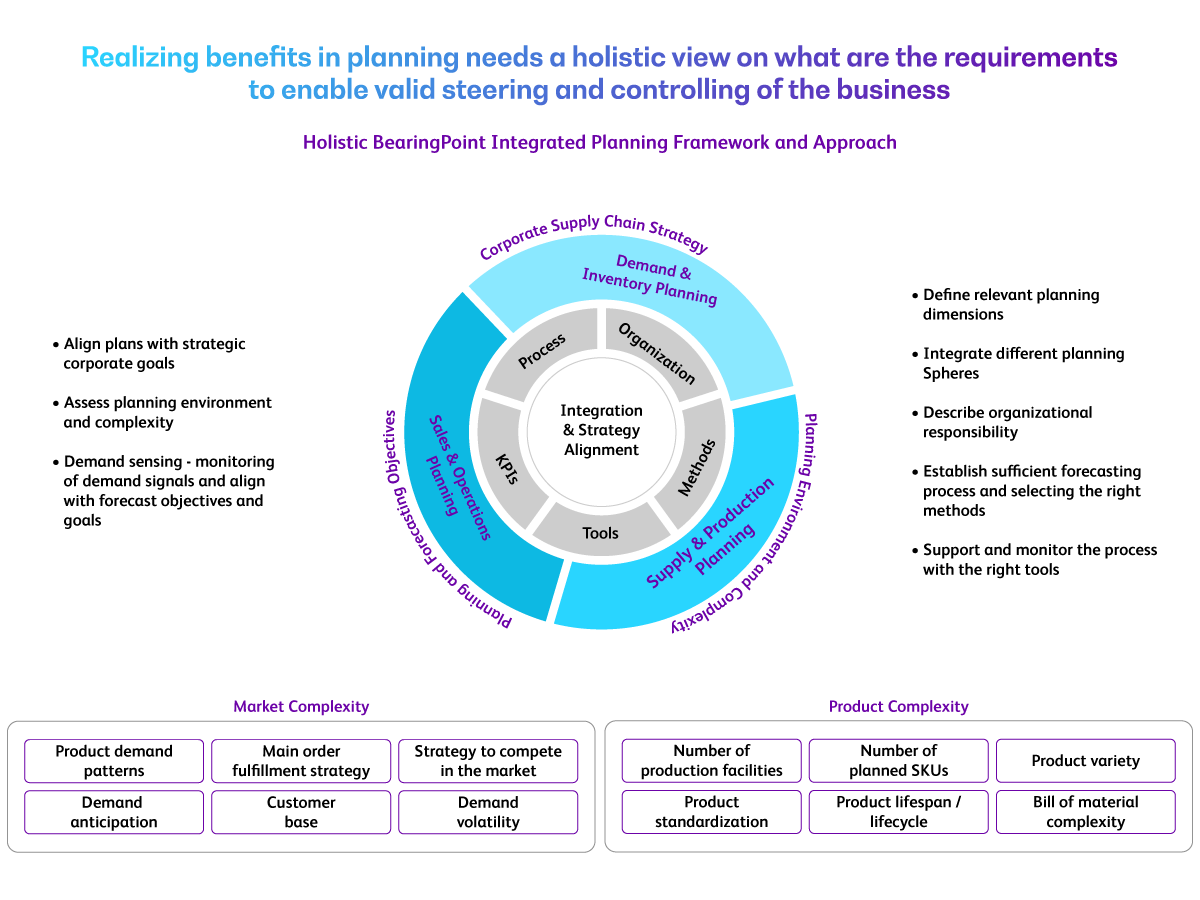
Global supply chains have changed over the years. They have moved from being primarily an industrial problem to becoming a serious economic threat. It is important to stay up-to-date with the latest developments. Global supply chains can be complex and interconnected in many ways.
Global value chain are made up of capital, flows, and intangibles. They are a reflection of economies of scale and long-standing relationships, as well as specialization. Some value chains have high capital requirements, but others are more regionalized.
Global supply chain dynamics are complex and multidimensional. They are an integral part of global trade as well as the functioning of countries. They are also vulnerable to disruptions. These disruptions could be either temporary or permanent. It is essential to have a diverse, flexible, and resilient supply network in order to avoid these disruptions. This requires a comprehensive approach which includes structural reforms and prudent risk management. The first step in building a supply network that can withstand the next storm is to identify the most pressing issues and determine the solutions.
Companies should assess the risks of supply-chain disruptions and also consider the risks associated manufacturing, energy, and materials. They should also simulate extreme supply/demand disruptions in an effort to gauge their impact. They should also review their inventories of critical materials and make sure they have sufficient supply for foreseeable demand. To develop a resilient supply system, it requires a strategic approach. This could include prioritizing production, moving manufacturing to more flexible locations and improving supply chain technology.
The COVID-19 outbreak caused major disruptions to global supply networks. Many countries imposed tariffs against one another, while other countries imposed sanctions on the other. These tariffs and sanctions increased trade frictions, making it more difficult for the United States and other countries to sell certain products. These disruptions can lead to higher inflation. They have made companies more aware about the fragility and potential dangers of their supply chain and forced them to rethink their design and implementation.
The COVID-19 epidemic caused severe disruption in global supply chain operations, but the effects of the pandemic are still being felt. The blockage of the Suez Canal, for instance, has caused supply chain disruptions for up to six months. This has led to an increase in freight prices. Annual inflation in the UK is currently at 9%
It is difficult to ignore that China and the United States are currently in a trade dispute. Supply chain leaders have to question the logic of relying so heavily on outsourced networks. They need to consider the risks of labor shortages resulting from economic shocks. Supply chain leaders should also consider the benefits of new forms of cross-border finance and regulation, which can expand global integration.
Despite all the turmoil, we are still connected to the rest of the world. Global integration can be realized when firms take a holistic approach to their supply chain.
FAQ
Can we automate some parts of manufacturing?
Yes! Since ancient times, automation has been in existence. The wheel was invented by the Egyptians thousands of years ago. Nowadays, we use robots for assembly lines.
Robotics is used in many manufacturing processes today. They include:
-
Robots for assembly line
-
Robot welding
-
Robot painting
-
Robotics inspection
-
Robots that create products
Manufacturing could also benefit from automation in other ways. For instance, 3D printing allows us make custom products and not have to wait for months or even weeks to get them made.
What is the best way to learn about manufacturing?
The best way to learn about manufacturing is through hands-on experience. But if that is not possible you can always read books and watch educational videos.
What are manufacturing and logistics?
Manufacturing refers to the process of making goods using raw materials and machines. Logistics covers all aspects involved in managing supply chains, including procurement and production planning. Manufacturing and logistics can often be grouped together to describe a larger term that covers both the creation of products, and the delivery of them to customers.
How can efficiency in manufacturing be improved?
The first step is to identify the most important factors affecting production time. We then need to figure out how to improve these variables. If you aren't sure where to begin, think about the factors that have the greatest impact on production time. Once you have identified the factors, then try to find solutions.
How can overproduction in manufacturing be reduced?
In order to reduce excess production, you need to develop better inventory management methods. This would reduce the time spent on unproductive activities like purchasing, storing and maintaining excess stock. By doing this, we could free up resources for other productive tasks.
Kanban systems are one way to achieve this. A Kanban board, a visual display to show the progress of work, is called a Kanban board. A Kanban system allows work items to move through several states before reaching their final destination. Each state has a different priority level.
If work is moving from one stage to the other, then the current task can be completed and moved on to the next. However, if a task is still at the beginning stages, it will remain so until it reaches the end of the process.
This allows for work to continue moving forward, while also ensuring that there is no work left behind. Managers can view the Kanban board to see how much work they have done. This information allows them to adjust their workflow based on real-time data.
Lean manufacturing can also be used to reduce inventory levels. Lean manufacturing seeks to eliminate waste from every step of the production cycle. Any product that isn't adding value can be considered waste. These are some of the most common types.
-
Overproduction
-
Inventory
-
Packaging that is not necessary
-
Excess materials
These ideas can help manufacturers improve efficiency and reduce costs.
Statistics
- In the United States, for example, manufacturing makes up 15% of the economic output. (twi-global.com)
- [54][55] These are the top 50 countries by the total value of manufacturing output in US dollars for its noted year according to World Bank.[56] (en.wikipedia.org)
- You can multiply the result by 100 to get the total percent of monthly overhead. (investopedia.com)
- Many factories witnessed a 30% increase in output due to the shift to electric motors. (en.wikipedia.org)
- Job #1 is delivering the ordered product according to specifications: color, size, brand, and quantity. (netsuite.com)
External Links
How To
How to Use 5S for Increasing Productivity in Manufacturing
5S stands in for "Sort", the "Set In Order", "Standardize", or "Separate". Toyota Motor Corporation invented the 5S strategy in 1954. It allows companies to improve their work environment, thereby achieving greater efficiency.
The basic idea behind this method is to standardize production processes, so they become repeatable, measurable, and predictable. This means that tasks such as cleaning, sorting, storing, packing, and labeling are performed daily. Through these actions, workers can perform their jobs more efficiently because they know what to expect from them.
Implementing 5S involves five steps: Sort, Set in Order, Standardize Separate, Store, and Each step has a different action and leads to higher efficiency. If you sort items, it makes them easier to find later. When items are ordered, they are put together. Then, after you separate your inventory into groups, you store those groups in containers that are easy to access. Labeling your containers will ensure that everything is correctly labeled.
This requires employees to critically evaluate how they work. Employees should understand why they do the tasks they do, and then decide if there are better ways to accomplish them. They will need to develop new skills and techniques in order for the 5S system to be implemented.
In addition to increasing efficiency, the 5S method also improves morale and teamwork among employees. They feel more motivated to work towards achieving greater efficiency as they see the results.