.org)
- According to a Statista study, U.S. businesses spent $1.63 trillion on logistics in 2019, moving goods from origin to end user through various supply chain network segments. (netsuite.com)
External Links
How To
How to Use Six Sigma in Manufacturing
Six Sigma is defined by "the application SPC (statistical process control) techniques to achieve continuous improvements." Motorola's Quality Improvement Department, Tokyo, Japan, developed it in 1986. Six Sigma is a method to improve quality through standardization and elimination of defects. In recent years, many companies have adopted this method because they believe there is no such thing as perfect products or services. Six Sigma's main objective is to reduce variations from the production average. This means that you can take a sample from your product and then compare its performance to the average to find out how often the process differs from the norm. If there is a significant deviation from the norm, you will know that something needs to change.
Understanding how your business' variability is a key step towards Six Sigma implementation is the first. Once you've understood that, you'll want to identify sources of variation. These variations can also be classified as random or systematic. Random variations occur when people make mistakes; systematic ones are caused by factors outside the process itself. These are, for instance, random variations that occur when widgets are made and some fall off the production line. If however, you notice that each time you assemble a widget it falls apart in exactly the same spot, that is a problem.
Once you've identified the problem areas you need to find solutions. You might need to change the way you work or completely redesign the process. To verify that the changes have worked, you need to test them again. If they don’t work, you’ll need to go back and rework the plan.