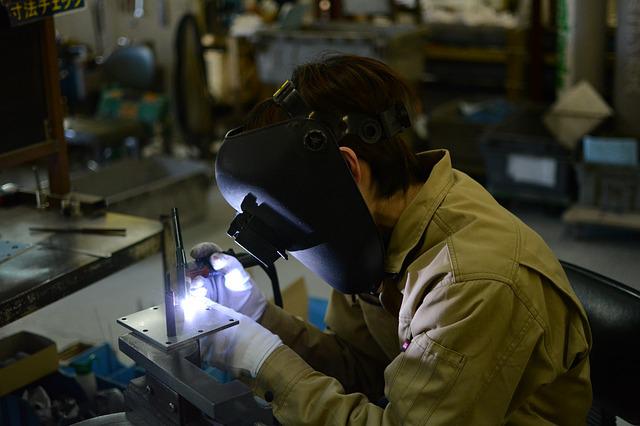
SIPOC Diagram is a visual aid that can be used to identify the inputs as well as outputs in a process. This tool allows members of a team to identify areas for improvement or any gaps that exist in the operations.
The sipoc diagram can often be found in the DMAIC cycle of process improvement, a framework that is used to create a business process which can be improved by analysis and continual improvement. The sipoc diagram helps teams and sponsors to agree on project scope and boundaries, as well Key Process Input Variables.
What is SIPOC?
The SIPOC diagram provides a visual representation that is simple to understand and follow of the inputs, outputs, and steps of a business process. The primary purpose of this diagram is to assist the team in understanding and analyzing the business processes at a higher level. This includes providing a picture that clearly shows the steps required to transform inputs to desired outputs.
What is the history of the sipoc diagram?
The sipoc Diagram can be traced all the way back to late 1980s. This was part of Total Quality Management (TQM), a model of business process improvement based on Six Sigma. It has since been widely used in lean-manufacturing and business process improvement programmes, as it's an effective tool for streamlining, identifying improvements, and improving communications between stakeholders.
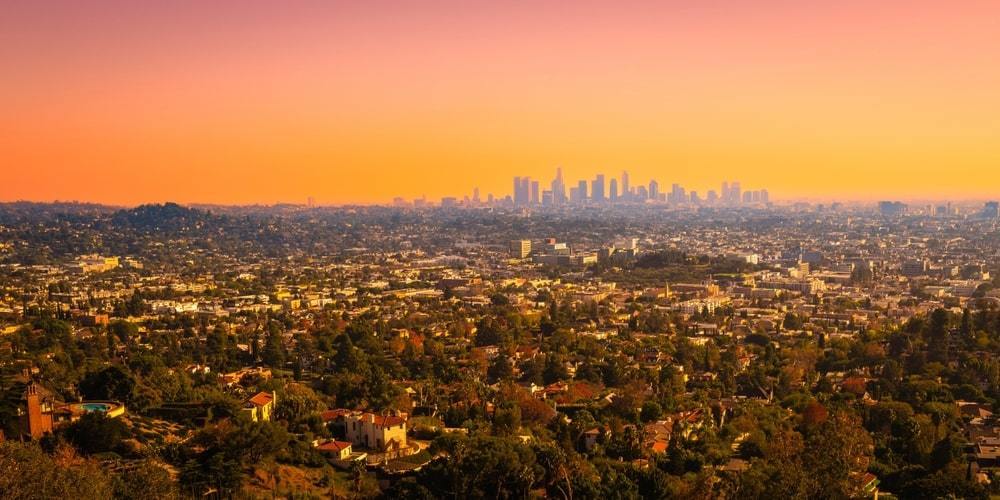
How to Make SIPOCs
To begin, you must first choose the process that you want to analyze. This will help you and your team to focus on the most important areas and ensure that no important details are overlooked.
Next, you will need to identify all the inputs needed for the process. This includes who supplies these inputs. List each supplier, their contact details and the raw materials they supply to the process.
List all clients, internal and outside, who will receive the product or service. This can ensure that the business is providing products and services of high quality.
Inputs is the first part of the SIPOC diagram. It contains the specifications for the materials or information that the process requires. Material can either be physical goods such as products or information such as reports.
Outputs are the second section on a SIPOC. This section is usually a summary of all the products or services produced as a direct result of the SIPOC process. The outputs need to reflect the value the customer expects from the process and meet their needs.
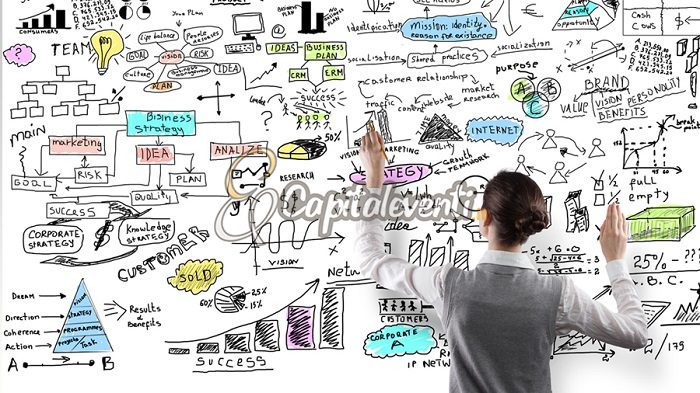
Customers: This final section of the SIPOC diagram identifies customers, both inside and outside the organization. This can include the maintenance team, line operators, and other internal and external clients.
SIPOCs are powerful visual tools that can be used for improving business processes and communication among all stakeholders. The diagram is easy to make and can be used to help team members understand the business processes being studied. It's best to use templates that include all key diagram components such as inputs or outputs. It can save you time as well as effort by using a pre-made template.
FAQ
What are the responsibilities of a logistic manager?
A logistics manager makes sure that all goods are delivered on-time and in good condition. This is done through his/her expertise and knowledge about the company's product range. He/she should ensure that sufficient stock is available in order to meet customer demand.
Do we need to know about Manufacturing Processes before learning about Logistics?
No. No. However, knowing about manufacturing processes will definitely give you a better understanding of how logistics works.
Why is logistics important in manufacturing
Logistics are essential to any business. They help you achieve great results by helping you manage all aspects of product flow, from raw materials to finished goods.
Logistics also play a major role in reducing costs and increasing efficiency.
Statistics
- You can multiply the result by 100 to get the total percent of monthly overhead. (investopedia.com)
- According to a Statista study, U.S. businesses spent $1.63 trillion on logistics in 2019, moving goods from origin to end user through various supply chain network segments. (netsuite.com)
- In the United States, for example, manufacturing makes up 15% of the economic output. (twi-global.com)
- Many factories witnessed a 30% increase in output due to the shift to electric motors. (en.wikipedia.org)
- (2:04) MTO is a production technique wherein products are customized according to customer specifications, and production only starts after an order is received. (oracle.com)
External Links
How To
How to Use Six Sigma in Manufacturing
Six Sigma is defined by "the application SPC (statistical process control) techniques to achieve continuous improvements." Motorola's Quality Improvement Department created Six Sigma at their Tokyo plant, Japan in 1986. Six Sigma's core idea is to improve the quality of processes by standardizing and eliminating defects. Many companies have adopted Six Sigma in recent years because they believe that there are no perfect products and services. Six Sigma seeks to reduce variation between the mean production value. This means that if you take a sample of your product, then measure its performance against the average, you can find out what percentage of the time the process deviates from the norm. If it is too large, it means that there are problems.
Understanding the nature of variability in your business is the first step to Six Sigma. Once you've understood that, you'll want to identify sources of variation. Also, you will need to identify the sources of variation. Random variations occur when people do mistakes. Symmetrical variations are caused due to factors beyond the process. Random variations would include, for example, the failure of some widgets to fall from the assembly line. But if you notice that every widget you make falls apart at the exact same place each time, this would indicate that there is a problem.
After identifying the problem areas, you will need to devise solutions. That solution might involve changing the way you do things or redesigning the process altogether. After implementing the new changes, you should test them again to see if they worked. If they don't work you need to rework them and come up a better plan.