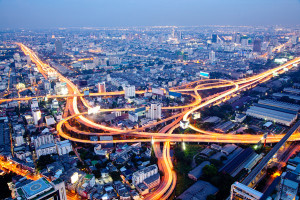
They are responsible for analysing process data and offering technical support to maintenance staff. They can also help with short-term planning and system improvements.
This profession is growing in popularity. A mechanic should be able communicate with customers and share his or her knowledge. The skills that are essential for this job include knowledge of technical language, strong time management abilities, and the ability to work in a team.
These engineers also have the technical skills needed to work in sales and marketing, and have the ability to manage and troubleshoot problems. As demand grows for more efficient machinery, so does the expectation of these professionals to deliver high-quality work.
This field requires a high level of education. Mechanical engineers need to learn the science behind designing and producing products in order to reach this goal. In the field of heat engineering they study heat flow in structures. The design of equipment for transport and air conditioning is another aspect of heat engineering.
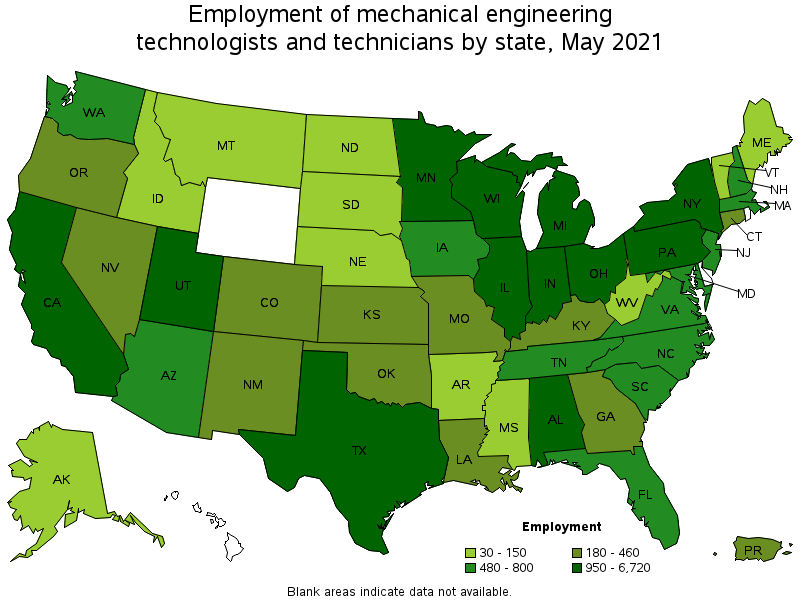
Mechanical engineers have been at the forefront technology for a long time. Mechanical engineers are now able to design new materials and designs for smaller machines. A further advantage is the ability to use nanotechnology for designing at the smallest scale. Composites allow mechanics to combine various materials into one product.
These professionals use rationalized design and manufacturing methods. Value engineering is one of these methods. It seeks to maximize the use of resources. Another approach is operations research.
Mechanics are always looking for jobs. Many aspire to establish business exchanges with foreigners. To secure a job overseas, they must be able demonstrate good English skills.
It is important that you have a broad vocabulary. A mechanic can improve his English skills by attending industry events, and reading English-language magazines. To improve their skills, they can also enroll in an online course.
These skills are not enough. Mechanical technicians must also be able manage their time. Two years experience is required for mechanical technicians. They should possess excellent analytical and critical skills, as well the ability to use diagnostic software.
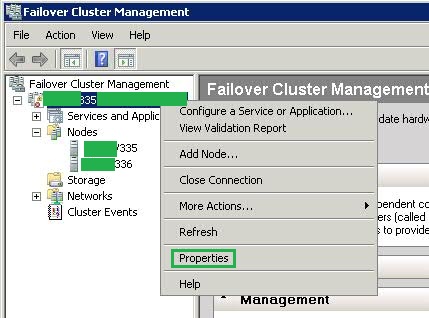
It is important to be able to use computers effectively in order to pursue a career as a computer-aided designer. It is also a good idea if you have an associate's in mechanical engineering technology.
These specialists assist craftsmen by analyzing process data, assisting them with their daily management, and providing technical leadership to employees. They are also able to solve problems that recur.
Mechanical engineers work closely with civil engineers, electrical engineers, and chemical engineers in order to improve the performance of vehicles, equipment and systems. They also participate in research, design, and construction. Many mechanical engineers are employed full-time.
FAQ
What are the four types in manufacturing?
Manufacturing is the process by which raw materials are transformed into useful products through machines and processes. It can involve many activities like designing, manufacturing, testing packaging, shipping, selling and servicing.
Can certain manufacturing steps be automated?
Yes! Yes! Automation has existed since ancient times. The Egyptians discovered the wheel thousands and years ago. Today, robots assist in the assembly of lines.
There are many uses of robotics today in manufacturing. These include:
-
Line robots
-
Robot welding
-
Robot painting
-
Robotics inspection
-
Robots that create products
There are many other examples of how manufacturing could benefit from automation. 3D printing makes it possible to produce custom products in a matter of days or weeks.
What is the difference between Production Planning and Scheduling?
Production Planning (PP) is the process of determining what needs to be produced at any given point in time. This is done through forecasting demand and identifying production capacities.
Scheduling refers the process by which tasks are assigned dates so that they can all be completed within the given timeframe.
How can I find out more about manufacturing?
Practical experience is the best way of learning about manufacturing. But if that is not possible you can always read books and watch educational videos.
What type of jobs is there in logistics
There are different kinds of jobs available in logistics. Here are some examples:
-
Warehouse workers - They load and unload trucks and pallets.
-
Transportation drivers: They drive trucks and trailers and deliver goods and make pick-ups.
-
Freight handlers: They sort and package freight in warehouses.
-
Inventory managers – They manage the inventory in warehouses.
-
Sales representatives: They sell products to customers.
-
Logistics coordinators – They plan and coordinate logistics operations.
-
Purchasing agents are those who purchase goods and services for the company.
-
Customer service representatives are available to answer customer calls and emails.
-
Shipping clerks - They process shipping orders and issue bills.
-
Order fillers - They fill orders based on what is ordered and shipped.
-
Quality control inspectors – They inspect incoming and outgoing products to ensure that there are no defects.
-
Others - There are many other types of jobs available in logistics, such as transportation supervisors, cargo specialists, etc.
How can efficiency in manufacturing be improved?
First, identify the factors that affect production time. The next step is to identify the most important factors that affect production time. If you don’t know how to start, look at which factors have the greatest impact upon production time. Once you have identified them, it is time to identify solutions.
Statistics
- According to a Statista study, U.S. businesses spent $1.63 trillion on logistics in 2019, moving goods from origin to end user through various supply chain network segments. (netsuite.com)
- In 2021, an estimated 12.1 million Americans work in the manufacturing sector.6 (investopedia.com)
- Job #1 is delivering the ordered product according to specifications: color, size, brand, and quantity. (netsuite.com)
- It's estimated that 10.8% of the U.S. GDP in 2020 was contributed to manufacturing. (investopedia.com)
- In the United States, for example, manufacturing makes up 15% of the economic output. (twi-global.com)
External Links
How To
How to use the Just In-Time Production Method
Just-in-time (JIT) is a method that is used to reduce costs and maximize efficiency in business processes. This is where you have the right resources at the right time. This means you only pay what you use. The term was first coined by Frederick Taylor, who developed his theory while working as a foreman in the early 1900s. Taylor observed that overtime was paid to workers if they were late in working. He concluded that if workers were given enough time before they start work, productivity would increase.
JIT is a way to plan ahead and make sure you don't waste any money. Also, you should look at the whole project from start-to-finish and make sure you have the resources necessary to address any issues. If you anticipate that there might be problems, you'll have enough people and equipment to fix them. This will ensure that you don't spend more money on things that aren't necessary.
There are many JIT methods.
-
Demand-driven: This type of JIT allows you to order the parts/materials required for your project on a regular basis. This will enable you to keep track of how much material is left after you use it. You'll also be able to estimate how long it will take to produce more.
-
Inventory-based: This is a type where you stock the materials required for your projects in advance. This allows you predict the amount you can expect to sell.
-
Project-driven: This is an approach where you set aside enough funds to cover the cost of your project. Once you have an idea of how much material you will need, you can purchase the necessary materials.
-
Resource-based JIT: This type of JIT is most commonly used. Here you can allocate certain resources based purely on demand. You might assign more people to help with orders if there are many. If you don't have many orders, you'll assign fewer people to handle the workload.
-
Cost-based: This approach is very similar to resource-based. However, you don't just care about the number of people you have; you also need to consider how much each person will cost.
-
Price-based: This is very similar to cost-based, except that instead of looking at how much each individual worker costs, you look at the overall price of the company.
-
Material-based: This approach is similar to cost-based. However, instead of looking at the total cost for the company, you look at how much you spend on average on raw materials.
-
Time-based JIT is another form of resource-based JIT. Instead of worrying about how much each worker costs, you can focus on how long the project takes.
-
Quality-based JIT: This is another variation of resource based JIT. Instead of thinking about how much each employee costs or how long it takes to manufacture something, you think about how good the quality of your product is.
-
Value-based JIT is the newest form of JIT. In this case, you're not concerned with how well the products perform or whether they meet customer expectations. Instead, you are focused on adding value to the marketplace.
-
Stock-based: This stock-based method focuses on the actual quantity of products being made at any given time. This method is useful when you want to increase production while decreasing inventory.
-
Just-intime (JIT), planning is a combination JIT management and supply chain management. This refers to the scheduling of the delivery of components as soon after they are ordered. It's important because it reduces lead times and increases throughput.