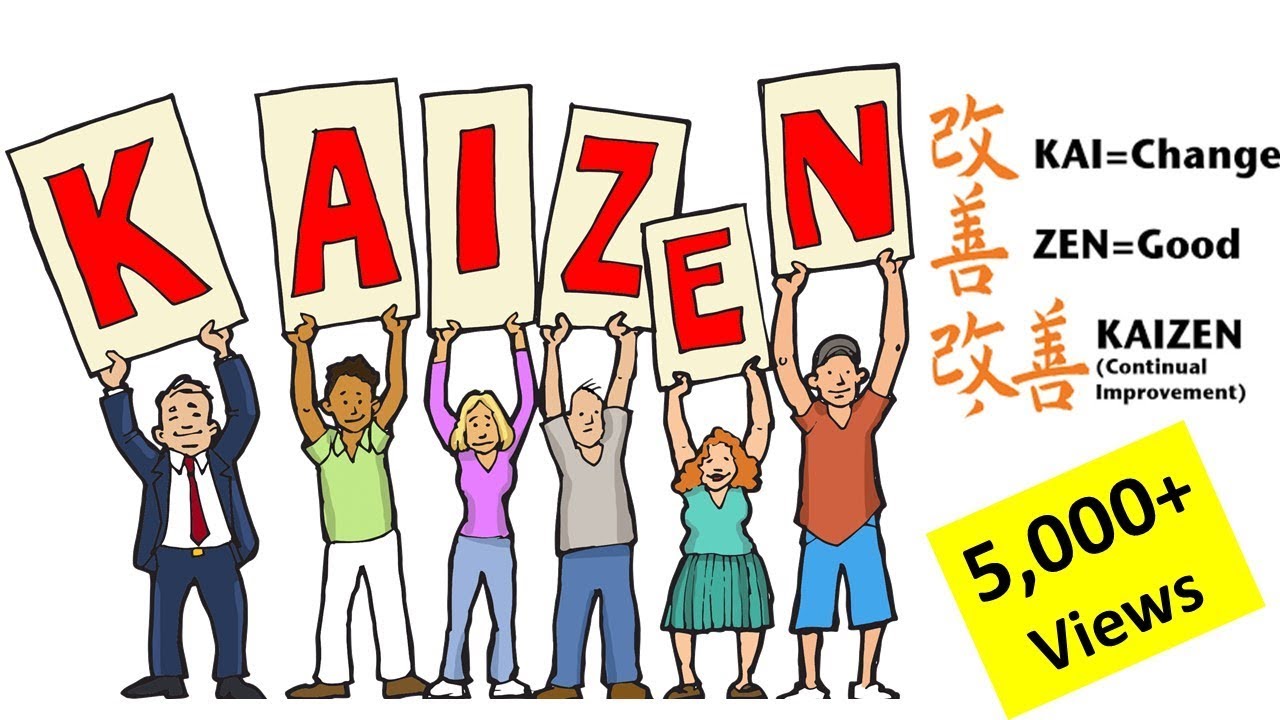
There are a wide variety of logistics jobs in Tampa. Many of these jobs are in the manufacturing, construction or healthcare industries. However you can work in the wholesale trading industry, consulting firms, or other businesses that streamline supply chains.
A degree in Logistics can lead to a variety of career options. Associate degrees can lead to entry-level jobs such as shipping clerks, but bachelor's degree holders are more likely to find higher paying positions. You may decide to specialize in one area of logistic, such as warehouse management or supply chain.
BLS data indicates that career opportunities in logistics are growing. The BLS predicts employment growth for this profession of 5% from 2018 to 2028. Job growth will be even more pronounced for those who concentrate on business operations.
You can get a logistics degree either at a 4-year university or a community-college. These programs offer a variety of logistics concentrations so that you can develop specialized skills as you progress up the career ladder.
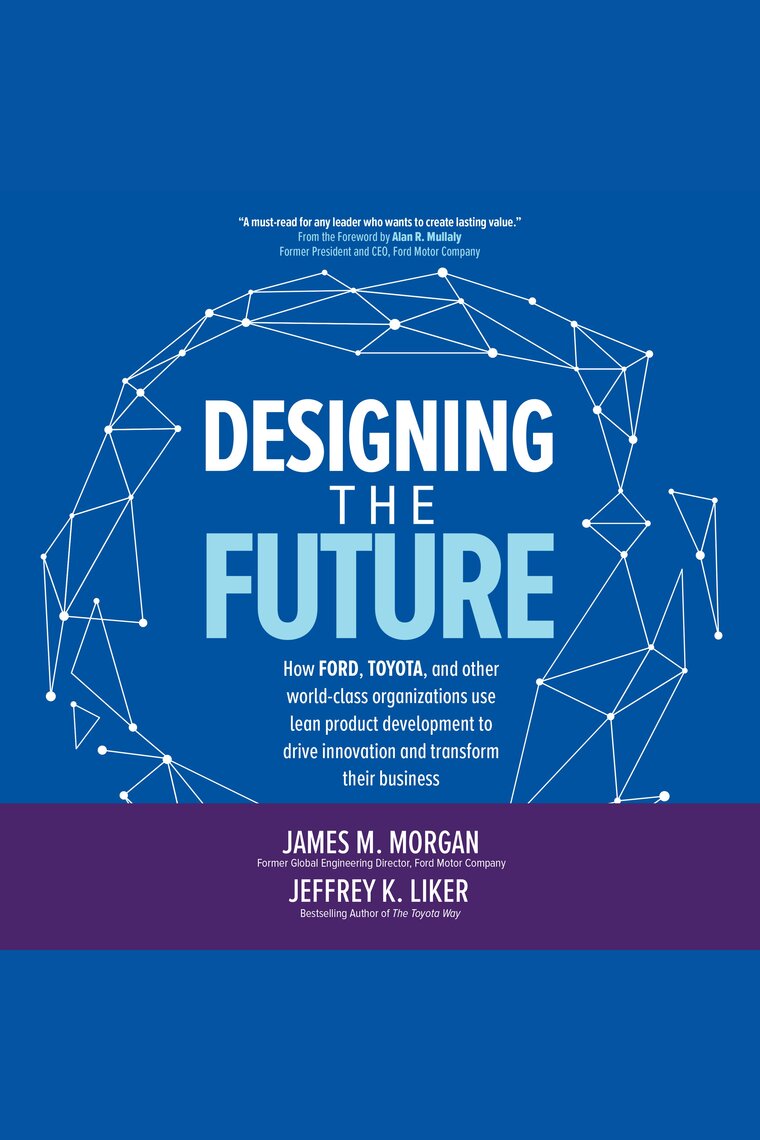
As well as pursuing their bachelor's degrees, students are encouraged to take advantage of internships and networking events. These experiences can provide you with valuable, hands-on work experience. They can also help you find a logistics job.
The logistics sector has a diverse work force, and the job prospects are usually good. Logistics jobs are available throughout the United States, but especially in growing and large states such as California and Texas. Careers are available in several specific sectors, including aerospace and oil & gas.
Consider the size and capability of a company when selecting a logistics service. You should choose a 3PL who understands your business, and can provide you with a tailored solution that meets your needs. You can reduce your costs and improve your efficiency.
Your business's supply chain plays a vital role in the success of its operations. The right people and tools are needed to make sure that your products reach their destination at the right time and in the best condition. Choose a third-party logistic provider with expertise in your field and the ability to deliver goods on schedule, every time.
Sheer is a Tampa based full-service 3PL. We can help you improve your supply chain's speed and efficiency while lowering costs. We offer a wide range of services for our customers including transportation, shipping, and inventory management.
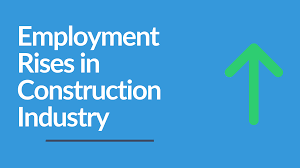
Our suite of tools will also help you to track and manage the supply chain. We offer a suite of cloud-based systems that integrate with your existing ERP system, making it easy to monitor and control all aspects of your business.
Sheer’s multimodal freight networks can turn your supply chain around from a liability into an asset. You can count on Sheer to deliver your goods safely, on time and every time.
FAQ
What are manufacturing and logistic?
Manufacturing is the act of producing goods from raw materials using machines and processes. Logistics encompasses the management of all aspects associated with supply chain activities such as procurement, production planning, distribution and inventory control. It also includes customer service. Sometimes manufacturing and logistics are combined to refer to a wider term that includes both the process of creating products as well as their delivery to customers.
What does it take to run a logistics business?
You need to have a lot of knowledge and skills to manage a successful logistic business. To communicate effectively with clients and suppliers, you must be able to communicate well. You must be able analyze data and draw out conclusions. You need to be able work under pressure and manage stressful situations. You need to be innovative and creative to come up with new ways to increase efficiency. You need to have strong leadership qualities to motivate team members and direct them towards achieving organizational goals.
You must be organized to meet tight deadlines.
What is the difference between a production planner and a project manager?
A production planner is more involved in the planning phase of the project than a project manger.
What is the role of a logistics manager
Logistics managers are responsible for ensuring that all goods arrive in perfect condition and on time. This is achieved by using their knowledge and experience with the products of the company. He/she also needs to ensure adequate stock to meet demand.
How can overproduction in manufacturing be reduced?
Improved inventory management is the key to reducing overproduction. This would reduce time spent on activities such as purchasing, stocking, and maintaining excess stock. This would allow us to use our resources for more productive tasks.
Kanban systems are one way to achieve this. A Kanban board, a visual display to show the progress of work, is called a Kanban board. In a Kanban system, work items move through a sequence of states until they reach their final destination. Each state represents a different priority.
For instance, when work moves from one stage to another, the current task is complete enough to be moved to the next stage. If a task is still in its beginning stages, it will continue to be so until it reaches the end.
This helps to keep work moving forward while ensuring that no work is left behind. Managers can view the Kanban board to see how much work they have done. This data allows them adjust their workflow based upon real-time data.
Lean manufacturing, another method to control inventory levels, is also an option. Lean manufacturing focuses on eliminating waste throughout the entire production chain. Waste includes anything that does not add value to the product. Some common types of waste include:
-
Overproduction
-
Inventory
-
Unnecessary packaging
-
Excess materials
Manufacturers can increase efficiency and decrease costs by implementing these ideas.
What is the role of a production manager?
Production planners make sure that every aspect of the project is delivered on-time, within budget, and within schedule. A production planner ensures that the service and product meet the client's expectations.
Statistics
- According to the United Nations Industrial Development Organization (UNIDO), China is the top manufacturer worldwide by 2019 output, producing 28.7% of the total global manufacturing output, followed by the United States, Japan, Germany, and India.[52][53] (en.wikipedia.org)
- [54][55] These are the top 50 countries by the total value of manufacturing output in US dollars for its noted year according to World Bank.[56] (en.wikipedia.org)
- Job #1 is delivering the ordered product according to specifications: color, size, brand, and quantity. (netsuite.com)
- (2:04) MTO is a production technique wherein products are customized according to customer specifications, and production only starts after an order is received. (oracle.com)
- Many factories witnessed a 30% increase in output due to the shift to electric motors. (en.wikipedia.org)
External Links
How To
Six Sigma in Manufacturing
Six Sigma is defined as "the application of statistical process control (SPC) techniques to achieve continuous improvement." Motorola's Quality Improvement Department in Tokyo, Japan developed Six Sigma in 1986. The basic idea behind Six Sigma is to improve quality by improving processes through standardization and eliminating defects. This method has been adopted by many companies in recent years as they believe there are no perfect products or services. Six Sigma seeks to reduce variation between the mean production value. If you take a sample and compare it with the average, you will be able to determine how much of the production process is different from the norm. If it is too large, it means that there are problems.
Understanding the dynamics of variability within your business is the first step in Six Sigma. Once you understand this, you can then identify the causes of variation. You'll also want to determine whether these variations are random or systematic. Random variations occur when people do mistakes. Symmetrical variations are caused due to factors beyond the process. Random variations would include, for example, the failure of some widgets to fall from the assembly line. But if you notice that every widget you make falls apart at the exact same place each time, this would indicate that there is a problem.
Once you identify the problem areas, it is time to create solutions. It might mean changing the way you do business or redesigning it entirely. Once you have implemented the changes, it is important to test them again to ensure they work. If they don't work, you will need to go back to the drawing boards and create a new plan.