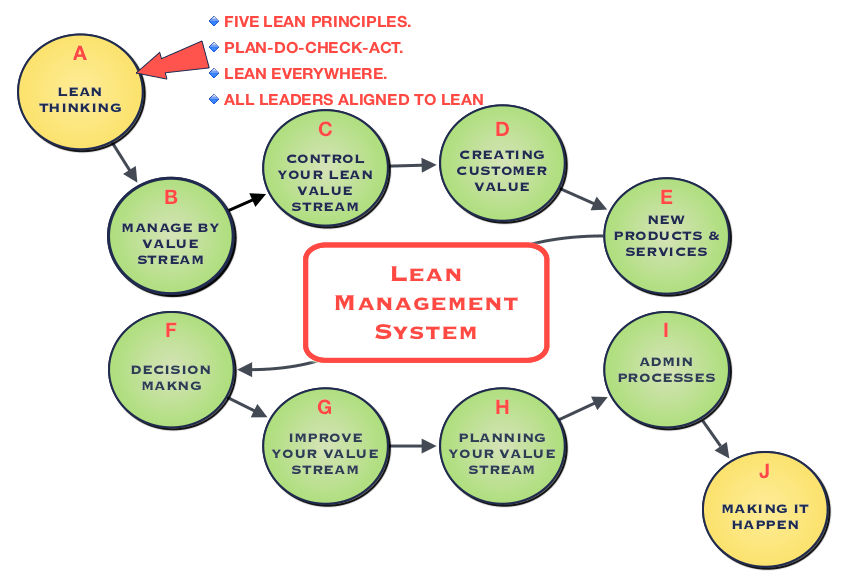
Materials engineers are responsible for the design, development, and research of new materials, which will enable future technology. They use metals, composites, ceramics, and plastics to create materials which meet specific chemical, mechanical, and electrical requirements.
What does a materials engineer do?
A material engineer tests, processes and develops raw materials, which are then used to create a range of products including aircraft wings or computer chips. They can also be involved in the development of biomedical devices or golf clubs. These engineers evaluate and study the properties and structures of metals such as ceramics or plastics. They also examine nanomaterials which are extremely small substances.
The duties of a materials engineering vary according to their industry and the materials they are using. However, they are often responsible for assessing production costs, quality control, creating budgets, and supervising technicians.
What is an materials science engineer (MSI)?
Materials science engineers work with different materials, such as metals, composites, ceramics and ceramics to make them lighter, stronger and more durable. A materials science engineer can create new materials or improve on existing ones.
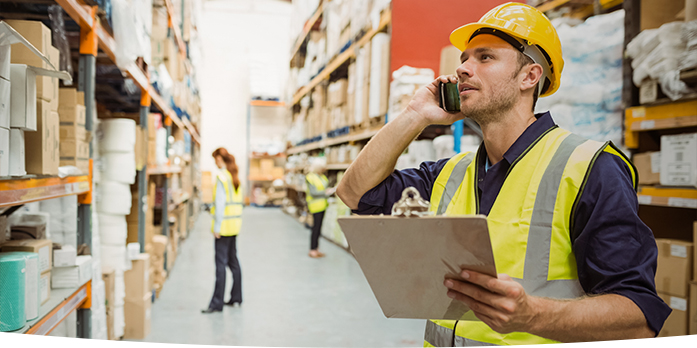
What do materials engineers need?
You will need a degree in engineering, materials science or a related field to become a Materials Engineer. This degree should include classroom and laboratory work with an emphasis on engineering principles. It may take several years to finish the program.
You can find a job as a materials engineer after graduation and you can expect to earn a salary of around PS25,000 a year. Your salary will rise significantly as you gain experience.
How to become a materials engineer
The qualifications you need to be a materials engineer vary between industries and employers. Most jobs require a bachelor's in materials science or engineer. This will involve studies in chemistry, math, and physics.
Qualifications for a career as a materials science engineer are generally high school diploma and a bachelor's degree in a relevant field such as physics, chemistry or engineering. For higher-level positions in research, a master's degree or doctoral qualification is often required.
How much can I expect to earn as a material engineer?
Salary levels for materials engineers vary depending upon their level of experience, industry and company size. You can also expect bonuses and other benefits for your work.
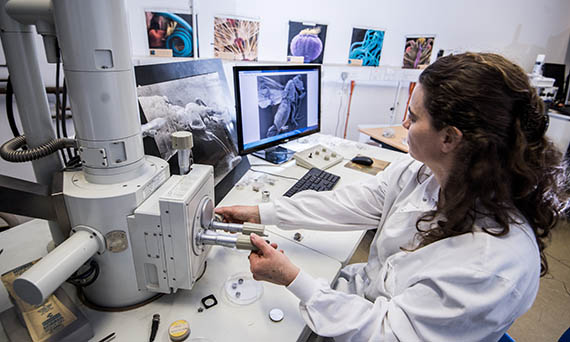
What are the prospects for a career in materials engineering?
The future of the materials engineering career is expected to be very good, with a lot of new opportunities opening up for those who want to get into this line of work. It is due to the growing demand for advanced, newer materials in various fields, such as medicine and architecture.
Studying metallurgy or chemistry can lead to a career as a materials engineer. This will give you the knowledge you need to pursue a career in this industry and may open up more opportunities for you down the line. You will benefit from a degree, such as in chemistry, if you want to improve your research skills. For additional experience, it is possible to work in a company that specializes in a certain field of materials.
FAQ
What are the logistics products?
Logistics is the process of moving goods from one point to another.
They include all aspects associated with transport including packaging, loading transporting, unloading storage, warehousing inventory management customer service, distribution returns and recycling.
Logisticians ensure that the right product reaches the right place at the right time and under safe conditions. They help companies manage their supply chain efficiency by providing information on demand forecasts, stock levels, production schedules, and availability of raw materials.
They can also track shipments in transit and monitor quality standards.
What are manufacturing and logistics?
Manufacturing refers the process of producing goods from raw materials through machines and processes. Logistics encompasses the management of all aspects associated with supply chain activities such as procurement, production planning, distribution and inventory control. It also includes customer service. Sometimes manufacturing and logistics are combined to refer to a wider term that includes both the process of creating products as well as their delivery to customers.
What skills do production planners need?
To become a successful production planner, you need to be organized, flexible, and able to multitask. Communication skills are essential to ensure that you can communicate effectively with clients, colleagues, and customers.
How can manufacturing efficiency improved?
The first step is to identify the most important factors affecting production time. We then need to figure out how to improve these variables. You can start by identifying the most important factors that impact production time. Once you've identified them, try to find solutions for each of those factors.
Are there any Manufacturing Processes that we should know before we can learn about Logistics?
No. No. It is important to know about the manufacturing processes in order to understand how logistics works.
Why automate your warehouse
Modern warehouses have become more dependent on automation. The rise of e-commerce has led to increased demand for faster delivery times and more efficient processes.
Warehouses have to be flexible to meet changing requirements. Technology is essential for warehouses to be able to adapt quickly to changing needs. Automating warehouses has many benefits. These are some of the benefits that automation can bring to warehouses:
-
Increases throughput/productivity
-
Reduces errors
-
Increases accuracy
-
Safety increases
-
Eliminates bottlenecks
-
Companies can scale more easily
-
Makes workers more efficient
-
The warehouse can be viewed from all angles.
-
Enhances customer experience
-
Improves employee satisfaction
-
Reducing downtime and increasing uptime
-
This ensures that quality products are delivered promptly
-
Eliminates human error
-
It helps ensure compliance with regulations
Statistics
- (2:04) MTO is a production technique wherein products are customized according to customer specifications, and production only starts after an order is received. (oracle.com)
- You can multiply the result by 100 to get the total percent of monthly overhead. (investopedia.com)
- In the United States, for example, manufacturing makes up 15% of the economic output. (twi-global.com)
- Many factories witnessed a 30% increase in output due to the shift to electric motors. (en.wikipedia.org)
- [54][55] These are the top 50 countries by the total value of manufacturing output in US dollars for its noted year according to World Bank.[56] (en.wikipedia.org)
External Links
How To
How to Use Six Sigma in Manufacturing
Six Sigma is defined by "the application SPC (statistical process control) techniques to achieve continuous improvements." Motorola's Quality Improvement Department, Tokyo, Japan, developed it in 1986. Six Sigma's basic concept is to improve quality and eliminate defects through standardization. Since there are no perfect products, or services, this approach has been adopted by many companies over the years. Six Sigma's primary goal is to reduce variation from the average value of production. If you take a sample and compare it with the average, you will be able to determine how much of the production process is different from the norm. If this deviation is too big, you know something needs fixing.
Understanding the nature of variability in your business is the first step to Six Sigma. Once you have a good understanding of the basics, you can identify potential sources of variation. It is important to identify whether the variations are random or systemic. Random variations are caused by human errors. Systematic variations can be caused by outside factors. You could consider random variations if some widgets fall off the assembly lines. If however, you notice that each time you assemble a widget it falls apart in exactly the same spot, that is a problem.
Once you identify the problem areas, it is time to create solutions. The solution could involve changing how you do things, or redesigning your entire process. Once you have implemented the changes, it is important to test them again to ensure they work. If they fail, you can go back to the drawing board to come up with a different plan.