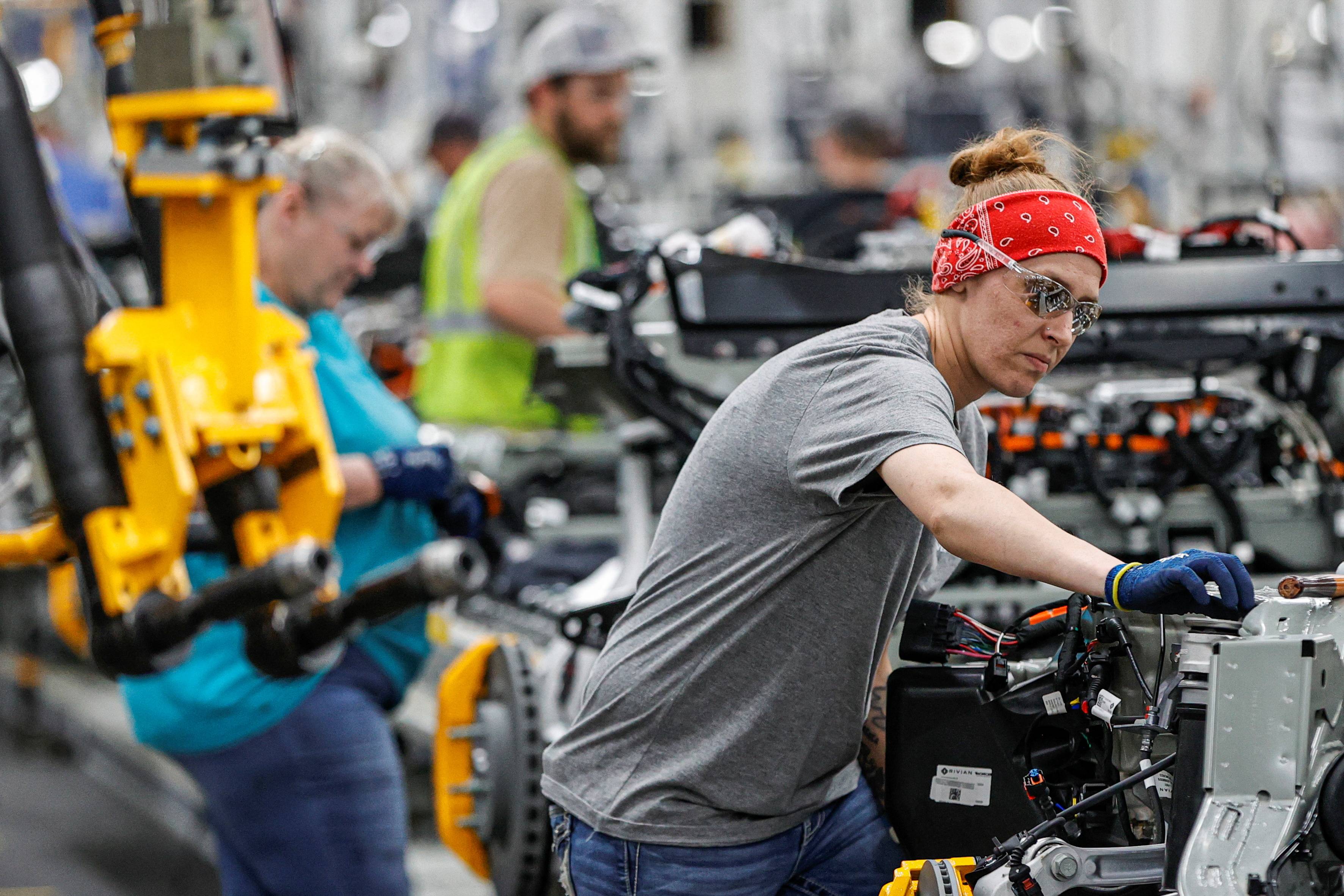
Houston offers many career opportunities in logistics. There are many job opportunities in this sector, including warehouse jobs, logistic coordinator jobs, and warehouse manager positions. If you are interested to work in the logistics industry you can sign-up for job alerts via email.
Interfaith ministries in Greater Houston
Interfaith Ministries in Greater Houston bring together people of different faith traditions to improve Houston's communities. These organizations offer services such as meals for homebound seniors, refugee services, and volunteering. They promote interfaith relationships and community partnerships. Interfaith Ministries Greater Houston exists to bring people with different faith traditions together in order to create bridges and understanding.
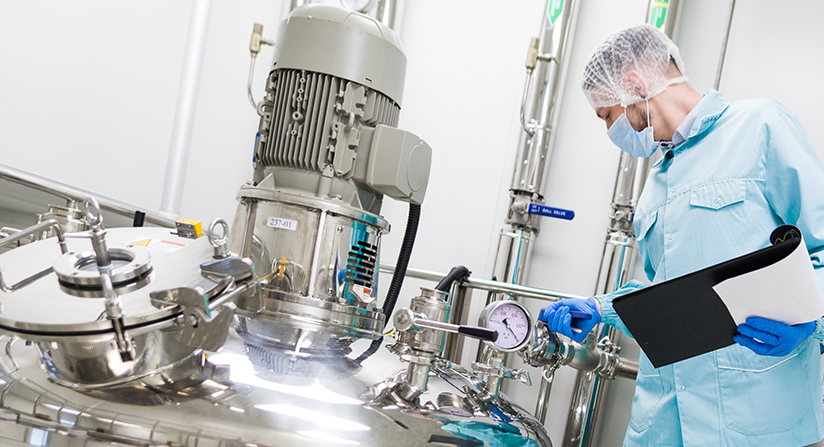
The organization was founded in 1955 as the Church Welfare Bureau, which organized the Protestant community to minister to the poor. The organization was reorganized under the name of Protestant Charities in 1964 and expanded to include Jewish people. Houston Metropolitan Ministries was established as the charter organization for Interfaith Ministries Greater Houston in 1969. Interfaith Ministries continues to serve the Houston community.
Interfaith Ministries Greater Houston offers refugee services to refugees fleeing persecution through the Refugee Services Program. This organization is a partner with Episcopal Migration Ministries, and the U.S. State Department in helping refugees settle in Houston. The program helps clients to become self-sufficient, productive members of their community in six months. Every year, this program aids hundreds of refugees.
Logistics careers
Houston logistics careers include jobs with logistics companies, manufacturing firms and third-party logistics businesses. These positions may be within a domestic organization or an international one. These professionals typically earn more than the national average and have many opportunities for advancement. High demand jobs for logistics professionals include those in government agencies and consulting companies. Students who have a degree in logistics can pursue many different career paths. This field has many advancement opportunities and great salaries.
For those interested in a career in logistics, Houston is a fantastic place to begin. Houston's expanding economy makes it an attractive place to live and work. The city offers a high salary and many top companies. If you are interested in international business, Houston logistics could be a good choice for you.
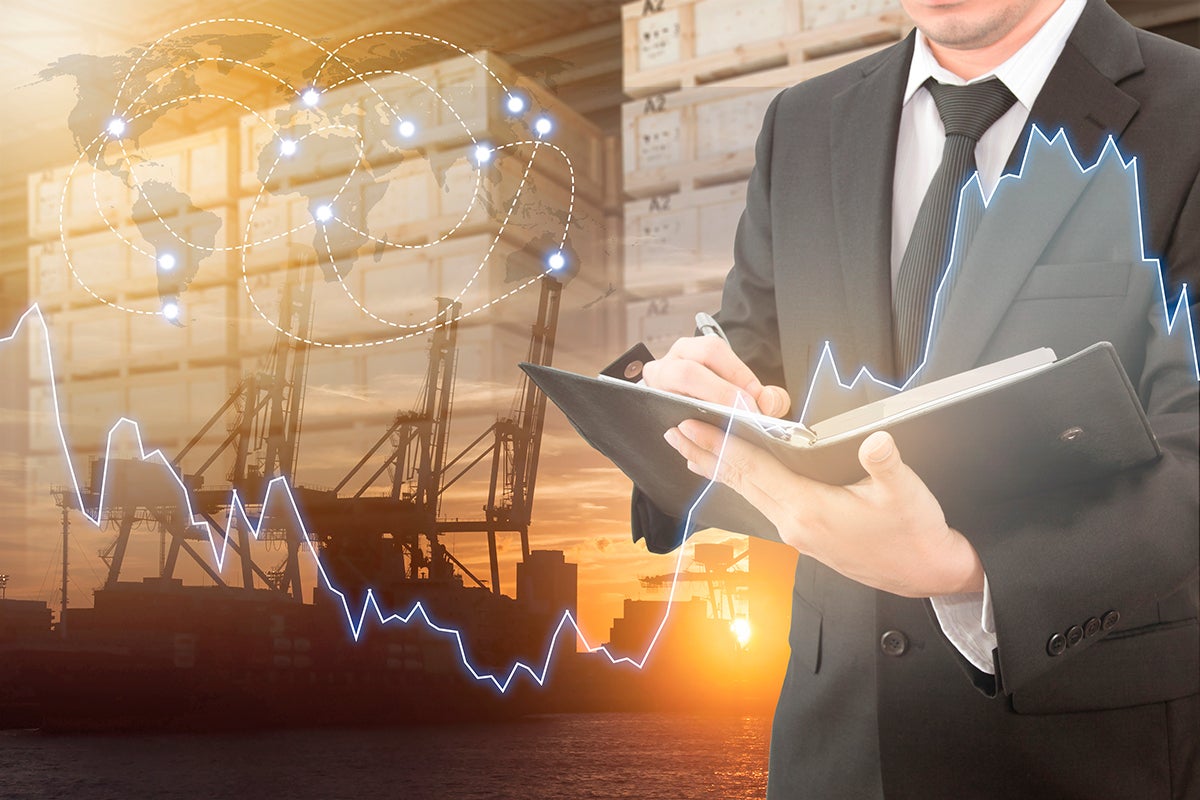
Job description
There are many opportunities available in Houston's logistics industry, whether you're looking to work full-time or part time. A career in logistics can be rewarding because there are so many local businesses. These positions include those in transport, manufacturing, and education. No matter your background, logistics jobs are great for those who want to advance their careers.
FAQ
What is production management?
Production Planning is the creation of a plan to cover all aspects, such as scheduling, budgeting. Location, crew, equipment, props and other details. This document ensures that everything is prepared and available when you are ready for shooting. This document should also include information on how to get the best result on set. This includes information on shooting times, locations, cast lists and crew details.
It is important to first outline the type of film you would like to make. You might have an idea of where you want to film, or you may have specific locations or sets in mind. Once you have identified your locations and scenes, you can start working out which elements you require for each scene. If you decide you need a car and don't know what model to choose, this could be an example. You could look online for cars to see what options are available, and then narrow down your choices by selecting between different makes or models.
Once you have found the right car, you can start thinking about extras. Are you looking for people to sit in the front seats? Perhaps you have someone who needs to be able to walk around the back of your car. You may want to change the interior's color from black or white. These questions will help to determine the style and feel of your car. Another thing you can do is think about what type of shots are desired. What type of shots will you choose? Maybe you want to show the engine and the steering wheel. These things will help you to identify the car that you are looking for.
Once you have made all the necessary decisions, you can start to create a schedule. You can create a schedule that will outline when you must start and finish your shoots. Every day will have a time for you to arrive at the location, leave when you are leaving and return home when you are done. This way, everyone knows what they need to do and when. Book extra staff ahead of time if you need them. There is no point in hiring someone who won't turn up because you didn't let him know.
When creating your schedule, you will also need to consider the number of days you need to film. Some projects are quick and easy, while others take weeks. While creating your schedule, it is important to remember whether you will require more than one shot per day. Multiple takes of the same location will lead to higher costs and take more time. If you are unsure if you need multiple takes, it is better to err on the side of caution and shoot fewer takes rather than risk wasting money.
Budgeting is another important aspect of production planning. As it will allow you and your team to work within your financial means, setting a realistic budget is crucial. It is possible to reduce the budget at any time if you experience unexpected problems. But, don't underestimate how much money you'll spend. If you underestimate how much something costs, you'll have less money to pay for other items.
Production planning can be a complex process. However, once you know how everything works together it will become easier to plan future projects.
How can manufacturing avoid production bottlenecks
You can avoid bottlenecks in production by making sure that everything runs smoothly throughout the production cycle, from the moment you receive an order to the moment the product is shipped.
This includes planning to meet capacity requirements and quality control.
Continuous improvement techniques like Six Sigma are the best way to achieve this.
Six Sigma management is a system that improves quality and reduces waste within your organization.
It's all about eliminating variation and creating consistency in work.
What are the 4 types of manufacturing?
Manufacturing is the process of transforming raw materials into useful products using machines and processes. Manufacturing involves many activities, including designing, building, testing and packaging, shipping, selling, service, and so on.
What is meant by manufacturing industries?
Manufacturing Industries are those businesses that make products for sale. These products are sold to consumers. These companies use a variety processes such as distribution, retailing and management to accomplish their purpose. They manufacture goods from raw materials using machines and other equipment. This includes all types of manufactured goods, including food items, clothing, building supplies, furniture, toys, electronics, tools, machinery, vehicles, pharmaceuticals, medical devices, chemicals, and many others.
What is the job of a manufacturer manager?
The manufacturing manager should ensure that every manufacturing process is efficient and effective. They should be alert for any potential problems in the company and react accordingly.
They should also be able and comfortable communicating with other departments like sales and marketing.
They must also keep up-to-date with the latest trends in their field and be able use this information to improve productivity and efficiency.
What are the 7 Rs of logistics?
The 7R's of Logistics is an acronym for the seven basic principles of logistics management. It was created by the International Association of Business Logisticians and published in 2004 under its "Seven Principles of Logistics Management".
The acronym is made up of the following letters:
-
Responsible - to ensure that all actions are within the legal requirements and are not detrimental to others.
-
Reliable – have faith in your ability and capability to keep promises.
-
Reasonable - use resources efficiently and don't waste them.
-
Realistic - Consider all aspects of operations, including environmental impact and cost effectiveness.
-
Respectful - show respect and treat others fairly and fairly
-
Resourceful - look for opportunities to save money and increase productivity.
-
Recognizable: Provide customers with value-added service
What does it take for a logistics enterprise to succeed?
To be a successful businessman in logistics, you will need many skills and knowledge. To communicate effectively with clients and suppliers, you must be able to communicate well. You should be able analyse data and draw inferences. You must be able manage stress and pressure under pressure. You need to be innovative and creative to come up with new ways to increase efficiency. You need to have strong leadership qualities to motivate team members and direct them towards achieving organizational goals.
You should also be organized and efficient to meet tight deadlines.
Statistics
- In the United States, for example, manufacturing makes up 15% of the economic output. (twi-global.com)
- According to the United Nations Industrial Development Organization (UNIDO), China is the top manufacturer worldwide by 2019 output, producing 28.7% of the total global manufacturing output, followed by the United States, Japan, Germany, and India.[52][53] (en.wikipedia.org)
- In 2021, an estimated 12.1 million Americans work in the manufacturing sector.6 (investopedia.com)
- According to a Statista study, U.S. businesses spent $1.63 trillion on logistics in 2019, moving goods from origin to end user through various supply chain network segments. (netsuite.com)
- [54][55] These are the top 50 countries by the total value of manufacturing output in US dollars for its noted year according to World Bank.[56] (en.wikipedia.org)
External Links
How To
How to Use the Just-In-Time Method in Production
Just-in-time (JIT) is a method that is used to reduce costs and maximize efficiency in business processes. It allows you to get the right amount resources at the right time. This means that your only pay for the resources you actually use. Frederick Taylor developed the concept while working as foreman in early 1900s. He observed how workers were paid overtime if there were delays in their work. He realized that workers should have enough time to complete their jobs before they begin work. This would help increase productivity.
JIT is about planning ahead. You should have all the necessary resources ready to go so that you don’t waste money. Look at your entire project, from start to end. Make sure you have enough resources in place to deal with any unexpected problems. You can anticipate problems and have enough equipment and people available to fix them. This will ensure that you don't spend more money on things that aren't necessary.
There are many JIT methods.
-
Demand-driven JIT: This is a JIT that allows you to regularly order the parts/materials necessary for your project. This will let you track the amount of material left over after you've used it. This will allow you to calculate how long it will take to make more.
-
Inventory-based: This type allows you to stock the materials needed for your projects ahead of time. This allows for you to anticipate how much you can sell.
-
Project-driven: This method allows you to set aside enough funds for your project. If you know the amount you require, you can buy the materials you need.
-
Resource-based: This is the most common form of JIT. This is where you assign resources based upon demand. You might assign more people to help with orders if there are many. If you don't have many orders, you'll assign fewer people to handle the workload.
-
Cost-based: This approach is very similar to resource-based. However, you don't just care about the number of people you have; you also need to consider how much each person will cost.
-
Price-based: This is similar to cost-based but instead of looking at individual workers' salaries, you look at the total company price.
-
Material-based: This is quite similar to cost-based, but instead of looking at the total cost of the company, you're concerned with how much raw materials you spend on average.
-
Time-based: This is another variation of resource-based JIT. Instead of focusing on the cost of each employee, you will focus on the time it takes to complete a project.
-
Quality-based JIT is another variant of resource-based JIT. Instead of looking at the labor costs and time it takes to make a product, think about its quality.
-
Value-based JIT : This is the newest type of JIT. In this instance, you are not concerned about the product's performance or meeting customer expectations. Instead, you're focused on how much value you add to the market.
-
Stock-based. This method is inventory-based and focuses only on the actual production at any given point. It's used when you want to maximize production while minimizing inventory.
-
Just-in-time planning (JIT): This is a combination JIT and supply-chain management. This refers to the scheduling of the delivery of components as soon after they are ordered. It reduces lead times and improves throughput.