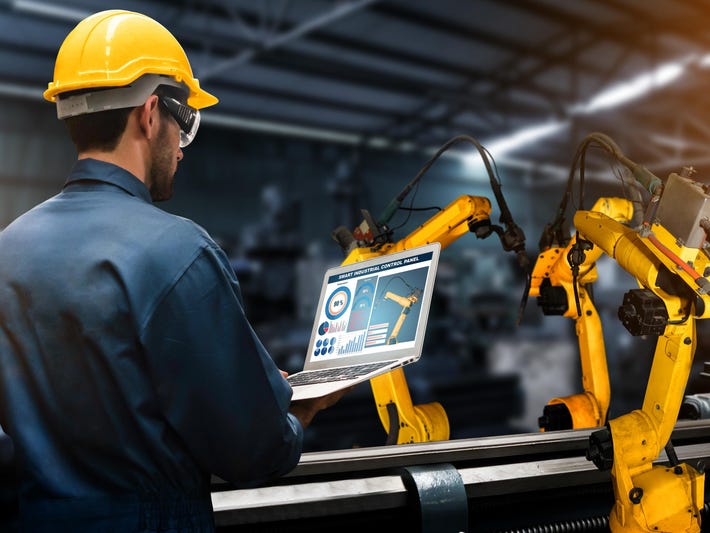
An industrial engineer's job is to optimize resource usage and reduce waste. These engineers work in diverse industries to help companies design efficient processes. They examine production schedules, design specifications, and workflows to create more efficient processes for the company. To make the company more profitable, industrial engineers analyze production processes and provide recommendations. They can also improve the overall quality and value of products and services.
Industrial engineers need to be employed
An Industrial Engineer is an essential role in a manufacturing company. He or she uses innovative design systems for efficient operations in the natural and organic food sectors. This individual develops innovative solutions for internal customers and manages dynamic projects to improve the manufacturing process. To qualify for this job, an individual must be qualified and able to perform all essential duties satisfactorily. Industrial engineers must be familiar with AutoCAD and Pro-E, and they must be knowledgeable of advanced product quality planning and the production part approval process.
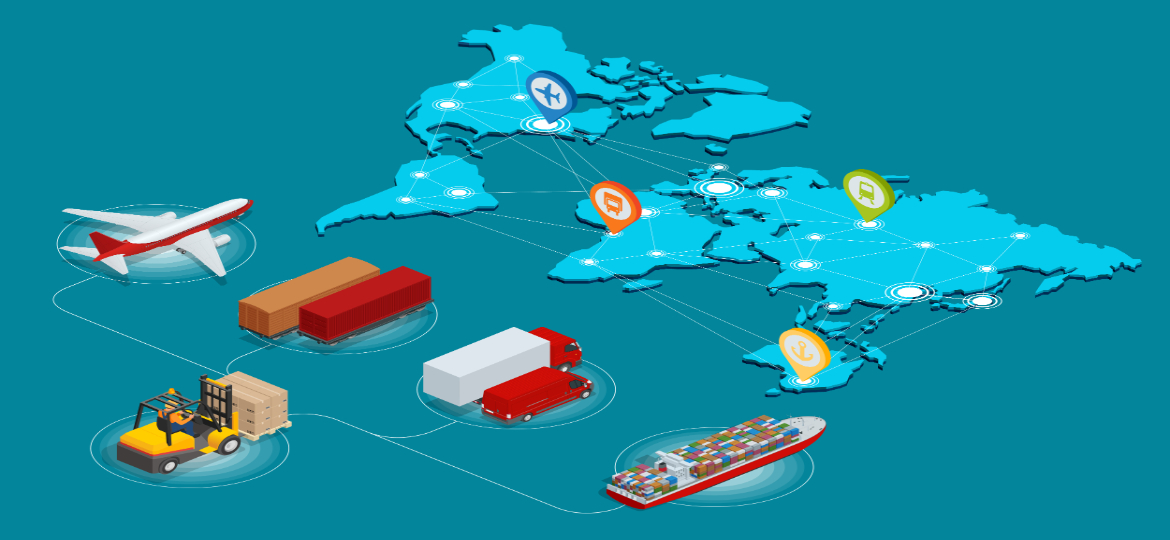
Industrial Engineers work on optimizing efficiency through the design and testing of integrated systems. This job is not limited to this. It also includes studying human work factors to increase product quality and efficiency. Other responsibilities include cost analysis and guest coordination. Additionally, the person must have advanced technical skills like Microsoft Office. Also required is experience in manufacturing, logistics, systems design. In Orlando, you must have the technical skills necessary to perform your job well.
Industrial engineer salary
The salaries in Orlando are a good place to start if you're thinking about a career as an Industrial & Manufacturing Engineer. Orlando has a $80,325 average annual salary, making it one of the most desirable places to live. This is 6% less than the national average and 9% below the New York, NY average. The salary range in Orlando is between $64,260 and $96,390, with the middle 67% earning $85,000 per year and the top ten percent earning $102,000.
Industrial Engineers can earn salaries ranging from $89,700 to $114,300 USD. Industrial engineers can earn a variety of salaries, just like other careers. These figures are based upon the average salary of an Industrial Engineer with 5-10 years experience. However, those with more experience can expect to earn almost twice the salary as those without. Different industrial engineers have different pay scales.
Industrial engineer responsibilities
This position will allow you to determine the best process design and implement strategies to improve your processes. It is your responsibility to develop and implement flexible, efficient and effective processes that meet customer requirements and goals. The Industrial Engineer is responsible for many tasks such as Process Improvement, Capacity Planning and Reporting, Cost Analysis, Data Analysis, Capital Project Management and Discrete Events Simulation. Additionally, you will be required to perform time studies and observations as well as assist in the development of cross-functional improvement initiatives.
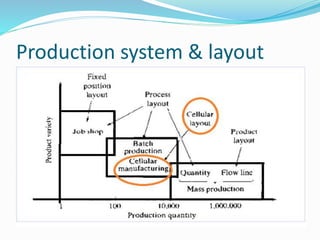
Strong communication skills are required, as well as engineering experience and a strong grasp of statistical analysis, to be able do this job. Industrial engineers will work closely with management to develop design standards and lead moderately complex industrial engineering projects. They will create statistical reports and analyze data to improve process flow, quality, and standard time. They will coordinate key research and produce key metrics reports.
FAQ
What is production planning?
Production planning is the process of creating a plan that covers all aspects of production. This includes scheduling, budgeting and crew, location, equipment, props, and more. This document aims to ensure that everything is planned and ready when you are ready to shoot. It should also contain information on achieving the best results on set. This information includes locations, crew details and equipment requirements.
The first step in filming is to define what you want. You may have decided where to shoot or even specific locations you want to use. Once you have identified the scenes and locations, you can start to determine which elements are required for each scene. Perhaps you have decided that you need to buy a car but aren't sure which model. To narrow your options, you can search online for available models.
After you have chosen the right car, you will be able to begin thinking about accessories. Do you need people sitting in the front seats? Maybe you need someone to move around in the back. You may want to change the interior's color from black or white. These questions will help determine the look and feel you want for your car. The type of shots that you are looking for is another thing to consider. What type of shots will you choose? Perhaps you want to show the engine or the steering wheel? These things will help you to identify the car that you are looking for.
Once you have established all the details, you can create a schedule. You can create a schedule that will outline when you must start and finish your shoots. Each day will include the time when you need to arrive at the location, when you need to leave and when you need to return home. This way, everyone knows what they need to do and when. It is possible to make arrangements in advance for additional staff if you are looking to hire. You should not hire anyone who doesn't show up because of your inaction.
You will need to factor in the days that you have to film when creating your schedule. Some projects take only a few days while others can last several weeks. It is important to consider whether you require more than one photo per day when you create your schedule. Shooting multiple takes over the same location will increase costs and take longer to complete. It's better to be safe than sorry and shoot less takes if you're not certain whether you need more takes.
Budgeting is another important aspect of production planning. You will be able to manage your resources if you have a realistic budget. Keep in mind that you can always reduce your budget if you face unexpected difficulties. However, it is important not to overestimate the amount that you will spend. You'll end up with less money after paying for other things if the cost is underestimated.
Production planning is a complicated process. But once you understand how everything works together, it becomes much easier to plan future project.
Can certain manufacturing steps be automated?
Yes! Since ancient times, automation has been in existence. The Egyptians invent the wheel thousands of year ago. Today, robots assist in the assembly of lines.
Actually, robotics can be used in manufacturing for many purposes. These include:
-
Robots for assembly line
-
Robot welding
-
Robot painting
-
Robotics inspection
-
Robots that create products
Manufacturing can also be automated in many other ways. For instance, 3D printing allows us make custom products and not have to wait for months or even weeks to get them made.
How can manufacturing avoid production bottlenecks
The key to avoiding bottlenecks in production is to keep all processes running smoothly throughout the entire production cycle, from the time you receive an order until the time when the product ships.
This includes both quality control and capacity planning.
Continuous improvement techniques like Six Sigma are the best way to achieve this.
Six Sigma Management System is a method to increase quality and reduce waste throughout your organization.
It emphasizes consistency and eliminating variance in your work.
What's the difference between Production Planning & Scheduling?
Production Planning (PP) is the process of determining what needs to be produced at any given point in time. Forecasting and identifying production capacity are two key elements to this process.
Scheduling refers the process by which tasks are assigned dates so that they can all be completed within the given timeframe.
What are the differences between these four types?
Manufacturing is the process of transforming raw materials into useful products using machines and processes. Manufacturing involves many activities, including designing, building, testing and packaging, shipping, selling, service, and so on.
How can I learn about manufacturing?
Experience is the best way for you to learn about manufacturing. You can read books, or watch instructional videos if you don't have the opportunity to do so.
Statistics
- Job #1 is delivering the ordered product according to specifications: color, size, brand, and quantity. (netsuite.com)
- In the United States, for example, manufacturing makes up 15% of the economic output. (twi-global.com)
- (2:04) MTO is a production technique wherein products are customized according to customer specifications, and production only starts after an order is received. (oracle.com)
- Many factories witnessed a 30% increase in output due to the shift to electric motors. (en.wikipedia.org)
- In 2021, an estimated 12.1 million Americans work in the manufacturing sector.6 (investopedia.com)
External Links
How To
How to Use the 5S to Increase Productivity In Manufacturing
5S stands for "Sort", 'Set In Order", 'Standardize', & Separate>. The 5S methodology was developed at Toyota Motor Corporation in 1954. It allows companies to improve their work environment, thereby achieving greater efficiency.
This method has the basic goal of standardizing production processes to make them repeatable. Cleaning, sorting and packing are all done daily. This knowledge allows workers to be more efficient in their work because they are aware of what to expect.
Implementing 5S requires five steps. These are Sort, Set In Order, Standardize. Separate. And Store. Each step has a different action and leads to higher efficiency. Sorting things makes it easier to find them later. When you arrange items, you place them together. After you have divided your inventory into groups you can store them in easy-to-reach containers. You can also label your containers to ensure everything is properly labeled.
Employees need to reflect on how they do their jobs. Employees should understand why they do the tasks they do, and then decide if there are better ways to accomplish them. In order to use the 5S system effectively, they must be able to learn new skills.
The 5S method increases efficiency and morale among employees. They will feel motivated to strive for higher levels of efficiency once they start to see results.