
Wichita, just a short drive away from Topeka or Salina, is home to many great things to see and do. It is also an ideal place to do business, if you are looking for new locations for your company. CTDI is a great place to find logistics support if that's what you're looking.
CTDI stands out among the many companies offering logistics services. CTDI is a full-service engineering and logistics company that provides a variety of services to cable companies and customers. CTDI not only offers the best solutions for the communication industry but also improves the efficiency of their logistic operations. The company's customers can therefore be certain that they will receive their goods promptly and in good condition.
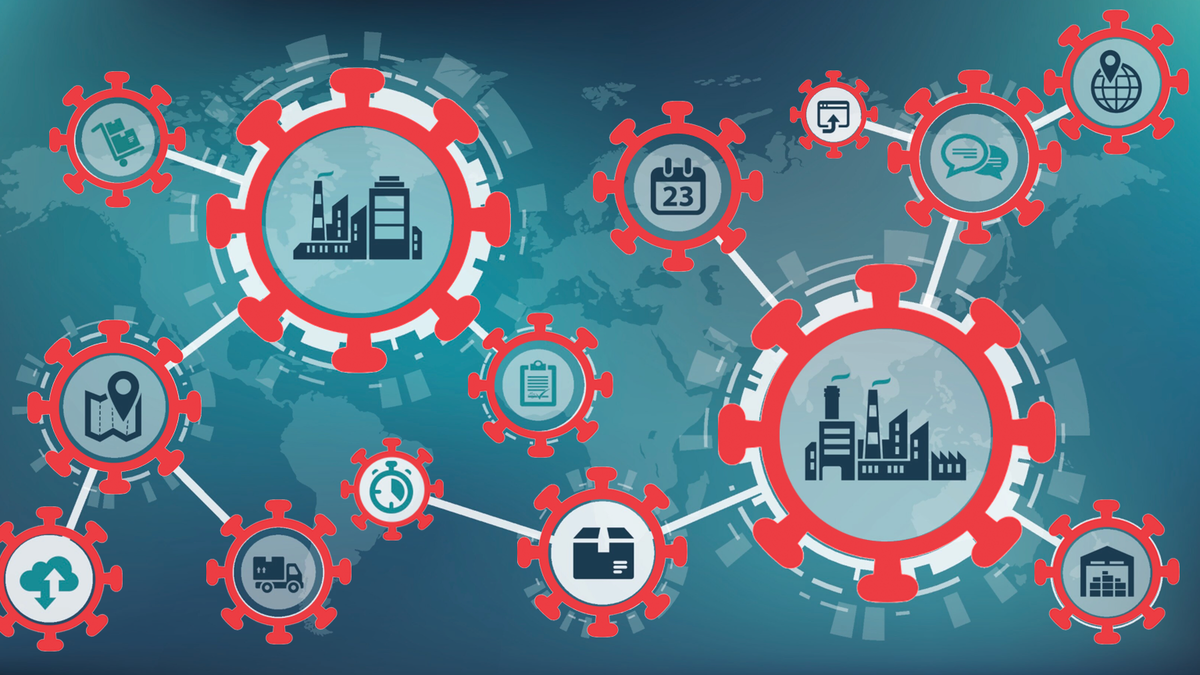
CTDI's Wichita Kansas facility can be found at 3434 North Comotara Street. Other facilities are available in the United States as well as at 47 locations in Canada or China. The company has a small staff, but is expanding as the company begins to service the markets of Wichita, Oklahoma City, and Tulsa.
CTDI has been in business for several years, and provides services to some of the largest cable providers in the country. They are a Cisco repair facility. They also have an impressive number of facilities in Canada, and in China and Europe. In addition, they have a number of telecommunications products in their inventory, including wireless and wireline telephones and cable television sets. Many cable companies use their products, including Spectrum and AT&T, Time Warner Cable, Verizon, Comcast and Spectrum.
CTDI's recent acquisition of a state-of-the-art distribution center for Cox Communications is one of their most notable accomplishments. This facility is located in Wichita, Kansas, and will be the largest of three Cox distribution centers in the state. The company plans to expand the facility to include a repair operation. CTDI will be adding more staff to Wichita as the center expands.
The company also has a telecommunications center in West Chester, Pennsylvania. The facility was awarded a number of awards by the Transportation Research Board, such as being the cheapest carrier for its class and the lowest carrier for its state class by the Society for Logistics Management. Other impressive achievements include providing engineering services for the cable industry. Its ability to offer services to some of the most important telecommunications companies around the globe was the company's greatest accomplishment.
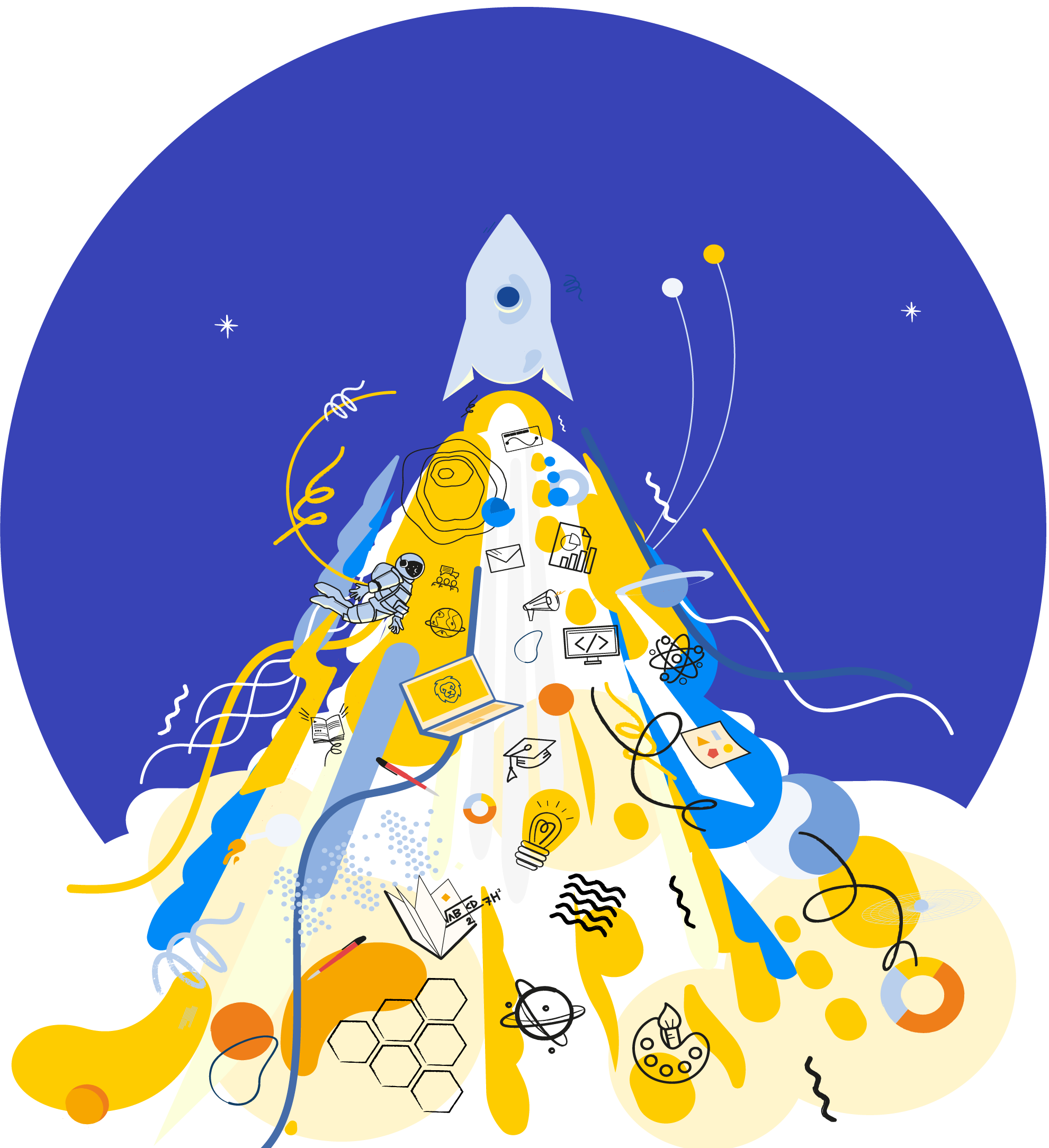
CTDI's most notable achievement is its use the latest technology to offer the best logistics solutions to its customers. They also offer equal opportunities to all employees, including those of different races and genders. You can also enjoy a variety of fun and interesting benefits like a health club, and a gym for free.
FAQ
What is the difference between manufacturing and logistics
Manufacturing is the process of creating goods from raw materials by using machines and processes. Logistics is the management of all aspects of supply chain activities, including procurement, production planning, distribution, warehousing, inventory control, transportation, and customer service. As a broad term, manufacturing and logistics often refer to both the creation and delivery of products.
What are the differences between these four types?
Manufacturing refers the process of turning raw materials into useful products with machines and processes. Manufacturing involves many activities, including designing, building, testing and packaging, shipping, selling, service, and so on.
What are the goods of logistics?
Logistics involves the transportation of goods from point A and point B.
They include all aspects of transport, including packaging, loading, transporting, unloading, storing, warehousing, inventory management, customer service, distribution, returns, and recycling.
Logisticians ensure that the right product reaches the right place at the right time and under safe conditions. They help companies manage their supply chain efficiency by providing information on demand forecasts, stock levels, production schedules, and availability of raw materials.
They monitor shipments in transit, ensure quality standards, manage inventories, replenish orders, coordinate with suppliers and other vendors, and offer support services for sales, marketing, and customer service.
Statistics
- It's estimated that 10.8% of the U.S. GDP in 2020 was contributed to manufacturing. (investopedia.com)
- According to a Statista study, U.S. businesses spent $1.63 trillion on logistics in 2019, moving goods from origin to end user through various supply chain network segments. (netsuite.com)
- You can multiply the result by 100 to get the total percent of monthly overhead. (investopedia.com)
- (2:04) MTO is a production technique wherein products are customized according to customer specifications, and production only starts after an order is received. (oracle.com)
- In 2021, an estimated 12.1 million Americans work in the manufacturing sector.6 (investopedia.com)
External Links
How To
How to use Lean Manufacturing in the production of goods
Lean manufacturing is a management system that aims at increasing efficiency and reducing waste. It was developed in Japan during the 1970s and 1980s by Taiichi Ohno, who received the Toyota Production System (TPS) award from TPS founder Kanji Toyoda. Michael L. Watkins published the book "The Machine That Changed the World", which was the first to be published about lean manufacturing.
Lean manufacturing is often described as a set if principles that help improve the quality and speed of products and services. It is about eliminating defects and waste from all stages of the value stream. Lean manufacturing is called just-in-time (JIT), zero defect, total productive maintenance (TPM), or 5S. Lean manufacturing seeks to eliminate non-value added activities, such as inspection, work, waiting, and rework.
In addition to improving product quality and reducing costs, lean manufacturing helps companies achieve their goals faster and reduces employee turnover. Lean manufacturing has been deemed one of the best ways to manage the entire value-chain, including customers, distributors as well retailers and employees. Lean manufacturing is widely practiced in many industries around the world. Toyota's philosophy is a great example of this. It has helped to create success in automobiles as well electronics, appliances and healthcare.
Lean manufacturing is based on five principles:
-
Define Value - Determine the value that your business brings to society. Also, identify what sets you apart from your competitors.
-
Reduce waste - Stop any activity that isn't adding value to the supply chains.
-
Create Flow – Ensure that work flows smoothly throughout the process.
-
Standardize & Simplify - Make processes as consistent and repeatable as possible.
-
Build Relationships - Establish personal relationships with both internal and external stakeholders.
Although lean manufacturing has always been around, it is gaining popularity in recent years because of a renewed interest for the economy after 2008's global financial crisis. To increase their competitiveness, many businesses have turned to lean manufacturing. Some economists even believe that lean manufacturing can be a key factor in economic recovery.
With many benefits, lean manufacturing is becoming more common in the automotive industry. These include improved customer satisfaction, reduced inventory levels, lower operating costs, increased productivity, and better overall safety.
It can be applied to any aspect of an organisation. However, it is particularly useful when applied to the production side of an organization because it ensures that all steps in the value chain are efficient and effective.
There are three main types in lean manufacturing
-
Just-in Time Manufacturing (JIT), also known as "pull system": This form of lean manufacturing is often referred to simply as "pull". JIT refers to a system in which components are assembled at the point of use instead of being produced ahead of time. This approach reduces lead time, increases availability and reduces inventory.
-
Zero Defects Manufacturing - ZDM: ZDM focuses its efforts on making sure that no defective units leave a manufacturing facility. It is better to repair a part than have it removed from the production line if it needs to be fixed. This is true even for finished products that only require minor repairs prior to shipping.
-
Continuous Improvement: Continuous Improvement aims to improve efficiency by continually identifying problems and making adjustments to eliminate or minimize waste. It involves continuous improvement of processes, people, and tools.