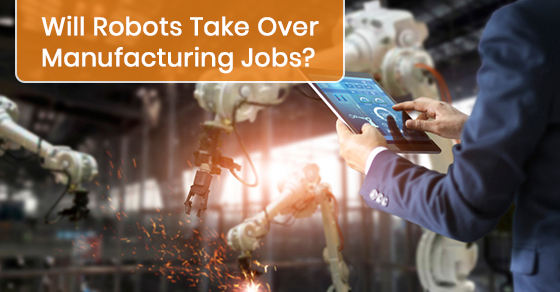
Cost estimates are required for nearly all business activities. Cost estimators are responsible for this. They are required to help companies calculate the cost of manufacturing and developing new services and products. They are also required to evaluate the cost of building a new structure. This includes the analysis of the labor and material costs.
Construction companies employ the majority of cost estimators. They must have a good understanding of construction methods and processes. They must also be familiar with computer-aided designs (CAD) software. This software is used for improving the efficiency of design, and manufacturing. It is also necessary for cost estimators to be able read data from databases. They can also use Microsoft Excel or other software.
Cost estimators work with other professionals to make accurate cost estimates. They review the project blueprints and site conditions to determine the cost of each component. They might also collaborate with engineers to determine the required gauges and machining operations.
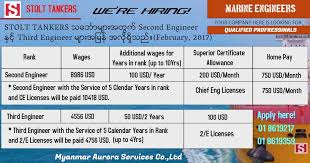
Cost estimators need to be detailed-oriented, confident, and reliable. They must be able to analyze information that is difficult to interpret. They must also be able to present findings accurately and assertively. In addition, they must be able to work with professionals and clients.
Cost estimators usually work in the cost or engineering departments of companies. They should have a solid knowledge of science and math. They should also be familiar with computer software, including CAD, BIM, and commercial software. They might also need to complete a certification course. Some certifications include the Certified Cost Estimator/Analyst (CCEA), Professional Cost Estimator/Analyst, and Certified Professional Estimator.
Cost estimators may specialize in particular industries or services. While some specialize in building and construction costs, others are more focused on software development costs. Cost estimators are also able to find work in other areas, such as auto repair and maintenance, construction, and specialty trade contractors.
The occupation involves communicating with clients, suppliers, and engineers. They also have a good understanding of industry terminology. They are also able to build a solid knowledge base in order to prepare cost estimates. In addition to preparing cost estimates, many individuals in this occupation conduct studies, study the effects of different processes on costs, and find ways to reduce costs.
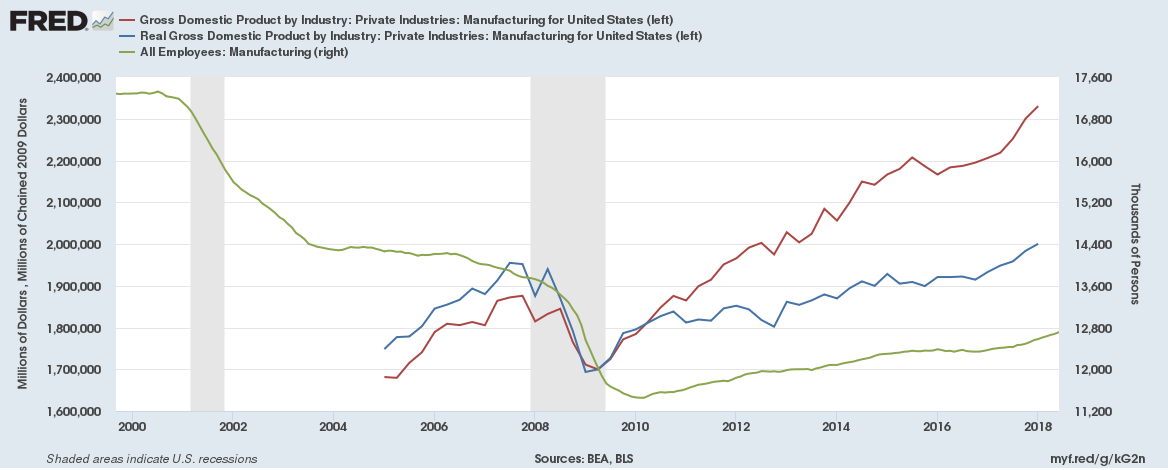
The industry may require job applicants to have a bachelor’s degree. They may also require an internship. They may also be eligible for cooperative education programs. A degree in building construction, or construction management is also an advantage for construction companies.
They work in construction and other manufacturing companies. They provide accurate estimates to companies that enable them to make profitable bids. They also analyze data concerning the supply chain and other factors that can affect costs. You can also hire cost estimators to work on government programs. They may also be required to redesign existing products.
Cost estimators should have a good understanding of computer-aided planning (CAD) software. They can also be trained to use automatic cost estimation software.
FAQ
What is the difference between a production planner and a project manager?
A production planner is more involved in the planning phase of the project than a project manger.
What is it like to manage a logistics company?
A successful logistics business requires a lot more than just knowledge. For clients and suppliers to be successful, you need to have excellent communication skills. You need to understand how to analyze data and draw conclusions from it. You must be able and able to handle stress situations and work under pressure. To improve efficiency, you must be innovative and creative. To motivate and guide your team towards reaching organizational goals, you must have strong leadership skills.
It is also important to be efficient and well organized in order meet deadlines.
What are the 4 types manufacturing?
Manufacturing refers the process of turning raw materials into useful products with machines and processes. Manufacturing involves many activities, including designing, building, testing and packaging, shipping, selling, service, and so on.
What is production planning?
Production planning is the process of creating a plan that covers all aspects of production. This includes scheduling, budgeting and crew, location, equipment, props, and more. This document aims to ensure that everything is planned and ready when you are ready to shoot. You should also have information to ensure the best possible results on set. This includes location information, crew details, equipment specifications, and casting lists.
First, you need to plan what you want to film. You may have decided where to shoot or even specific locations you want to use. Once you have identified your locations and scenes, you can start working out which elements you require for each scene. You might decide you need a car, but not sure what make or model. You could look online for cars to see what options are available, and then narrow down your choices by selecting between different makes or models.
After you've found the perfect car, it's time to start thinking about adding extras. Are you looking for people to sit in the front seats? You might also need someone to help you get around the back. Maybe you want to change the interior color from black to white? These questions will help guide you in determining the ideal look and feel for your car. Also, think about what kind of shots you would like to capture. What type of shots will you choose? Maybe you want the engine or the steering wheels to be shown. All of these things will help you identify the exact style of car you want to film.
Once you have all the information, you are ready to create a plan. The schedule will show you when to begin shooting and when to stop. Each day will include the time when you need to arrive at the location, when you need to leave and when you need to return home. This way, everyone knows what they need to do and when. It is possible to make arrangements in advance for additional staff if you are looking to hire. You don't want to hire someone who won't show up because he didn't know.
Your schedule will also have to be adjusted to reflect the number of days required to film. Some projects only take one or two days, while others may last weeks. When you are creating your schedule, you should always keep in mind whether you need more than one shot per day or not. Multiple takes at the same place will result in higher costs and longer completion times. It's better to be safe than sorry and shoot less takes if you're not certain whether you need more takes.
Budgeting is another crucial aspect of production plan. You will be able to manage your resources if you have a realistic budget. It is possible to reduce the budget at any time if you experience unexpected problems. However, it is important not to overestimate the amount that you will spend. If you underestimate the cost of something, you will have less money left after paying for other items.
Planning production is a tedious process. Once you have a good understanding of how everything works together, planning future projects becomes easy.
Is there anything we should know about Manufacturing Processes prior to learning about Logistics.
No. It doesn't matter if you don't know anything about manufacturing before you learn about logistics. It is important to know about the manufacturing processes in order to understand how logistics works.
Is automation important for manufacturing?
Automation is essential for both manufacturers and service providers. It enables them to provide services faster and more efficiently. In addition, it helps them reduce costs by reducing human errors and improving productivity.
Statistics
- Many factories witnessed a 30% increase in output due to the shift to electric motors. (en.wikipedia.org)
- Job #1 is delivering the ordered product according to specifications: color, size, brand, and quantity. (netsuite.com)
- According to a Statista study, U.S. businesses spent $1.63 trillion on logistics in 2019, moving goods from origin to end user through various supply chain network segments. (netsuite.com)
- According to the United Nations Industrial Development Organization (UNIDO), China is the top manufacturer worldwide by 2019 output, producing 28.7% of the total global manufacturing output, followed by the United States, Japan, Germany, and India.[52][53] (en.wikipedia.org)
- It's estimated that 10.8% of the U.S. GDP in 2020 was contributed to manufacturing. (investopedia.com)
External Links
How To
How to Use Just-In-Time Production
Just-in-time (JIT) is a method that is used to reduce costs and maximize efficiency in business processes. It allows you to get the right amount resources at the right time. This means you only pay what you use. Frederick Taylor developed the concept while working as foreman in early 1900s. He noticed that workers were often paid overtime when they had to work late. He decided to ensure workers have enough time to do their jobs before starting work to improve productivity.
JIT is a way to plan ahead and make sure you don't waste any money. It is important to look at your entire project from beginning to end and ensure that you have enough resources to handle any issues that may arise. You'll be prepared to handle any potential problems if you know in advance. This way, you won't end up paying extra money for things that weren't really necessary.
There are many types of JIT methods.
-
Demand-driven: This type of JIT allows you to order the parts/materials required for your project on a regular basis. This will let you track the amount of material left over after you've used it. This will let you know how long it will be to produce more.
-
Inventory-based: You stock materials in advance to make your projects easier. This allows for you to anticipate how much you can sell.
-
Project-driven: This means that you have enough money to pay for your project. You will be able to purchase the right amount of materials if you know what you need.
-
Resource-based JIT : This is probably the most popular type of JIT. Here, you allocate certain resources based on demand. If you have many orders, you will assign more people to manage them. You'll have fewer orders if you have fewer.
-
Cost-based: This is a similar approach to resource-based but you are not only concerned with how many people you have, but also how much each one costs.
-
Price-based pricing: This is similar in concept to cost-based but instead you look at how much each worker costs, it looks at the overall company's price.
-
Material-based: This approach is similar to cost-based. However, instead of looking at the total cost for the company, you look at how much you spend on average on raw materials.
-
Time-based: This is another variation of resource-based JIT. Instead of focusing on how much each employee costs, you focus on how long it takes to complete the project.
-
Quality-based JIT - This is another form of resource-based JIT. Instead of thinking about how much each employee costs or how long it takes to manufacture something, you think about how good the quality of your product is.
-
Value-based JIT is the newest form of JIT. This is where you don't care about how the products perform or whether they meet customers' expectations. Instead, you focus on the added value that you provide to your market.
-
Stock-based: This is an inventory-based method that focuses on the actual number of items being produced at any given time. This is used to increase production and minimize inventory.
-
Just-in-time (JIT) planning: This is a combination of JIT and supply chain management. It is the process of scheduling components' delivery as soon as they have been ordered. This is important as it reduces lead time and increases throughput.