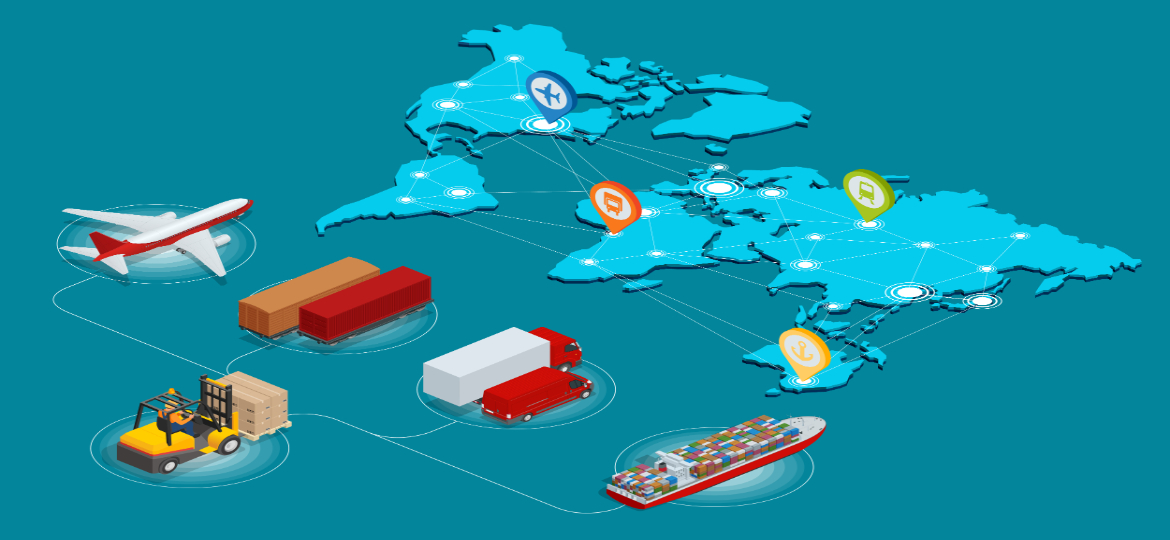
You need to be familiar with the five s's to make your manufacturing process a lean machine. These are Standardize. Here are some steps you should follow. You must train your team leaders and frontline operators to maximize your lean transformation.
Standardize
Clean and organize your workspace is the first step in the 5S process. This may be a one-time job, but if you standardize the process, it can become a routine. To ensure a consistent approach to 5S tasks, you can use visual cues, checklist templates, and checklists.
These five s's can help your workplace be more productive and efficient. This will encourage staff to be more organized and streamline their work. By organizing and cleaning up your workspace, you can improve efficiency. You can improve safety in your workplace by using the five s’s of lean. An organized workspace can prevent accidents and reduce the chances of making mistakes. It will also increase productivity.
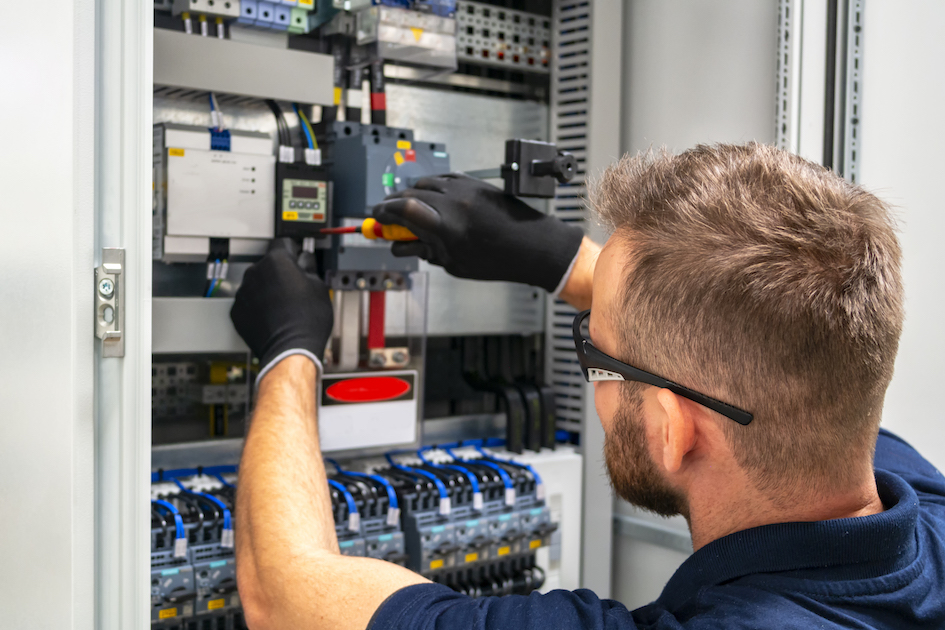
Straighten
It doesn't need to be hard to get your 5 s's in order. Businesses can improve their business processes if they follow lean principles. Workers will be able find the parts they need faster if the components are organized in an assembly plant. This will save time searching for the wrong parts and reduce company safety.
You can also reduce the amount of items that are in each work area and save money on consumables. This can help you reduce your office supply bills. Straightening work cells can not only help you save money, but it will also improve your production processes and increase quality, safety, standard work, and efficiency.
Shine
Shine involves inspecting and identifying problems in the workspace. By examining equipment and tools, Shine helps to improve flow and reduce waste. Shine helps workers identify potential problems before they hamper production. Shine can also be used to standardize a workspace to improve output.
Shine is a tool that can be used to lean manufacturing. This technique is designed to automate and streamline work processes, reduce waste, and increase efficiency. It can be applied in any industry including manufacturing. It applies the 5S principles in a business. It assists companies in reducing inventory, work-in progress, and stock.
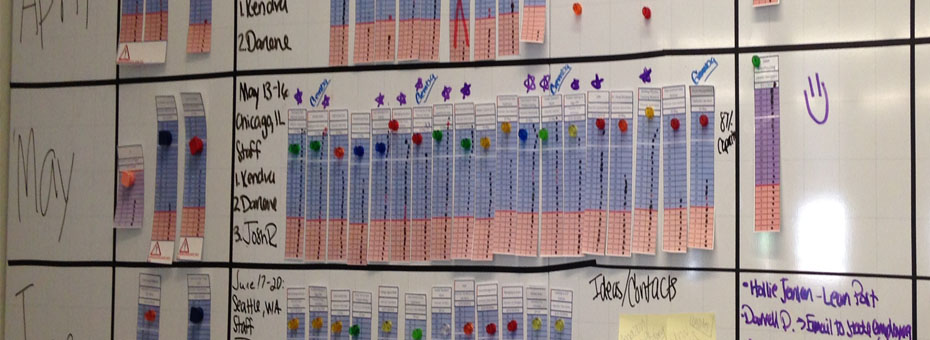
Continue to Sustain
To sustain the 5 s's, a facility must be re-introduced to a standard system. This is an ongoing process and should be repeated in order to make sure that the facility runs at its best. This is why employees need to be trained in 5S auditing.
The 5S approach focuses on reducing waste and optimizing productivity while maintaining a clean and orderly workplace. It is a method of organizing workplaces that follows the five principles outlined in the Toyota Production System. Hiroyuki Hirano developed it in Japan post-war to improve the efficiency of manufacturing facilities.
FAQ
How does manufacturing avoid bottlenecks in production?
Avoiding production bottlenecks is as simple as keeping all processes running smoothly, from the time an order is received until the product ships.
This includes both quality control and capacity planning.
The best way to do this is to use continuous improvement techniques such as Six Sigma.
Six Sigma Management System is a method to increase quality and reduce waste throughout your organization.
It is focused on creating consistency and eliminating variation in your work.
Is automation necessary in manufacturing?
Not only are service providers and manufacturers important, but so is automation. It enables them to provide services faster and more efficiently. It helps them to lower costs by reducing human errors, and improving productivity.
What makes a production planner different from a project manger?
A production planner is more involved in the planning phase of the project than a project manger.
How can excess manufacturing production be reduced?
In order to reduce excess production, you need to develop better inventory management methods. This would reduce time spent on activities such as purchasing, stocking, and maintaining excess stock. By doing this, we could free up resources for other productive tasks.
This can be done by using a Kanban system. A Kanbanboard is a visual tool that allows you to keep track of the work being done. In a Kanban system, work items move through a sequence of states until they reach their final destination. Each state represents a different priority level.
If work is moving from one stage to the other, then the current task can be completed and moved on to the next. But if a task remains in the beginning stages it will stay that way until it reaches its end.
This keeps work moving and ensures no work is lost. Managers can see how much work has been done and the status of each task at any time with a Kanban Board. This allows them to adjust their workflows based on real-time information.
Lean manufacturing, another method to control inventory levels, is also an option. Lean manufacturing seeks to eliminate waste from every step of the production cycle. Anything that does not contribute to the product's value is considered waste. The following are examples of common waste types:
-
Overproduction
-
Inventory
-
Unnecessary packaging
-
Overstock materials
These ideas can help manufacturers improve efficiency and reduce costs.
What is the responsibility of a manufacturing manager?
A manufacturing manager must ensure that all manufacturing processes are efficient and effective. They should be alert for any potential problems in the company and react accordingly.
They should also learn how to communicate effectively with other departments, including sales and marketing.
They should be up to date on the latest trends and be able apply this knowledge to increase productivity and efficiency.
How can I learn about manufacturing?
Hands-on experience is the best way to learn more about manufacturing. You can read books, or watch instructional videos if you don't have the opportunity to do so.
Statistics
- [54][55] These are the top 50 countries by the total value of manufacturing output in US dollars for its noted year according to World Bank.[56] (en.wikipedia.org)
- According to the United Nations Industrial Development Organization (UNIDO), China is the top manufacturer worldwide by 2019 output, producing 28.7% of the total global manufacturing output, followed by the United States, Japan, Germany, and India.[52][53] (en.wikipedia.org)
- In the United States, for example, manufacturing makes up 15% of the economic output. (twi-global.com)
- You can multiply the result by 100 to get the total percent of monthly overhead. (investopedia.com)
- Job #1 is delivering the ordered product according to specifications: color, size, brand, and quantity. (netsuite.com)
External Links
How To
How to use 5S to increase Productivity in Manufacturing
5S stands for "Sort", "Set In Order", "Standardize", "Separate" and "Store". Toyota Motor Corporation was the first to develop the 5S approach in 1954. This methodology helps companies improve their work environment to increase efficiency.
The idea behind standardizing production processes is to make them repeatable and measurable. This means that tasks such as cleaning, sorting, storing, packing, and labeling are performed daily. These actions allow workers to perform their job more efficiently, knowing what to expect.
Implementing 5S requires five steps. These are Sort, Set In Order, Standardize. Separate. And Store. Each step is a different action that leads to greater efficiency. If you sort items, it makes them easier to find later. When items are ordered, they are put together. Once you have separated your inventory into groups and organized them, you will store these groups in easily accessible containers. Labeling your containers will ensure that everything is correctly labeled.
This process requires employees to think critically about how they do their job. Employees should understand why they do the tasks they do, and then decide if there are better ways to accomplish them. To implement the 5S system, employees must acquire new skills and techniques.
The 5S method increases efficiency and morale among employees. They feel more motivated to work towards achieving greater efficiency as they see the results.