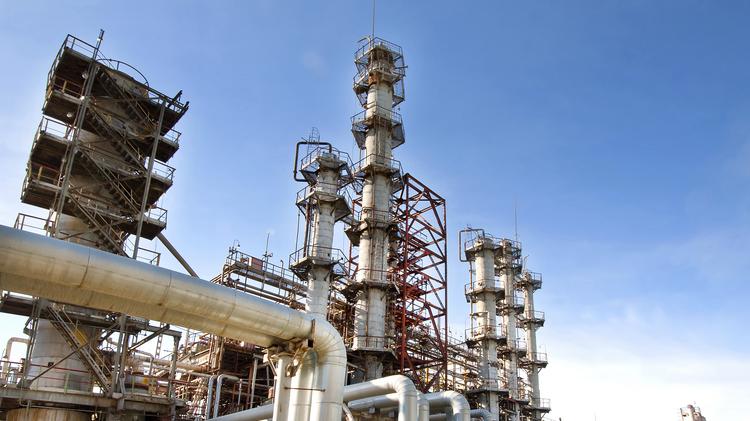
The logistics industry can seem daunting. You may have to take some extra courses or complete some internships before you can start your new job. The good news is that there are plenty of entry level logistics jobs available to help you get your foot in the door.
Most of these positions require an associate's degree, but a bachelor's degree is also beneficial. The degree will give you a better understanding of how the supply chain works. Having a degree will also help you qualify for professional certifications. You can also enroll in online courses on specialized topics. In some cases, you can get reimbursed for the cost of your graduate program.
Entry level logistics jobs can be found in a variety of industries. One example is in the aerospace, oil and natural gas or freight transportation industry. You may also have the opportunity to work in international settings, in a variety industries.
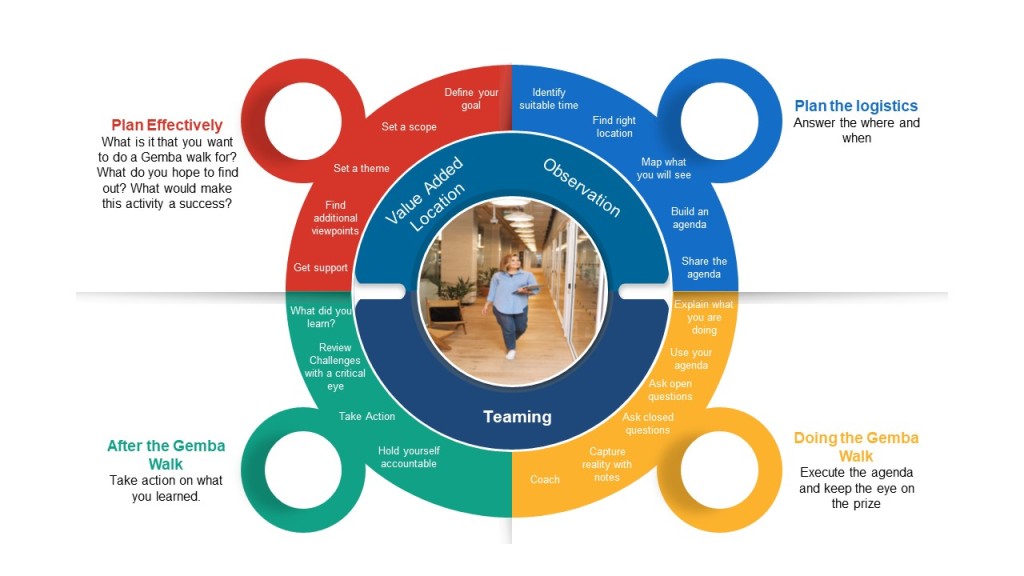
Logistics professionals use both sides of their brains to solve problems. They use their skills to create sustainable supply chains. They can also influence the operational and executive decision-making. The job can be challenging, but it can also be very rewarding. In a booming economy, the logistics industry is experiencing rapid growth.
Strong leadership and management skills are essential for logistics workers. They also need to be able to communicate effectively. They also need to be able use specialized software. They may be in charge of finding storage space near shipping ports. They may also be responsible to make sure that the goods are cleared at customs.
Logistics is continuously evolving. The industry is constantly changing with new technologies and business models. These changes are important to understand. A bachelor's degree can help you become a skilled logistics professional. You can also build a professional network. You can also attend seminars and conferences in the industry. Accredited institutions can also offer a degree.
Administrative jobs can also be found. These require strong communication and analytical skills. Some roles are within the company while others involve customers, suppliers, and other business functions.
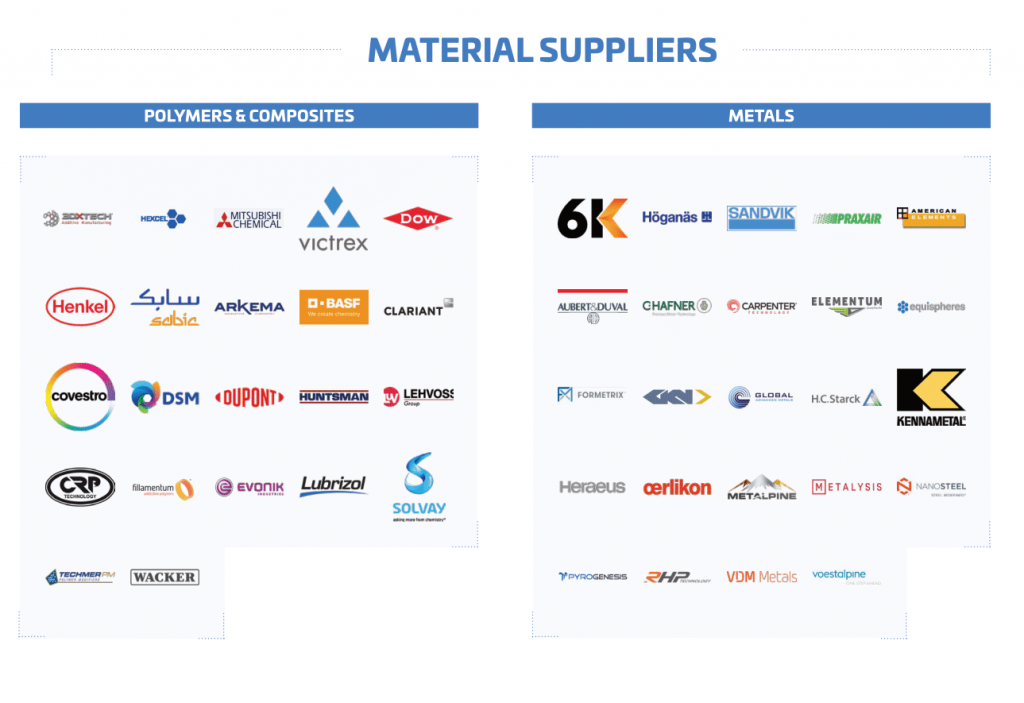
You can start your career in logistics by becoming a member a professional association. These organizations offer information about professional certifications, industry news, job board listings, and other useful information. They might also be able help you find mentors. These organizations may even offer graduate fellowships to students.
Numerous countries also offer vocational certificates, which do not require any prior logistics experience. These certifications can be especially valuable to companies that own their own transport fleets. You can also get a Certificate of Professional Competence in Road Transport Operations, which is highly valued by enterprises with in-house transportation fleets.
You can find entry level jobs in logistics all over the country. Online resources are also available for job seekers. For help, you can also tap into your family and friends.
FAQ
What is production planning?
Production planning is the process of creating a plan that covers all aspects of production. This includes scheduling, budgeting and crew, location, equipment, props, and more. It is important to have everything ready and planned before you start shooting. It should also provide information about how best to produce the best results while on set. This includes information on shooting times, locations, cast lists and crew details.
First, you need to plan what you want to film. You might have an idea of where you want to film, or you may have specific locations or sets in mind. Once you have identified your locations and scenes it's time to begin figuring out what elements you will need for each one. For example, you might decide that you need a car but don't know exactly what model you want. You could look online for cars to see what options are available, and then narrow down your choices by selecting between different makes or models.
After you have selected the car you want, you can begin to think about additional features. Do you need people sitting in the front seats? Maybe you need someone to move around in the back. You might want to change your interior color from black and white. These questions will help you determine the exact look and feel of your car. The type of shots that you are looking for is another thing to consider. You will be filming close-ups and wide angles. Maybe you want to show the engine and the steering wheel. These details will help identify the exact car you wish to film.
Once you have made all the necessary decisions, you can start to create a schedule. You will know when you should start and when you should finish shooting. Every day will have a time for you to arrive at the location, leave when you are leaving and return home when you are done. It will help everyone know exactly what they have to do and when. It is possible to make arrangements in advance for additional staff if you are looking to hire. You don't want to hire someone who won't show up because he didn't know.
When creating your schedule, you will also need to consider the number of days you need to film. Some projects may only take a couple of days, while others could last for weeks. While creating your schedule, it is important to remember whether you will require more than one shot per day. Shooting multiple takes over the same location will increase costs and take longer to complete. You can't be certain if you will need multiple takes so it is better not to shoot too many.
Budget setting is an important part of production planning. You will be able to manage your resources if you have a realistic budget. If you have to reduce your budget due to unexpected circumstances, you can always lower it later. You shouldn't underestimate the amount you'll spend. If you underestimate the cost of something, you will have less money left after paying for other items.
Planning production is a tedious process. Once you have a good understanding of how everything works together, planning future projects becomes easy.
What is the job of a production plan?
A production planner makes sure all project elements are delivered on schedule, within budget, as well as within the agreed scope. They make sure that the product and services meet client expectations.
What does it take to run a logistics business?
It takes a lot of skills and knowledge to run a successful logistics business. To communicate effectively with clients and suppliers, you must be able to communicate well. It is important to be able to analyse data and draw conclusions. You must be able manage stress and pressure under pressure. To improve efficiency, you must be innovative and creative. You must be a strong leader to motivate others and direct them to achieve organizational goals.
You should also be organized and efficient to meet tight deadlines.
What are the 7 R's of logistics?
The acronym "7R's" of Logistics stands for seven principles that underpin logistics management. It was developed by International Association of Business Logisticians (IABL), and published as part of their "Seven Principles of Logistics Management Series" in 2004.
The acronym is made up of the following letters:
-
Responsible - to ensure that all actions are within the legal requirements and are not detrimental to others.
-
Reliable - You can have confidence that you will fulfill your promises.
-
Reasonable - make sure you use your resources well and don't waste them.
-
Realistic – Consider all aspects, including cost-effectiveness as well as environmental impact.
-
Respectful: Treat others with fairness and equity
-
Be resourceful: Look for opportunities to save money or increase productivity.
-
Recognizable is a company that provides customers with value-added solutions.
What does it mean to be a manufacturer?
Manufacturing Industries are companies that manufacture products. Consumers are those who purchase these products. To accomplish this goal, these companies employ a range of processes including distribution, sales, management, and production. They make goods from raw materials with machines and other equipment. This includes all types manufactured goods such as clothing, building materials, furniture, electronics, tools and machinery.
Statistics
- It's estimated that 10.8% of the U.S. GDP in 2020 was contributed to manufacturing. (investopedia.com)
- According to the United Nations Industrial Development Organization (UNIDO), China is the top manufacturer worldwide by 2019 output, producing 28.7% of the total global manufacturing output, followed by the United States, Japan, Germany, and India.[52][53] (en.wikipedia.org)
- In the United States, for example, manufacturing makes up 15% of the economic output. (twi-global.com)
- Many factories witnessed a 30% increase in output due to the shift to electric motors. (en.wikipedia.org)
- (2:04) MTO is a production technique wherein products are customized according to customer specifications, and production only starts after an order is received. (oracle.com)
External Links
How To
How to Use the 5S to Increase Productivity In Manufacturing
5S stands to stand for "Sort", “Set In Order", “Standardize", and "Store". Toyota Motor Corporation was the first to develop the 5S approach in 1954. This methodology helps companies improve their work environment to increase efficiency.
This approach aims to standardize production procedures, making them predictable, repeatable, and easily measurable. It means tasks like cleaning, sorting or packing, labeling, and storing are done every day. These actions allow workers to perform their job more efficiently, knowing what to expect.
Implementing 5S involves five steps: Sort, Set in Order, Standardize Separate, Store, and Each step requires a different action, which increases efficiency. If you sort items, it makes them easier to find later. When you set items in an order, you put items together. You then organize your inventory in groups. Finally, when you label your containers, you ensure everything is labeled correctly.
Employees will need to be more critical about their work. Employees need to understand the reasons they do certain jobs and determine if there is a better way. To be successful in the 5S system, employees will need to acquire new skills and techniques.
In addition to increasing efficiency, the 5S method also improves morale and teamwork among employees. They will feel motivated to strive for higher levels of efficiency once they start to see results.